- FMA
- The Fabricator
- FABTECH
- Canadian Metalworking
Categories
- Additive Manufacturing
- Aluminum Welding
- Arc Welding
- Assembly and Joining
- Automation and Robotics
- Bending and Forming
- Consumables
- Cutting and Weld Prep
- Electric Vehicles
- En Español
- Finishing
- Hydroforming
- Laser Cutting
- Laser Welding
- Machining
- Manufacturing Software
- Materials Handling
- Metals/Materials
- Oxyfuel Cutting
- Plasma Cutting
- Power Tools
- Punching and Other Holemaking
- Roll Forming
- Safety
- Sawing
- Shearing
- Shop Management
- Testing and Measuring
- Tube and Pipe Fabrication
- Tube and Pipe Production
- Waterjet Cutting
Industry Directory
Webcasts
Podcasts
FAB 40
Advertise
Subscribe
Account Login
Search
Generous spirit forms essence of welder/fabricator/artist
Big heart and big talent go hand-in-hand at Flying J
- By Eric Lundin
- March 3, 2017
- Article
- Arc Welding
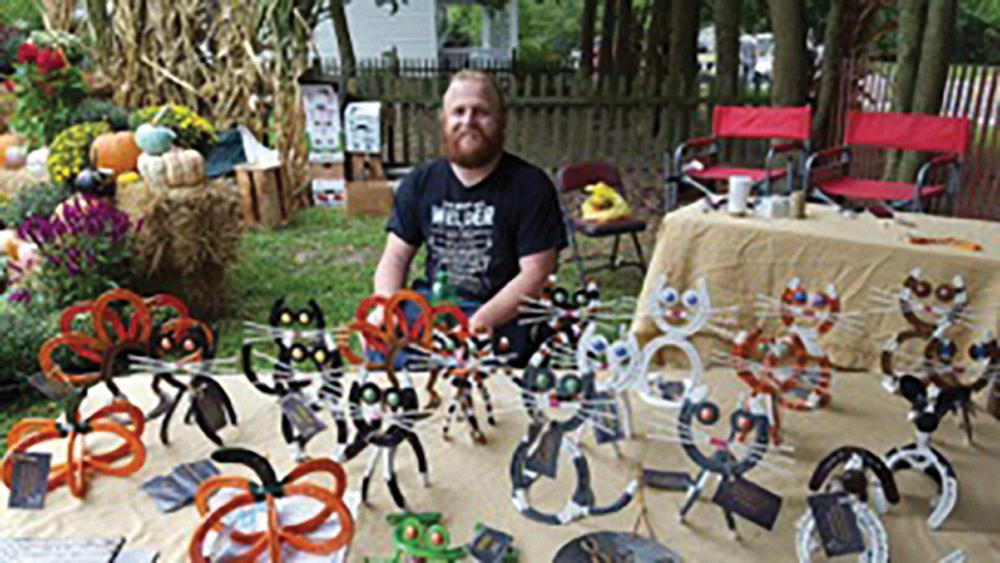
Raised on a farm, metal artist John Eckbold uses a substantial number of horseshoes in his work. No one-trick pony, he also does quite a bit of fabrication work involving machinery, making components and doing repair welding.
If you’ve ever played a game of horseshoes and abided by the official rules of the National Horsehoe Pitchers Association, you have thrown shoes that weigh a maximum of 2 pounds 10 ounces at a stake 40 feet away. If you had to throw a shoe made for a Clydesdale, you’d probably want to bring the stakes in a bit, because Clydesdales have huge hooves and therefore huge shoes, which weigh up to 5 lbs.
None of this is news to John Eckbold, founder of Flying J Metal Arts & Fabrication, Egg Harbor Township, N.J. Having grown up on a farm, he’s well-versed in the details of raising and caring for farm animals. He learned to weld as many farm kids do—by watching others weld—and later took a welding course to learn more about the craft and refine what he already knew. Before long he was welding horseshoes to make artistic pieces, and after asking around at several farms in his area, found himself receiving a steady supply of old horseshoes of many sizes.
One thing led to another, and these days Eckbold does a variety of work, including welding repairs; making replacement components to get broken machines running again; and creating metal sculptures, both on speculation and commission. Because he does quite a bit of repair work on agricultural equipment—and occasionally welds massive Clydesdale horseshoes—he relies on equipment that can handle thick steel (see Figure 1). For welding, this means pushing a substantial amount of current. Eckbold uses a Miller power supply, a Dynasty® 350, which develops up to 350 amps of output for shielded metal arc welding (SMAW, better known as stick) and gas tungsten arc welding (GTAW). For cutting, the main tool is a CNC plasma machine powered by a Hypertherm 80, which can cut steel up to 7/8 in. thick.
His shop is equipped for finishing work too. “We have a sandblasting cabinet and powder-coating oven big enough to walk in,” he said.
This equipment is supplemented by other machines—shears, saws, and so on—for the variety of work that comes his way, and quite a variety it is (see Figure 2). At one end of the spectrum is the structural sort of work in thick metals, projects that need more strength than precision. One such repair involved making seven ripper teeth and welding them to an excavator bucket. At the other end is the delicate, precise sort of work necessary for artistic applications, such as a backdrop for a bar at a local country club, which Eckbold did in a leaf motif.
