Senior Editor
- FMA
- The Fabricator
- FABTECH
- Canadian Metalworking
Categories
- Additive Manufacturing
- Aluminum Welding
- Arc Welding
- Assembly and Joining
- Automation and Robotics
- Bending and Forming
- Consumables
- Cutting and Weld Prep
- Electric Vehicles
- En Español
- Finishing
- Hydroforming
- Laser Cutting
- Laser Welding
- Machining
- Manufacturing Software
- Materials Handling
- Metals/Materials
- Oxyfuel Cutting
- Plasma Cutting
- Power Tools
- Punching and Other Holemaking
- Roll Forming
- Safety
- Sawing
- Shearing
- Shop Management
- Testing and Measuring
- Tube and Pipe Fabrication
- Tube and Pipe Production
- Waterjet Cutting
Industry Directory
Webcasts
Podcasts
FAB 40
Advertise
Subscribe
Account Login
Search
Robots for hire
A new approach to automation: Paying robots by the hour
- By Tim Heston
- March 24, 2017
- Article
- Automation and Robotics
Matt Bush runs an employment agency, of sorts. His workers always start their shifts on time. In fact, Bush knows where they are at all times, tracks their performance, even trains them himself.
Thing is, his workers aren’t humans, though he occasionally mistakes them for humans. They’re robots, rented from Hirebotics.
When Bush and his business partner, Rob Goldiez, launched the company in December 2015, their aim was to make automation more accessible and flexible than it is today, particularly for the high-product-mix world. And they’re achieving this in creative ways, thanks in part to the technology behind collaborative robotics.
Robots on Wheels
Before launching Hirerobotics, the founders spent years in various manufacturing businesses, from electronic circuitry manufacturing to machine shops. Most recently Bush was director of operations and Goldiez was general manager at Scott Fetzer Electrical Group (SFEG) in Tennessee. In 2014 and 2015 the two worked to help automate the factory, basically to make it globally competitive.
Still, the high product mix at SFEG, including the large variety of enclosures produced by the sheet metal department, presented challenges. Most machines didn’t run constantly, and depending on the product mix, some equipment didn’t run for days or even weeks at a time. SFEG certainly couldn’t dedicate a conventional robot to running those machines, considering the integration effort involved. But it also had difficulty finding skilled people to run the equipment, a familiar problem to anyone in manufacturing.
Conventional robots also required adequate safeguarding like safety cages. As robots traverse a weld or manipulate a formed part, they can’t actively sense the world around them, so they need space for adequate safeguarding.
Bush then came across a white paper from Irvine, Calif.-based Universal Robots (UR) USA, a collaborative robotics supplier, and his imagination started churning. These robots sense the world around them, which gives them a human way of moving about an area. When a collaborative robot arm touches an obstruction, it stops. It also can sense pressure, which allows it to, say, slide a part against a press brake backgauge with enough force to ensure it’s secure, just as a human would do.
Although collaborative robots can “talk” to modern controllers and other mechatronic elements, they don’t have to. And they don’t require safety cages, though the machines they’re tending require adequate guarding, optoelectronic or otherwise. All this allows people on the floor not just to operate the automation, but to work with it—hence the term collaborative robotics.
“An extension of this is the ability to easily deploy the robot quickly,” said Douglas Peterson, UR’s general manager for the Americas. “You don’t need a team of robotic programmers and engineers on-site to deploy the robot. And you often can deploy them without making dramatic changes to your production.”
Most significant for SFEG, the robots are portable. “We saw the technology and thought, ‘We could put these on mobile bases and have an entire fleet of robotic workers,’” Bush recalled.
