President
- FMA
- The Fabricator
- FABTECH
- Canadian Metalworking
Categories
- Additive Manufacturing
- Aluminum Welding
- Arc Welding
- Assembly and Joining
- Automation and Robotics
- Bending and Forming
- Consumables
- Cutting and Weld Prep
- Electric Vehicles
- En Español
- Finishing
- Hydroforming
- Laser Cutting
- Laser Welding
- Machining
- Manufacturing Software
- Materials Handling
- Metals/Materials
- Oxyfuel Cutting
- Plasma Cutting
- Power Tools
- Punching and Other Holemaking
- Roll Forming
- Safety
- Sawing
- Shearing
- Shop Management
- Testing and Measuring
- Tube and Pipe Fabrication
- Tube and Pipe Production
- Waterjet Cutting
Industry Directory
Webcasts
Podcasts
FAB 40
Advertise
Subscribe
Account Login
Search
Aspectos generales y beneficios del desbarbado moderno
Sopesar todas las opciones es un gran paso adelante
- By Tony McCue
- November 12, 2010
- Article
- Finishing
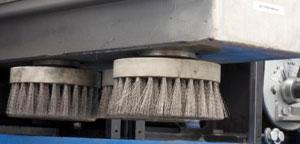
Figure 1: Las máquinas desbarbadoras multimedia usan tanto cintas abrasivas como cepillos. Estos cepillos de taza o de disco han sido sacados para inspección.
La tecnología de la fabricación ha avanzado de manera espectacular. Los láseres son más poderosos que nunca; los sistemas punzonadores de torreta están haciendo más formado; las máquinas de chorro de agua son algo común. Y todos estos sistemas de obtención de piezas de trabajo generan rebabas o esquinas filosas que son lastres potenciales. Es aquí donde puede ser de utilidad el desbarbado.
Antes de elegir una máquina desbarbadora, defina los bordes deseados que requieren sus partes. Esto suena simple; después de todo, la mayoría de las publicaciones dice que las partes deben ser “libres de rebabas”. Pero, ¿qué nivel de desbarbado requiere realmente esta especificación? Ningún estándar industrial define qué constituye exactamente algo “libre de rebabas”, y no hay dos personas que coincidan en qué tan bueno es “demasiado bueno”.
Tárdese demasiado desbarbando, y los costos se disparan; demasiado poco tiempo, y la parte puede requerir volver a trabajarse. Actualmente, el fabricante tiene la responsabilidad de encontrar el balance óptimo.
Tipos de Rebabas
Quienes procesan hojas metálicas y placas de acero se enfrentan con dos tipos de rebabas, mecánicas y térmicas. Una rebaba mecánica se crea por cizallamiento, punzonado, aserrado, rebajado y perforado. Herramientas filosas, separación adecuada del dado, así como ritmos de alimentación precisos reducen sustancialmente las rebabas, pero no las eliminan.
Una rebaba térmica usualmente es referida como desperdicio o escoria. Esta rebaba ocurre durante el corte con plasma o láser. La mezcla de combustible y la velocidad de corte adecuada, el reemplazo de puntas de quemado, y la óptica y gases correctos en los láseres pueden reducir sustancialmente las rebabas.
Las escotaduras, o marcas de recorte, son similares a las rebabas, pero en los bordes verticales de la parte, creadas durante el punzonado de torreta por un movimiento repetitivo de la herramienta de escotar. El desbarbado tradicional cubre solamente la superficie de trabajo, no esas escotaduras en los bordes verticales. Note que ninguna máquina de desbarbado de cinta ancha puede eliminar marcas de recorte de todo el borde de la parte.
Aspectos Generales de las Máquinas
Los sistemas de desbarbado usan cintas, cepillos o una combinación de éstos (vea la Figura 1 y Figura 2). Los cepillos y las cintas pueden configurarse para la aplicación. Hace años, la máquina de cinta abrasiva de una sola cabeza era lo más común. Ésta eliminaba la rebaba vertical y creaba un acabado de grano o cepillo. Pero también dejaba rebabas horizontales y orillas filosas. En otras palabras, muchas rebabas se quitaban—pero no se eliminaban.
