Independent Consultant
- FMA
- The Fabricator
- FABTECH
- Canadian Metalworking
Categories
- Additive Manufacturing
- Aluminum Welding
- Arc Welding
- Assembly and Joining
- Automation and Robotics
- Bending and Forming
- Consumables
- Cutting and Weld Prep
- Electric Vehicles
- En Español
- Finishing
- Hydroforming
- Laser Cutting
- Laser Welding
- Machining
- Manufacturing Software
- Materials Handling
- Metals/Materials
- Oxyfuel Cutting
- Plasma Cutting
- Power Tools
- Punching and Other Holemaking
- Roll Forming
- Safety
- Sawing
- Shearing
- Shop Management
- Testing and Measuring
- Tube and Pipe Fabrication
- Tube and Pipe Production
- Waterjet Cutting
Industry Directory
Webcasts
Podcasts
FAB 40
Advertise
Subscribe
Account Login
Search
La gente y los procesos detrás de poka-yoke
- By Gary Conner
- April 6, 2015
- Article
- Assembly and Joining
En muchos de nuestros talleres mostramos un video de 30 segundos de gente que está pasando varias pelotas hacia atrás y hacia adelante. Cuando se les indica que vean y cuenten el número de veces que un grupo de gente con camisa blanca transfiere la pelota, los participantes del taller usualmente tienen un acalorado debate sobre el número real de transferencias de pelotas. Sin embargo, lo más sorprendente es que casi todos pasan por alto el hecho de que un enorme gorila pasa por la escena, se golpea el pecho y desaparece con toda tranquilidad.
Los humanos no son buenos en multitareas ni inspeccionando defectos. El propósito de técnicas Six Sigma como poka-yoke (a prueba de errores) es eliminar la necesidad de intervención o inspección por parte del operador. Construir un proceso libre de variación casi elimina la necesidad de buscar un defecto.
Un mecanismo a prueba de errores requiere más que simplemente conocer sobre Six Sigma y otros métodos de mejora continua. Ejemplo: durante la década de 1980, el equipo de dirección de nuestro taller de chapa metálica de precisión asistió con frecuencia a conferencias y talleres en un esfuerzo por instruirse (y por extensión instruirnos a los demás) sobre la mejora continua. Tuvimos a la mano un tsunami de estrategias y libros, que promovían todo desde JIT (justo a tiempo), el Sistema de Producción Toyota, filosofías de reingeniería en los negocios y otras teorías de diversa índole. Cada seis meses los directivos de la compañía regresaban de una conferencia trayendo brazadas de nuevos libros, y declarando que habían descubierto “la respuesta”, el “Magic Bullet” que prometía convertir nuestra compañía en el estándar con el que otras compañías serían medidas en las décadas futuras (vea la Figura 1).
Déjeme que le cuente, fue algo frustrante para mí y para mi equipo. Aun cuando su corazón estaba en el lugar correcto, es como si estuviéramos empezando a cada rato. Después de una plática muy seria con los directivos de la compañía, coincidimos en que necesitábamos distinguir entre herramientas de mejora y objetivos. Las herramientas vendrán y se irán, pero los objetivos deben permanecer intactos. Queríamos ser el proveedor de chapa metálica preferido de nuestros clientes, y ese objetivo no cambiaría sólo porque alguien escribiera un nuevo libro o descubriera una nueva técnica o herramienta.
Manufactura esbelta (lean), Six Sigma y demás disciplinas de mejora son simplemente un conjunto de herramientas, y no todas las herramientas se usan a diario. Tenemos la obligación de enseñar a nuestros equipos cómo identificar un problema, y luego ser capaces de aplicar la técnica de mejora continua correcta para reparar o regresar el proceso a una condición deseada.
Con frecuencia se piensa incorrectamente que la manufactura esbelta es un subconjunto de Six Sigma o viceversa. Algunas disciplinas Six Sigma pasan por alto el valor de la manufactura esbelta, y a veces los proponentes de la manufactura esbelta minimizan la importancia de Six Sigma. Sí, manufactura esbelta y Six Sigma son diferentes, pero pueden complementarse en lugar de contradecirse o competir entre sí.
