Editor-in-Chief
- FMA
- The Fabricator
- FABTECH
- Canadian Metalworking
Categories
- Additive Manufacturing
- Aluminum Welding
- Arc Welding
- Assembly and Joining
- Automation and Robotics
- Bending and Forming
- Consumables
- Cutting and Weld Prep
- Electric Vehicles
- En Español
- Finishing
- Hydroforming
- Laser Cutting
- Laser Welding
- Machining
- Manufacturing Software
- Materials Handling
- Metals/Materials
- Oxyfuel Cutting
- Plasma Cutting
- Power Tools
- Punching and Other Holemaking
- Roll Forming
- Safety
- Sawing
- Shearing
- Shop Management
- Testing and Measuring
- Tube and Pipe Fabrication
- Tube and Pipe Production
- Waterjet Cutting
Industry Directory
Webcasts
Podcasts
FAB 40
Advertise
Subscribe
Account Login
Search
Heating up with a new punch/laser combo
Commercial microwave manufacturer invests in new technology as it ramps up new product lines
- By Dan Davis
- September 1, 2016
- Article
- Laser Cutting

Figure 1
Commercial microwave ovens quickly cook food in such a way that diners don’t realize that a microwave was used to cook it.
The microwave has come a long way since self-taught engineer Percy Spencer was working with active radar while at Raytheon in 1945. He noticed that microwaves from the radar melted a candy bar in his pocket.
More than 70 years later, microwaves are doing much more than melting chocolate. Since Amana introduced the first countertop microwave oven in 1967, the quick-cooking appliance has emerged as a staple in residential and commercial kitchens worldwide.
The Amana name actually lives on as one of the brands owned by ACP Inc., Cedar Rapids, Iowa. The manufacturer’s Amana and Menumaster brands can be found in fast-food restaurants, gas stations, convenience stores, pizzerias, and high-end eateries all over the world.
In many instances, however, these appliances are not simply warming a cup of coffee or heating a wiener. They are fine-tuned devices (see Figure 1) that cook foods in precise ways so that eaters believe that a chef slaved over a meal for hours, not recognizing that a microwave did a lot of the final cooking.
ACP, which is part of the Ali Group, an Italian company with extensive holdings in the food service equipment industry, actually has an in-house culinary team of chefs and food scientists that work in a fully equipped commercial kitchen in the company’s 92,000-square-foot facility. The team provides customer support, such as assisting commercial kitchens in developing menu items that can be made in the quick-cooking appliances and in determining the right cooking times. The team also keeps tabs on the latest food trends and develops new recipes for the ACP microwave ovens.
In 2007, when it moved to its current location from nearby Amana, Iowa, ACP was manufacturing only a portion of its products. It relied on its own six hard-tooled punch presses and a network of job shops to fabricate the parts needed to make the company’s many microwave ovens. The need to invest in a used turret punch for additional in-house fabricating flexibility would soon manifest itself, according to Jason Schwenke, ACP’s director of manufacturing.
“A few years later, we began developing a new oven model that would require additional soft tooling,” Schwenke said. “As a result, we purchased a used Laser Brilliance, a used Night Train material management system, and a new robotic press brake” from the manufacturer now named Prima Power.
The success with that equipment led to a desire for more in-house fabricating flexibility in 2014, when the company introduced a new Menumaster steamer oven and the Jetwave combination oven, which replaced an older model. ACP manufacturing management (see Figure 2) liked the performance of its older 2,000-W CO2 punch/laser combination machine so it wanted a new version. In the end, they felt comfortable with their relationship with Prima Power and the warranty extension that it provided for the older combination machine. It purchased an LPe6f punch/laser combination machine and integrated it into the Night Train material handling system. At that time, according to Senior Manufacturing Engineer Ty Hill, Prima Power offered the only combination machine with a fiber laser.
The microwave manufacturer was about to heat up its own production efforts.
High-performance Production
The new punch/laser combination (see Figure 3) offers the flexibility that one might expect from such a machine. The servo-electric punching functionality allows the machine to handle a lot of the holemaking in the microwave parts, but also the limited amount of forming, embossing, and tapping that the company occasionally requires, Hill said. The 3,000-W fiber laser, which the company says consumes significantly less energy than a similarly powered CO2 laser power source, rips through the stainless steel sheet that is thrown onto the table. (ACP cuts primarily 0.020- to 0.060-inch-thick materials.)
