Contributing Writer
- FMA
- The Fabricator
- FABTECH
- Canadian Metalworking
Categories
- Additive Manufacturing
- Aluminum Welding
- Arc Welding
- Assembly and Joining
- Automation and Robotics
- Bending and Forming
- Consumables
- Cutting and Weld Prep
- Electric Vehicles
- En Español
- Finishing
- Hydroforming
- Laser Cutting
- Laser Welding
- Machining
- Manufacturing Software
- Materials Handling
- Metals/Materials
- Oxyfuel Cutting
- Plasma Cutting
- Power Tools
- Punching and Other Holemaking
- Roll Forming
- Safety
- Sawing
- Shearing
- Shop Management
- Testing and Measuring
- Tube and Pipe Fabrication
- Tube and Pipe Production
- Waterjet Cutting
Industry Directory
Webcasts
Podcasts
FAB 40
Advertise
Subscribe
Account Login
Search
How adjustable V dies streamline plate bending
The latest systems aim to help maximize productivity and operator safety
- By David Bishop
- October 27, 2016
- Article
- Bending and Forming
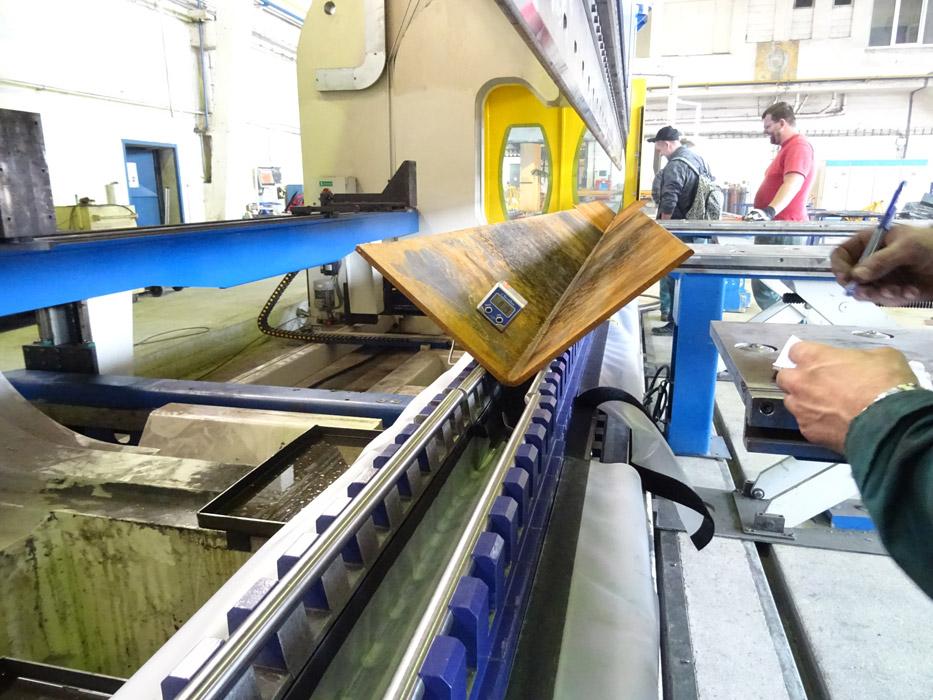
Figure 1
This long workpiece was formed on a tandem press brake with a kind of adjustable V die called a multi-V die.
Over the past four decades, high-precision, quick-change tooling; single-operator tool loading/unloading; and the ability to store tooling in a lockable cabinet at the press brake have become the norm for a large percentage of sheet metal fabricators that fabricate parts from 20-gauge through 1⁄4-in.-thick mild steel.
These innovations have helped many to realize tremendous gains in productivity. Unfortunately, during that same period, an equally large percentage of fabricators that produce parts made of thick plate have realized very little in the way of productivity gains.
