Senior Editor
- FMA
- The Fabricator
- FABTECH
- Canadian Metalworking
Categories
- Additive Manufacturing
- Aluminum Welding
- Arc Welding
- Assembly and Joining
- Automation and Robotics
- Bending and Forming
- Consumables
- Cutting and Weld Prep
- Electric Vehicles
- En Español
- Finishing
- Hydroforming
- Laser Cutting
- Laser Welding
- Machining
- Manufacturing Software
- Materials Handling
- Metals/Materials
- Oxyfuel Cutting
- Plasma Cutting
- Power Tools
- Punching and Other Holemaking
- Roll Forming
- Safety
- Sawing
- Shearing
- Shop Management
- Testing and Measuring
- Tube and Pipe Fabrication
- Tube and Pipe Production
- Waterjet Cutting
Industry Directory
Webcasts
Podcasts
FAB 40
Advertise
Subscribe
Account Login
Search
Big press brake bending, high throughput
Overcome productivity challenges in large-workpiece bending
- By Tim Heston
- June 29, 2016
- Article
- Bending and Forming
A long blank is cut on a fiber laser and offloads onto an automated system that transports, orients, and feeds it into the side of a tandem press brake, with front and back workpiece positioners (which double as front- and backgauges) that guide the part through forming. From there a pusher integrated into the brake table offloads the part to a conveying system that takes the piece to a fixture for seam welding.
Steve Claude, president of Durma USA, Cornelius, N.C., described the previous operation, a light pole application that demanded extremely quick lead times. The company chose to cut the blanks with a fiber laser not only for speed, but also to attain edge quality requirements—the piece went from forming in the tandem brake straight to seam welding, without deburring or weld prep.
Although such automation wouldn’t make business sense for a high-product-mix, low-volume shop, it does prove a point: In large-scale bending, be it on one large press brake or a tandem machine, the actual bending doesn’t take long. Operators instead spend most of their days doing everything else: getting the massive workpiece to and from the brake, positioning the piece between bends, waiting for cranes, and changing tools.
Plunging into the large-workpiece bending arena can be a tempting idea; perhaps it will help set a fab shop apart from competitors. But when a shop is investing in such processes, sources named several factors that can affect how quickly work flows through the facility.
Tandem or One Large Brake?
Say you have one large brake. You form one massive part followed by several other parts too big for your other press brakes but relatively small for the large brake’s long bed. Meanwhile, other larger parts sit in queue, waiting their turn.
With a tandem press brake, being two smaller brakes tied together, operators could have formed those small-part batches on the individual brakes, then return to tandem mode to process the next large part in the queue. But then another job comes up for bid, one that requires the forming of an extremely large part. Your tandem brake has the tonnage per foot required, and you even have the right tooling. Yet several bends in the part require significant clearance behind the tooling. That’s clearance your tandem machine doesn’t have thanks to the throat in the middle of the bed—space behind the tools in the center of the bed, where the two brakes are joined together. Try and form this particular job, and the workpiece would collide with the machine frame.
Having one large machine, with open space behind the tooling and no throat in the middle of the bed, you would have been able to take on this and other extreme jobs. And perhaps those jobs would be lucrative enough to make up for the extra expense of installing one large press brake, including the extra foundation required.
According to sources, which press brake to choose depends on a fab shop’s current and potential product mix. One large press brake could tackle work requiring many feet of open space behind the tooling. But you also give up the flexibility and throughput offered by the tandem machine.
“One large press brake usually has more transport costs, more foundation costs, and the productivity will be less [than with a tandem machine],” said Lieven Vanhoenacker, a sales manager at LVD. “Still, it really depends on the operation’s product requirements.” Vanhoenacker added that many operations choose one smaller brake and then, as opportunities arise to bend longer parts down the road, connect another brake to make a tandem system.
Applications like light pole manufacturing may not need the flexibility: that is, forming smaller parts in the two smaller brakes and then forming a large part with the system in tandem mode. But they do need the higher speeds a tandem system offers. And pole manufacturers usually need not worry about having a large open space behind the tooling, though tandem brake manufacturers continue to offer deeper throats to accommodate a greater variety of jobs (see Figure 1).