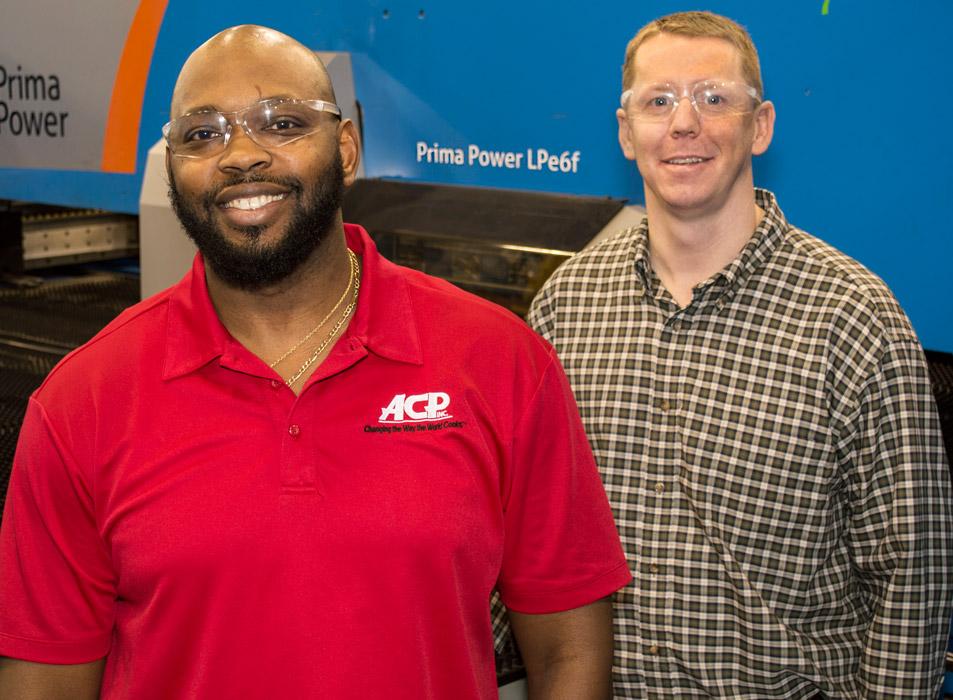
Figure 2
Ty Hill, a senior manufacturing engineer, and Jason Schwenke, ACP’s director of manufacturing, liked the idea of adding another punch/laser combination machine, this time with fiber laser cutting capability, to its manufacturing mix in 2014.
“The LPe6f greatly increased our productivity,” Hill said. “We were at full capacity with the older laser, and the new combination machine relieved that pressure. Around the time the LPe6f was installed, we had some huge orders coming through our facility. Our volume doubled and tripled during that time.”
The new machine is that much faster than the older technology. For example, the punch has automatic tool length measurement, stroke length optimization features, and easy adjustment of the punching stroke. The features help to contribute to faster setups and ease of operation.
Meanwhile, the fiber laser doesn’t require as much maintenance as a CO2 laser cutting machine. No laser gases are needed, so that doesn’t have to be monitored. The laser beam is manipulated through a fiber-optic cable, not through a series of precisely positioned mirrors like in a CO2 laser, so that is not a concern either.
To ensure maximized uptime during laser cutting, the combination machine has cutting head collision protection programming, which keeps the lens and nozzle in good shape, and sheet vibration damping, which helps to maintain quality cutting of thin material.
Because both punch/laser combination machines are connected to the automated material handling system, ACP can run the punching and laser cutting operations without constant supervision. A loading and stacking robot not only delivers full sheets to the machines, but also handles parts removal, stacking, and skeletons. Hill said the Night Train’s 52 shelves (see Figure 4) accommodate raw material (24 shelves), parts (24 shelves), and skeletons (four shelves).
In fact, the Night Train has become a key factor in helping to eliminate some extra racks on the shop floor. Hill said that they are actually manually loading some parts, which might come out of the combination machines via conveyor, into the giant racking setup to keep the parts in one central location.
What sort of impact has the new equipment made? Hill described a former tapping job that used to take six hours to complete. One sheet had 560 parts, and each part required two taps in the 11-gauge material. ACP ran this part during off-hours, between the second shift of the day and the morning shift, so it was OK that the job was eating up machine time. (The tapping unit, which is attached to the side of the laser cutting head/turret punch, can run without human intervention, but it is a time-consuming process, taking up almost half of the six-hour run-time.) Because of the newfound production efficiencies, the new punch/laser combination can turn around the job in four hours.
