Editor-in-Chief
- FMA
- The Fabricator
- FABTECH
- Canadian Metalworking
Categories
- Additive Manufacturing
- Aluminum Welding
- Arc Welding
- Assembly and Joining
- Automation and Robotics
- Bending and Forming
- Consumables
- Cutting and Weld Prep
- Electric Vehicles
- En Español
- Finishing
- Hydroforming
- Laser Cutting
- Laser Welding
- Machining
- Manufacturing Software
- Materials Handling
- Metals/Materials
- Oxyfuel Cutting
- Plasma Cutting
- Power Tools
- Punching and Other Holemaking
- Roll Forming
- Safety
- Sawing
- Shearing
- Shop Management
- Testing and Measuring
- Tube and Pipe Fabrication
- Tube and Pipe Production
- Waterjet Cutting
Industry Directory
Webcasts
Podcasts
FAB 40
Advertise
Subscribe
Account Login
Search
Employees set the pace for success
New solid-state lasers and an electric brake boost productivity at Wisconsin Metal Parts, but employees make the flow work
- By Dan Davis
- June 25, 2015
- Article
- Bending and Forming
Industry experts like to stress the pace of modern metal fabricating. Lead times are tight as customers look for just-in-time deliveries, and fabricators hope to minimize the order-to-cash cycle to maximize the cash available for reinvestment in the company. Cutting-edge machine tool technology is used as a competitive advantage and keeps the shop floor filled with work-in-process.
But is it really that much different from what metal stampers have been doing for several decades?
When a metal stamper is running presses at around 600 strokes per minute, shop floor personnel have to keep track of a lot of parts. For stampers, customers demanding metal parts in a couple of weeks—even days in some instances—instead of eight to 10 weeks is not a new phenomenon.
Wisconsin Metal Parts (WMP) Inc., Waukesha, Wis., is comfortable with the modern pace of manufacturing—or “controlled chaos” as the company’s general manager, Joe Pease, calls it. The company has been in business for 27 years, supplying tooling and metal parts. The original company name was Die Concepts, a designer and builder of stamping dies and gauges. About 20 years ago the company began to change its business focus toward becoming a production supplier of metal parts. In 2010 WMP adopted the current name to better describe its business.
Today WMP is a production supplier of fabricating, CNC machining and turning, stamping, welding, assembly, and prototyping services, while also still maintaining a full-service toolroom. However, it’s the metal fabricating side of the business that has really taken off in recent years, and it’s the company’s employees that have helped it control the chaos.
People Make It Happen
“Absolutely, there is chaos in rapid growth,” Pease said. “There are days that you’re like, ‘How can this be happening?’
“But you sit down, take a look, put some things in place, move some people around, and hire some new people,” he added. “That gives people the opportunity to be here.”
WMP has 70 employees now, with most working on first shift, although it does run three shifts. The management team and a majority of the employees have “lived their lives in job shops,” Pease said. The general manager himself has been at it for 40 years.
WMP is an ISO 9001-certified company, and the management team credits the organizational quality efforts for providing the structure for thorough planning and quick decision-making. The fabricator also has had good success with filling skills gaps in the organization with talented hires. A cross-training program keeps a skilled, nimble workforce in place to serve customers.
The toolroom actually is a farm system of sorts for the leaders that WMP wants to grow. They work as apprentices to learn the skills and disciplines of the tool and die craft, but at the same time they are learning to work independently. They ultimately plan their own work from daily tasks to weekly project schedules.
“You build those independent contractors, and then you put them in a different area. They have that can-do mindset, so they don’t need as much supervising. They help with the job planning,” Pease said. “We work with our people to find what part of the business best fits their skill set and their ambitions.”
