President
- FMA
- The Fabricator
- FABTECH
- Canadian Metalworking
Categories
- Additive Manufacturing
- Aluminum Welding
- Arc Welding
- Assembly and Joining
- Automation and Robotics
- Bending and Forming
- Consumables
- Cutting and Weld Prep
- Electric Vehicles
- En Español
- Finishing
- Hydroforming
- Laser Cutting
- Laser Welding
- Machining
- Manufacturing Software
- Materials Handling
- Metals/Materials
- Oxyfuel Cutting
- Plasma Cutting
- Power Tools
- Punching and Other Holemaking
- Roll Forming
- Safety
- Sawing
- Shearing
- Shop Management
- Testing and Measuring
- Tube and Pipe Fabrication
- Tube and Pipe Production
- Waterjet Cutting
Industry Directory
Webcasts
Podcasts
FAB 40
Advertise
Subscribe
Account Login
Search
Aluminum Workshop: Understanding AC and HAZ ‘cracks’
- By Frank Armao
- January 2, 2015
- Article
- Aluminum Welding
Q: I know that when aluminum alloys are gas tungsten arc-welded (GTAW), usually we use alternating current (AC) because it give some sort of cleaning action. Can you explain what it is and how it works?
A: Sure, let’s try. But before I start, let me admit that this explanation is a bit of a simplification. If I were to give a strictly correct explanation, it would take a lot more space than I have here. Also the following explanation will be of more practical use. So I’ll ask forgiveness in advance from all the physicists out there and proceed.
It isn’t actually the AC that gives the cleaning action; it’s the part of the AC cycle when the tungsten electrode is positive. At these times the electrode is said to be the cathode in the circuit (the work is the anode), so this process sis called cathodic cleaning.
When the tungsten is positive, electrons flow from the work to the tungsten. At this time, the arc uses most of its energy to heat the tungsten and produces shallow penetration. However, a counterflow of current—made of ionized atoms of shielding gas—also exists. For the moment let’s assume the shielding gas is argon. These ions, formed in the 10,000-degree-F-plus arc, have a positive charge and are attracted to the work surface, which at this time is charged negatively. So they accelerate because of the voltage difference and hit the work surface. The easiest way to understand this phenomenon (here comes the simplification) is to visualize the argon ions as sandblasting the surface of the aluminum and cleaning the oxide from it.
So the electrode-positive part of the AC cycle gives us cathodic cleaning to remove the oxide from the surface of the aluminum, which we need, but it doesn’t help give us penetration, which is what we want. The penetration comes from the part of the AC cycle in which the electrode is negative. So we use AC to get both.
Back when GTAW power supplies generated a simple sine wave, we were constrained to use 50 percent electrode negative and 50 percent electrode positive. However, we don’t need 50 percent electrode positive to get adequate arc cleaning. With the advent of square wave power supplies around 1975, we could adjust the balance of the wave to get a higher percentage of electrode negative and a lower percentage of electrode positive.
It was found that a balance of about 65 to 70 percent electrode negative and 30 to 35 percent electrode positive gave sufficient arc cleaning. It also gave more weld penetration and less tungsten heating than a 50 percent positive arc. Some newer power supplies can provide adequate arc cleaning with as little as 10 to 15 percent electrode positive. From the standpoint of efficiency, set the balance control on your power supply as far toward “Penetration” or “Negative” as possible while still maintaining adequate arc cleaning.
The sandblasting analogy can help explain a few other phenomena. We all know that argon gas shielding gives more arc cleaning than helium. Why? Consider the difference between sandblasting with sand versus features. The heavier medium gives the best results. The same is true with shielding gases. The heavier gas molecule gives more arc cleaning. What about gas metal arc welding (GMAW)? Because aluminum GMAW normally is performed with the electrode positive at all times, we get a lot of arc cleaning.