Con los años, los desempeños de clase mundial y la mejora continua en nuestros ambientes de manufactura han dejado de ser opcionales. No se trata de ir por esta o por aquella metodología de mejora continua. Se trata de elegir las herramientas que funcionen, y aprender a usarlas correctamente. Al final de cuentas, usted puede usar herramientas de mejora, incluyendo poka-yoke, para mejorar no sólo los procesos de la compañía, sino también su cultura. Todo esfuerzo de mejora realmente sostenible requiere ambos.
Los procesos detrás de los mecanismos a prueba y error
Considere una compañía que fabrica y ensambla computadoras centrales de 3 pies (91 cm) de ancho por 4 pies (122 cm) de profundidad por 6 pies (183 cm) de alto. En un punto este fabricante estaba teniendo 24,000 defectos por millón de oportunidades (DPMO) en su departamento de ensamble. La mayoría de los defectos estaban relacionados con los 450 remaches ciegos que se estaban usando en el subensamble y en el proceso de ensamble final.
Si alguien olvidaba un solo remache ciego, no se vería sino hasta varios meses después durante la instalación de alguna guía de tarjeta por el departamento de IT del usuario final. En algunos casos, la compañía tenía que mandar a alguien a recorrer medio mundo para desensam-blar el enorme gabinete para tener acceso e instalar un remache faltante. Esto le costaba a la compañía alrededor de $400,000 al año.
Se reunió un equipo kaizen (cambio positivo) para examinar sus procesos y hacer lluvia de ideas sobre formas de minimizar o eliminar la probabilidad de que alguien pasara por alto un remache, tornillo, cinturón u otro componente electromecánico. El objetivo del equipo era reducir la cifra DPMO a menos de 2,400. Una organización operando bajo Six Sigma no tendría más de 3.4 defectos por millón.
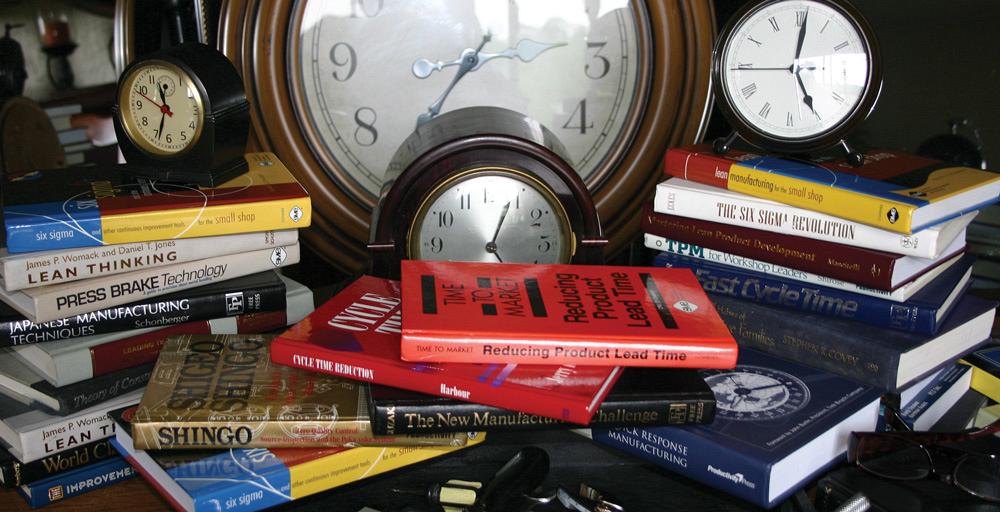
Figura 1
En sí mismas, las
metodologías de mejora—como se describe
en infi nidad de libros—son sólo
herramientas. Para ser efectivas, necesitan
ser elegidas con cuidado y usadas en
la forma correcta.
Una solución adoptada fue proporcionar al equipo de ensamble un juego de charolas de remaches ciegos precargados. Esto significaba que los remaches ciegos eran presentados a un ángulo preciso, repetible y ergonómicamente amigable. Las charolas estaban dispuestas en la secuencia exacta en la que se iban a instalar, creando una mejor práctica y un método de trabajo estandarizado.
