- FMA
- The Fabricator
- FABTECH
- Canadian Metalworking
Categories
- Additive Manufacturing
- Aluminum Welding
- Arc Welding
- Assembly and Joining
- Automation and Robotics
- Bending and Forming
- Consumables
- Cutting and Weld Prep
- Electric Vehicles
- En Español
- Finishing
- Hydroforming
- Laser Cutting
- Laser Welding
- Machining
- Manufacturing Software
- Materials Handling
- Metals/Materials
- Oxyfuel Cutting
- Plasma Cutting
- Power Tools
- Punching and Other Holemaking
- Roll Forming
- Safety
- Sawing
- Shearing
- Shop Management
- Testing and Measuring
- Tube and Pipe Fabrication
- Tube and Pipe Production
- Waterjet Cutting
Industry Directory
Webcasts
Podcasts
FAB 40
Advertise
Subscribe
Account Login
Search
What happens when a nonwelder meets a laser?
6 questions for Tracy Stenger, laser welding machine operator
- By Amanda Carlson
- January 27, 2016
- Article
- Assembly and Joining
The path to becoming a laser welding machine operator had nothing to do with welding for Tracy Stenger of Superior Joining Technologies, Machesney Park, Ill. The mechanical design engineer by trade had never welded a day in his life until six years ago when he was hired by the company.
Just 10 years earlier, Stenger was in business for himself as a contractor for companies around Rockford, Ill., including Thom and Teresa Shelow at Superior Joining Technologies. But like for most small businesses at that time, the dismal economy wreaked havoc, leaving Stenger light on work.
It was then, out of the blue, that he got a phone call from the Shelows, who were in a pinch and looking to hire someone to operate their brand-new TRUMPF TruLaser 7040, a 5,000-watt, 5-axis CO2 laser welding machine. The operator they had initially hired decided he didn’t want the job.
“They asked me if I wanted to learn how to do it. So I went in a couple of hours before the training started and have been here ever since. I never thought I’d be here a year, much less six years.
Since then Stenger has found his new position to be fulfilling and challenging. But what about his skill set made him a good fit? What aptitude or experience does someone need to be a successful laser welding machine operator? Practical Welding Today® sat down with Stenger to find out.
PWT: You mentioned you never thought you’d be doing this for six years. What’s kept you there?
We don’t do high production of anything. We do a lot of programming, a lot of fixturing, and a lot of setup. It keeps me active and keeps me thinking. If it was just production work, it would be a different story.
PWT: What skill sets are necessary for someone to thrive in your position?
I was a mechanical design engineer since the late 1970s. I designed machinery, gauges, and fixtures. I designed equipment similar to the laser itself, although not a laser. There are a lot of components in the machine that I’ve never dealt with, mainly automation and assembly machines.
For laser welding machine operators, mechanical aptitude is helpful. You also should possess programming skills and experience as well as advanced computer skills in multiple CAD software programs. A laser welding background would be nice, but that’s difficult, if not impossible, to find.
You’ve got to be extremely organized because you have to keep track of all of what you’re doing to debug these welds to get them to the point where the customer is pleased, and where the welds are performing the way they are supposed to. If you’re not keeping good documentation of how you got to that point, then you’re just spinning your wheels.
PWT: What do you mean when you say “debug” the welds?
If we are starting out with just a basic weld on a sheet of steel, we’re looking to get rid of porosity, the heat-affected zone (HAZ), and we’re looking for the penetration or the depth of the weld. And we continue to do that on the sample piece until the results are what we need them to be.
From there we section the weld and take a closer look by chemically etching the side of the weld to make sure it meets qualifications. Then our CWI [certified welding inspector] takes a look and lets us know if it passes or if we need to keep tweaking.
We get a lot closer to achieving the results we need on the first attempt now compared to when we first started. But Thom Shelow and the CWI make my life easier because they know what they’re looking at. They give me suggestions on what adjustments I need to make, and at that point I become a welding operator.
PWT: What is involved with fixturing, which plays a huge role in laser welding?