Whenever you gas tungsten arc-weld aluminum using AC or gas metal arc-weld aluminum, you should be able to see the evidence of arc cleaning. It should look like a bright, frosty stripe about 1/16 to 1/8 inch wide along each side of the weld bead. If you can’t see these cleaning lines, you’ve done something wrong.
Q: I work in the aerospace industry. We have to liquid penetrant-test all of our aluminum welds. Sometimes when we test a weld made using GTAW, we see all sorts of indications in the heat-affected zone (HAZ) that look like cracks. Sometimes there are so many cracks it almost looks like a spider web. We never see this in welds made using GMAW. What’s going on?
A: First of all, it’s difficult to liquid penetrant-test aluminum. The aluminum oxide on the surface is porous. If you aren’t really careful about cleaning off the penetrant before spraying on the developer, you’ll get all sorts of spurious penetrant indications. However, this isn’t your problem. The cracks you see probably are confined to the area next to the weld that has been cleaned by the arc. These cracks also are probably very shallow, only 0.002 to 0.003 in. deep. You can check by sanding them lightly and then liquid penetrant-testing again. If the cracks go away, they were very shallow.
If this is the case—and I bet it is—your cracks are caused by adjusting the high-frequency (HF) intensity too high. Many people make the mistake of setting the HF intensity to maximum and leaving it there. In most cases, this causes no problems because the HF is on only briefly at the arc start. However, in aluminum AC welding, the HF is on continuously. If it is set too high, it can etch the surface of the aluminum adjacent the weld. Because the grain boundaries in the aluminum are areas of higher energy, the HF etches them preferentially. So the cracks you see actually are the preferentially etched grain boundary network. The etching is very shallow, but deep enough to hold dye penetrant. The remedy? Turn the HF intensity down a bit and the cracks will go away.
About the Author
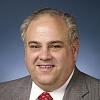
Frank Armao
Aluminum Consulting Inc.
440-479-0239
About the Publication
Related Companies
subscribe now
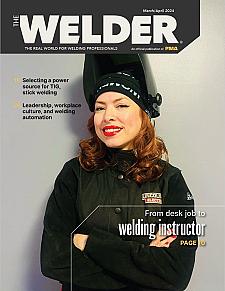
The Welder, formerly known as Practical Welding Today, is a showcase of the real people who make the products we use and work with every day. This magazine has served the welding community in North America well for more than 20 years.
start your free subscription- Stay connected from anywhere
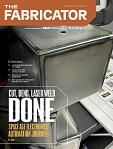
Easily access valuable industry resources now with full access to the digital edition of The Fabricator.
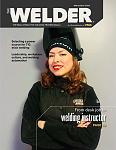
Easily access valuable industry resources now with full access to the digital edition of The Welder.
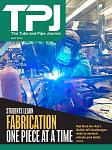
Easily access valuable industry resources now with full access to the digital edition of The Tube and Pipe Journal.
- Podcasting
- Podcast:
- The Fabricator Podcast
- Published:
- 05/07/2024
- Running Time:
- 67:38
Patrick Brunken, VP of Addison Machine Engineering, joins The Fabricator Podcast to talk about the tube and pipe...
- Trending Articles
The role of flux in submerged arc welding performance
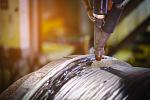
Aluminum MIG wires offer smooth feeding, reduced tangling
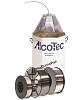
How welders can stay safe during grinding
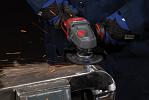
Connecticut students compete in Maritime Welding Competition
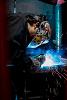
Three ESAB welding machines win Red Dot Awards for product design
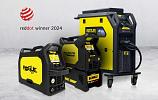
- Industry Events
World-Class Roll Forming Workshop
- June 5 - 6, 2024
- Louisville, KY
Advanced Laser Application Workshop
- June 25 - 27, 2024
- Novi, MI
Precision Press Brake Certificate Course
- July 31 - August 1, 2024
- Elgin,