Director of Marketing - Global Cutting Technologies
- FMA
- The Fabricator
- FABTECH
- Canadian Metalworking
Categories
- Additive Manufacturing
- Aluminum Welding
- Arc Welding
- Assembly and Joining
- Automation and Robotics
- Bending and Forming
- Consumables
- Cutting and Weld Prep
- Electric Vehicles
- En Español
- Finishing
- Hydroforming
- Laser Cutting
- Laser Welding
- Machining
- Manufacturing Software
- Materials Handling
- Metals/Materials
- Oxyfuel Cutting
- Plasma Cutting
- Power Tools
- Punching and Other Holemaking
- Roll Forming
- Safety
- Sawing
- Shearing
- Shop Management
- Testing and Measuring
- Tube and Pipe Fabrication
- Tube and Pipe Production
- Waterjet Cutting
Industry Directory
Webcasts
Podcasts
FAB 40
Advertise
Subscribe
Account Login
Search
One laser head, one plasma torch, one cutting table
One laser head, one plasma torch, one cutting table
- By Douglas Shuda
- July 8, 2011
- Article
- Laser Cutting
Until recently shop owners who wanted to process a range of thicknesses and material types—from thin gauge to extremely heavy plate—had only one choice when it came to thermal cutting. They could buy a laser cutting system for thin stock and purchase a plasma arc cutting system to process heavy plate.
The situation, however, has changed dramatically. Solid-state lasers have entered the sheet metal cutting arena, and when it comes to how they are integrated with a cutting table, in some respects they resemble their plasma counterparts. Solid-state lasers, including fiber lasers, deliver the beam to the workpiece via an optical fiber; plasma arc cutting uses a lead-style delivery. Neither thermal cutting technology relies on mirrors or other optical alignment between the power source and the cutting head.
This makes integration easier in any automated setting. It also makes it easier to produce combination cutting systems. Today both plasma and fiber laser technologies can be installed on one cutting table, resulting in a primary cutting system that cuts fine features in thin sheet and cuts effectively on thick plate.
Precision Plasma
Cutting with plasma technology provides an optimal mix of cut quality, productivity, and low operating costs for mild steel, stainless steel, and aluminum across a range of thicknesses. Certain plasma arc cutting iterations, such as underwater PAC, may not complement the laser, of course; the laser cutting process and water don’t mix well.
But other plasma iterations do show significant potential for combination cutting, including certain precision plasma systems. One particular high-definition process uses a vortex design with a vented, two-piece nozzle designed to stabilize the arc precisely in the center of the electrode.
Various advances in plasma arc technology have improved edge quality for difficult geometries. For instance, one hole-cutting method makes real-time process adjustments to produce a smooth hole edge without the taper that’s especially common in thick plate sections. Specifically, the technology pierces at the center of the hole, applies a semicircle lead-in, then switches to the optimal speed as it cuts the hole circumference; upon closing the hole circle, it begins a current ramp-down to minimize the ding or divot at the point where the plasma finishes cutting the hole. Cutting gas is tightly controlled and adjusted to match the desired cutting action at specific cut locations.
Such holemaking technology doesn’t work for every material and hole geometry. It’s designed to cut holes in mild steel having 1-to-1 to 2-to-1 thickness-to-diameter ratios. If a shop needs to cut geometries beyond the capability of the plasma, a laser can fit the bill.
Precision Laser
Besides intricate geometries, the solid-state laser excels at cutting thin sheet extremely quickly, thanks to the process’s very high power density. Because of its short wavelength—many times shorter than a CO2 laser beam—the laser can slice through highly reflective materials such as copper and brass.
The fiber laser doesn’t come without its challenges, of course. The laser’s 1-micron wavelength means it can be transmitted through the cornea to the retina, making the safety threshold higher. Therefore, system setups should ensure operator safety via enclosures, laser safety eyewear, and other methods.
But as long as systems are designed with laser safety in mind, the solid-state laser’s benefits abound. It uses no resonator gas, requires no beam pathway purge, and offers more than 30 percent wall plug efficiency. In other words, more of the energy the laser consumes actually goes into making the cut.
When fabricators see a seemingly simple fiber making its way from the laser source to the cutting table, they may think about the low cost of ownership. When system integrators see that delivery fiber, they see other potential. The laser’s no-loss fiber delivery allows for great flexibility. There is no practical limit to a solid-state laser’s bed size. A larger cutting table requires merely a longer delivery fiber.
Importance of Control
There’s more to mechanized thermal cutting than just the power source and cutting head. The cutting process, be it with a laser or plasma, cannot produce smooth, high-quality, dross-free cuts if motion control is inadequate.
The motion control must have excellent acceleration and deceleration characteristics; fluidic, vibration-free contouring capabilities; along with accuracy and repeatability specifications exceeding those of conventional devices. Parameters such as speed; the distance between the workpiece and plasma cutting torch or laser cutting head; and gas pressures and purity all must be maintained according to specifications to optimize cutting.
A mechanized cutting system without high repeatability and quick acceleration and deceleration can diminish the benefits inherent in the cutting processes. Consider the fiber laser, which can cut complex shapes in thin-gauge material faster than most conventional thermal cutting methods. But what if a nest involves a series of small parts with intricate cutouts and small holes? In these cases, the speed the head moves between cuts is just as important as the speeds achieved during cuts.
