Senior Editor
- FMA
- The Fabricator
- FABTECH
- Canadian Metalworking
Categories
- Additive Manufacturing
- Aluminum Welding
- Arc Welding
- Assembly and Joining
- Automation and Robotics
- Bending and Forming
- Consumables
- Cutting and Weld Prep
- Electric Vehicles
- En Español
- Finishing
- Hydroforming
- Laser Cutting
- Laser Welding
- Machining
- Manufacturing Software
- Materials Handling
- Metals/Materials
- Oxyfuel Cutting
- Plasma Cutting
- Power Tools
- Punching and Other Holemaking
- Roll Forming
- Safety
- Sawing
- Shearing
- Shop Management
- Testing and Measuring
- Tube and Pipe Fabrication
- Tube and Pipe Production
- Waterjet Cutting
Industry Directory
Webcasts
Podcasts
FAB 40
Advertise
Subscribe
Account Login
Search
3 questions to ask for better laser cutting
Without the fundamentals, getting a clean cut edge is an uphill battle
- By Tim Heston
- June 28, 2016
- Article
- Laser Cutting
Brent Donner is known for pushing the envelope. Back in the 1990s he went to college to study metallurgy. That experience gave him a foundation for how different metals react to different manufacturing methods. He also has a natural knack for asking the right questions and experimentation.
All this has helped him build a reputation as a laser cutting operator who can tweak settings and achieve cut edges in thick plate that few others can—cutting material 1.5 inch (and even thicker) cleanly, without a trace of burr. “For some reason, it has always come naturally for me,” he said. “I don’t know why.”
Since 2007 Donner has consulted with various fabricators, helping them get more out of their laser cutting systems. In 2008 he launched a job shop in New Ulm, Minn., DLC Manufacturing and Fabrication. It remains a small shop with a handful of highly skilled technicians (people who will be featured in the pages of this magazine later this summer).
When Donner visits operations as a consultant, quite often he sees how people miss some of the fundamentals of laser cutting. So before delving into operational complexities, he first asks a few basic questions.
1. Are you cleaning your cutting lens or cover glass properly?
Cleaning procedures differ depending on the laser type. For a fiber or disk laser, operators need to clean the cover glass, or shoots glass, protecting the optics in the cutting head.
When he purchased his first fiber machine, Donner said he referred to the manufacturer’s recommendations. From this, Donner said he has tweaked and perfected his cleaning method, extending the life of the cover glass even longer. His method is proprietary, but generally speaking, he scrutinizes the cover glass for any remaining film after cleaning and uncovers ways to remove it. After this, the glass is clear, film-free, and ready for cutting. “In our fiber laser, we usually go six to eight months before we need to use a new [cover] glass,” Donner said. “But the cutting conditions have to be just right.”
For a CO2 laser, operators need to clean the cutting lens. Donner and his team cleans his lasers using TRUMPF’s Topol polish. “A lot of operators really don’t know how to apply it,” Donner said. “Often when I walk into a facility, I see that the lens is severely scratched. Instead of polishing it regularly, they just put in a new lens. But over the long term, that can get really expensive.”
So how do you teach an operator how to properly apply lens polish? “Every operator is different,” he said. When observing them, Donner pays attention to their dexterity, cleaning motion, and the force they apply to the lens, then determines how they should perfect their polishing technique. They never should apply excessive pressure, which can scratch the lens severely. At the same time, they need to apply enough pressure to remove contaminants effectively. It can be quite the balancing act.
Donner applies a judicious amount of polish in a circular pattern across the lens, but this technique just happens to work for him. “You need to figure out how the operator works.”
To really polish a lens correctly, an operator needs to see the imperfections. For CO2 systems, Donner suggests purchasing a polarizer, which costs a few hundred dollars. But when it’s used properly, the investment pays for itself in no time. The operator simply places the lens on top of the device, which shines a bright light through the lens from below, a little like the base of an overhead projector used in schools. “As you turn the polarizer’s top lens, it will polarize the cutting lens you place on top, and, if the lens is bad, you will be able to see internal cracks and other imperfections.”