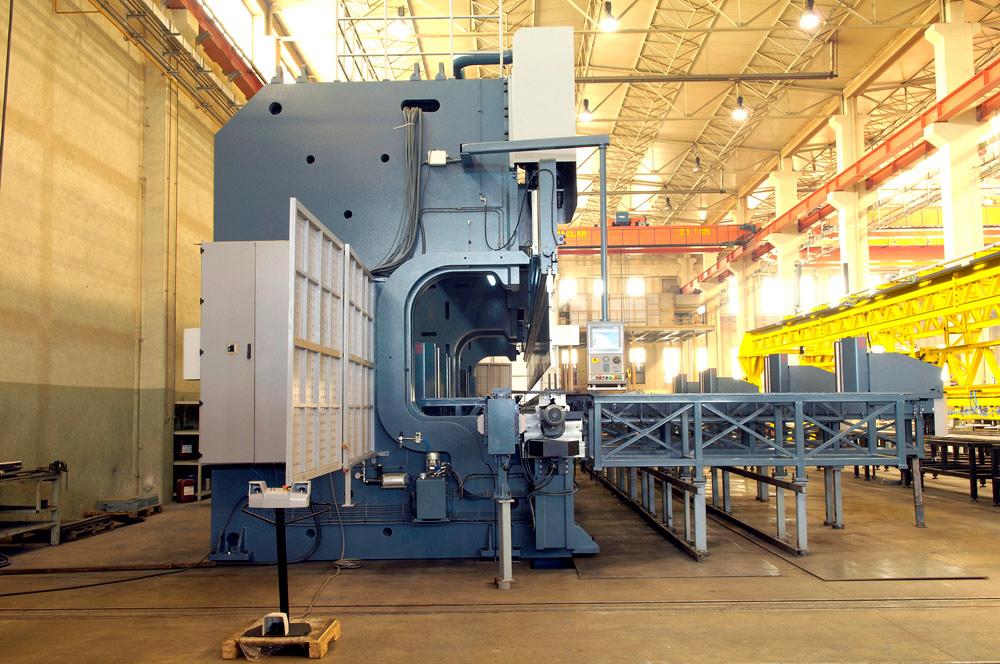
Figure 1
The throat on a tandem press brake can be quite deep. But if a job requires an extremely large amount of open space behind the tools, one large press brake may be the way to go. Photo courtesy of JMT USA.
Deciding which route to take involves more than looking at part geometries, or even at how many jobs need to be produced over a day or month. As Shane Reynolds, national sales manager for Salt Lake City-based JMT USA, put it, “Often managers need to look at where the business is today, where it has been, and future growth. How has the business changed or expanded over the past 20 years? And where is their business going?”
He added that this sometimes leads to some tough conversations, but before taking the plunge into a massive press brake investment, the answers to those questions can be extremely valuable.
Material Handling
How automated can a press brake operation be? To answer this question, shops may be able to identify product or part families, including parts that may be for different customers or even industries and yet share similar attributes such as size, shape, or material. Then the shop may be able to move forward with some type of material handling automation, if the investment makes sense for the product family’s volume and demand consistency (see Figure 2). Pole bending is a common example.
“For instance, some automated systems actually can lift one sheet and place it onto a shuttle table that feeds it into the press brake,” Durma’s Claude said, adding that such sheets often are moved in front of the tools, at which point individual pushers move the plate into position between the tools and against positioners in front of and behind the tools.
Those positioners, again, can also act as a frontgauge and backgauge. These pushing devices position large workpieces throughout the forming cycle. “As you start forming up, you no longer have a workpiece edge parallel to the floor,” Claude said. “So gauging and part manipulating is typically done with devices with large vertical surfaces on them, so they can still manipulate the piece after it’s formed.” Think of a typical backgauge, with fingers that may be only a half inch or so tall. In these applications, Claude said, they can be a foot tall.
