Contributing Writer
- FMA
- The Fabricator
- FABTECH
- Canadian Metalworking
Categories
- Additive Manufacturing
- Aluminum Welding
- Arc Welding
- Assembly and Joining
- Automation and Robotics
- Bending and Forming
- Consumables
- Cutting and Weld Prep
- Electric Vehicles
- En Español
- Finishing
- Hydroforming
- Laser Cutting
- Laser Welding
- Machining
- Manufacturing Software
- Materials Handling
- Metals/Materials
- Oxyfuel Cutting
- Plasma Cutting
- Power Tools
- Punching and Other Holemaking
- Roll Forming
- Safety
- Sawing
- Shearing
- Shop Management
- Testing and Measuring
- Tube and Pipe Fabrication
- Tube and Pipe Production
- Waterjet Cutting
Industry Directory
Webcasts
Podcasts
FAB 40
Advertise
Subscribe
Account Login
Search
Are company politics undermining your robotic projects?
- By Jim Berge
- January 10, 2006
- Article
- Automation and Robotics
![]() |
"Politicians and diapers should be changed often, and for the same reason."
Whether or not you agree with this statement, it actually says more about the process of politics than politicians. Those stuck in an environment of political fervor may find it very difficult to break free and see things clearly. One of my earlier articles, How to Kill a Robotic Project in Five Easy Steps, addressed some of the more common causes of robotic implementation failure, but it didn't address fully one of the most difficult problems to overcome: company politics.
A company's political environment can do more damage to a robot project's success than most other factors. Problems like poor part repeatability or a part design unsuitable for robotic welding can be solved relatively easily, but to solve political problems most often requires cultural change, one of the most challenging processes an organization can undertake. This article identifies some of the problems political grandstanding and misunderstandings cause and suggests ways to overcome them.
The success of robot projects seems to be particularly vulnerable to problems caused by internal politics. Perhaps this is because of an anthropomorphism that makes a robot seem so close in functionality to a human being. Since the industrial robot revolution began a couple of decades ago, factory floor workers have feared losing their jobs to these amazingly flexible, programmable machines, because unlike a lathe or machining center, they really do mimic the human arm motion. Although it is receding gradually and continuously, that fear of robots still exists today, even though most manufacturers are embracing the technology.
Problems Politics Pose
Because robotic technology seems to struggle in highly political environments, special care must be taken to foster a culture in which robots will thrive. Let's begin by identifying some problems company politics causes.
1. Politics stand in the way of personnel development.
A highly political atmosphere can deemphasize training and overemphasize actions that deter success. For example, a company that makes seniority the only criterion for advancement into robotic technician or programmer jobs suffers.
Seniority is an important criterion for advancement, but if it is the only standard used to choose robot programmers, technicians, and operators, then unqualified people may be chosen for these jobs, which happens often. It is easy to see how the robot's performance then can suffer as well as the ill-prepared individual put in charge of the robot.
I once visited a factory that had a union policy of rotating workers regularly in and out of the robot cell. The problem with that policy was that no one ever had enough time to become familiar with the equipment—how to operate it, how to troubleshoot, or how to keep the robot running. I advised managers that their robots would never work to full capacity until they stopped the rotation and devoted some operators to the robot department. They chose to continue the rotation policy because of political pressure. Needless to say, the robots never performed even close to their potential, and the company and its customers suffered as a result.
On the other hand, many union shops are very successful robotics users. Whether or not they are union, the factories that succeed with robotics are those in which workers and management have learned to support each other in their initiatives to save jobs by keeping the company healthy. In a tough global marketplace, robots often are the only means of staying competitive and creating jobs, which is good for both labor and management.
2. Politics divert focus from performance and turn it toward personal agendas.
I have seen it too many times: Someone—whether on the shop floor or in the front office—has problems with productivity, quality, or efficiency and needs a scapegoat. Many upper managers are not tuned in to the everyday workings of their factories, so it's easy for operators, technicians, or engineers to pull the wool over their eyes and blame the robot. For example, almost every time a welding robot misses the welding joint, it is accused of "not repeating" its path. But it is very uncommon for a robot actually to misposition a weld.
In most instances, when a robot misses the welding joint, the true cause is something other than the robot. It's easy to blame the robot because workers (including the one assigning blame) often don't understand the true root cause of the problem. Robots are more complex than most factory automation equipment. They are more unfamiliar and more difficult to fine-tune to the high degree of performance that their owners expect. When political posturing occurs, it's often the robot's reputation and performance that suffer. Only by defining the real problems can the real solutions be found.
3. Politics become a substitute for good policies.
The problems with robot systems can be solved by identifying the root causes of failure. Putting good policies in place can eliminate these causes. But it doesn't always happen that way. Often the root causes cannot be identified accurately because no one is willing to shoulder the responsibility for the failure. If the root cause is poor component parts coming from upstream, for example, it may be difficult for the upstream workers to admit they are making bad parts, especially in politically charged environments.
The more complex the robotic system or the parts being processed by the robot, the easier it is to hide root causes and pass the buck. The problem could be caused by the incoming steel, the laser or plasma cutter, the beveler, the press brake, the vendor supplying any one of these processes, the janitor or ... the list goes on. Unfortunately, some employees who engage in finger-pointing do so out of justified fear of reprimand because of misguided company policies.
THESolution
The word "the" is emphasized in this heading for a reason. One might rightfully ask, "You mean there is a single solution to these problems?" The answer is, in a way, yes, because there is one thing that will disarm misguided political posturing and reveal the real solution for all to see: honesty.