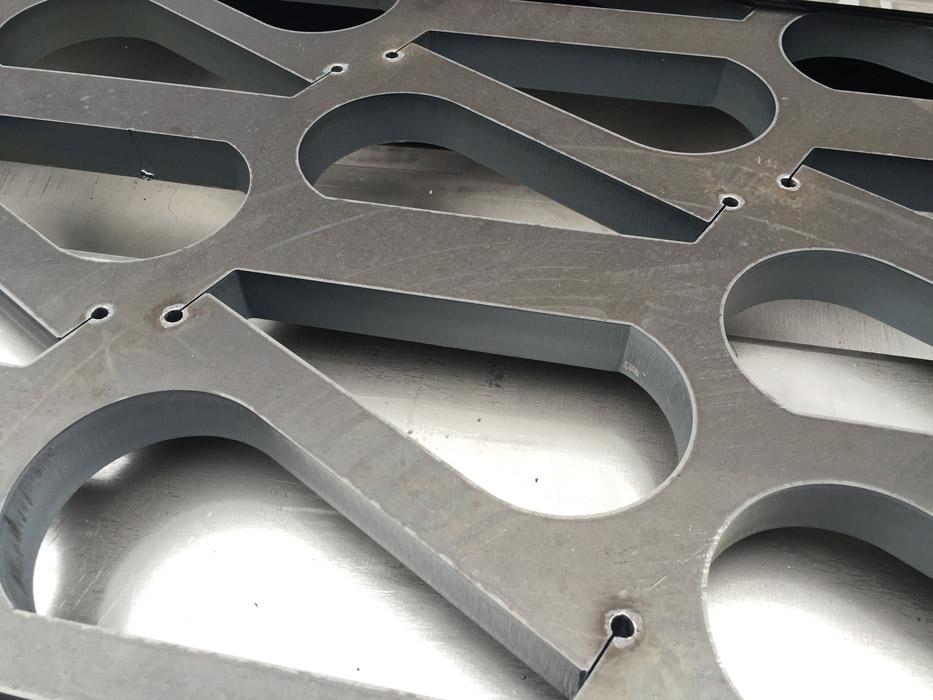
This 1-in.-thick plate, cut at a Utah job shop, was processed at 28 IPM with a 1-second pierce on a 5-kW laser that’s a dozen years old. Donner set this machine’s cutting conditions to match the material and environment, accounting for the Utah shop’s high altitude and dry air.
Donner has followed a regular, careful cleaning regimen for his 6-kW CO2 laser for almost a decade, and even in this high-powered system, he said that the shop needs to replace the cutting lens only every six to eight months.
2. Is your nozzle really centered?
To perform a tape shot, operators shoot the beam at low power through tape for about one second, then look at the resulting hole and make sure it’s centered.
“Operators take this tape, shine a light up to it, and they try to see if the hole is in the center,” Donner said. “But that hole might be only 1 mm across. How are you really going to see if that hole is centered to the nozzle? So I bring a 10X magnifying light, a Bausch + Lomb Sight Saver, with a 3⁄8-in.-diameter hole to look through. It’s the best $30 you’ll ever spend.
“I usually bring it to the shop, set it up, and tell the operator to look over my shoulder. I ask him, ‘Is this nozzle centered?’ And the operator usually sees it [in the magnifying light] and says, ‘Wow, I can actually see it.’ You may have been cutting at 80 inches per minute. But now, if you have the nozzle precisely centered, you will gain anywhere from 20 to 40 percent in your cutting speed, as long as your cutting conditions are correct.”
3. When was your last focus test?
Quite often Donner asks this question, and operators give him a blank look. “They sometimes don’t know what a focus-test program is.”
He clarified that on many modern machines, the focus test occurs automatically. On older machines, though, the actual test varies depending on the machine manufacturer. Some machine-makers have what they call “light tests” and other methods.
On an older Mazak machine, for instance, the beam turns on at low power, and the operator turns a knob and finds absolute focus by observing the beam color, which turns blue once it’s dialed in. “You then write the number down,” Donner said, “bring the head back up, do that three times in row, take an average of those numbers, and that’s the number you plug into the controller.”
In his shop, Donner runs TRUMPF lasers, which have a focus test that marks a series of lines of different widths on a coupon, the number of which depends on the lens diameter (3.75, 5, 7.5, and 10 in.). The test then engraves the controller settings next to those lines, giving each a positive number, negative number, or zero.
“You need to find the thinnest line in the coupon and make sure that the focus setting in the controller is at zero for that thinnest line,” Donner explained. If the thinnest line is at a -3, then the operator dials in the focus by 3 mm and retests until he sees that thinnest line is at zero.
Donner reiterated that the exact method for testing the laser focus depends on the machine manufacturer. Regardless, a fab shop’s technicians should know how to calibrate the focus so that the focus reading on the CNC matches the beam’s actual focus position in the workpiece.
