- FMA
- The Fabricator
- FABTECH
- Canadian Metalworking
Categories
- Additive Manufacturing
- Aluminum Welding
- Arc Welding
- Assembly and Joining
- Automation and Robotics
- Bending and Forming
- Consumables
- Cutting and Weld Prep
- Electric Vehicles
- En Español
- Finishing
- Hydroforming
- Laser Cutting
- Laser Welding
- Machining
- Manufacturing Software
- Materials Handling
- Metals/Materials
- Oxyfuel Cutting
- Plasma Cutting
- Power Tools
- Punching and Other Holemaking
- Roll Forming
- Safety
- Sawing
- Shearing
- Shop Management
- Testing and Measuring
- Tube and Pipe Fabrication
- Tube and Pipe Production
- Waterjet Cutting
Industry Directory
Webcasts
Podcasts
FAB 40
Advertise
Subscribe
Account Login
Search
Transforming a welding program from zero to hero
Meet Kurt Billsten, 2017 PWTeacher of the Year
- By Amanda Carlson
- July 25, 2017
- Article
- Arc Welding
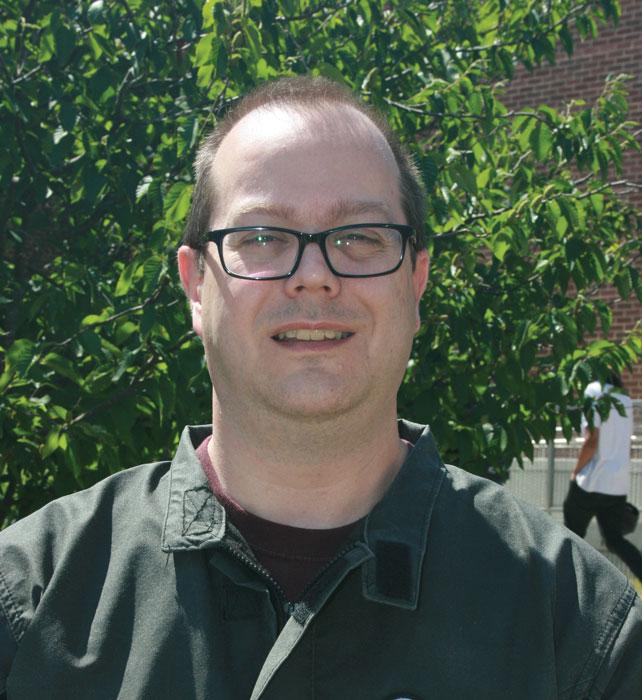
As much as he loved his career as a maintenance and repair welder, Kurt Billsten, the 2017 PWTeacher of the Year, enjoys teaching because it allows him to help individuals create a better life for themselves.
It’s a Thursday afternoon in mid-June and most of the welding students enrolled in summer term at Harper College, Palatine, Ill., are long gone for the weekend. For as robust as the program is currently—more than 500 students strong and growing during the fall and spring terms—it’s tough to believe from the years 2000 to 2003 the school, located in the heart of the northwest Chicago suburbs, had no welding program at all. The transformation is remarkable, and a lot of the credit goes to the man who, before taking the job, never even knew he wanted to teach.
Building a Welding Program (and Teacher) From the Ground Up
Some people say that everything happens for a reason. Well, Billsten had a great reason for enrolling in a gas tungsten arc welding (GTAW) class at Elgin Community College (ECC), Elgin, Ill., while working as a maintenance and repair welder in the construction industry. The company had switched from steel chutes to aluminum chutes, but no one knew how to fix them when they’d crack or break. So Billsten decided to learn how to do it himself. Little did he know that would be the start of something much bigger than himself.
He started welding at a pretty young age to help his dad fix equipment for his business, Billsten Builders. He’d never really had formal training before that GTAW class, but he was experienced in work and life, he had a college degree in business, and was a fairly good welder in his own right. It didn’t take long for other students to gravitate to him as a mentor.
