- FMA
- The Fabricator
- FABTECH
- Canadian Metalworking
Categories
- Additive Manufacturing
- Aluminum Welding
- Arc Welding
- Assembly and Joining
- Automation and Robotics
- Bending and Forming
- Consumables
- Cutting and Weld Prep
- Electric Vehicles
- En Español
- Finishing
- Hydroforming
- Laser Cutting
- Laser Welding
- Machining
- Manufacturing Software
- Materials Handling
- Metals/Materials
- Oxyfuel Cutting
- Plasma Cutting
- Power Tools
- Punching and Other Holemaking
- Roll Forming
- Safety
- Sawing
- Shearing
- Shop Management
- Testing and Measuring
- Tube and Pipe Fabrication
- Tube and Pipe Production
- Waterjet Cutting
Industry Directory
Webcasts
Podcasts
FAB 40
Advertise
Subscribe
Account Login
Search
Stamping complex parts
Hydraulic presses expand deep-draw capabilities
- March 7, 2006
- Article
- Bending and Forming
![]() |
Wisconsin-based Tools Inc. is proud of its deep-drawing expertise for highly complex parts.
In the past, however, producing highly stylized shapes posed a continual challenge.
"Our in-house stamping capabilities consisted entirely of mechanical presses," said Chris Snyder, general manager of Tools Inc. "They are more than adequate for blanking and simple forming, but their fixed speeds and pressures make them poorly suited for certain deep-draw geometries."
According to the company, its mechanical presses turn out acceptable product, but some applications took a lot of effort and resulted in excessive scrap. To sidestep these problems, the stamper resorted to buying time on another stamper's hydraulic press. "In addition to increasing lead-times and production costs, paying another stamper to produce these parts meant giving business directly to our competitors," Snyder said.
As a result, Tools Inc. avoided contracts for large production runs of highly cosmetic stampings. However, by 1998 the stamper was in line for several sizable contracts that required turning out complicated deep—drawn shapes on a production basis.
The time had come to bring hydraulic stamping capabilities in-house.
Getting Control of the Deep-Draw Process
When it came to press features, Tools Inc. knew exactly what it needed: a hydraulic press with a large bed to accommodate the asymmetric pressures encountered in the blanking and drawing of complex parts, including adjustable operating parameters to produce a range of deep-drawn stampings cost-effectively.
After researching several presses, the stamper purchased a ZM 800, an 800-ton hydraulic press from AP&T. "The ZM let us program every operating parameter, from ram speed and position to cushion, tonnage, dwell, and return points," Snyder said.
According to Snyder, the ZM's controls allowed operators to program multiple speed and pressure sequences into a single cycle to produce variable forces required for some deep-drawn parts with better consistency and efficiency. "Controlling the ram velocity also softens the initial shock line characteristic in deep drawing and helps to reduce aesthetic or structural damage to the metal," he said.
The press system gave Tools Inc. production-scale stamping capabilities as well as the ability to perform in-house tryout and prototyping for customers with hydraulic applications. Production problems such as wrinkling, galling, and fracturing that severely limited the stamper's previous deep-draw output were minimized.
An Internet link connects the press's computer controls with the press manufacturer's home office in Sweden, allowing engineers to evaluate, diagnose, troubleshoot, and keep the hydraulic workhorse in top condition.
Snyder estimated that more than 40 percent of the company's parts are now made on the press. These parts could not have been produced on the company's mechanical presses.
![]() |
Figure 1 With the new hydraulic press system, Tools Inc. now can efficiently manufacture a greater range of complicated shapes and at a higher rate than ever before. |
New Capabilities, New Opportunities
With the new hydraulic press system, the stamper now could efficiently manufacture a greater range of complicated shapes and at a higher rate than ever before (see Figure 1). This capability quickly transformed the nature of stamping operations at the company.
Before production-scale hydraulic press capabilities were added, stamping was a small part of the business. Today stamping is one of the supplier's strong suits and a major contributor to its competitive position as a comprehensive turnkey supplier. "Instead of changing the geometry of a customer's parts to work with our presses, we can tailor the stamping process to suit their requirements," Snyder said. "To create a production line-ready part, OEMs usually deal with multiple suppliers to secure tooling, stamping, and finishing services. By adding this press system, we now have the ability to handle every aspect of the project."
The ability to produce more elaborate stampings allowed the company to secure new customers and contracts. Many of these contracts are for automotive, appliance, and lawn equipment parts that receive cosmetic paint or chrome finishes. "In particular, stamping motorcycle parts is like making jewelry," Snyder said. "The standards are incredibly high, and the parts have to be as close to flawless as possible."
Adding a Second Hydraulic Press
By 2000 demand for Tools Inc.'s deep-draw stampings threatened to outstrip the ZM 800's capacity.
To keep up with demand, the company added a second AP&T ZM press, a 450-ton model. The success of the 800-ton press resulted in more customer requests for long-run cosmetic stampings. The size of some of these parts made the 450-ton model the perfect choice to broaden the stamper's capabilities. Over the five years since the second press was added, both machines have handled heavy work loads and sophisticated production requirements without needing any upgrades.
As business continues to grow, Tools Inc. looks forward to expanding its line of hydraulic presses to include transfer systems.
Tools Inc., N5500 Executive Drive, Sussex, WI 53089, 262-246-3400, fax 262-246-3414, info@toolsinc.com, www.toolsinc.com
AP&T North America Inc., 4817 Persimmon Court, Monroe, NC 28110, 704-292-2900, fax 704-292-2906,info@apt-usa.com, www.apt.se
Related Companies
subscribe now
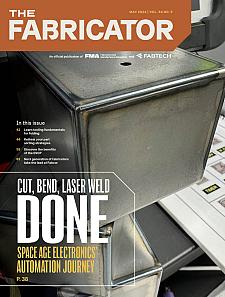
The Fabricator is North America's leading magazine for the metal forming and fabricating industry. The magazine delivers the news, technical articles, and case histories that enable fabricators to do their jobs more efficiently. The Fabricator has served the industry since 1970.
start your free subscription- Stay connected from anywhere
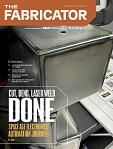
Easily access valuable industry resources now with full access to the digital edition of The Fabricator.
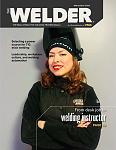
Easily access valuable industry resources now with full access to the digital edition of The Welder.
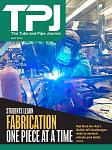
Easily access valuable industry resources now with full access to the digital edition of The Tube and Pipe Journal.
- Podcasting
- Podcast:
- The Fabricator Podcast
- Published:
- 04/16/2024
- Running Time:
- 63:29
In this episode of The Fabricator Podcast, Caleb Chamberlain, co-founder and CEO of OSH Cut, discusses his company’s...
- Industry Events
16th Annual Safety Conference
- April 30 - May 1, 2024
- Elgin,
Pipe and Tube Conference
- May 21 - 22, 2024
- Omaha, NE
World-Class Roll Forming Workshop
- June 5 - 6, 2024
- Louisville, KY
Advanced Laser Application Workshop
- June 25 - 27, 2024
- Novi, MI