El número de remaches ciegos en el juego coincidía exactamente con el número requerido para el subensamble. Si quedaba alguno, el equipo de ensamble sabía que necesitaban llevar a cabo una acción correctiva. Vieron una mejora significativa y, como resultado de este proyecto, usaron variaciones de esta estrategia en muchas otras áreas de en-samble.
De manera similar, un miembro del equipo en Madras, Keith Manufacturing, ubicada en Ore., productor de pasillos para la industria camionera, vino con un tablero blanco pequeño dispuesto como un tablero de siluetas para ayudar a hacer a prueba de fallas el ensamble de colectores hidráulicos de fluido. Si faltaba un anillo O o una válvula de retención durante el ensamble, un técnico de campo tendría que volar a North Dakota en pleno invierno para tirarse de espalda sobre una carretera cubierta de hielo y a-rrastrarse debajo de un tráiler de 53 pies (16 m) para desensamblar y reparar un sistema hidráulico inoperante. Hace una década, un evento así era algo común. No hubo inspección que resolviera este problema. Sin embargo, el desarrollo de este dispositivo poka-yoke—un simple tablero de siluetas- lo ha eliminado por completo.
Como prueba, regresemos al párrafo anterior y contemos cuántas veces aparece la letra “m”. La mayoría de la gente cuenta 14 o 15-pero en realidad hay 20. No somos buenos inspeccionando. Por eso debemos encontrar formas de sacar el elemento humano del proceso de inspección. Quite variación y variables, y eliminará defectos.
Considere otro ejemplo, una compañía de fundición de precisión que estaba lidiando con una tasa de desperdicio del 6 por ciento. El fabricante hace varios productos para la industria médica, incluyendo rodillas y caderas artificiales, junto con infinidad de componentes aeroespaciales y comerciales. Aun cuando no se trata de un taller de chapa metálica, la historia de la compañía muestra la necesidad de examinar cada proceso para identificar y eliminar la variación.
El taller tenía un proceso que gene-raba seis defectos de cada 100 moldes. Los moldes desarrollarían fisuras pequeñas que eran detectables sólo cuando fallaban después de verter en ellos metal fundido. Tener cobalto fundido a 2,700 grados F (1482 grados C) saliendo de un molde agrietado hacia el piso (en realidad hacia un foso de arena) era un riesgo sustancial de seguridad, así como un pro-blema de desperdicio de varios millones de dólares. A $35 millones de ventas anuales, el taller estaba tirando alrededor de $2.1 millones en productos. Los defectos requerían que los empleados quitaran los rasguños de los moldes, lo que por supuesto aumentaba significativamente los tiempos de entrega.
Después de escudriñar el proceso, el equipo kaizen identificó 150 variables de proceso, y descubrieron seis relacionadas con dos tipos diferentes de cera que se estaban usando para crear un molde. Se usaba cera virgen para el componente en sí, mientras que se usaba cera recuperada para proporcionar vías para que el metal fundido se moviera a través del molde y entrara a la cavidad del componente.
Resultó que la cera virgen se fundía a una temperatura inferior que la cera recuperada, la cual tiende a endurecer después de ciclos repetidos de fusión. Debido a la colocación requerida del molde en la autoclave, la diferencia en la temperatura de fusión permitía a la cera virgen fundirse, expandirse y a veces fracturar el molde mucho antes de que la cera recuperada empezara a fundirse.
La compañía no quería afrontar el costo de usar cera virgen para todo el molde, por lo que el equipo probó y comprobó que implementar una ventilación en cada molde permitía a la cera virgen expandirse mientras que daba tiempo suficiente para fundir la cera recuperada.
He aquí el punto clave: en lugar de tratar de desarrollar un método de detectar o inspeccionar la existencia de defectos, el equipo diseñó un proceso para eliminar fisuras. El problema se resolvió y no se requirieron más inspecciones. Esto produjo ahorros anuales de casi $3 millones, y por si fuera poco, la compañía obtuvo una mejora significativa en seguridad.