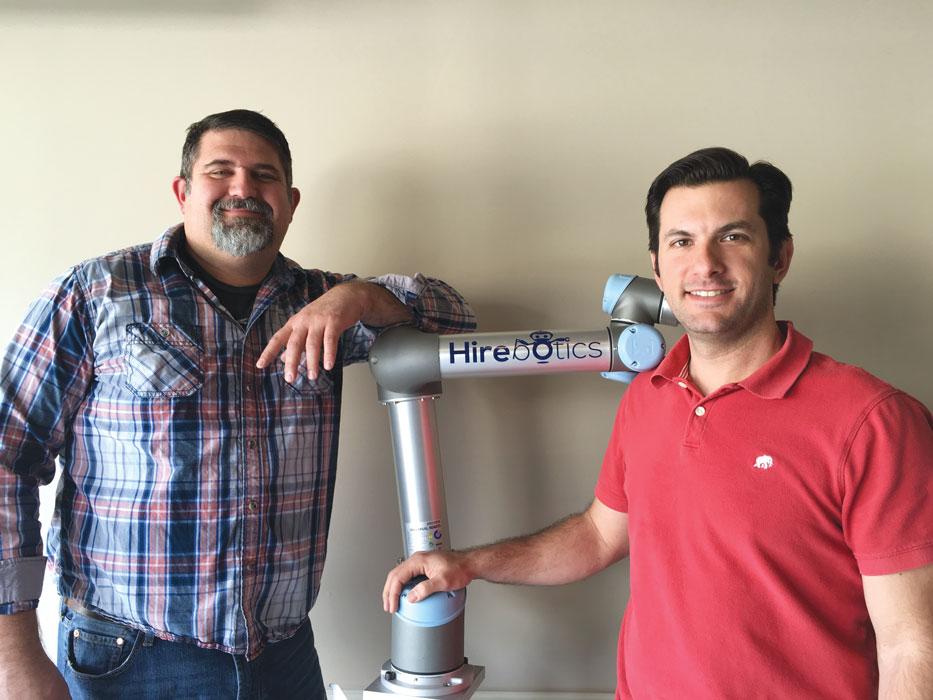
In December 2015 Matt Bush (left) and Rob Goldiez launched Hirebotics, a company that allows manufacturers to hire collaborative robots by the hour. Photo courtesy of Hirebotics.
SFEG purchased 14 robots from UR, and over the ensuing months it deployed them. The company had certain product lines that ran all the time, and it made sense to place robots on those lines to handle the monotonous tasks.
“We found that we could place these robots on the line to handle mundane tasks, and then move people to stations on the line where we really needed the manual dexterity and cognitive ability,” Bush said.
The company did have one robot, affectionately named Waldo, that moved all over the plant. “People never knew where Waldo was going to be,” he said. “He was our guinea pig.” If Bush and his team wondered if a certain complex task, like punch press or press brake operation, could be handled by a collaborative robot, Waldo was there to help them find out. Once the concept was proven out, the team implemented the task in production, and Waldo moved on to other experiments.
For Manufacturing DaySM several years ago, SFEG invited the public to see how collaborative robots were working with human assemblers. As Bush recalled, “We talked about the status of robots in manufacturing, and how we had robots on the line working shoulder to shoulder with people, doing jobs that nobody really wanted to do. That just shocked a lot of people who visited the plant. They thought robots were supposed to be behind cages.”
As of 2015, the company began to use collaborative robots on various machines, and because they were on wheels, they could be moved throughout the plant. After a robot finished one operation, it literally could be wheeled to another machine and, after being connected to the Ethernet and a few other inputs and outputs, be up and running again.
I/O setups designed into each machine connected various sensors, air cylinders, and whatever else the operation required. “All that stayed at the machine,” Bush said. “All we needed to do was plug in an Ethernet cable and pull up the program for that machine, and the robot immediately knew how to run each machine based on the program that was loaded.”
Integration with existing equipment wasn’t always very complex. For instance, the robot used in front of forming machines was not in constant communication with the controller. But I/Os were set up so that the robot knew when the program commenced and when each ram cycle was complete, triggering the robot to move on to the next bend in the sequence.
A New Kind of Worker
Several years ago Goldiez and Bush sat on a beach. “We were doing what you do on vacation: thinking about what to do next,” Bush recalled, “and we asked ourselves, ‘How can we make automation easier for small and midsized manufacturing companies? How can you make it like you’re hiring a person? Could we deploy these robots like workers, and structure the business model so that you literally pay for the robot by the hour, just as if it were a human?’”
That’s exactly what they did. After launching Hirebotics in December 2015, the two began working with manufacturers at the beginning of 2016. The firm uses off-the-shelf robots and components, and works exclusively with collaborative robots from UR.
The two had early successes in various manufacturing scenarios. The details of the deployments are protected by nondisclosure agreements, but for all of them, Goldiez and Bush can access every “robot worker” and monitor it remotely.