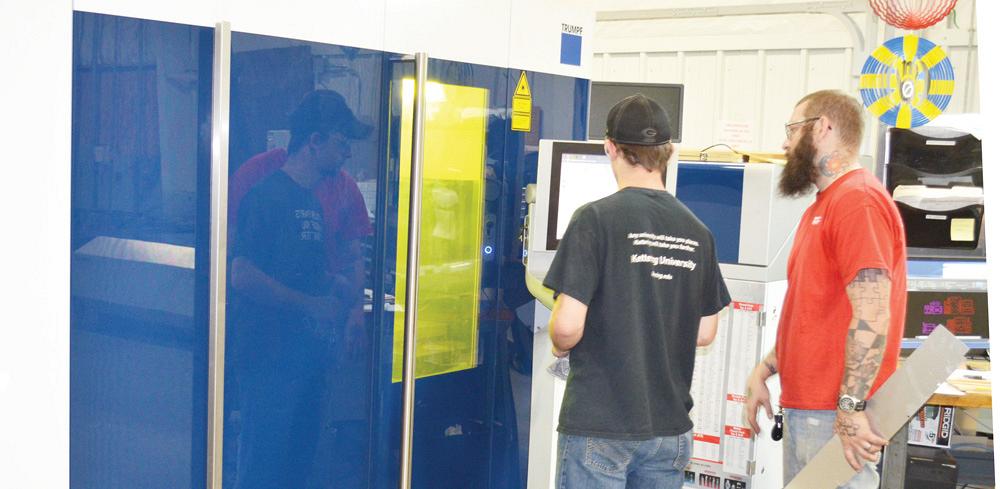
Figure 1
Wisconsin Metal Parts’ TRUMPF 5030 fiber solid-state laser
has caught the attention of nearby OEMs that realize they
can save money and time outsourcing laser cutting to the
metal fabricator rather than trying to push their older CO2
laser cutting machines.
Being so close to the shop floor, those in the toolroom understand how metal flows through the shop to become the final component or assembly that is to be delivered to the customer. They may build the die components for stamping jobs, fixtures to assist in assembly, or even gauges for quality checks after welding or assembly is done. They are tangentially connected to almost every shop floor activity.
Their ability to work independently and manufacturing experience make these toolroom veterans prime candidates for leadership positions within WMP. A couple of years ago, 15 employees worked in the toolroom; today the number is nine as people have been moved around to lead new areas.
To refill the talent pipeline, WMP works closely with the area schools to find that next generation of skilled workers.
“At any given time we have two to four apprentices working throughout our shop,” Pease said.
With a solid leadership team in place across the organization, communication flows easily among the employees spread across three facilities in the area. Daily production meetings are held, and any action items that need to be addressed as a result of those meetings are shared with the corresponding team leaders. The team leaders then can share the information with the employees in their departments.
“We try and give our people a clear plan and direction of what we can do and give them backup plans if something doesn’t go quite as we planned it,” Pease said. “Our cross-training program allows us to quickly shift our workforce to different departments as they are needed. This keeps our work flow going.
“Our average on-time delivery rate is above 96 percent companywide. We are very proud of that,” he added.
Jumping on the Cutting Edge
In late 2013 WMP made the decision to bring in solid-state laser cutting capabilities. WMP wanted to acquire the latest technology that would leave other metal fabricators in the area struggling to keep up with its newfound cutting prowess.
The company purchased a TruLaser 5030 fiber powered by a 5-kW TruDisk laser from TRUMPF Inc. The solid-state laser, which emits a 1-µm wavelength beam, can slice through thin materials at a much faster rate than traditional CO2 laser cutting technology thanks to the large power source (see Figure 1).
“We started doing market research with our customers and getting work lined up [before the equipment arrived],” said Dave Holzer, WMP’s business development manager. “Being able to go out and say we have something that runs three to five times faster than what other people are doing, it opens doors for us. People are interested, and they want to hear more.”