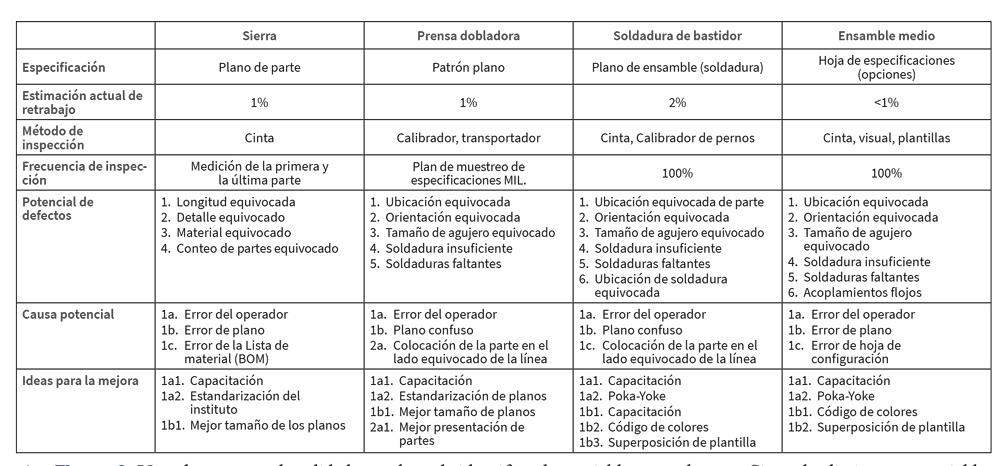
Figura 2
Usando un mapa de calidad, usted puede identificar las variables en cada paso. Si puede eliminar una variable,
ya no tendrá que buscar el defecto relacionado con esa variable.
Como en fundición de precisión, maquinado y cualquier otra operación de manufactura, la fabricación de chapa metálica con precisión tiene muchas variables: condición del material, tipo de material, condición de las herramientas, método de configuración, método de manejo, configuración de la máquina, y así sucesivamente. Cuando usted hace mapas de flujo de valor, también puede hacer un ejercicio de mapas de calidad. No es raro identificar de 100 a 200 varia-bles en un proceso típico de 10-15 pasos: cizalla, punzón, láser, grano, hardware, forma, soldadura de puntos, soldadura, pintura, ensamble, y así sucesivamente. Usando un mapa de calidad usted puede identificar las variables en cada paso. Si puede eliminar una variable, ya no tendrá que buscar el defecto relacionado con esa variable (vea la Figura 2).
Cuestión de cultura
Hace unos siete años, Alvin Elbert, dueño de A.R.E. Manufacturing, en Newberg, Ore., estaba frustrado con las actitudes arrogantes y falta de lealtad entre los solicitantes de empleos experimentados. Así que decidió explorar una alternativa. Sacar la magia negra del proceso y hacer más fácil la capacitación de nuevos empleados. Actualmente evita contratar maquinistas experimentados con mala actitud. Muchos contratados nuevos son recién egresados de preparatoria.
Por supuesto, Elbert no se despertó un día y decidió cambiar sus prácticas de contratación. La decisión vino después de varios años de mejora continua sostenida. En 2005, era muy probable que A.R.E. ampliara su edificio actual a un costo de más de $1 millón. Gastando $300,000 en estandarización de herramientas, los gerentes encontraron la productividad y la capacidad que necesitaban—sin ampliar el edificio.
Un beneficio inesperado de sus esfuerzos de estandarización y simplificación fue que ellos de manera no intencionada desarrollaron un proceso a prueba de errores. Esto les permite a los operadores enfocarse en el trabajo productivo y no en el llenado sin fin de gráficas de comportamiento, y eliminó la necesidad de escrutinio constante.