De ahí el porqué de que las máquinas multimedia de cintacepillo se hayan vuelto más populares durante los últimos 20 años. Actualmente, muchos se dan cuenta del beneficio de tres o cuatro cabezas en una máquina y quieren la flexibilidad de combinar cintas abrasivas y cepillos. Éstos eliminan rebabas de forma efectiva y producen partes con superficies y orillas lisas.
La cinta abrasiva va alrededor de un rodillo de contacto, o tambor, y un rodillo de tensión. El rodillo de contacto trabaja con el rodillo de tensión para tensar y mantener en su sitio la cinta abrasiva. Los tambores de contacto, usualmente de hule, pueden variar ampliamente en tamaño, pero con frecuencia tienen un diámetro de entre 6 y 11 pulgadas.
La dureza del hule del tambor de contacto—denominada dureza Shore o durómetro—también varía, usualmente de 25 a 85 Shore. El hule de 25 Shore es suave y flexible, lo cual le permite adaptarse a la forma de la parte; el hule de 85 Shore es duro y más adecuado para la eliminación de material involucrado en el granulado.
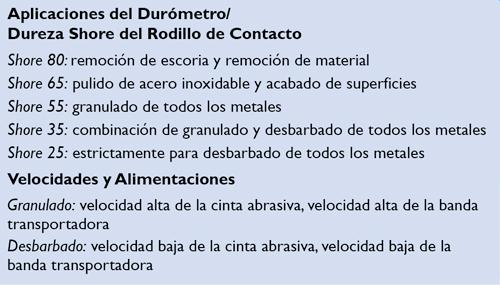
Figura 4: La gráfica de velocidad/alimentación muestra que un rodillo de contacto más duro a una velocidad alta, combinado con una velocidad alta de la banda transportadora, producirá un acabado de grano.
Típicamente, el rodillo de contacto es dentado a un ángulo de 30 a 60 grados. Treinta grados es mejor para un acabado ligero, mientras que un dentado a 60 grados es más agresivo, usado con frecuencia para remoción de material o remoción de escoria pesada del corte con plasma.
El tambor de contacto es realmente la “herramienta de corte” de la máquina, y su velocidad determina el acabado. En años pasados, la cabeza abrasiva usualmente tenía una sola velocidad, pero actualmente los sistemas de velocidad variable se han vuelto algo común. Sobre todo, esas velocidades variables le permiten al sistema obtener el mejor uso del material abrasivo moderno. La velocidad de la banda que transporta la parte a través de la máquina también determina el acabado.
El desbarbado y el granulado, cada uno requiere una velocidad y alimentación diferente. Combine un rodillo de contacto suave con los abrasivos correctos a una velocidad lenta, y una banda transportadora que alimente lentamente la parte por abajo, y usualmente usted puede obtener una parte desbarbada de manera efectiva. Esta combinación produce una elasticidad del abrasivo en 3-D que reacciona con alta presión de abrasión sobre rebabas y bordes, creando muy poca presión sobre la superficie de la parte (vea la Figura 3). Esto también hace posible eliminar rebabas verticales y redondear bordes cuando se usa en combinación con un cepillo. Ajustar la máquina en la configuración opuesta—un rodillo de contacto duro que mueve al abrasivo a alta velocidad, y una banda transportadora rápida—producirán un acabado de grano sobre la superficie de la parte (vea la Figura 4).
¿En Húmedo o en Seco?
¿Debe usar una máquina desbarbadora en seco o en húmedo? Es un viejo debate, y a decir verdad, cada sistema tiene sus ventajas y desventajas.
