- FMA
- The Fabricator
- FABTECH
- Canadian Metalworking
Categories
- Additive Manufacturing
- Aluminum Welding
- Arc Welding
- Assembly and Joining
- Automation and Robotics
- Bending and Forming
- Consumables
- Cutting and Weld Prep
- Electric Vehicles
- En Español
- Finishing
- Hydroforming
- Laser Cutting
- Laser Welding
- Machining
- Manufacturing Software
- Materials Handling
- Metals/Materials
- Oxyfuel Cutting
- Plasma Cutting
- Power Tools
- Punching and Other Holemaking
- Roll Forming
- Safety
- Sawing
- Shearing
- Shop Management
- Testing and Measuring
- Tube and Pipe Fabrication
- Tube and Pipe Production
- Waterjet Cutting
Industry Directory
Webcasts
Podcasts
FAB 40
Advertise
Subscribe
Account Login
Search
Inside Frank’s Aluminum Workshop
How he became an aluminum guru and what he’s learned along the way
- By Amanda Carlson
- July 20, 2016
- Article
- Arc Welding
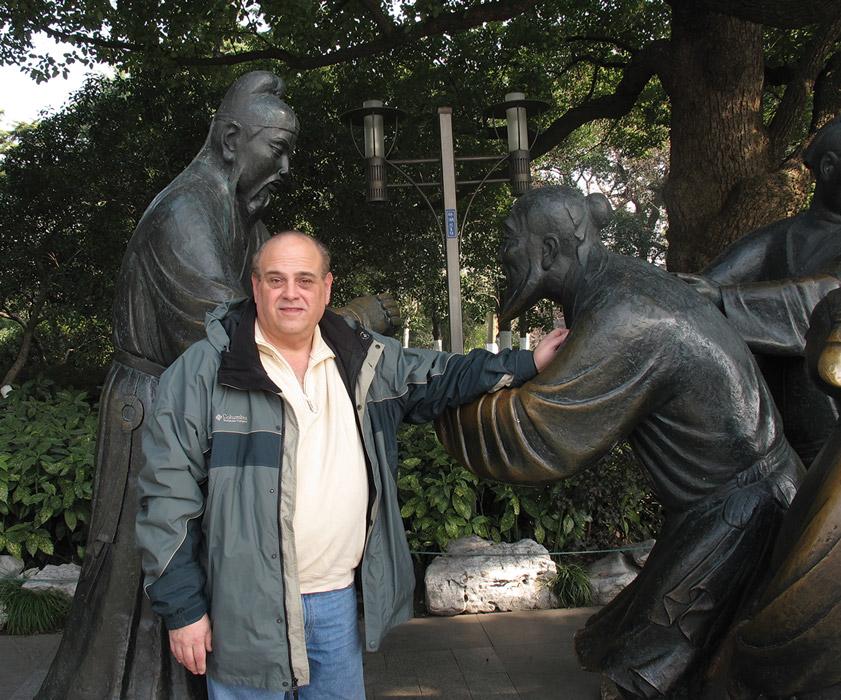
Frank Armao has spent the last 14 years answering your aluminum welding questions. He’s also spent much of that time on the road or living abroad in places like Korea and China. Photos courtesy of Frank Armao.
If you’d have told Frank Armao’s younger self that he’d spend the next 40 years in the welding industry, he probably wouldn’t have believed you. After all, the younger Armao has aspirations of being a metallurgist—certainly not a far cry from welding, but still a very different path.
A snap decision early on in his career led Armao, currently the director of aluminum welding technology at Lincoln Electric Co., Cleveland, down a path that has involved significant world travel—60 countries and counting—allowing him to do and see things most people only find in books or online.
He’s been this magazine’s expert aluminum guru since his first Aluminum Workshop column debuted in the July/August 2002 issue. His 14 years as a contributor makes him the longest-tenured editorial contributor to date. He’s had to juggle his writing responsibilities with those of his regular job and his hectic travel schedule, sometimes hitting send on his latest column from various hotel business offices, on location in exotic cities like Shanghai, or, occasionally, poolside with a tropical drink nearby (I don’t know this for sure about the drink, but it’s always the way I imagined it).
Armao’s extensive aluminum knowledge paired with his loyal readership have made his name almost synonymous with the material he knows just about as well as the back of his hand.
How He Got Here
It was the middle of the Vietnam War when Armao embarked on a career in what he thought would be metallurgy. He interviewed at Westinghouse for two departments, physical metallurgy and welding. Both divisions were hiring, and Armao had his choice between the two. It was, as he said, a pretty easy choice.
“I said something like, ‘I don’t know anything about welding, so I’ll take the physical metallurgy job.’ I worked in the metallurgy group for maybe three months when one day my boss’s boss came over and said that the welding division needed help and that I was being transferred there. That’s how I got started,” he said.
Since then his welding journey took him to an Alcoa location in Pittsburgh where in 1999 he found himself wondering, “What’s next?” So he reached out to a contact in Detroit who floated the possibility of Lincoln Electric needing someone with his skill set. A sent resume, a few phone calls, and an interview later, Armao was a Lincoln Electric employee, where he’s been ever since.