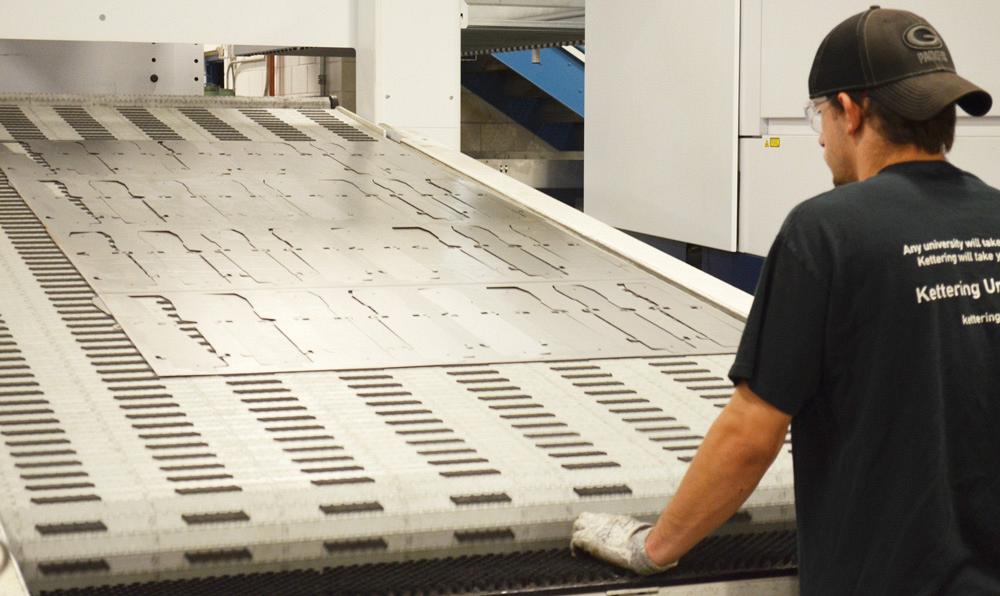
Figure 2
Cut parts and the sheet skeleton are delivered to the laser operator via a conveyor after
each sheet is laser-cut.Figure 1
Holzer was referring to the tried-and-true CO2 laser resonator technology that has served the metal fabricating world well over the past two decades. It is a reliable technology, but has been overshadowed in recent years by new solid-state laser technology and its ability to rip through gauge-thickness metals and to cut reflective metals, which CO2 lasers struggle with.
Even though WMP had no experience with solid-state laser cutting, it wasn’t intimidated. It wanted to make a big splash.
“There were 3,000-W fibers out there, but again we’re not trying to be the same as other shops,” Pease said. “The question was how we could be a little different to gain a little market advantage in the beginning and then build relationships.”
To prepare for the arrival of the laser cutting machine, WMP cleared space for it and the automated LiftMaster compact material load/unload system (see Figure 2) by moving welding cells around and shifting material storage to another facility. Employees also received training on how to operate the equipment, which was an extension of the cross-training efforts already underway at the company.
The first TruLaser 5030 fiber arrived in January 2014, and by the end of March it was cutting at 70 percent capacity, processing almost 200,000 lbs. of material per month. The company had to absorb a lot of new work in a short period of time. The laser’s cutting speed made short work of a majority of the thin metal jobs, and the edge quality caught the attention of current customers and helped to win new ones.
Holzer recalled the “chaos” of that time, but he said that employees responded to keep the parts moving through the shop—even when turnaround time was two to three days.
“We have people review the incoming POs and folders, and we have job trackers, routers, and inspection forms. So the checks and planning were already in place,” Pease said. “But if something slipped through the cracks or became a rush, the employees were focused on what needed to get done. They were looking at the jobs and ahead to the next job or the job after that.”
They made it work. So well, in fact, that WMP added a second TRUMPF 5030 fiber later in the year.
Forming: The Future
WMP wanted to offer its customers something more in the brake press department as well.
With the speed of the laser, they needed more bending capacity to keep up with orders. In September 2014 it installed an all-electric 13.45-ft., 330-ton SafanDarley E-Brake (see Figure 3). Again, WMP decided to jump into an area where few other fabricators have ventured.
“I have learned—and anybody in a job shop has learned—no matter what equipment you buy, it will always be too small,” Pease said. “So this 330-ton electric brake, from what I could research and find, is one of the largest ones made.”