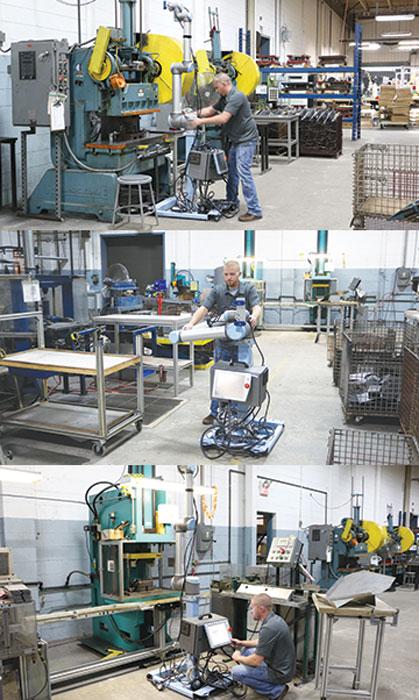
At the sheet metal operation at Scott Fetzer Electrical Group, a worker moves a collaborative robot on wheels from one machine to the next. Photos courtesy of Universal Robots.
Once the robots are running, Bush and Goldiez don’t sit in their office in Franklin, Tenn., and stare at a bank of screens. All the robot monitoring happens through a mobile app.
The remote monitoring also allows Hirebotics to bill only for the hours the robot works. Hirebotics bills its customers weekly, just as an agency would for its temporary workers. “If a robot works 16 hours, 32 minutes, and 18 seconds in a day, that’s what you get billed for,” Bush said. He added that the minimum period is 80 hours, or two shifts, a week. “But anything beyond that, we bill to the second.” If the robot has worked more than 80 hours and is sitting idle, Hirebotics doesn’t charge for that time. “If one week they need to run 84 hours, they run 84 hours. If the next week they need to run 120 hours, they run 120 hours,” Bush said. “And they don’t get overtime.”
From anywhere in the world, Bush and Goldiez can fine-tune robot parameters through the app. In one pick-and-place application, a robot uses plastic grippers so it doesn’t mar the workpiece. The gripper may wear over time, which slightly changes the positional data, be it from an integrated camera or anything else. To accommodate for this, Bush calls the operation up on his app and tweaks the offset parameters for the gripper.
“I can change the offset values while it’s placing parts,” Bush said. “I watch it via FaceTime, then adjust it up and down and left and right, as it’s moving, all from my mobile app. We don’t do this for all customers or installations, but we do offer it where it makes sense.”
All this is possible because every robot is cloud-connected. “We’ve got robots in Michigan, New York, Miami, Tennessee, and elsewhere, and we can monitor these robots wherever they are,” Bush said. “It allows us to measure their diagnostic state, their performance, and we send production data back to our customers via a mobile app. Customers can log in and see exactly how the robots are running at any given moment.”
Bush added that the new company is a full, turnkey integrator. Customers sign a two-page agreement that resembles an employment contract, but for robots instead of humans. “There’s no upfront money, and there are no long-term commitments. Customers are essentially hiring an at-will worker.” As long as a customer gives Hirebotics sufficient notice, as specified by the contract, they can terminate the agreement.
When working with traditional automation, an integrator might design and build an entire system off-site. The customer then flies out to the integrator, gives input, and eventually signs off. The entire system then is installed in production.
“We don’t do that,” Bush said. “We show up with a box of parts, and we start integrating with your existing equipment. We come in, install the robots, teach them, and design end effectors and tooling. Previously there was a person standing by the machine, and now there’s a collaborative robot.”
At this writing, the company was installing a collaborative robot to run five different pieces of equipment that included three machines and an inbound and outbound conveyor. Bush and Goldiez showed up on a Friday, installed the system that very day, programmed and perfected it over the weekend, and on Monday the robot was up and running.
In many cases the robots are handling higher-volume production, taking on simple, repetitive work. But in at least one case the robots are taught to do several completely different tasks in one location. If the robots need to switch tasks, shop operators simply call up a task on their mobile phone or tablet, which then shows a bar code. They scan the bar code at the workstation, and the robot is good to go.