De acuerdo con Elbert, después de unos tres años de esfuerzos de mejora, se estabilizaron y pronto vieron que para llegar al siguiente nivel de desempeño, necesitaban atender el elemento humano. Trajeron gente de capacitación para ayudar a la administración de A.R.E. a manejar al personal de manera más efectiva. El simple hecho de que Elbert y unos cuantos más tuvieran años de experiencia no significaba necesariamente que estuvieran altamente calificados para dirigir sus equipos.
La evidencia demuestra que tomaron la decisión correcta. Su tasa de rotación del 2008 fue del 30 por ciento; ahora es menor al 7 por ciento. Gastan un poco más de tiempo en la oficina, entrevis-tando gente no sólo por su experiencia como maquinista, sino por sus aptitudes matemáticas y mecánicas. Además implementaron un programa de capacita-ción en manufactura esbelta en toda lacompañía. Se requiere que cada empleado participe en más de 40 horas de capaci-tación en manufactura de clase mundial, un programa desarrollado por Megan, la hija de Alvin. La capacitación ha ganado premios y ha sido reconocida por el estado de Oregon por su excelencia.
Piénselo: todo este reconocimiento va a un taller donde los recién contratados a veces son recién egresados de preparatoria y tienen poca o nula experiencia en maquinado. Estandarizando el herramental y documentando las mejores prácticas, programando a una carga de herramienta estándar, y preacomodando herramientas para cada uno de los cientos de combinaciones de trabajos que podrían hacer en un día dado, Elbert ha podido extraer el conocimiento tribal del proceso (vea la Figura 3). Un trabajo que solía requerir un maquinista con tres o cuatro años de experiencia, ahora puede ser hecho por alguien con tres o cuatro meses de capacitación.
Esto resalta un elemento importante de los mecanismos a prueba de error, así como de la mejora continua en general. Un taller de chapa metálica puede desarrollar tableros de siluetas; cortar pestañas y ranuras de forma que ambos componentes formados puedan ir juntos de una sola manera; desarrollar secuencias de doblez de forma que sea físicamente imposible doblar una pestaña hacia atrás; y las ideas siguen y siguen.
Sin embargo, ningún proceso a prueba de error puede superar malas actitudes o dirección no calificada. Mediante la estandarización, los mecanismos a prueba de error y una fuerte capacitación, A.R.E. facilitó la capacitación y amplió su reserva de talento potencial. La compañía además brindó capacitación a sus directivos.
Los mecanismos a prueba de error y la estandarización son herramientas de mejora continua que pueden abrir infinidad de oportunidades, y no sólo en eficiencia de la manufactura. En un sentido, pueden ser sólo una chispa pequeña (entre muchas otras) que puede encender el cambio cultural positivo.
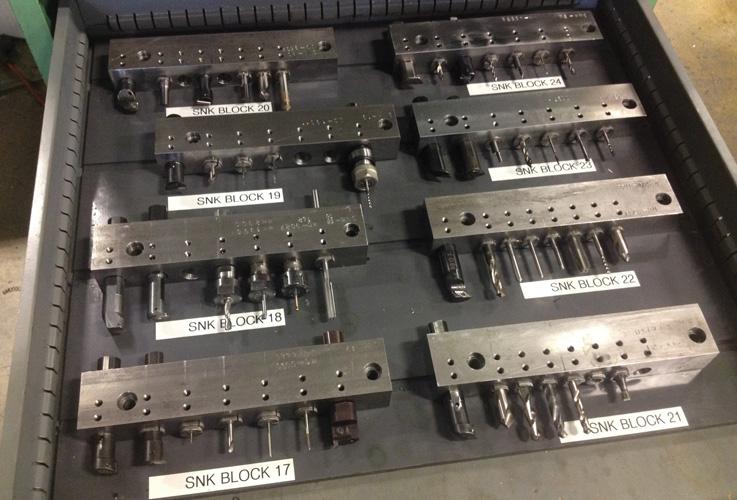
Figura 13
Una buena organización
y prácticas bien documentadas, junto
con una capacitación integral, permitieron
a A.R.E. Manufacturing tener
éxito al contratar nuevos empleados
con poca o nula experiencia técnica.
¿ Quién es Emma Dias?
