Contributing Writer
- FMA
- The Fabricator
- FABTECH
- Canadian Metalworking
Categories
- Additive Manufacturing
- Aluminum Welding
- Arc Welding
- Assembly and Joining
- Automation and Robotics
- Bending and Forming
- Consumables
- Cutting and Weld Prep
- Electric Vehicles
- En Español
- Finishing
- Hydroforming
- Laser Cutting
- Laser Welding
- Machining
- Manufacturing Software
- Materials Handling
- Metals/Materials
- Oxyfuel Cutting
- Plasma Cutting
- Power Tools
- Punching and Other Holemaking
- Roll Forming
- Safety
- Sawing
- Shearing
- Shop Management
- Testing and Measuring
- Tube and Pipe Fabrication
- Tube and Pipe Production
- Waterjet Cutting
Industry Directory
Webcasts
Podcasts
FAB 40
Advertise
Subscribe
Account Login
Search
Evaluating the Danger of Loud Noises in Tube and Pipe Shops
How OSHA's Rules Protect Your Employees
- By Linda Baldwin
- October 24, 2002
- Article
- Safety
![]() |
DoALL continuously tests and develops quieter band sawing blades. Here a technician uses an audiometer to measure noise levels created during sawing. |
Loud noise in the workplace traditionally has been associated with employee hearing loss. However, the Occupational Safety and Health Administration (OSHA) acknowledges that consistent exposure to 95 decibels (dB) or more may threaten the cardiovascular, digestive, and respiratory systems. Prolonged exposure to excessive noise may also reduce the eyes' ability to focus, which potentially could lead to more accidents and injuries.
In work environments where noise may be a potential risk, employers are responsible for protecting their employees' hearing and, when necessary, for implementing a hearing conservation program.
If employees complain about noises or hearing loss, employers should evaluate the environment. In addition, employers should be aware of work areas in which normal conversation is difficult. Under these circumstances, employers are required by OSHA to take action and determine if employees are at risk.
Noise in Tube and Pipe Shops
Two notable sources of substantial noise in tube and pipe fabricating and producing shops are cutting and material handling operations. The noise from cutting pipe can be controlled largely through the type of equipment used. Laser, rotary, and lathe cutting are relatively quieter methods. Sawing generally is the noisiest method, followed by shearing machines that make loud popping sounds as they cut some types of tubing.
In evaluating noise levels, employers should be most concerned with the manual handling of tube and pipe.
Alec Banish of Haven Manufacturing Corp., Brunswick, Ga., described the noise from material handling in a tube and pipe mill. "Consider a typical tube cutting process: Cut tubes fall to a table, nine or 10 tubes roll down an incline into a nesting area, and finally, perhaps 60 tubes are bundled together," he said. "The manual movement of tubing creates noise levels that generally exceed the 85-dB level and may exceed the 140-dB level, depending on the tube diameter."
Changing exit handling after the tubing is cut can help reduce this noise. "Nesting equipment guides cut tubes and lowers them gently onto a soft surface," continued Banish. "Urethane can eliminate some of the noise; for instance, bonded urethane placed on the back of the tube receptacle can decrease noise substantially."
The numerous variables involved in the cutting and handling of pipes make it impossible to approximate noise level in a producing or fabricating shop. The noise level varies according to factors such as the tube material, length, diameter, and wall thickness.
OSHA's Time-weighted-average Requirements
OSHA requires employers to evaluate environments where they suspect continuous noise levels exceed the permissible 85 dB or where impact noise or short explosions of sound exceed 140 dB.
As a guideline for determining what noise equates to in decibels, the National Institute for Occupational Safety and Health (NIOSH) developed estimates of work-related noises (seeFigure 1).
OSHA allows for a time-weighted average of 85 dB over eight hours before requiring a hearing conservation program. For instance, if a shop accepts a shipment of tubing and the initial noise from unloading the shipment lasts for a few minutes at 115 dB, the employees' exposure to noise would not be calculated at 115 dB; rather, the time-weighted average would take into account other lower decibel noises heard throughout the day.
However, this assumes that impulse noises do not exceed 140 dB. Continuous noises are defined as having an interval of less than one second between occurrences. If momentary explosions exceed 140 dB, a hearing conservation program should be implemented regardless of the time-weighted average.
In addition, if daily noise hazards are suspected to exceed the 85-dB time-weighted average, OSHA initially requires employers to protect their employees by reducing engineered noise where possible. Engineered noise results from machines and operations in the area. If employers cannot control the engineered noise levels within the environment to 85 dB or less, a hearing conservation program must be implemented.
![]() |
Figure 1: NIOSH developed these estimates of the dB levels of work-related noises. |
Protecting Employees
Per OSHA regulations (Standards -- 29 CFR, Occupational noise exposure. -- 1910.95), specific requirements of this program include monitoring noise exposure in the environment, audiometric testing and evaluation for employees, and hearing protection for employees and visitors. In addition, employers must train and educate employees to act in accordance with the employer's hearing conservation program. Employers also are required to keep records of noise exposure levels and audiometric tests on employees.