“I’d have other students, younger guys, who seemed like they were lost, both in the welding lab and in life in general. It became a mentorship type thing where I’d work with someone who was a fellow student at the time. They’d go to work, get a job or a promotion, and come back to me and say, ‘Hey, I tried doing what you told me and it worked.’”
Helping others succeed was a feeling unlike any other, and it was an act that didn’t go unnoticed by his instructor at ECC, who asked Billsten to join the faculty as an adjunct instructor after completing just one class.
He was stunned and a little taken aback by the offer, so naturally he ignored it. After all, during his nearly 10 years of welding on construction and heavy equipment, teaching had never even crossed his radar. But after a few years and a few more classes, the opportunity to teach as an adjunct at ECC returned, at which time he accepted.
Around the same time, Harper College’s welding program was dead. Harper’s dean at the time reached out to ECC’s welding instructor to ask for guidance in locating qualified instructors who could help revive the program. That instructor passed on the information to Billsten, who agreed to a visit.
His first impression of the lab wasn’t great; he called it a dungeon, but he saw an opportunity to help students, even if there were only a few, looking for training. He agreed to join the program as a part-time adjunct to teach one class. It was small—only nine students—but he absolutely loved it, and so did they. So much so that all nine of those students wanted to take more classes. The only problem was there weren’t any; that basic welding class was it in terms of curriculum. So Billsten spoke to the dean, who explained to him that he, Billsten, would need to create a curriculum for what he had in mind.
Leaning on his industry experience, he first wrote a 16-credit-hour welding certificate and maintenance welding class, addressing needs that he encountered daily on the job, and things progressed from there.
A few years later nine students turned into 100. When it became clear that he was becoming more attached to his work at Harper, Billsten left his teaching position at ECC and focused instead on continuing to build Harper’s program while still juggling his full-time welding job. When a full-time position became available at Harper in 2007, Billsten took it.

Billsten stands in front of the FMA Metal Fabrication Lab, which opened in 2016. The lab helps Harper College prepare students for careers in advanced manufacturing.
“It was a tough decision, but it was easier in the sense that I had to make it. I knew enough about the construction industry that I felt confident that I could always go back into it if I needed to. I realized that teaching was what I really liked to do.”
Starting from scratch was, of course, difficult, but he relished the idea of having ultimate decision-making ability over the direction of the program, the curriculum, the culture, and the staffing.
“I could come in, start over, and do things the way I wanted to. When you have a program that’s been around for 30 or 40 years, there’s not a lot you can change about it. It’s so difficult to change the lab, the curriculum, or even the culture. Coming to Harper was like coming in fresh. I had no expectations, and I knew I could try anything.”
Billsten had designed a program with everything he knew about what local industry needed in mind. He recruited adjunct instructors from industry who had different strengths and specialties.
“That was accidentally by design because everyone I knew was from industry. I didn’t really know any educators. So when we were recruiting and hiring people, that’s where I gravitated toward, and I found they have made the best educators for the technical trades.”
He called local employers soliciting feedback. He contacted equipment manufacturers and asked for equipment donations. He pushed for a larger, cleaner welding lab. His legwork, combined with a grant from the Illinois Network for Advanced Manufacturing, gave the program another boost with the addition of advanced manufacturing.
The program now includes maintenance technology, welding technology, and manufacturing technology, each with degree and certificate offerings. Billsten serves as department coordinator for all three, overseeing 17 instructors and 400 students with room to grow.
As a department coordinator, Billsten teaches a full course load but also focuses on purchasing materials, maintaining equipment, fostering relationships with local industry, maintaining a qualified staff, marketing, counseling students, and ensuring the program is meeting the needs of local industry.
Generating Interest
How do you attract young people to welding and fabrication, and how do you keep them interested? It’s the million-dollar question that every welding school must answer. It starts when students are young, which is why the college hosts middle school tours at least once a week. When students tour the welding and fabrication lab, they get to learn about metalworking and see the processes and equipment up close.