In fact, it is still common for press brake operators, along with operators that have been pulled from other machines to assist in setup, to spend as much as an hour or more changing very large, heavy, and often worn-out punches and dies. No doubt much of this is due to the fact that, until recently, plate fabricators had few tooling options to reduce setup times and improve their productivity.
Fortunately, the latest advances in high-precision, adjustable V dies help change all of that.
Recent Developments
One recent development in this technology is a series of dies referred to as multi-V dies, which are available from multiple press brake machine and tooling suppliers (see Figures 1 and 2). Some models have a V-opening range from 0.095 in. up to 4.88 in., while other, larger models have ranges extending up to 15.75 in. The concept is based on the use of a row of small, replaceable segments on the front and back of modular dies that sit atop a U-shaped base, or “saddle.” V-opening widths are established via the use of precision-machined spacers that rest between the saddle and the die segments.
To narrow the V opening, operators remove the spacers by sliding them out the ends of the dies and replacing them with spacers of a larger width. Inserting spacers of a smaller width widens the V opening. The spacers are available in versions that can be connected at the ends, so it is possible to replace them quickly on machines that are 10 feet and longer. After inserting a set of spacers, operators can lock the V opening in place by tightening two set screws on each die module.
Roller Bars
Multi-V dies come with hardened and replaceable roller bars on the shoulders of the V openings. Being hardened prolongs service life; being replaceable prolongs die life. The roller bars reduce friction and subsequent die marking on the material. They also are designed to reduce bending force (tonnage) requirements.
Depending on the model, operators can change the die opening either by manually moving die components or by using a mechanized or fully automated system.
For instance, certain multi-V die units use a chain drive that is driven using an electric hand drill (see Figure 3). While it still uses spacers to establish the width of the V opening, the drive system allows one operator to use an electric drill to open and close the V openings on the die segments regardless of how many segments are installed in the press brake.
This allows operators to open various die segments quickly to remove or install the spacers, and then close the segments against the spacers to set the V opening. This can be especially beneficial on long installations that involve multiple die units.
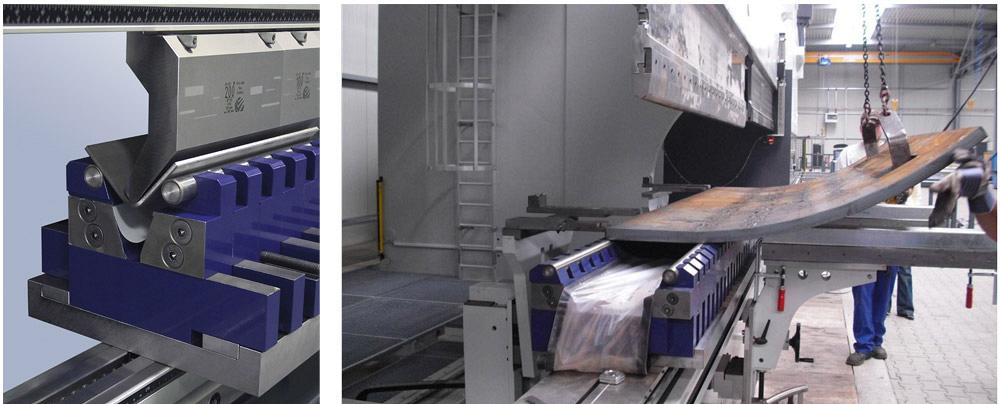
Figure 2
On the left, a type of adjustable V die called a multi-V die is being used with a heavy-duty gooseneck punch. Note the U-shaped saddle at the bottom of the V. On the right, a large multi-V die is expanded to a wide die opening for bumping 2-in.-thick plate. The hardened-steel roller bars on the die shoulders can be replaced as needed.
Some adjustable V dies have a CNC motor-driven system that can be programmed for specific V openings (see Figure 4). These kinds of dies do not require spacers. Instead, the width of the V opening is established and maintained via the CNC drive motors.