Las máquinas desbarbadoras en mojado llenan de refrigerante el área de trabajo. La gravedad regresa el refrigerante con suciedad y partículas del rectificado a un filtro que captura las partículas y recicla el refrigerante hacia el tanque principal. Algunas máquinas tienen un sistema de filtrado como unidad independiente, mientras que otros tienen una unidad de filtración debajo de la máquina para ahorrar espacio. Los sistemas en húmedo eliminan la necesidad de un colector de polvo, ofrecen una larga vida de la cinta y minimizan riesgos al trabajar con metales diferentes.
Sin embargo, los sistemas en húmedo requieren un estricto régimen de mantenimiento. Ciertas mezclas de refrigerante trabajan mejor con ciertos materiales, y ocurre corrosión excesiva si no se mantienen mezclas adecuadas de agua y lubricante. Numerosos factores afectan la química del agua en una máquina. Por ejemplo, el agua regular de la llave trae disueltos sodio, calcio, magnesio y azufre, y conforme el agua se evapora del tanque, va dejando estos minerales dañinos.
La diaria limpieza y monitoreo de la composición química del refrigerante son vitales para un desempeño óptimo de la máquina. Algunas máquinas en húmedo tienen acero inoxidable en áreas críticas para evitar la corrosión. Unas cuántas máquinas están hechas por completo de acero inoxidable para adaptarse incluso a las aplicaciones más rigurosas.
La vida de los rodamientos es el problema más difícil con las máquinas en húmedo. En algunos sistemas más nuevos, cojinetes presurizados evitan que entre la humedad, pero ésta es una tecnología relativamente nueva un tanto sin probar. Como siempre, el mantenimiento adecuado es la solución más efectiva.
Las máquinas en seco pueden requerir menos mantenimiento y brindar una vida más larga, y pueden ser menos caras de comprar y operar. Sin embargo, es muy importante estar concientes de los problemas potenciales. El polvo de aluminio se puede acumular en la tubería, y basta una sola chispa para iniciar un incendio. De nuevo, el mantenimiento es crítico, y limpiar la máquina después de cambiar de un material a otro es esencial.Las máquinas en seco también pueden dejar partículas de polvo y arena sobre la superficie de la parte. Si esas superficies planas no se limpian, pueden desgastar prematuramente el herramental de la prensa dobladora, lo cual puede ser caro, especialmente si usted está usando punzones y dados templados maquinados con precisión.
Los sistemas en seco también requieren extractores de polvo, ya sea en seco o en húmedo. Los extractores en seco son adecuados para recolectar polvo de varios procesos. Éstos deben cambiarse regularmente y eliminarse adecuadamente. Sin embargo, implican graves riesgos si no se mantienen adecuadamente. Los filtros secos constan de tela, papel, material sintético y otros materiales. Varios metales, arenas abrasivas, fibras de cepillo y residuo de aceite pueden entrar a los filtros, y una chispa caliente podría causar un incendio. Verifique con su departamento de bomberos las leyes locales sobre recolección de polvo.
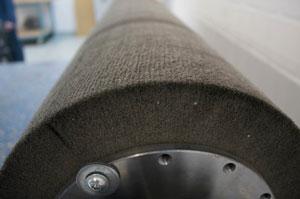
Figure 5: Los cepillos cilíndricos trabajan bien para las partes que requieren un acabado de grano en línea recta.
Éste es el porqué de que los extractores de polvo se hayan vuelto tan populares. Eliminan el costo de los cambios y la eliminación regular de filtros. Pero lo más importante, el medio de filtrado—usualmente sólo agua de la llave—satura las partículas y evita toda chispa caliente. El polvo es jalado hacia un baño de agua o un sistema de lavado, y las partículas se van al fondo de donde pueden removerse fácilmente. La mayoría de los filtros en húmedo son de acero inoxidable, por lo que la oxidación no es un problema.