The CNC is another vital factor. The complementary nature of the plasma and fiber laser delivery—that is, similar lead-style delivery, gas delivery methodology and management, table design, and implementation flexibility—means that effectively one table and in many cases one gantry can accommodate both thermal cutting processes. But the benefits of such integration cannot be fully realized without an advanced CNC.
Such CNCs can control parameters of the laser and plasma cutting by working from a database that contains all parameters for both processes, including height control. The advantages become apparent quickly. If the application requires thin sheet or fine-featured cutting that might not be suited for the plasma, the operator may select the laser process. In cases where higher productivity in thicker plate is needed—applications often not best-suited for the laser—the operator can use the plasma process. In short, the combination allows fabricators to use the right thermal cutting process for the application.
Cutting Thin to Thick
Any thermal cutting of sheet or plate relies on the delivery of energy. For plasma, system parts are configured to constrict and focus the vortex of ionized gas on an electrically conductive material so that the material can be cut with precision and accuracy. The ingredients used to create the plasma arc are the voltage (power) and the ionized gas. Once the gas is ionized, an electrical circuit will continue to operate as long as there is voltage, a vortex of ionized gas, and material to cut. The heart of PAC lies in electrical conductivity, which helps the plasma slice through relatively thick plate.
Lasers cut not with electricity but with light, meaning material reflectivity and absorption play a role. Because the light energy creates the cut, the beam’s shape helps determine how much material that laser can penetrate. During cutting, the beam’s depth of focus has an hourglass shape, crossing over at the laser focal point. It’s true that a fiber laser offers very high energy density, which allows it to cut extremely quickly on thin metal, much faster than any plasma arc process. But as plates get thicker, the plasma process begins to show its benefits.
Providing Diversity and Capacity
Combining the two on one machine may help a shop expand into new markets without having to invest in an entirely new machine dedicated to one process. Say a job shop specializes in thin sheet fabrication, but the owner does see demand picking up for thick plate cutting from local customers. If a shop purchases a stand-alone plasma system, the overflow demand may not be enough to fill the machine’s capacity. Even if the shop were able to fill the plasma table’s capacity, the purchase may not leave enough money to expand the shop’s core competency—that is, precision laser cutting.
In this case, a combination plasma/laser system could fit the bill, allowing the shop to both expand existing laser cutting capacity (especially considering the fiber laser’s productivity on thin sheet) while also diversifying into the thick plate cutting arena. This is just one possible scenario, of course. OEMs, top-tier suppliers, and other metal fabricators may benefit from a combination machine’s flexibility and space-saving features.
As always, machine choice depends on the application. Regardless, fabricators at all levels now have another cutting option to consider. Plasma systems can handle many material thicknesses, but on thin metal they can’t beat the fiber laser’s cutting speed. For the right application, a combination system may allow fabricators to take advantage of the best of both cutting processes.
About the Author
Douglas Shuda
411 S. Ebenezer Road
Florence, SC 29501
843-669-4411
Related Companies
subscribe now
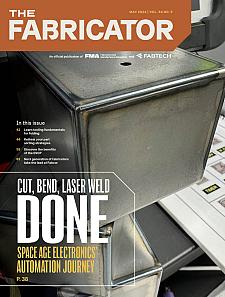
The Fabricator is North America's leading magazine for the metal forming and fabricating industry. The magazine delivers the news, technical articles, and case histories that enable fabricators to do their jobs more efficiently. The Fabricator has served the industry since 1970.
start your free subscription- Stay connected from anywhere
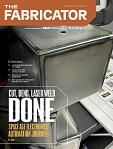
Easily access valuable industry resources now with full access to the digital edition of The Fabricator.
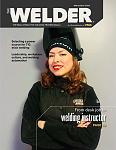
Easily access valuable industry resources now with full access to the digital edition of The Welder.
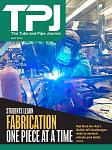
Easily access valuable industry resources now with full access to the digital edition of The Tube and Pipe Journal.
- Podcasting
- Podcast:
- The Fabricator Podcast
- Published:
- 04/16/2024
- Running Time:
- 63:29
In this episode of The Fabricator Podcast, Caleb Chamberlain, co-founder and CEO of OSH Cut, discusses his company’s...
- Trending Articles
Capturing, recording equipment inspection data for FMEA
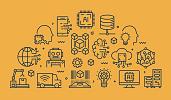
Tips for creating sheet metal tubes with perforations
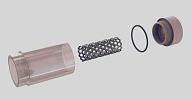
Are two heads better than one in fiber laser cutting?
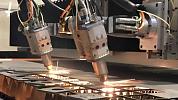
Supporting the metal fabricating industry through FMA
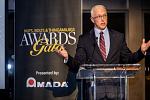
Omco Solar opens second Alabama manufacturing facility
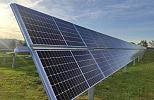
- Industry Events
16th Annual Safety Conference
- April 30 - May 1, 2024
- Elgin,
Pipe and Tube Conference
- May 21 - 22, 2024
- Omaha, NE
World-Class Roll Forming Workshop
- June 5 - 6, 2024
- Louisville, KY
Advanced Laser Application Workshop
- June 25 - 27, 2024
- Novi, MI