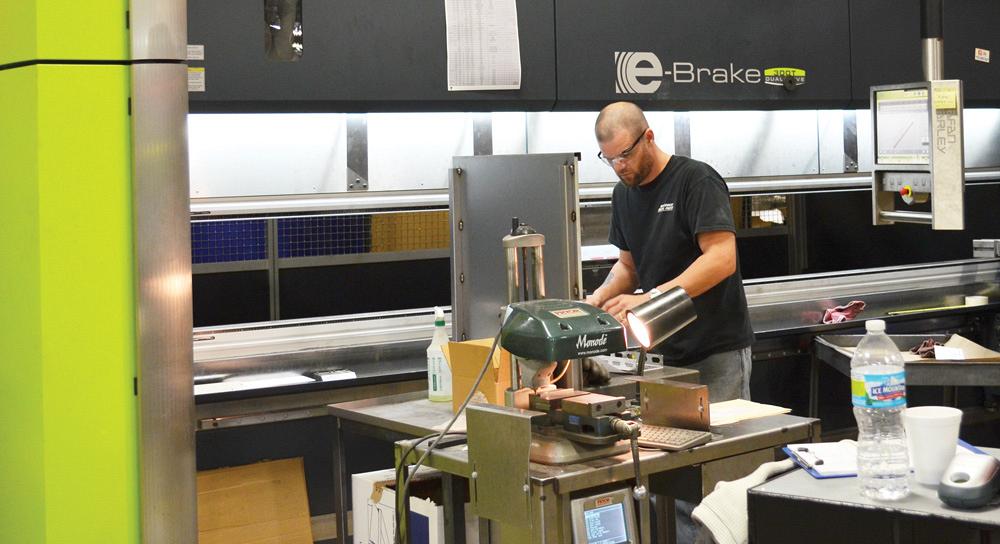
Figure 3
While the metal fabricator doesn’t bend too many parts that extend past 13 feet, the longer press bed of the new SafanDarley electric brake is useful for setting up multiple tool sets for staged bending of complicated parts.
Pease said that one of the first things that jumps out at an operator is the quiet performance of the machine. Its servomotors provide near-silent operation.
“If you had a 300-ton hydraulic brake, you know what the noise would be,” he said.
The press brake also moves much more quickly than hydraulic brakes, almost 10 to 20 percent faster, according to Pease. This really isn’t noticeable over a 10-part run, but over larger jobs the increased speed is quite evident, he said.
The brake’s 13.45-ft. length is good not only for longer parts, but also multiple setups. An operator can do multiple bends while walking the part down the brake until it is finished. This way the operator doesn’t have to put the parts to the side after a few bends, change the tooling, and complete the bending job.
This type of setup expertise is again an example of the shop floor personnel making a big difference. Managers may suggest how a bending job might run, but it’s the operators who have the final say.
He added that the machine really shines with larger job runs, where the operators are able to take advantage of the press brake’s light guard (see sidebar More Than a Safety Tool) and eliminate wasted press brake motion commonly associated with older press brakes, which have rams that have to retreat to the top of the operational window before they can cycle down for another hit. The right combination of operator and new technology makes a big difference in efficient product flow.
The new electric brake contributes to consistent part quality because it delivers very precise movement. Unlike a hydraulic press brake that requires hoses be filled with hydraulic oil before the ram can come to a complete stop, the electric brake’s ram, controlled by a servo-electric drive and a double-pulley system, can stop in milliseconds.
The brake also has a gauge measurement tool on it. If an operator places a piece of material onto the brake that is 0.005 in. thicker than the preceding blank, the brake automatically adjusts the ram’s bending target, which allows the press brake to deliver bends that are consistently within the job’s specs. The brake’s 6-axis backgauge helps to ensure that the blank is located where it needs to be and the bends occur in the order intended and in proper relation to each other.
Controlling the Future
With the new equipment in place, Holzer said the stress point for WMP really resides with the sales department to bring in more work. So far that has worked out well because WMP has proven to be responsive to customers.
“We invest heavily in new technology and training a skilled and empowered workforce,” Pease said. “We also try not to outsource any of our manufacturing. When components leave your building, you can lose control of quality and delivery. We have a great vendor base to complement our assembly and production services, but those vendors also have other customers and their own business plans in play. For that reason, we try to keep as much as possible of our work in-house. We find that gives our customers the best security and the best service.”That means embracing the chaos of fabricating, so the customer doesn’t have to worry about it.