Crowning System Compatibility
Because most adjustable V dies will be installed on press brakes used to bend thick plate, it normally will be necessary to address machine deflection. These dies can be used on press brakes with built-in crowning systems to compensate for machine deflection, as well as on machines equipped with crowning systems provided by tooling suppliers.
In installations that involve crowning systems provided by tooling suppliers, the bottom of an adjustable V die such as a multi-V die may, depending on the application, be designed to serve as the top of the crowning system. This helps to reduce the stackup height of all of the different components required, thus consuming less of the machine’s open height.
Most adjustable V dies can be used with a variety of crowning systems, including those that are CNC motor-driven and, in many cases, those driven by a hand crank.
As adjustable V dies are designed to remain in the press brake, they can eliminate the need for hydraulic die clamping on the crowning system. During die installation, set screws in the crowning system can be tightened to secure the die location.
When selecting a crowning system for a press brake that is going to be used to bend thick plate with an adjustable V die, be sure to consider the crowning system’s tonnage capacity on a per-foot or per-meter basis. Also consider whether the average number of setups in a given year are going to justify the use of a CNC motor-driven crowning system, and if the crowning system is going to be used in a harsh environment where it would be beneficial to have a hardened load-bearing surface.
Range of V Openings
While certain adjustable V dies are available with a predetermined range of V openings, it is possible to install within certain multi-V die models a set of adjustable inserts, also equipped with hardened roller bars. The inserts can be adjusted by widening and narrowing the opening on the die. These inserts make it possible to reduce the effective range of V openings. This allows the press brake operator to bend material as thin as 20-ga. mild steel on certain die models.
In addition, some tools have a die holder available that, mounted on the adjustable die, enables the press brake operator to utilize standard (1V) dies.
Because they offer a range of V openings, adjustable V dies rarely have to be removed from the press brake. This eliminates the need for operators to move large, heavy dies in and out of the press brake via an overhead crane, jib crane, or forklift, or retrieve these heavy tools from a storage rack. As such, they make the process of changing from one V opening to another much safer.
Range of Press Brakes
Adjustable V dies can be installed on various styles of press brakes. For instance, a multi-V die can be installed on a press brake via a bolt-down base in which the saddle is bolted directly to the bed of the machine, or via a tang that will fit into a slot on the bed of the machine with set screws, common to American-style press brakes. Saddles are also available to allow the dies to be installed on a European-style lower beam.
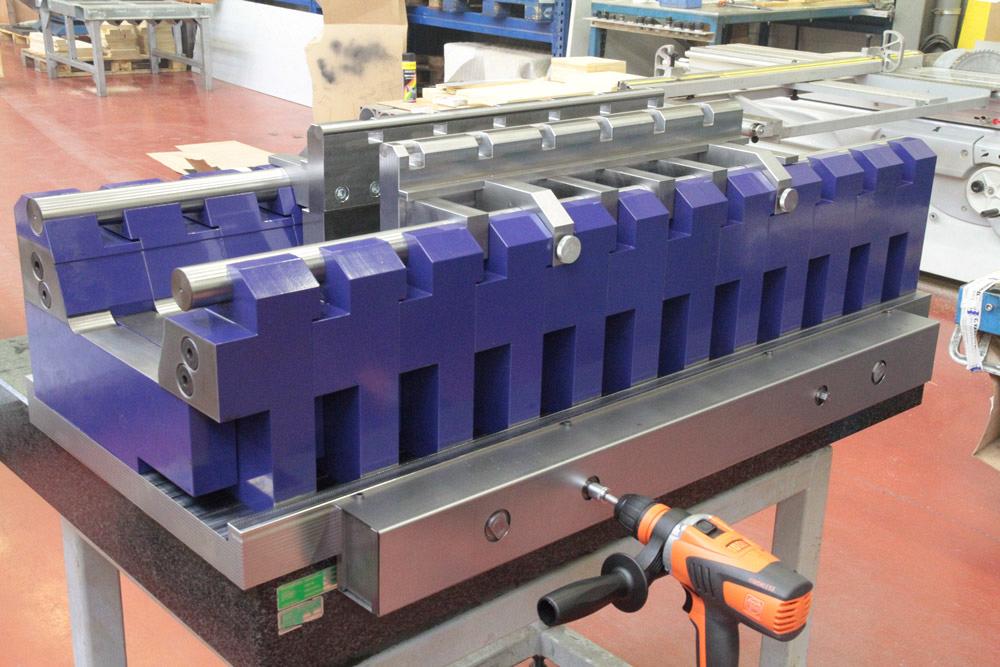
Figure 3
With this semiautomatic adjustable multi-V die, the operator uses an electric drill to actuate a chain drive, which moves the die to the desired width.