“We try to make it so our customers don’t really need to know anything about robotics,” Bush said.
At this point Hirebotics’ work has involved longer-term engagements, but eventually Bush said he hopes to make deployments simple enough so that it would make sense to use the robots for projects that may last just a week or two.
Still, most of Hirebotics’ customers are contract manufacturers. If, say, a contract is pulled, those companies now aren’t left with a large, now obsolete automated system. Instead, Hirebotics can deploy the robots in another area of the plant.
“These are not purpose-built robots that know how to do only one thing,” Bush said, adding that Hirebotics standardizes the types of sensors, grippers, and other peripherals when possible. All this helps redeploy robots quickly.
Pushing the Limits
Collaborative robots’ positioning accuracy has improved, but it still doesn’t compare to the accuracy of a traditional articulated robot arm. In bending applications, for instance, the accuracy of an articulated robot arm allows it to follow a part throughout a forming operation and position workpieces without using a backgauge.
Collaborative robots operate like humans. They rely on the force feedback given as the part slides against a backgauge. Bush added that a collaborative robot need not rely on communication between it and the CNC to follow the part through the bend. The robot instead can again rely on force feedback. The robot supports the sheet metal throughout the stroke by keeping its end effector steady under the sheet, pressing up with a certain amount of force. When the ram starts the bending cycle and the flange moves upward, the robot arm can be taught to maintain a certain low level of force feedback, which causes it to follow the flange as it swings upward—again, very much how a human would. (One caveat: Following the sheet throughout the bend cycle may not be possible if the part swings upward faster than the robot can move.)
Instead of using precise positioning data from a machine program, the collaborative robot adjusts its position based off of feedback it gets from the action (be it forming, assembly, or any other operation) happening in the moment.
Even the programming aspect has a humanistic quality. You don’t “program” a collaborative robot; you “teach” it, and the teaching varies depending on the system employed. Some are taught kinetically, by moving the robot from point to point; others are taught using a controller interface; and third-party providers offer programming that occurs in separate software, which then transfers those taught motions to the robot.
Regardless of the method, the teaching process involves waypoints—that is, pick it up here (point 1) and put it there (point 2). A task may require that some intermediate points be defined, but individual joint motions need not be taught.
Hirebotics now is working on implementing hand-like end effectors from Robotiq that can pick up different tools, designing toolholders that all mate to the robot’s hand in the same way. Using its end effectors, the robot could pick up a fixture, place and secure it on the table, place a part in it, then pick up a drill or soldering iron (each encased in the standard toolholder) to make a hole or solder a joint.
This, Bush said, may lay the groundwork for a new approach to joining automation. In effect, a collaborative robot could move and work just like a human welder. The robot could pick up a fixture, load a part, push toggle clamps to lock the part in place, then pick up a robotic welding gun to lay a bead. It then would put the welding gun down, flip the part over in the fixture and lock it down, and then grab the gun and lay another bead.
Such a setup is a distinct possibility, particularly with simple linear welds. A robot could also be taught to pick up a welding gun followed by another tool, such as a plasma torch. “You no longer have to work with a robot that has just a welder on the end of its arm,” Bush said. “That’s how we view the flexibility [of collaborative robotics].”
Bush and Goldiez do have a lab near Nashville where they perform basic application research, but most of their work has involved perfecting their ability to monitor and operate their robots remotely. Their work also has included controlling and perfecting how the robot cell communicates with the workers around it. For instance, say a robot picks up parts from a stack; once the stack reaches a certain level, a yellow light alerts material handlers who then replenish stock.
Bush said that the biggest remote-monitoring advancement has involved their ability to tweak robot parameters as it’s running, and then receive immediate feedback to confirm whether those changes improved the operation. Bush called this “dialing in the task.” If he had to start and stop robots continually for every small change, the robot’s efficiency would plummet.
“This also allows us to service customers instantly,” Bush said. “We don’t need to book the next flight out to fix a problem. I just need a couple minutes to find a conference room. I log on to the app and fix the problem.”
Collaborative robots aren’t suited for every task, of course. The systems still have payload capacity limitations, though even here, Bush and Goldiez have found a way to overcome them with workpiece counterweights and other measures. Collaborative robots could be designed to handle heavy parts, but the higher their payload capacity, the slower they need to move. And as parts become heavier, safety issues arise.