More Than a Safety Tool
In most instances, light guarding on a press brake is associated with a simple safety function. If the light curtain sensors on either side of the bending window pick up anything other than the metal to be bent, the safety system shuts the machine down. The operator or interloper, whatever the case may be, is safe, but the bending process is stopped.
The light guard for the SafanDarley E-Brake, which is integrated into the press brake, provides the same safety function, but it also can be used to improve bending cycle times.
“Most people don’t want to invest in safety because they think it slows down productivity,” said Mauricio Gutierrez Matta, SafanDarley’s area export manager. “That’s why we invented something that would improve productivity and improve safety at the same time.”
The press brake has been engineered so that the operator can use the light guard as a means to direct operation of the ram. Different modes allow the operator to use the foot pedal or interruption of the light curtain or a combination of the two to run the machine.
For example, the machine’s “one break” mode can be set up for a rapid bending job. The operator’s simple interruption of the focus area in the bending tooling can trigger the ram to advance at 10 mm per second to produce the bend; the operator can then remove the bent part, put another blank in its place (which triggers the ram to advance), and continue the process. This type of option also is helpful when an operator is struggling with a large or awkward-shaped part and is unable to reach the foot pedal.
In many of the modes, the press brake is intelligent enough to advance to just millimeters above the actual pinch point to accelerate the bending process. Typically a press brake needs a couple of seconds to cycle from the top of the bending window to the actual bend for every step in a bending job. If the ram is situated to allow just enough room for a flat part to be inserted, the press brake does not require several seconds to complete the forming action. When the operator has to extract the bent part, the press brake knows that the ram has to fully rise to accommodate the removal of the part.
The light curtain is able to keep tabs on the bending area while also allowing other movement in the press brake window because the sensors focus on an area of about 30 mm, or a little over 1 inch, where the bending takes place.
These different modes are hard-wired into the machine. Any adjustment requires the operator to have a key and to walk to the side of the machine to select the appropriate bending mode.
If a mistake is made and the light guard senses a presence that it shouldn’t, the ram stops within 80 milliseconds. The servomotors controlling the ram movement can stop it much more precisely than a hydraulic system.
About the Author
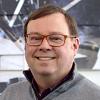
Dan Davis
2135 Point Blvd.
Elgin, IL 60123
815-227-8281
Dan Davis is editor-in-chief of The Fabricator, the industry's most widely circulated metal fabricating magazine, and its sister publications, The Tube & Pipe Journal and The Welder. He has been with the publications since April 2002.
subscribe now
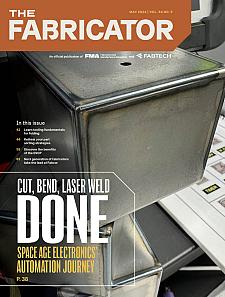
The Fabricator is North America's leading magazine for the metal forming and fabricating industry. The magazine delivers the news, technical articles, and case histories that enable fabricators to do their jobs more efficiently. The Fabricator has served the industry since 1970.
start your free subscription- Stay connected from anywhere
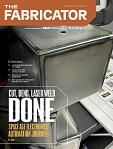
Easily access valuable industry resources now with full access to the digital edition of The Fabricator.
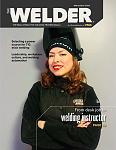
Easily access valuable industry resources now with full access to the digital edition of The Welder.
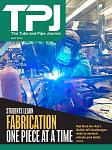
Easily access valuable industry resources now with full access to the digital edition of The Tube and Pipe Journal.
- Podcasting
- Podcast:
- The Fabricator Podcast
- Published:
- 04/16/2024
- Running Time:
- 63:29
In this episode of The Fabricator Podcast, Caleb Chamberlain, co-founder and CEO of OSH Cut, discusses his company’s...
- Industry Events
16th Annual Safety Conference
- April 30 - May 1, 2024
- Elgin,
Pipe and Tube Conference
- May 21 - 22, 2024
- Omaha, NE
World-Class Roll Forming Workshop
- June 5 - 6, 2024
- Louisville, KY
Advanced Laser Application Workshop
- June 25 - 27, 2024
- Novi, MI