- FMA
- The Fabricator
- FABTECH
- Canadian Metalworking
Categories
- Additive Manufacturing
- Aluminum Welding
- Arc Welding
- Assembly and Joining
- Automation and Robotics
- Bending and Forming
- Consumables
- Cutting and Weld Prep
- Electric Vehicles
- En Español
- Finishing
- Hydroforming
- Laser Cutting
- Laser Welding
- Machining
- Manufacturing Software
- Materials Handling
- Metals/Materials
- Oxyfuel Cutting
- Plasma Cutting
- Power Tools
- Punching and Other Holemaking
- Roll Forming
- Safety
- Sawing
- Shearing
- Shop Management
- Testing and Measuring
- Tube and Pipe Fabrication
- Tube and Pipe Production
- Waterjet Cutting
Industry Directory
Webcasts
Podcasts
FAB 40
Advertise
Subscribe
Account Login
Search
Examining respiratory safety
What three companies are doing to protect their welders
- By Amanda Carlson
- September 11, 2007
- Article
- Safety
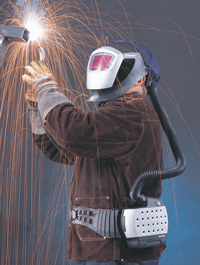
Welders from JH Kelly, Total Fab LLC, and P&H Mining said that they feel more refreshed after using breathing apparatuses, similar to this one, a Speedglas with Adflo system from 3M. Photo courtesy of 3M.
Time's up. As of May 30, 2007, large and small companies alike were required to comply with the Occupational Safety and Health Administration's (OSHA) hexavalent chromium standard, which states that the permissible exposure limit (PEL) for all companies is 5 micrograms per cubic meter as an eight-hour time-weighted average. Fab shops across the nation were forced to rework their respiratory safety guidelines and implement the necessary equipment to ensure exposure limit compliance.
Some welding shops, however, had strict respiratory guidelines in place for its welders long before the OSHA standard was set into motion.
Practical Welding Today talked to three fab shops to find out what measures they have in place for their welders and the pros and cons of using respiratory equipment while on the job.
And the Survey Says …
JH Kelly, a mechanical contractor located in Longview, Wash., was one of many companies that implemented a hexavalent chromium program in light of the OSHA standard. Because it employs 44 people in its fabrication shop, the company was required to fall into compliance in November 2006. According to Shop Foreman Mike Riddle, the company's six welders are equipped with an Adflo™ powered air purifying respirator (PAPR) manufactured by 3M, which comprises a utility belt with an onboard filter and air pump exchanger. It has two different air filters—a particulate filter specifically for hexavalent chromium and another for organic compounds. The air pump exchanger filters the air, which travels through the pump and is released directly into the hood.
Riddle said that each welder was given a medical evaluation to ensure he was fit to wear the device. The hood itself has a false front so the welders don't have to remove it to perform grinding or polishing. The shop's six welding bays also share three Lincoln Mobiflex fume extractors.
Riddle said one of the most difficult aspects of the transition for some of the more experienced welders was adjusting to the different colored lens.
"They're used to looking through the typical green lens, and this particular color took a while for them to get used to.
"At first it was cumbersome to use the hood, but it's like anything else new. After a little while you just get used to the new standards that are employed," Riddle said.
Despite the adjustment, Riddle added, the welders now find that they are blowing fewer particles out of their noses at the end of the day and tend to feel more refreshed because of the cool air that circulates within the hood.
Fred Moore, owner of Total Fab LLC, Wallingford, Conn., said the decision to implement respiratory equipment for the company's welders was more about providing them with cleaner air and less about the hexavalent chromium standard. Right now two of the company's six welders use the 3M Adflo system, but the company plans to issue the equipment to all welders.
"This was to get us to step up to the 21st century and take better care of the employees and the welders, to look out for the interest of everybody," Moore said.