La mayoría de las aplicaciones pesadas de rectificado se hacen en seco. Cuando se trabaja con aluminio y acero en la misma máquina, se debe usar un colector de polvo en húmedo para evitar incendios causados por ignición del polvo. Sin embargo, sin importar qué colector use, es imperativo que verifique y limpie diariamente la tubería para eliminar todo riesgo de incendio.
Medios de Cepillo
Alambre de acero, alambre de acero inoxidable, Scotch-Brite™, fibra de nylon, rueda de aletas—la lista sigue cuando se trata de medios de cepillo disponibles, y abundan variaciones de cada uno de estos cepillos. Sólo de la marca Scotch-Brite hay 40 tipos de cepillos.
Los Cepillos de alambre de acero, una opción económica, funcionan bien si sus aplicaciones involucran sólo acero laminado en frío. Evite usar esos cepillos en máquinas desbarbadoras en húmedo o si usted trabaja además acero inoxidable. De lo contrario, las partículas del laminado en frío impregnarán el acero inoxidable. Los cepillos de acero inoxidable, los más versátiles y durables disponibles, vienen en varios diámetros y densidades.
Los cepillos marca Scotch-Brite hacen un excelente trabajo de desbarbado en todos los materiales. Vienen en muchos tipos diferentes, desde los que brindan un acabado satinado hasta grano, o acabado No. 4. Finalmente, los cepillos de fibra de nylon y rueda de aletas funcionan bien para extrusiones y formas verticales, así como lugares de difícil acceso que requieren que el cepillo sea flexible.
Estilos de Cepillo
Los cepillos estilo taza o de disco así como los cepillos cilíndricos son los más comunes. Los cepillos de disco (vea la Figura 1) desbarban una gama de materiales ferrosos y no ferrosos, partes galvanizadas, recubiertas o formadas verticalmente. Los cepillos de disco con alambre de acero inoxidable además remueven la oxidación de los bordes cortados con láser. Los cepillos cilíndricos funcionan bien para partes que además requieren un acabado de grano en línea recta (vea la Figura 5). Con una máquina de cuatro cabezas ajustada con una secuencia de dos cintas y dos cepillos cilíndricos, una pieza de acero inoxidable con un acabado de fresa 2b puede ser desbarbado y recibir un acabado No. 4 en un solo paso.
Criterios Básicos de la Máquina
Por supuesto, un cepillo solo no desbarbará sus partes. La elección correcta de tambor de contacto, cinta abrasiva, velocidad del abrasivo, velocidad de la banda transportadora y selección del cepillo trabajan en conjunto para producir el acabado y calidad de orilla correctos.
Al elegir un sistema de desbarbado, asegúrese de evaluar algunos criterios básicos. Primero, considere la complejidad del diseño; una alta complejidad con frecuencia puede ser más cara de operar y mantener. ¿Qué tan difícil es reemplazar los cepillos cuando los medios de cepillo se desgastan? Mientras más fácil sea cambiar sus cepillos, menor será su tiempo improductivo.
Algunas máquinas permiten cambiar el estilo de cepillo en cada cabeza individual, lo cual puede beneficiar a las operaciones que demandan versatilidad. Por ejemplo, un taller que procesa partes cortadas con láser mediante cepillos de disco de alambre de acero inoxidable con una especificación de “sólo desbarbado” puede concluir el trabajo, luego cambiar rápidamente a un cepillo cilíndrico y procesar una orden completamente diferente, como una que involucre aluminio que sale de una punzonadora para ser desbarbado y granulado en una pasada.
Las máquinas con cabezas de cepillo de velocidad variable pueden aceptar la inmensa variedad de abrasivos disponibles actualmente. Un cepillo de alambre de disco funcionando a una eficiencia óptima tendrá una especificación de velocidad que difiere de muchos tipos de cepillos cilíndricos. La oscilación también puede ser importante cuando se usan cepillos tanto de disco como cilíndricos. Muchas aplicaciones de desbarbado requieren que los cepillos oscilen a la frecuencia correcta.