He doesn’t back away from a challenge when he sees one. When he took on the bucket repair job, he wasn’t quite sure how to model a ripper tooth, but he figured out a fast and practical way to do it. He made a mockup in plywood, spray-painted the prototype on a white background, and then took a photograph of the image. It wasn’t exactly what he needed, but it was close. After uploading the photo to the CNC, he did a little bit of manual programming and was ready to start cutting. On another occasion, he modified his plasma machine’s X-Y table for better access.
“I cut some parts off the table,” he said. Now he’s considering adding to the bed of it to increase its capacity.
Dedicated to Giving
Eckbold’s life is remarkable in that, shortly after his birth, most professionals in the medical establishment predicted that he wouldn’t get nearly this far. He was born 12 weeks early with spina bifida, and although the doctors who cared for him proceeded with a surgery on his spine, they warned his parents that he likely would never see or hear. His journey has been grueling, consisting of more than 30 surgeries in total, but at age 27, he’s already well into a career of great productivity and success.
More remarkable is his generous spirit. Formerly the recipient of others’ generosity regarding his medical costs, Eckbold usually charges little, and often charges nothing, when doing work for those known for making contributions to others, such as hospitals, churches, and miltary veterans. He credits his strong faith in getting to where he is today and guiding him along life’s path.
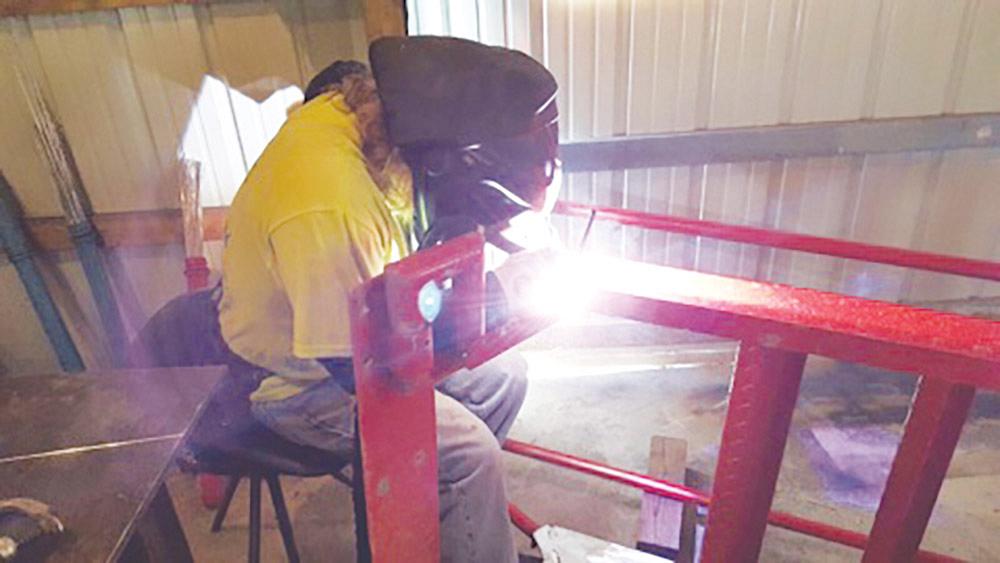
Figure 1
Welding artist and fabricator John Eckbold does all manner of fabrication, including making some components for the Ben Franklin Bridge, which spans the Delaware River between Philadelphia and Camden, N.J.
“If you’re not generous, you’re not grateful,” Eckbold said.
Flying J Metal Arts & Fabrication, 189 Asbury Road, Egg Harbor Township, NJ 08234, 609-653-8862, www.flyingjmetalart.com
About the Author
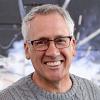
Eric Lundin
2135 Point Blvd
Elgin, IL 60123
815-227-8262
Eric Lundin worked on The Tube & Pipe Journal from 2000 to 2022.
subscribe now
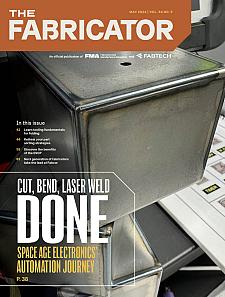
The Fabricator is North America's leading magazine for the metal forming and fabricating industry. The magazine delivers the news, technical articles, and case histories that enable fabricators to do their jobs more efficiently. The Fabricator has served the industry since 1970.
start your free subscription- Stay connected from anywhere
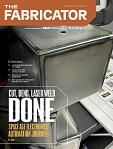
Easily access valuable industry resources now with full access to the digital edition of The Fabricator.
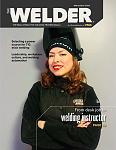
Easily access valuable industry resources now with full access to the digital edition of The Welder.
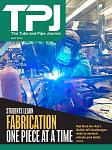
Easily access valuable industry resources now with full access to the digital edition of The Tube and Pipe Journal.
- Podcasting
- Podcast:
- The Fabricator Podcast
- Published:
- 04/16/2024
- Running Time:
- 63:29
In this episode of The Fabricator Podcast, Caleb Chamberlain, co-founder and CEO of OSH Cut, discusses his company’s...
- Industry Events
16th Annual Safety Conference
- April 30 - May 1, 2024
- Elgin,
Pipe and Tube Conference
- May 21 - 22, 2024
- Omaha, NE
World-Class Roll Forming Workshop
- June 5 - 6, 2024
- Louisville, KY
Advanced Laser Application Workshop
- June 25 - 27, 2024
- Novi, MI