Audiometric Testing. As part of a hearing conservation program, OSHA requires employers to make free audiometric testing available to all employees whose exposure to noise equals or exceeds an eight-hour time-weighted average of 85 dB. The initial test result establishes an employee's baseline hearing level to which future audiograms, required at least annually, will be compared.
After future audiograms, employers must inform employees in writing if the change, or standard threshold shift, from the baseline is an average of 10 dB or more at 2,000, 3,000, and 4,000 hertz in either ear. In addition, employers must keep formal records of standard threshold shifts that are 25 dB or more.
Currently OSHA is re-evaluating the 25-dB level for recording standard threshold shifts and expects to have a final decision by January 2003. The recording level may change at that time.
Personal Protective Equipment. OSHA requires employers to provide their employees with personal protective equipment, at no cost to the employees. In addition, OSHA places responsibility on the employer that hearing protectors be worn and that employees be properly trained in using them.
For continuous noise levels of 85 dB or more, single-use earplugs or molded earplugs may be the best option for protection. In work areas with varying noise levels, band-type hearing protectors or ear canal caps are more convenient to use. They are attached to a band that can rest on the employee's neck when not needed.
Earmuffs also are an option; however, they require a perfect seal around the ear. Glasses, long hair, and facial movements may lessen their effectiveness.
More technically advanced hearing protectors also are available. Often used for in-flight noise reduction, active noise canceling headsets electronically cancel background noise while enhancing audio delivered through the headset. In addition, special microphones in communication headsets block unwanted noise and allow for better two-way communication.
OSHA does not specify what type of hearing protectors should be used in any given situation, but it does require employers to give employees a variety of suitable hearing protectors from which to choose.
Linda Baldwin is a free-lance writer based in Rockford, Ill., and can be reached by e-mail at lindakbaldwin@aol.com.
The FABRICATOR® acknowledges the contributions of Haven Mfg. Corp., 370 Sterling Industrial Park, Brunswick, GA 31525, phone 912-265-7536, fax 912-264-9001, Web site www.havencut.com.
Occupational Safety and Health Administration, 200 Constitution Ave. N.W., Washington, DC 20210, 800-321-6742, www.osha.gov.
National Institute for Occupational Safety and Health, Hubert H. Humphrey Bldg., 200 Independence Ave. S.W., Washington, DC 20201, 800-356-4674, www.cdc.gov/niosh/homepage.html.
Providing safety-related information such as that found in this article is one of the goals of the FMA/CNA Safety Committee. The committee comprises representatives of the Fabricators & Manufacturers Association, International (FMA); Norman-Spencer Inc.; and CNA. The Safety Committee provides information and assistance to improve workplace safety and the manufacturing environment. For information, call FMA's customer service department at 815-399-8775 or visit FMA's Web site at www.fmametalfab.org/fmaabout/safecomit.htm.
About the Author
Related Companies
subscribe now
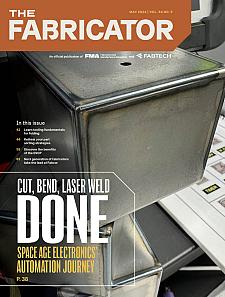
The Fabricator is North America's leading magazine for the metal forming and fabricating industry. The magazine delivers the news, technical articles, and case histories that enable fabricators to do their jobs more efficiently. The Fabricator has served the industry since 1970.
start your free subscription- Stay connected from anywhere
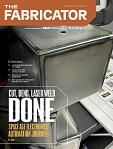
Easily access valuable industry resources now with full access to the digital edition of The Fabricator.
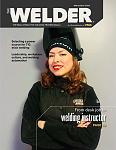
Easily access valuable industry resources now with full access to the digital edition of The Welder.
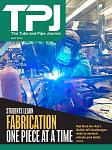
Easily access valuable industry resources now with full access to the digital edition of The Tube and Pipe Journal.
- Podcasting
- Podcast:
- The Fabricator Podcast
- Published:
- 04/16/2024
- Running Time:
- 63:29
In this episode of The Fabricator Podcast, Caleb Chamberlain, co-founder and CEO of OSH Cut, discusses his company’s...
- Trending Articles
Capturing, recording equipment inspection data for FMEA
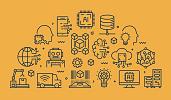
Tips for creating sheet metal tubes with perforations
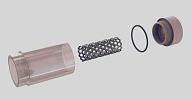
Are two heads better than one in fiber laser cutting?
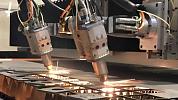
Supporting the metal fabricating industry through FMA
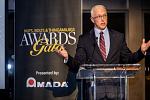
Omco Solar opens second Alabama manufacturing facility
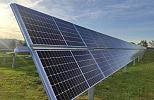
- Industry Events
16th Annual Safety Conference
- April 30 - May 1, 2024
- Elgin,
Pipe and Tube Conference
- May 21 - 22, 2024
- Omaha, NE
World-Class Roll Forming Workshop
- June 5 - 6, 2024
- Louisville, KY
Advanced Laser Application Workshop
- June 25 - 27, 2024
- Novi, MI