Billsten said if young people don’t see something that’s fun and exciting, then they aren’t interested. Students no longer choose a career path based on how much money they will make; instead, they choose a career path because it’s something they enjoy.
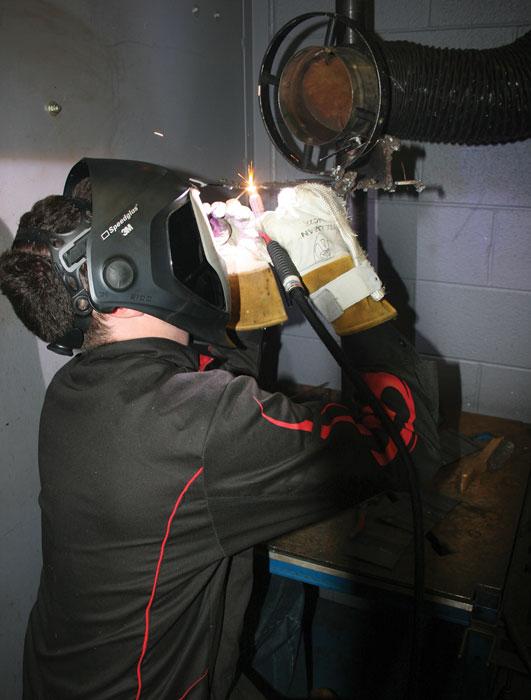
Billsten and his staff have created a tight-knit family atmosphere that builds accountability and confidence.
“We want our shop culture to be close-knit and fun, like a family. Everyone here works together. Here, everyone is valued. I’ve toured other schools that seem to have a very rigid culture where everything had to be a certain way. I’m trying to look at it from industry. ‘What is important to me if I was the one hiring them? What is important to me if I were their supervisor?’ I want them to be on time, to be sober, so it’s those types of things plus safety that we stress. And, of course, doing the best that they can always.”
Keeping students motivated is key. The program gets students out of the classroom doing real work, which hopefully gets them excited to continue to learn more. One thing Billsten said helps is the internship partnership the school has with local companies. Students typically begin an internship at the end of their first semester and there are a few reasons for this. First, at this point they’ll have just enough skill to be useful to the company they are interning with. Second, it’s still early on enough in their education for students to alter or change focuses based on what they learn and see in their internship.
Internships offer valuable life experience as well.
“I’ve had students who have come into the program with a bad attitude. They had the skills, but once they got the opportunity to work for a real company, they changed. I had one student that really liked the company he was interning at and wanted to be hired on full time, but he just had a bad attitude and got fired. It was that wakeup call he needed and it came early enough for him to make a change. That same student came back to school, took classes for another semester, applied for another internship, and ended up being hired full time.”
Classroom learning is important, too, and Billsten and the other instructors make sure to create realistic scenarios that students must work through. The more the students advance, the more they must be able to do. Things like setting up their machines, choosing and installing their consumables, using the right shielding gas blend, pulling material from the warehouse and cutting it to size. They do these tasks through written prints and lists.
“We’ll break a band on a band saw and the students will have to get a new band saw blade off the roll, cut it, weld it, and it’ll take them a bunch of times. One of us instructors could go out and do it really quick, but the students won’t learn anything that way. It might take three of them a half hour to do, but when they’re done, they’ll know how to weld band saw blades.”
The feedback he gets from companies that have hired his students is they are impressed by the nonwelding skills that they possess.
More Than Welding in the Golden Corridor
Harper College is located in the heart of Chicagoland’s Golden Corridor, a 26-mile stretch of Interstate 90 between Elgin, Ill., and O’Hare International Airport, home to a bevy of metal fabricators and advanced manufacturing firms, according to a report from Chicagoland Metropolitan Agency for Planning.
Calling home to such a hotbed of advanced manufacturing required Billsten and his staff to answer two questions: What do these employers need? How do we prepare students to fill this need? It was clear that while area employers needed individuals who could weld, they also needed individuals who could fabricate.