Velocidades y Alimentaciones
Con cualquier tipo de aplicación de maquinado o rectificado, las velocidades de alimentación y las velocidades de la herramienta de corte trabajan en conjunto para producir el acabado requerido. Esto también aplica para las máquinas desbarbadoras de cinta ancha. Una banda transportadora de velocidad variable puede ayudarle a lograr el acabado correcto de partes en una pasada. Una banda transportadora lenta se usa para remover rebabas y puede ajustarse para la severidad de la rebaba. Una banda transportadora rápida se usa para granulado, ya que toma el patrón de grano de superficie S impartido por la trayectoria de la cinta abrasiva y lo estira. Ésta y otras funciones de máquina hacen que ese patrón S sea difícil si no imposible de notar.
Muchas máquinas ofrecen un motor de una sola velocidad alta; otras vienen con un motor de velocidad variable. La velocidad alta es necesaria en una aplicación de granulado pues produce un rasguño menor y una mejor apariencia de la parte. La cinta abrasiva de alta velocidad también puede remover la escoria endurecida que se acumula en las partes de acero inoxidable cortadas con láser.
Una velocidad más lenta de la cinta abrasiva da un mayor control sobre la remoción de material, y permite que la cinta abrasiva se flexione alrededor de las orillas de la parte. El tener control sobre la velocidad puede ayudar enormemente cuando se desbarban metales galvanizados o preacabados que tienen recubrimientos protectores.
Efectos del Láser y del Plasma
Los láseres y las máquinas de plasma de alta definición han ocasionado nuevas configuraciones de máquina de desbarbado. La escoria del láser en acero inoxidable se endurece y algunas veces se vuelve a soldar sobre la superficie de la parte.
La remoción de esta escoria requiere rectificado de alta presión en el punto de contacto. Esto puede lograrse únicamente usando un tambor de contacto más duro, entre 55 y 85 Shore. Un tambor así de duro producirá una rebaba secundaria horizontal. Así que usar un tambor de 35 Shore como una segunda cabeza y luego un cepillo, o dos cepillos contrarotatorios puede producir los mejores resultados.
Por supuesto, el volumen puede influir en la configuración de la máquina. La decisión de incluir un tambor duro en la primera cabeza debe basarse en el porcentaje de partes que tienen una orilla de diente de sierra o material vuelto a soldar sobre la superficie de la parte.
Rectificado de Escoria
La escoria es el metal fundido que se deja endurecer en la orilla inferior de una parte que se ha cortado mediante una máquina de plasma. Las rectificadoras de escoria en años pasados eran mucho más populares que ahora, debido a las mejoras tecnológicas en el proceso de corte. De todos modos, hasta ahora algunos usan un cincel o rectificador manual para remover la escoria, lo cual por supuesto requiere mucha mano de obra y es muy ineficiente.
Las máquinas rectificadoras de escoria pueden remover grandes cantidades de escoria de piezas de trabajo grandes y pesadas, que con frecuencia pesan más de 1,000 libras (454 kg) con espesores de 0.5 a 6 pulgadas (1.27 cm a 15.24 cm). Para estas aplicaciones, la mayoría usa un tambor de contacto duro de hule sólido con una cinta abrasiva gruesa y motores de alta potencia. La mayoría de las aplicaciones requiere cintas abrasivas múltiples. Las máquinas de rectificado de escoria usualmente remueven sólo la escoria y no las escamas de laminación en la superficie del material.
El rectificado de escoria es una de las aplicaciones más extremas para una rectificadora de cinta ancha. Éste prueba los límites de la máquina y de los abrasivos. Varias máquinas remueven escoria de diferentes maneras, pero todos los sistemas requieren alta rigidez y potencia para llevar a cabo la tarea.
Selección del Abrasivo
Usted no usaría un desarmador de punta recta para un tornillo Phillips. Es probable que lo hiciera funcionar, pero seguro sería mucho más fácil usar la herramienta adecuada. Piense en los abrasivos de la misma forma.