Then you need to get these large formed parts out of the brake. Light pole manufacturers have ejector systems that push the pole out the side to another material handling system, like a roller conveyor. These pushers may be mounted below or above the bed, or they may be mounted to the material handling table (see Figures 3 and 4).
“Then you have the issue of scraping these workpieces across the die [during part ejection],” Claude said, adding that systems can be integrated in which rollers emerge from below to lift the workpiece off the surface of the die shoulders, allowing the piece to roll smoothly out of the work envelope.
Although not necessarily used for pole bending, sheet followers can also help make the forming process easier and eliminate the need for a crane to hold the workpiece in place. These followers, designed for large-workpiece bending, are a CNC axis. As the ram pushes into die and metal, the followers know at what speed and angle the sheet is being bent, and they help support the work as it goes up and releases downward.
“Imagine you had a pan that’s 20 feet long with a 4-inch flange and 40 inches hanging out the front side,” Claude said. “If you have followers, you can bend that part with one operator.”
According to sources, the most common type of material handling aid in high-product-mix operations remains a dedicated crane (see Figure 5). Some mount directly to the machine frame. No longer does the brake operator need to wait for an overhead crane to become available, and neither do other people need to wait for the crane as it’s tied up at the brake. All that waiting can put a serious strain on overall shop throughput.
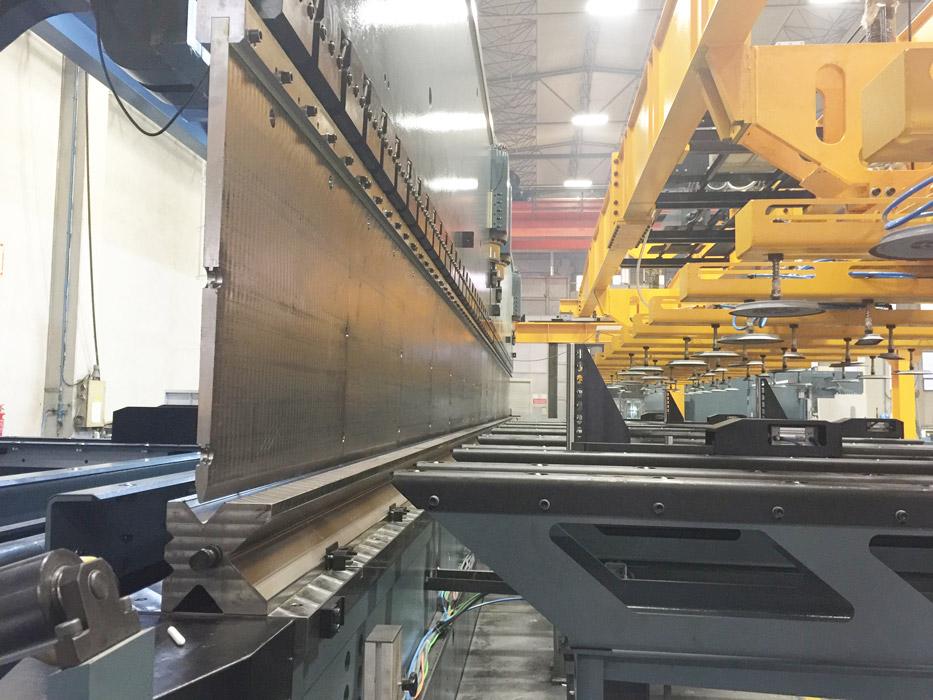
Figure 2
In this automated setup, a dedicated material handling system lifts the blank and places it on the feed table in front of the tandem press brake. Photo courtesy of Durma USA.
Press Brake Operation
Such material handling automation has a direct and obvious effect on throughput and forming cycle time. But for those shops in which the range of work is just too diverse, sources said they must look to less obvious factors in the cycle time equation.
For one thing, ensure that the machine runs as it should and is calibrated properly. Handling large parts, backgauges (and sometimes frontgauges) need to move significant distances, and the distance between the center of the V die and the surface of the gauge needs to be exact. If the actual positions of the backgauges don’t match the positions given in the controller, problems ensue, and bending cycle times grow ever longer as operators struggle to make it work.