Press Brake Requirements
Aside from the obvious need for a press brake to have adequate tonnage and bending length capacity for the full range of material types, thicknesses, and part geometries, a very large open height is undoubtedly the greatest need when using multi-V dies and similar adjustable V dies in a press brake.
Bending thick plate requires dies with a very deep V opening. This allows enough die penetration to form such plates to 90 degrees and to compensate for the amount of springback often present in these materials. Therefore, the V openings on some adjustable V dies are much taller than those typically on adjustable dies that use shims to establish the width of the V openings. Except in extreme cases, the additional die height helps prevent the need for additional time and steps required to bump-bend parts to 90 degrees.
With that in mind, it is very important for you to consider the following when planning to install an adjustable V die on a new or existing press brake:
- Maximum length of the die that will be necessary to meet all of your part requirements.
- Maximum amount of bending force (tonnage) required to bend the full range of material types and thicknesses that you will need to bend.
- Open height available between the ram and the bed.
- Enough ram stroke length to bring all of your punches to the bottom of the stroke.
- The height of the clamping system, if a hydraulic clamping system is installed on the press brake.
- The height of the crowning system.
- The heights of the various punches that will be required.
- The amount of vertical adjustment provided with the backgauge. This is extremely important because of the height of some adjustable V dies. They often require the backgauge to operate at a position that is much higher to clear the top of the die.
- The amount of working space available between the punch and die for part manipulation during bending after everything has been installed, including the clamping system, punches, adjustable V dies, saddle, and the crowning system.
About the Author
David Bishop
443-459-5496
Related Companies
subscribe now
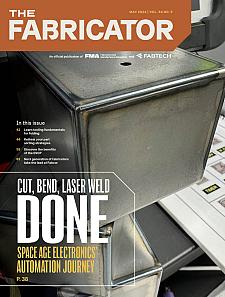
The Fabricator is North America's leading magazine for the metal forming and fabricating industry. The magazine delivers the news, technical articles, and case histories that enable fabricators to do their jobs more efficiently. The Fabricator has served the industry since 1970.
start your free subscription- Stay connected from anywhere
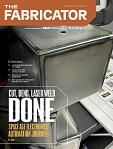
Easily access valuable industry resources now with full access to the digital edition of The Fabricator.
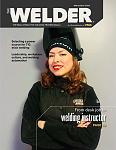
Easily access valuable industry resources now with full access to the digital edition of The Welder.
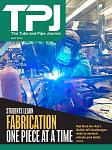
Easily access valuable industry resources now with full access to the digital edition of The Tube and Pipe Journal.
- Podcasting
- Podcast:
- The Fabricator Podcast
- Published:
- 04/16/2024
- Running Time:
- 63:29
In this episode of The Fabricator Podcast, Caleb Chamberlain, co-founder and CEO of OSH Cut, discusses his company’s...
- Industry Events
16th Annual Safety Conference
- April 30 - May 1, 2024
- Elgin,
Pipe and Tube Conference
- May 21 - 22, 2024
- Omaha, NE
World-Class Roll Forming Workshop
- June 5 - 6, 2024
- Louisville, KY
Advanced Laser Application Workshop
- June 25 - 27, 2024
- Novi, MI