He became active in the AWS D1 Committee—and is still active today—where two interesting opportunities came his way. First, there was the opportunity to become chairman. Second, there was an opportunity to author an aluminum welding column for the AWS Welding Journal. His friend and fellow aluminum expert Tony Anderson of Miller Electric was also being considered for both opportunities.
“It came down to AWS not really wanting another columnist from Lincoln so they gave it to Tony, and we agreed to that between the two of us. He agreed to take the column and I agreed to the chairmanship position of the D1 Committee. At the same time roughly, PWT wanted to start up a column, so since Tony already had a column, I got this one.”
Taming the Aluminum Beast
Since then Armao has answered reader-generated questions about how to choose tungsten type and size for aluminum TIG, which aluminum alloys are weldable and which aren’t, the advantages of a push/pull gun in aluminum MIG, and why 6061 filler doesn’t exist, just to name a few. Aluminum is a completely different animal than steel, and it takes time, trial and error, and experience to learn its nuances. Armao has made a career educating fabricators and welders alike about how to approach aluminum to ensure they avoid critical, costly, and time-consuming mistakes.
The types of question he receives tend to be pretty basic and haven’t deviated much over his 14 years as columnist.“What I’ve seen in the industry is the players change every three or so years. They don’t stay in one place and they don’t stay welding aluminum all that long; well, some do, but usually it’s a couple of years and then they quit and move on and someone else takes their place.
“There’s a lot of sophisticated guys out there, but the kind of questions I get not only through the magazine but generally tend to stay the same. People are still making the same dumb mistakes today that they made 30 or 40 years ago.”
What kind of mistakes, you ask?
“This happens once a week. I’ll get a phone call and it’s usually something like this:
Caller: ‘I just spent a half-million dollars machining all of these aluminum parts to make a super widget, and now I want to go weld them together but I can’t find anyone to give me a recommended filler metal.’
Me: ‘OK, what alloy is it?’
Caller: ‘It’s 7075.’
Me: ‘Ah. Well the reason no one is going to recommend a filler metal for you is because you can’t weld that alloy. You just wasted a half-million dollars.’
“I’m not kidding about that amount—I’ve gotten that phone call a couple of times.”
Looking Back, Looking Ahead
Armao cites inverter technology as one of the most important advancements in welding over the last two decades. The technology, although it got off to a rough start, has stabilized nicely thanks to significant R&D efforts by power source manufacturers, he said.
As for where welding is headed in the future? It all depends on what’s driving technology and what’s happening within the industries that welding serves.
“Right now what is driving aluminum welding technology is the automotive industry. If you say to me, What advances have there been in the automotive industry? we could probably talk for quite a while. One of the big things out there—and again, the automotive industry is driving this—is finding a way to weld aluminum to steel. That’s a hot topic. Some of the more advanced processes, whether it be laser hot wire or something like that, are hot buttons with the bigger guys, not the smaller guys.
“Are there going to be advances in materials? I’m sure there are, but I have a difficult time envisioning what they are. Equipment is going to continue to advance I’m sure too.”
It’s been a wild ride, and if he has one complaint, it’s that he’d like to receive more reader-generated questions.
Just make sure you ask him if something can be welded before you make a $1 million investment.
About the Author
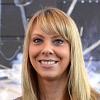
Amanda Carlson
2135 Point Blvd
Elgin, IL 60123
815-227-8260
Amanda Carlson was named as the editor for The WELDER in January 2017. She is responsible for coordinating and writing or editing all of the magazine’s editorial content. Before joining The WELDER, Amanda was a news editor for two years, coordinating and editing all product and industry news items for several publications and thefabricator.com.
About the Publication
subscribe now
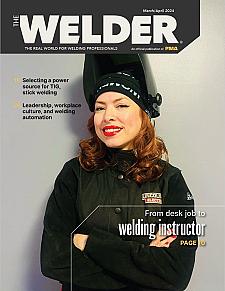
The Welder, formerly known as Practical Welding Today, is a showcase of the real people who make the products we use and work with every day. This magazine has served the welding community in North America well for more than 20 years.
start your free subscription- Stay connected from anywhere
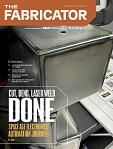
Easily access valuable industry resources now with full access to the digital edition of The Fabricator.
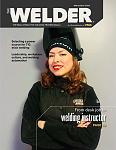
Easily access valuable industry resources now with full access to the digital edition of The Welder.
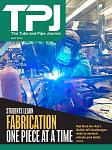
Easily access valuable industry resources now with full access to the digital edition of The Tube and Pipe Journal.
- Podcasting
- Podcast:
- The Fabricator Podcast
- Published:
- 04/16/2024
- Running Time:
- 63:29
In this episode of The Fabricator Podcast, Caleb Chamberlain, co-founder and CEO of OSH Cut, discusses his company’s...
- Industry Events
16th Annual Safety Conference
- April 30 - May 1, 2024
- Elgin,
Pipe and Tube Conference
- May 21 - 22, 2024
- Omaha, NE
World-Class Roll Forming Workshop
- June 5 - 6, 2024
- Louisville, KY
Advanced Laser Application Workshop
- June 25 - 27, 2024
- Novi, MI