The software we use is incredible. We bring a 3-D model into the workspace, position it where we want it with the machine visible in that workspace on the computer, and tell it where we want support ribs in the X and Y axis. The software will extrude ribs up to the outermost part of the model and stop.
Once we have a fixture that looks the way we want it after editing those lines, we can tell it to Create Fixture and it flops it out into the flat. We only have to organize the contours on a flat sheet of steel and then cut it. The fixture then snaps together and we tack weld it so it doesn’t fall apart. It’s a lot easier said than done, obviously, but the software makes it so much easier. We literally have a fixture that will hold just about any part configuration.
PWT: Describe something about your job that most people don’t know or understand.
Of all the guys here that see me use the machine, none of them want to touch it. They think it’s out of their league, but I think you can teach people how to do things if they have the beginning skill set we talked about.
I had a young high school kid in here once. He was in a robotics class and was a little bit cocky. He asked a few specific questions, which I answered specifically. He said, “Oh, that looks easy,” and then walked away. What he didn’t realize is this is a $1 million machine and you have to clear everything. You can’t be crashing into the fixture or hitting other things, and you can’t hit the part. Until that cycle fully completes and gets to a safe position and starts over again, that part of the job isn’t done. You have to make sure all of that is clear, works, then you can push the button and walk away. That’s the part of the job I don’t care for—pushing the button.
PWT: What advice do you have for someone interested in becoming a laser welding machine operator?
Think it out and move slow. There is no hurry to get it done. If you crash it, you’re down for possibly a week and it’ll cost tens of thousands of dollars to fix. It’s not worth the rush. Make sure you’ve got all of your bases covered.
There are different levels of crashes. Our machine has a magnetic head, so if you bump it or hit it against something, it comes off. I’ve been told that operating a laser is just like riding a motorcycle—there are operators who have crashed and there are operators who will crash. It’s not a question of if, it’s a matter of when and how severe. I’ve hit soft parts before, but had they been hard, it would have been a serious crash. I’ve been lucky.
About the Author
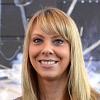
Amanda Carlson
2135 Point Blvd
Elgin, IL 60123
815-227-8260
Amanda Carlson was named as the editor for The WELDER in January 2017. She is responsible for coordinating and writing or editing all of the magazine’s editorial content. Before joining The WELDER, Amanda was a news editor for two years, coordinating and editing all product and industry news items for several publications and thefabricator.com.
About the Publication
subscribe now
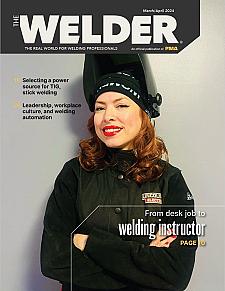
The Welder, formerly known as Practical Welding Today, is a showcase of the real people who make the products we use and work with every day. This magazine has served the welding community in North America well for more than 20 years.
start your free subscription- Stay connected from anywhere
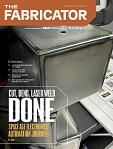
Easily access valuable industry resources now with full access to the digital edition of The Fabricator.
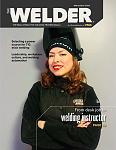
Easily access valuable industry resources now with full access to the digital edition of The Welder.
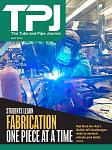
Easily access valuable industry resources now with full access to the digital edition of The Tube and Pipe Journal.
- Podcasting
- Podcast:
- The Fabricator Podcast
- Published:
- 04/16/2024
- Running Time:
- 63:29
In this episode of The Fabricator Podcast, Caleb Chamberlain, co-founder and CEO of OSH Cut, discusses his company’s...
- Industry Events
16th Annual Safety Conference
- April 30 - May 1, 2024
- Elgin,
Pipe and Tube Conference
- May 21 - 22, 2024
- Omaha, NE
World-Class Roll Forming Workshop
- June 5 - 6, 2024
- Louisville, KY
Advanced Laser Application Workshop
- June 25 - 27, 2024
- Novi, MI