“Proper calibration is especially critical when you’re making a part that’s spanning the difference between two machines,” JMT’s Reynolds said. He added that complex, coordinated backgauging between the two brakes needs to be working properly. And when operators are working with automatic feeding systems handle the material from in front and behind (again, acting both as a gauge and positioner), things can get especially complicated.
The beds of the two brakes should also be aligned. Most tandem machines have solid aligning methods involving secure bolt connections and precision leveling. If that alignment isn’t what it should be, the tools will be in the wrong position, and, again, problems ensue.
“The alignment here has to be spot-on,” Reynolds said. “[The beds] can be held together with brackets, push-and-pull bolts, and fastening bolts to hold them in place perfectly. Once they’re aligned, everything should work well. But that first time is critical to make sure everything matches up.”
Then come the tonnage considerations. Applications like light pole bending usually don’t push a typical tandem press brake to its limits. But many other applications do, especially considering the rising popularity of high-strength materials.
Often a tandem machine is simply two identical press brakes side by side, each with the same tonnage and bed length. But sometimes, because of various factors, one brake in a tandem arrangement may have a shorter or longer bed length and a lower or higher bending capacity. Regardless of the setup, tonnage per foot must be identical across both machines.
The same rules of side loading that apply to a single brake also apply to a tandem setup. If a workpiece is placed in a way such that one brake has forming pressure on just one side, repeatedly, the hydraulic components of that cylinder may wear prematurely.
“For example, if you continually load the tandem machine on the right side, where the part is extending to the second machine only several feet, you will get premature seal wear on your Y2 cylinder on the left machine,” Reynolds said. “It will heat up and prematurely wear, because that cylinder is being overworked compared to the other cylinder.”
Most important, say sources, is to never exceed the tonnage rating; this includes both the press brake and tooling. A shop should invest in a healthy tonnage buffer to avoid pushing the tonnage over the limit. And with today’s use of high-strength material, hardened tools designed to handle such material (with large radii, 10 to 12 times the material thickness) are a must.
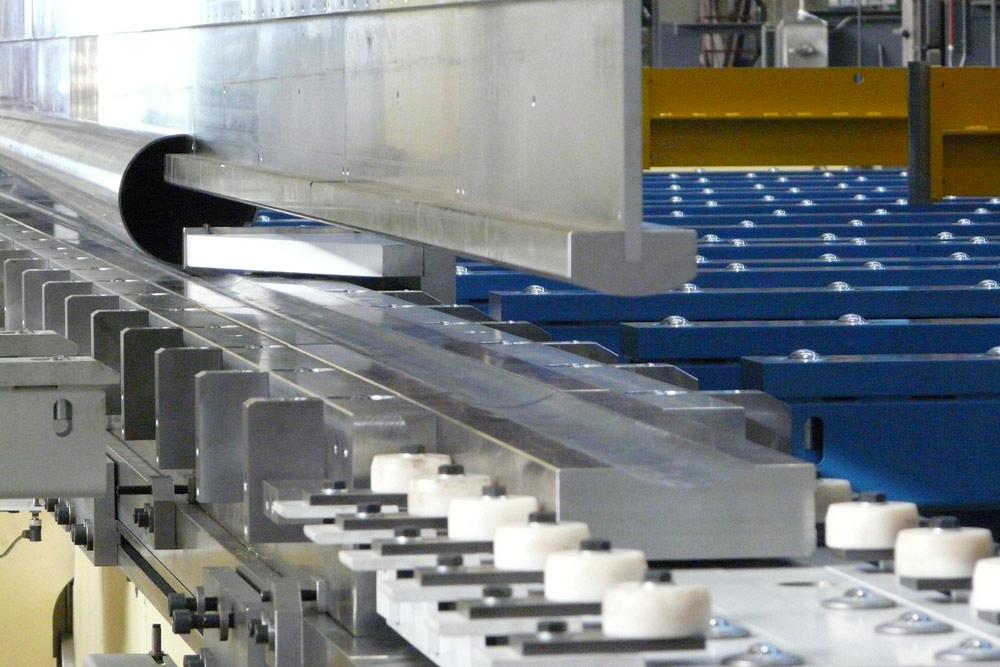
Figure 3
A pusher ejects a workpiece out the side of a tandem press brake. Photo courtesy of LVD Strippit.