“When I go and talk to shops, welding is just one tiny piece of getting a product to go to market. You used to see people hired just to weld and they couldn’t do anything else at all. When I talk to employers now, they want someone who can weld, read the print, order materials, maybe even do a cost estimate.”
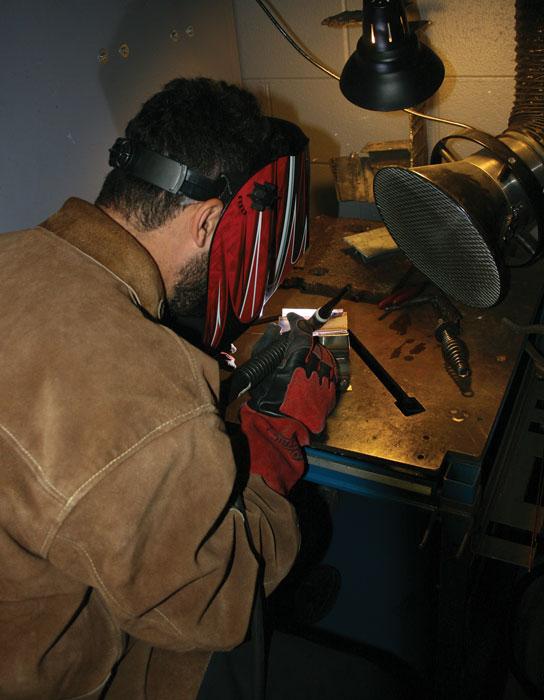
As students advance, they are expected to pull material and cut it to size, set up their machines, choose and install consumables, and set the appropriate shielding gas blend through written prints and lists. Billsten wants his lab to resemble a shop floor as much as possible.
That meant adding fabrication into the mix, expanding the lab’s overall footprint, and acquiring the type of fabricating equipment area employers were using in-house.
Billsten was active with the Fabricators & Manufacturers Association (FMA) through his involvement on the association’s Certified Education Council. Through the council he met Jim Warren, FMA’s education director, and the two struck up a conversation at FABTECH® in 2013. FMA had been challenged by its board of directors to create a workforce solution that would benefit its member companies.
That conversation laid the groundwork for the two institutions to collaborate on a metal fabrication lab. FMA pledged $500,000 over five years—$400,000 to help fund the program and $100,000 to provide financial assistance to students who qualified for the Harper Promise Scholarship, which guarantees local students up to two years of free tuition for earning good grades, performing community service, and achieving good attendance, among other criteria. That grant money, along with the relationships FMA had with machine tool manufacturers, helped
secure the high-end fabricating equipment needed to run a full-fledged advanced manufacturing program. Construction crews broke ground in mid-2015 and the facility opened less than a year later.
“I think we still would have had fabrication in here but not to the extent that we are doing now. It was the high-end equipment that I didn’t foresee being able to get in-house had it not been for the partnership with FMA.”
Today the state-of-the-art fabrication lab boasts equipment donated by Mitsubishi/MC Machinery Systems, Miller Electric, Miller Automation, Trilogy, ESAB Welding & Cutting Products, Wisco, TRUMPF, Haas, and Amada, to name a few. Enrollment has grown between 20 and 30 percent since the fabrication program was added, with room to grow. While separate certificates are offered for laser or press brake operation, Billsten said they did offer a stand-alone course this summer for those two pieces of equipment, which filled immediately.
“The welding students, most people are usually new to it, with some people taking specific classes like I did. But with the fabrication classes, you might have someone who’s gone through the welding program or even has experience, or you may have someone who comes in because they keep seeing help wanted ads for press brake operators. So we don’t have a prerequisite for that class because we want people to be able to come right in.”
The fabrication lab has served as a nice recruiting tool for prospective students and their parents. High-end equipment has a way of bringing legitimacy to a program.
“When people come in and see the press brake and laser, they figure if we have that kind of investment in here, then we must know what we’re doing with the other stuff.
“We’ve had people come through for a tour who have enrolled and paid the out-of-district rate to be here just because of what we have in the lab. And then they find out about the other things we have, like the job placement service, etc. Students like being here because they are exposed to a lot of equipment. They like the bigger space, the projects, it’s just like the real world,” Billsten said.