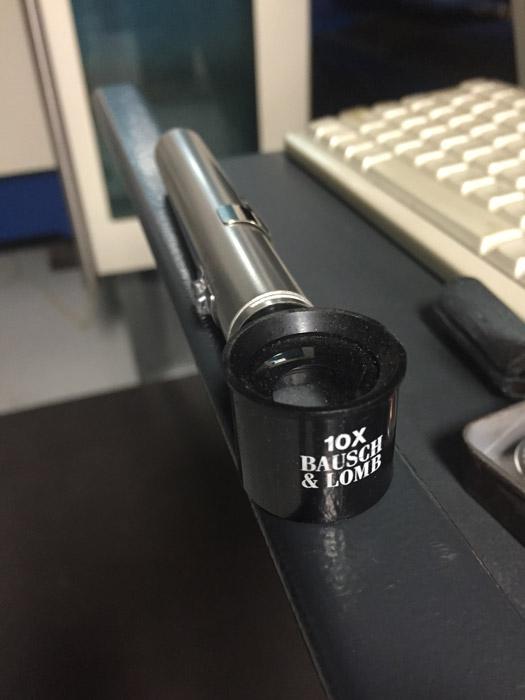
Donner’s shop uses this Bausch + Lomb Sight Saver to ensure the beam is truly centered in the nozzle.
A Foundation for Solid Cutting Conditions
These three fundamentals are just the beginning, of course. Shops may need to look into factors like shielding gas flow or adding extra protection to the beam delivery optics in the CO2 system. But these at least provide a starting point to develop finely tuned cutting conditions, which can vary, depending on a host of environmental factors, such as the material being cut and the shop’s location.
“If I have a 6-kW laser in Minnesota, it will not cut under the same conditions as a laser in Florida,” Donner said. “You have different temperatures, different humidity levels, and numerous other factors, so you need to adjust your laser to match those conditions.”
He added that developing good cutting conditions depends entirely on the job at hand, but conditions should be set only after the machine is as clean and calibrated as it should be.
In effect, these fundamentals really should be the starting line for optimizing the laser. Then it’s off to the races. Once you reach the finish line, the laser will cut so cleanly, with such fine edge quality, that deburring may no longer be needed for certain parts.
Donner summed it up: “Once you have these fundamentals, you can really dial in your parameters. Often you can get the machine to perform better than it did new.”
DLC Manufacturing and Fabrication Inc., 507-359-8050, www.donnerlaser.com
About the Author
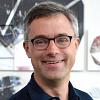
Tim Heston
2135 Point Blvd
Elgin, IL 60123
815-381-1314
Tim Heston, The Fabricator's senior editor, has covered the metal fabrication industry since 1998, starting his career at the American Welding Society's Welding Journal. Since then he has covered the full range of metal fabrication processes, from stamping, bending, and cutting to grinding and polishing. He joined The Fabricator's staff in October 2007.
Related Companies
subscribe now
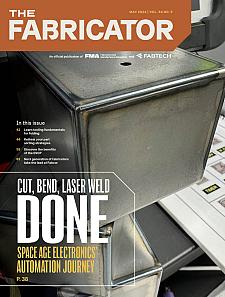
The Fabricator is North America's leading magazine for the metal forming and fabricating industry. The magazine delivers the news, technical articles, and case histories that enable fabricators to do their jobs more efficiently. The Fabricator has served the industry since 1970.
start your free subscription- Stay connected from anywhere
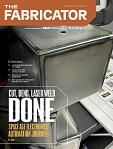
Easily access valuable industry resources now with full access to the digital edition of The Fabricator.
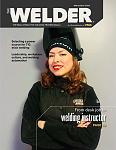
Easily access valuable industry resources now with full access to the digital edition of The Welder.
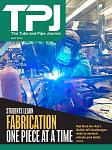
Easily access valuable industry resources now with full access to the digital edition of The Tube and Pipe Journal.
- Podcasting
- Podcast:
- The Fabricator Podcast
- Published:
- 04/16/2024
- Running Time:
- 63:29
In this episode of The Fabricator Podcast, Caleb Chamberlain, co-founder and CEO of OSH Cut, discusses his company’s...
- Industry Events
16th Annual Safety Conference
- April 30 - May 1, 2024
- Elgin,
Pipe and Tube Conference
- May 21 - 22, 2024
- Omaha, NE
World-Class Roll Forming Workshop
- June 5 - 6, 2024
- Louisville, KY
Advanced Laser Application Workshop
- June 25 - 27, 2024
- Novi, MI