“Make sure you’re within the comfort zone of what you’re trying to accomplish,” Reynolds said. “If you need 30 tons per foot, and your tools can handle up to 32 tons per foot, that’s probably not a good idea. If the material is just a little bit harder [than what’s specified], you won’t be in a good situation. You need a good buffer to account for that variation.”
Claude added another factor that has become almost a given: “You need a good, accurate automatic crowning system. When the control receives the information, it should calculate how much crowning is required to offset the deflection.”
“Crowning is really the most important element,” Vanhoenacker said, adding that crowning technology especially shines in tandem systems. “Modern systems synchronize the cylinders—two or [with tandem systems] four or [with tridem machines] even six—every 5 milliseconds,” he said. “The system continually checks to ensure you have constant straight-line movement in the machine.” (A tridem press brake is three machines connected together.)
Tooling Effects
In a high-product-mix operation, sources agreed that tooling changeover is one of the biggest causes of downtime in heavy bending. Changing over such large tools can take hours.
The options abound to shorten this time. Less expensive options include investing in or fabricating die carts to aid in removing and installing the massive punches and dies. The process still takes quite a while, but at the very least, the operator won’t need to wait around for a fork truck.
Another option is to invest in segmented tooling, which makes the tools easier to replace. Another tooling investment to consider are punches in which you can change out the tip radii. Operators still need to change out the tips manually, but it’s much less arduous than changing out an entire punch. It also encourages operators to use the right punch radius for the application—instead of inadvertently putting a crease in the bend from using a tip radius that’s too narrow for the job.
Probably the most effective option is also the most expensive: variable-width V dies. In air bending, the resulting radius depends on the die-opening width, and in a large-scale bending situation, changing out a die to one with a different width can take hours. A variable-width V die, controlled by the CNC, can change widths in a few minutes and eliminate the need to change out the V die (see Figure 6).
Sources cautioned that variable-width V dies don’t make sense for every application. “If you have a [variable-width] V die, know that you often can’t bend downwards,” said Vanhoenacker.
He explained that if a workpiece has to be flipped to form a tall negative flange, clearance issues can arise with a variable-width V die. The die shoulders sit on a wide block with tracks, which allow them to move to create a wider or narrower opening. A tall negative flange can collide with that block.
Overall, the tooling investment, though significant, can pay off. It again goes back to looking at the overall forming cycle and uncovering which tasks really take the most time. Waiting for a crane takes time. Positioning the workpiece takes time. Offloading can seem like a slow process—but changing out tools can eat up an entire day.