A Legacy of Helping Others
Growing from nine students to 400, adding fabrication capabilities, and turning the environment from dungeon-like to modern-day industrial is a legacy in and of itself. But it has and always will be about helping others find their path.
George Leddy, 32, didn’t truly find himself until he enrolled in the welding program at Harper College in August 2013. He’d never done any type of welding or metalworking in his life but took an interest in it after hearing friends talk about it.
“I tried other colleges and other things in life, but the welding program is something I really connected with,” Leddy explained.
He quickly fell in love with welding, working with his hands, and being in the shop environment. His teachers noticed and asked him to be a student aid. He found any excuse to work in the shop between classes, and then Billsten presented him with another opportunity.
“Kurt asked me what I knew about machining. That was intimidating because my math skills just weren’t there. I told him I thought it looked all right, so he told me to take a few classes and see if I liked it. So I did and I fell in love with it,” Leddy said.
He has thrown himself into just about every class he can take and was recently hired to be the pro-tech for the manufacturing program. Though he’s interested in pursuing a job in industry someday, perhaps something having to do with 5-axis CNC prototyping, he said he’d jump at the chance to join the ranks at Harper full time and give back.
“That place has totally changed my life. My GPA … it’s funny, about a year into the program I got a letter from the president saying that I was no longer on academic probation. My GPA was a one-something and now it’s a 3.4. I fell in love with what I was doing and with being there. Kurt Billsten is without a doubt the best boss that I’ve ever had. He has just done a lot for me and been there for me. I’ve never met anyone in my life who always remembers who somebody is no matter what is going on. He’s the kind of people we need leading the industry. People that care about those who work for him.”
And for Billsten, a welder at heart, he still misses the satisfaction of seeing a project through from start to finish. But in many ways he is still doing that, only now the projects aren’t metal railings or heavy equipment repairs, they’re people.
About the Author
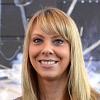
Amanda Carlson
2135 Point Blvd
Elgin, IL 60123
815-227-8260
Amanda Carlson was named as the editor for The WELDER in January 2017. She is responsible for coordinating and writing or editing all of the magazine’s editorial content. Before joining The WELDER, Amanda was a news editor for two years, coordinating and editing all product and industry news items for several publications and thefabricator.com.
About the Publication
subscribe now
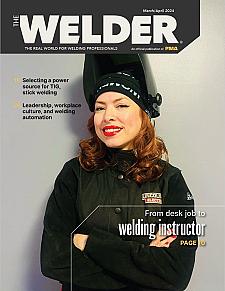
The Welder, formerly known as Practical Welding Today, is a showcase of the real people who make the products we use and work with every day. This magazine has served the welding community in North America well for more than 20 years.
start your free subscription- Stay connected from anywhere
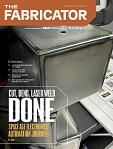
Easily access valuable industry resources now with full access to the digital edition of The Fabricator.
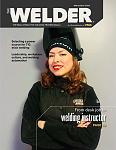
Easily access valuable industry resources now with full access to the digital edition of The Welder.
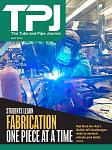
Easily access valuable industry resources now with full access to the digital edition of The Tube and Pipe Journal.
- Podcasting
- Podcast:
- The Fabricator Podcast
- Published:
- 04/16/2024
- Running Time:
- 63:29
In this episode of The Fabricator Podcast, Caleb Chamberlain, co-founder and CEO of OSH Cut, discusses his company’s...
- Industry Events
16th Annual Safety Conference
- April 30 - May 1, 2024
- Elgin,
Pipe and Tube Conference
- May 21 - 22, 2024
- Omaha, NE
World-Class Roll Forming Workshop
- June 5 - 6, 2024
- Louisville, KY
Advanced Laser Application Workshop
- June 25 - 27, 2024
- Novi, MI