Por Marcel SchaererEsta historia nos da una idea de como vemos y percibimos el mundo que nos rodea, y de como cada uno de nosotros, a través de nuestras lentes únicas, interpretamos la información presentada en los entornos de trabajo. Resalta la importancia de reflexionar sobre cuestiones de diversidad cultural, idioma y comunicación en el lugar de trabajo.
Mientras trabajaba con un cliente en un proyecto relativamente nuevo, asistí a una presentación típica de MSDS (hojas de datos de seguridad de materiales, ahora conocidas como SDSs, u hojas de datos de seguridad) a cargo de un gerente departamental. Después de la presentación, Rosa, quien trabajaba en el departamento de ensamble, se me acercó y cortésmente me pidió que habláramos en privado.
Nos alejamos del grupo y con curiosidad me preguntó, “Señor, who is Emma Dias? (Señor, ¿quien es Emma Dias?)
La miré y le dije, “What do you mean by Emma Dias?” (¿Qué quiere decir con Emma Dias?)
Ella lo dijo de nuevo. “I just want to know who Emma Dias is” (Sólo quiero saber quién es Emma Dias). Se detuvo, me vio de nuevo y dijo, “Emma Dias, the lady who is sometimes mentioned during our safety meetings” (Emma Dias, la señora que se menciona a veces durante nuestras juntas de seguridad).
De repente me di cuenta de lo que me estaba preguntando. Emma Dias era MSDS (que se pronuncia en inglés “Em Es Di Es”). Ella se refería al acrónimo MSDS que había escuchado—Em Es Di Es, Em Es Di Es (lentamente), Em Es Di Es (más lentamente)—y que con el tiempo en su mente se convirtió en Emma Dias. Ella lo escuchaba una y otra vez sin asociar los sonidos con las siglas MSDS. Ella pensaba en Emma Dias, una persona que de alguna forma tenía algo que ver con productos químicos y seguridad.
No podemos asumir que todos escuchan e interpretan la información de la misma manera, especialmente en ambientes multiculturales donde se hablan varios idiomas. Nuestra productividad, la robustez de nuestra seguridad y de nuestros sistemas de calidad está determinada por el nivel de entendimiento de los miembros de nuestro equipo.
Marcel Schaerer es presidente y dueño de International Professional Development Services, 5775 S. Fort Apache Road, Suite 100, Las Vegas, NV 89148, 702-930-8036, www.ipdstraining.com.
About the Author
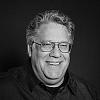
Gary Conner
About the Publication
subscribe now
FMA Communications ha introducido al mercado la edición en Español de la revista The Fabricator. Esta versión consiste del mismo tipo de artículos técnicos y sección de lanzamientos de nuevos productos que actualmente presentan el personal de primera categoría de Fabricator en Inglés.
start your free subscription- Podcasting
- Podcast:
- The Fabricator Podcast
- Published:
- 04/16/2024
- Running Time:
- 63:29
In this episode of The Fabricator Podcast, Caleb Chamberlain, co-founder and CEO of OSH Cut, discusses his company’s...
- Trending Articles
Los operadores de prensa dobladora inexpertos hacen indispensable el repensar la seguridad
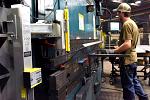
Prescripción para la reducción del desperdicio: arreglo esbelto de las instalaciones
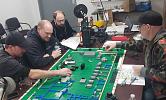
Máquina de corte por láser diseñada para el mercado mexicano
La máquina procesadora de placas crea biseles complejos en un solo corte
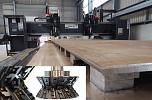
El software guía a los soldadores a través de instrucciones de trabajo
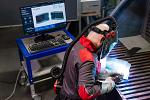
- Industry Events
16th Annual Safety Conference
- April 30 - May 1, 2024
- Elgin,
Pipe and Tube Conference
- May 21 - 22, 2024
- Omaha, NE
World-Class Roll Forming Workshop
- June 5 - 6, 2024
- Louisville, KY
Advanced Laser Application Workshop
- June 25 - 27, 2024
- Novi, MI