If workers at any level of the organization fear being truthful about their mistakes, of course they will try to hide them or, at the very least, minimize them. Workers will not volunteer the whole truth if they fear being reprimanded for what actually are typical everyday machine or process failures. When workers are allowed to make honest mistakes and discuss them openly, in an environment that encourages process improvement in a true team-building spirit, then pretension fades away. It is replaced by a pragmatism that attacks the core of the problem without identifying personal blame, which results in an environment that is more productive and more conducive to the flow of valuable ideas.
Honesty and openness can disarm much of the political atmosphere that can harm robotics installations. But what does this look like in practice?
Putting the Right People in Charge
Let's start with the need to put the right people in charge of robots. No one would suggest rationally that the person with the most seniority should become a company's chief financial officer. That position requires education and a certain skill set to handle financial matters properly, a skill set that many people just don't have. Why should it be different when it comes to the skills required to handle robots?
A strategy for ensuring the right personnel are in charge of robots might include the following:
- Place robot operators, programmers, and technicians in a unique classification, and dictate that this classification requires a certain skill set. A robot programmer or technician probably should be paid a bit more than, say, a welder, because these individuals are responsible not only for the weld quality, but also the performance of the robot, which is a very expensive and complex investment.
- If no one in the company possesses the necessary training and skill set, then find or set up a training program to provide it.
- Test individuals for aptitude and interest, and select the best person for the job, with the understanding that this employee also will become personally responsible for the performance and upkeep of an expensive piece of technology. Play no games, no favorites, no politics, just find a logical way to determine who is best-qualified for this important job. The company also must provide the proper tools and support along with the responsibility.
Minimizing the Effects of Personal Agendas
Several factors can help keep personal agendas from detracting from the robot's performance and reputation:
- One of the best defenses against the wool-over-the-eyes or fleecing technique is for managers and supervisors to understand the technology fully. It is surprisingly common for those with authority over robots to have little knowledge of what it takes to make robots perform well.
- Make the robot's performance a team effort. Doing so minimizes the effects of individual egos and neutralizes individual agendas. With a real team effort, it becomes more difficult to hide mistakes that ought to be brought into the open and discussed.
- Offering a bonus or some other reward to a team—preferably a cross-functional team—can keep everyone honest and striving toward the same goal.
Creating Good Policies
Good policies can overcome the negative effects of stifling politics. Clear policies and procedures are necessary to define:
- How the robots are to function.
- How the robots are expected to contribute to the bottom line, and at what level of performance they need to function to provide these returns.
- What gross results are expected from the robotic installations in terms of money savings, increases in throughput, increases in quality, and impact on safety and ergonomics.
- Who can become an operator/programmer/technician.
Just as in a good marriage, constant and effective communication is required to achieve the best results when introducing robots into your factory. The worst things to do are hide the facts, bring in robots without informing or gaining the trust of the workers, and manage the project with the outdated bossismapproach of "I'm the boss, you're the worker, so just do as I say." The complex and unique nature of robotics makes it even more important to live according to these fundamentals.
This article is not about ethics, but in the realm of robotics, as in life, an ethical and honest approach can have a positive effect on performance. Keep it honest, make the rules clear and easily understandable, let everyone share in the advantages and benefits that come with robotic automation, and emphasize and reward good teamwork. These simple guidelines will contribute toward an atmosphere in which less energy is wasted protecting political kingdoms and more is spent on productivity and success at every level.
About the Author
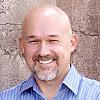
Related Companies
subscribe now
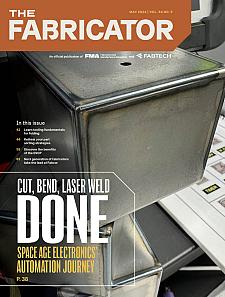
The Fabricator is North America's leading magazine for the metal forming and fabricating industry. The magazine delivers the news, technical articles, and case histories that enable fabricators to do their jobs more efficiently. The Fabricator has served the industry since 1970.
start your free subscription- Stay connected from anywhere
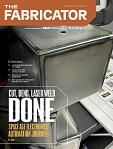
Easily access valuable industry resources now with full access to the digital edition of The Fabricator.
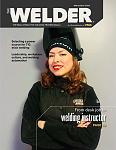
Easily access valuable industry resources now with full access to the digital edition of The Welder.
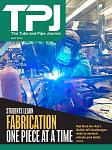
Easily access valuable industry resources now with full access to the digital edition of The Tube and Pipe Journal.
- Podcasting
- Podcast:
- The Fabricator Podcast
- Published:
- 04/16/2024
- Running Time:
- 63:29
In this episode of The Fabricator Podcast, Caleb Chamberlain, co-founder and CEO of OSH Cut, discusses his company’s...
- Trending Articles
Capturing, recording equipment inspection data for FMEA
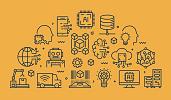
Tips for creating sheet metal tubes with perforations
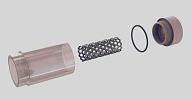
Are two heads better than one in fiber laser cutting?
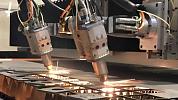
Supporting the metal fabricating industry through FMA
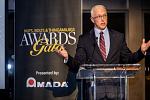
Omco Solar opens second Alabama manufacturing facility
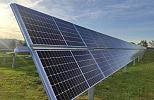
- Industry Events
16th Annual Safety Conference
- April 30 - May 1, 2024
- Elgin,
Pipe and Tube Conference
- May 21 - 22, 2024
- Omaha, NE
World-Class Roll Forming Workshop
- June 5 - 6, 2024
- Louisville, KY
Advanced Laser Application Workshop
- June 25 - 27, 2024
- Novi, MI