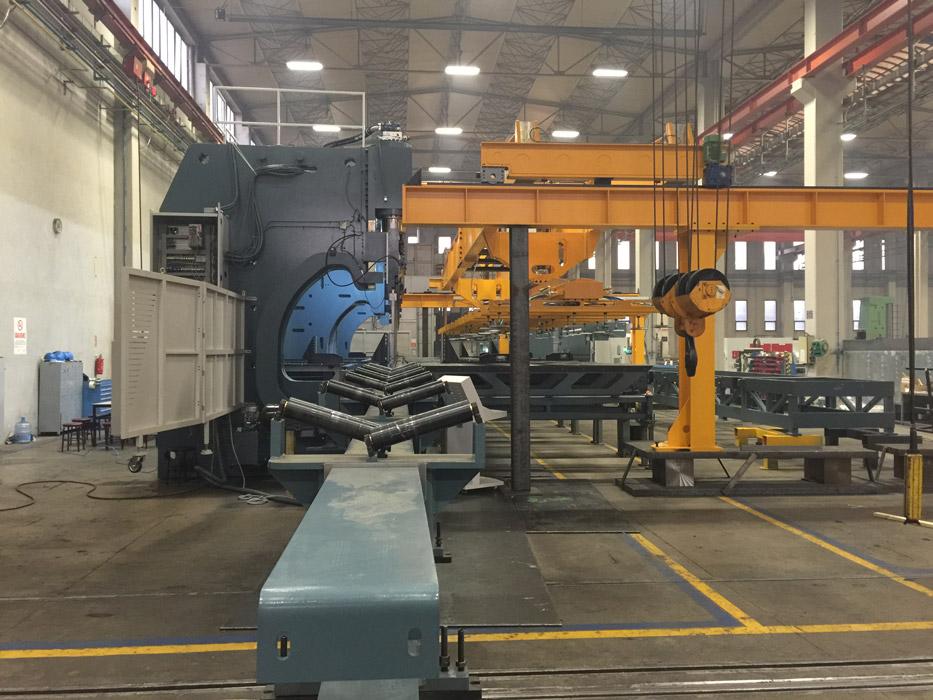
Figure 4
In this setup, formed workpieces are sent out the side of the brake to a roller conveyor. Photo courtesy of Durma USA.
“Some companies put spacers or plates to adjust the V dies manually,” Reynolds said, “but the tool still can take hours to adjust. Yes, if they spend the money upfront, [CNC adjustable V dies] can seem expensive, sometimes $100,000 or $200,000. But now bottom die adjustment takes a few minutes versus a couple of hours. How much does that save you during production?
“If you ask owners and operators out there [who have purchased a large press brake] what they would have done differently, they often say they would have gone with a CNC adjustable V die,” Reynolds continued. “I haven’t run into one yet who said they wish they didn’t make the investment.”
Durma USA, 800-367-6911, www.durmausa.com
JMT USA, 877-268-8671, www.jmtusa.com
LVD Strippit, 800-828-1527, www.lvdgroup.com
About the Author
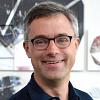
Tim Heston
2135 Point Blvd
Elgin, IL 60123
815-381-1314
Tim Heston, The Fabricator's senior editor, has covered the metal fabrication industry since 1998, starting his career at the American Welding Society's Welding Journal. Since then he has covered the full range of metal fabrication processes, from stamping, bending, and cutting to grinding and polishing. He joined The Fabricator's staff in October 2007.
Related Companies
subscribe now
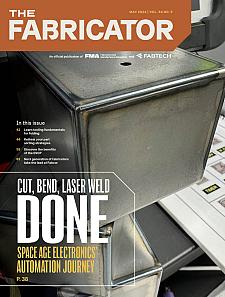
The Fabricator is North America's leading magazine for the metal forming and fabricating industry. The magazine delivers the news, technical articles, and case histories that enable fabricators to do their jobs more efficiently. The Fabricator has served the industry since 1970.
start your free subscription- Stay connected from anywhere
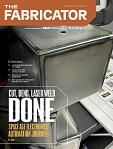
Easily access valuable industry resources now with full access to the digital edition of The Fabricator.
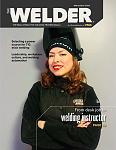
Easily access valuable industry resources now with full access to the digital edition of The Welder.
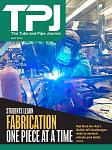
Easily access valuable industry resources now with full access to the digital edition of The Tube and Pipe Journal.
- Podcasting
- Podcast:
- The Fabricator Podcast
- Published:
- 04/16/2024
- Running Time:
- 63:29
In this episode of The Fabricator Podcast, Caleb Chamberlain, co-founder and CEO of OSH Cut, discusses his company’s...
- Industry Events
16th Annual Safety Conference
- April 30 - May 1, 2024
- Elgin,
Pipe and Tube Conference
- May 21 - 22, 2024
- Omaha, NE
World-Class Roll Forming Workshop
- June 5 - 6, 2024
- Louisville, KY
Advanced Laser Application Workshop
- June 25 - 27, 2024
- Novi, MI