Los abrasivos son como los zapatos: un tamaño no les queda a todos, y comprar por el precio puede ser un error, porque usar el abrasivo adecuado para su aplicación puede ahorrarle dinero a la larga. La mayoría de los constructores de máquinas pueden ayudarle en este proceso, pero siempre es aconsejable buscar ayuda de un fabricante de abrasivos.
¿Por qué Desbarbar?
En última instancia, el tipo de máquina y las opciones que elija dependerán del tipo de remoción de rebaba y del acabado que usted requiera. La decisión entre una máquina en húmedo o en seco, y las opciones necesitadas, deben hacerse después de que el constructor de la máquina haya hecho muestras. Una hoja de cálculo que incluya todas las funciones, especificaciones y costos es la forma más inteligente de comparar sistemas diferentes.
Pero hay una pregunta más amplia: ¿por qué desbarbar en primer lugar? La respuesta parece obvia. Después de todo, el proceso puede producir acabados de alta calidad, remover peligrosas rebabas filosas y producir una orilla lisa. La ausencia de rebabas u orillas filosas en las partes también conduce a un manejo más seguro del material y a una mayor seguridad del personal. La pintura se adhiere mejor, y, por supuesto, los productos se ven mejor.
Pero hay otro beneficio: un lastre menor. A diferencia de las máquinas de una sola cinta usadas hace décadas, las máquinas desbarbadoras modernas alisan tanto la superficie como las orillas. Históricamente, muchos talleres usaban una máquina de una sola cinta para arañar la superficie, remover la rebaba vertical y crear un acabado de grano o de cepillo. Sin embargo, esto creaba una rebaba horizontal u orilla filosa a 90 grados. Esto es lo que la mayoría de los talleres llamaban “desbarbado” hace 30 años. Actualmente es un lastre potencial.
Los sistemas modernos reducen considerablemente este lastre potencial al remover por completo rebabas de las superficies de la parte así como de las orillas interiores y exteriores. En esencia, ayudan a producir partes que son seguras, estéticas y listas para un procesado sin problemas corriente abajo.
About the Author
Tony McCue
114 Camars Drive
Warminster , PA 18974
215-293-0333
About the Publication
Compañías Relacionadas
subscribe now
FMA Communications ha introducido al mercado la edición en Español de la revista The Fabricator. Esta versión consiste del mismo tipo de artículos técnicos y sección de lanzamientos de nuevos productos que actualmente presentan el personal de primera categoría de Fabricator en Inglés.
start your free subscription- Podcasting
- Podcast:
- The Fabricator Podcast
- Published:
- 04/16/2024
- Running Time:
- 63:29
In this episode of The Fabricator Podcast, Caleb Chamberlain, co-founder and CEO of OSH Cut, discusses his company’s...
- Trending Articles
Los operadores de prensa dobladora inexpertos hacen indispensable el repensar la seguridad
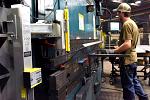
Prescripción para la reducción del desperdicio: arreglo esbelto de las instalaciones
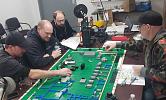
Máquina de corte por láser diseñada para el mercado mexicano
La máquina procesadora de placas crea biseles complejos en un solo corte
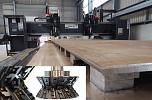
El software guía a los soldadores a través de instrucciones de trabajo
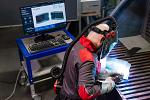
- Industry Events
16th Annual Safety Conference
- April 30 - May 1, 2024
- Elgin,
Pipe and Tube Conference
- May 21 - 22, 2024
- Omaha, NE
World-Class Roll Forming Workshop
- June 5 - 6, 2024
- Louisville, KY
Advanced Laser Application Workshop
- June 25 - 27, 2024
- Novi, MI