Regardless, Bush said that collaborative robots really focus on what he called “human-centric” tasks, which from a safety perspective shouldn’t entail extremely heavy parts anyway.
Today Hirebotics has robots working in companies that run the gamut from a four-person manufacturer to a multibillion-dollar conglomerate. According to Bush, the applications are extraordinarily diverse, but they all carry a common thread: All represent a new way to implement automation in a new way—by “hiring” robots when they’re needed.
Hirebotics, 919-946-0489, www.hirebotics.com
Etalex, 800-351-3125, www.etalex.ca
Scott Fetzer Electrical Group, 615-799-0551,www.sfeg.com
Universal Robots USA, 949-236-6082,www.universal-robots.com
Press brake automation, collaborative-style
When entering the 300,000-square-foot production hall at Montreal-based Etalex, you first encounter Universal Robots’ UR10 diligently unloading metal parts of various shapes and sizes into a large press brake with punch tooling. After the operation, the robot’s pneumatic suction cups pick the pieces back up and stack them in a patterned pile on a cart. As this happens, employees pass back and forth in front of the robot.
Being a collaborative robot, the UR10 has built-in force control that limits the force at contact, enabling it to work right beside employees, no safety cage required.
As Plant Engineer Jean Francois Rousseau explained, “We needed a flexible automaton solution that could be used for 10 different production cycles. Since I have only 6 feet of space in front of the brake press, it was important to run this application without safety caging around it.”
Information provided by Universal Robots USA.
About the Author
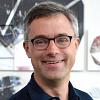
Tim Heston
2135 Point Blvd
Elgin, IL 60123
815-381-1314
Tim Heston, The Fabricator's senior editor, has covered the metal fabrication industry since 1998, starting his career at the American Welding Society's Welding Journal. Since then he has covered the full range of metal fabrication processes, from stamping, bending, and cutting to grinding and polishing. He joined The Fabricator's staff in October 2007.
subscribe now
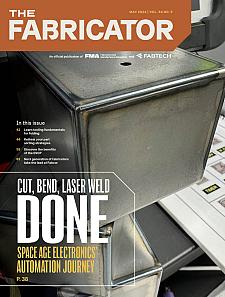
The Fabricator is North America's leading magazine for the metal forming and fabricating industry. The magazine delivers the news, technical articles, and case histories that enable fabricators to do their jobs more efficiently. The Fabricator has served the industry since 1970.
start your free subscription- Stay connected from anywhere
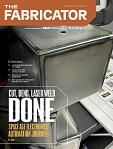
Easily access valuable industry resources now with full access to the digital edition of The Fabricator.
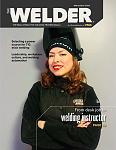
Easily access valuable industry resources now with full access to the digital edition of The Welder.
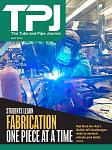
Easily access valuable industry resources now with full access to the digital edition of The Tube and Pipe Journal.
- Podcasting
- Podcast:
- The Fabricator Podcast
- Published:
- 04/16/2024
- Running Time:
- 63:29
In this episode of The Fabricator Podcast, Caleb Chamberlain, co-founder and CEO of OSH Cut, discusses his company’s...
- Trending Articles
Tips for creating sheet metal tubes with perforations
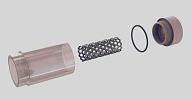
Supporting the metal fabricating industry through FMA
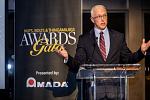
JM Steel triples capacity for solar energy projects at Pennsylvania facility
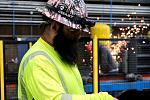
Are two heads better than one in fiber laser cutting?
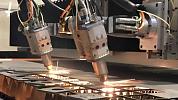
Fabricating favorite childhood memories
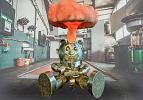
- Industry Events
16th Annual Safety Conference
- April 30 - May 1, 2024
- Elgin,
Pipe and Tube Conference
- May 21 - 22, 2024
- Omaha, NE
World-Class Roll Forming Workshop
- June 5 - 6, 2024
- Louisville, KY
Advanced Laser Application Workshop
- June 25 - 27, 2024
- Novi, MI