Like the welders at JH Kelly, Total Fab's welders now feel better at the end of the day from not breathing in smoke, Moore said. The units also help keep them cool during hot conditions.
"So far the guys seem to like them. The only complaint I've received is that the backpack is heavy."
P&H Mining Equipment has over 3,500 employees globally, 150 of which are manufacturing welders based in Milwaukee. Another 500 or so full-time welders work for the P&H MinePro Services side of the business, which is spread out globally in Canada, Chile, Mexico, Brazil, Peru, South Africa, China, and Australia. P&H Mining Equipment uses supplied-air respirator systems or powered air purifying systems. The 3M L-Series supplied-air units and the 3M PAPR units are the majority of the products used globally.
"Our philosophical approach was that we wanted our welders to be protected at the utmost level. Even though we were below the exposure levels required by OSHA and ACGIH, we chose to take a more proactive approach and give our welders the highest level of protection," said Ted Leamen, director of global environmental health and safety at P&H.
With recent reports pointing to a possible link between long-term fume exposure and illness, Leamen said the company would much rather protect its employees and prevent any future liability issues and health risks to its work force.
"P&H welders conduct a lot of welding in some pretty tight spaces, and while the supplied-air or PAPR systems can be cumbersome, at the end of the day, this inconvenience is well worth it to protect the health and safety of the employee," Leamen noted.
This respiratory program did present challenges for the company's older and longtime welders, who were used to doing things without any fume protection. These employees had a tough time accepting the need for respiratory equipment. The company resolved this issue by involving its welders in the decision- making process, letting them try equipment from several manufacturers, and then allowing them to provide input into the final product choice.
The younger welders, Leamen added, had a tendency to understand and appreciate the respiratory protection equipment and supported the company's efforts.
"The nice thing about the 3M product is the cooling vortex on the supplied-air system that literally cools the air and offers a very comfortable environment for our welders who are welding outside, in tropical countries, or during the hot summer months," Leamen said.
About the Author
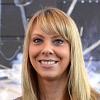
Amanda Carlson
2135 Point Blvd
Elgin, IL 60123
815-227-8260
Amanda Carlson was named as the editor for The WELDER in January 2017. She is responsible for coordinating and writing or editing all of the magazine’s editorial content. Before joining The WELDER, Amanda was a news editor for two years, coordinating and editing all product and industry news items for several publications and thefabricator.com.
About the Publication
Related Companies
subscribe now
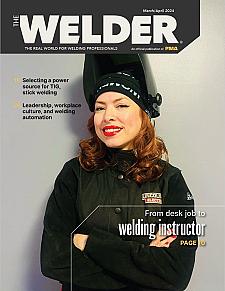
The Welder, formerly known as Practical Welding Today, is a showcase of the real people who make the products we use and work with every day. This magazine has served the welding community in North America well for more than 20 years.
start your free subscription- Stay connected from anywhere
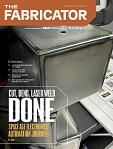
Easily access valuable industry resources now with full access to the digital edition of The Fabricator.
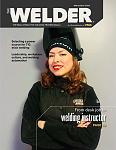
Easily access valuable industry resources now with full access to the digital edition of The Welder.
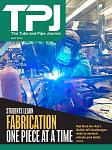
Easily access valuable industry resources now with full access to the digital edition of The Tube and Pipe Journal.
- Podcasting
- Podcast:
- The Fabricator Podcast
- Published:
- 04/16/2024
- Running Time:
- 63:29
In this episode of The Fabricator Podcast, Caleb Chamberlain, co-founder and CEO of OSH Cut, discusses his company’s...
- Industry Events
16th Annual Safety Conference
- April 30 - May 1, 2024
- Elgin,
Pipe and Tube Conference
- May 21 - 22, 2024
- Omaha, NE
World-Class Roll Forming Workshop
- June 5 - 6, 2024
- Louisville, KY
Advanced Laser Application Workshop
- June 25 - 27, 2024
- Novi, MI