In another laser cutting-intensive job, the fiber laser cut almost 45 minutes out of the 105-minute run-time.
“We try to make sure those types of parts are put on the fiber,” Hill said.
Cooking up Plans for the Future
The additional capacity helped ACP ramp up production of those two product lines quickly without hurting the company’s ability to produce its other domestic product lines. It also has allowed ACP to bring prototyping tasks in-house; the parts can be cut and formed quickly without throwing off production schedules.
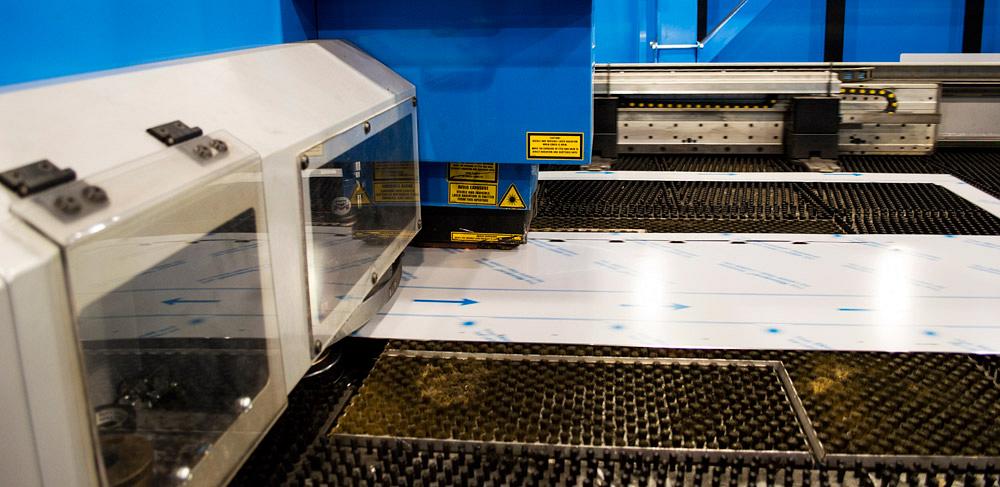
Figure 3
Because multiple operations can be performed on a punch/laser combination machine, a fabricator can theoretically reduce costs per part because parts are made fast and accurately on one device, eliminating the need to move a part from one machine to another.
Manufacturing management now is turning its attention to possibly bringing home higher-volume product lines that are made in Asia. This would require an investment in hard tooling and more stamping capacity, but Hill said the company is ready to make the necessary commitments. Moving manufacturing back to the U.S. is a priority for the company as it looks to hasten the pace of new product development for its line of food service equipment.
The investment in the new punch/laser combination machine may be the first step of a very exciting future for the manufacture of combination ovens in the U.S.
ACP Inc., 319-368-8120, www.acpsolutions.com
Prima Power North America Inc., 847-952-6500, www.primapower.com
About the Author
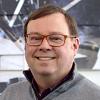
Dan Davis
2135 Point Blvd.
Elgin, IL 60123
815-227-8281
Dan Davis is editor-in-chief of The Fabricator, the industry's most widely circulated metal fabricating magazine, and its sister publications, The Tube & Pipe Journal and The Welder. He has been with the publications since April 2002.
subscribe now
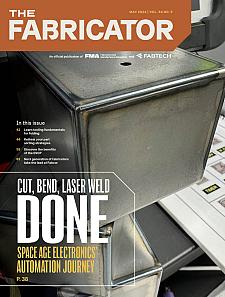
The Fabricator is North America's leading magazine for the metal forming and fabricating industry. The magazine delivers the news, technical articles, and case histories that enable fabricators to do their jobs more efficiently. The Fabricator has served the industry since 1970.
start your free subscription- Stay connected from anywhere
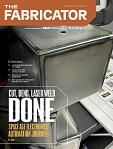
Easily access valuable industry resources now with full access to the digital edition of The Fabricator.
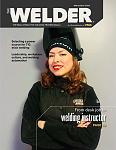
Easily access valuable industry resources now with full access to the digital edition of The Welder.
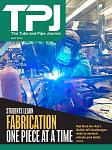
Easily access valuable industry resources now with full access to the digital edition of The Tube and Pipe Journal.
- Podcasting
- Podcast:
- The Fabricator Podcast
- Published:
- 04/16/2024
- Running Time:
- 63:29
In this episode of The Fabricator Podcast, Caleb Chamberlain, co-founder and CEO of OSH Cut, discusses his company’s...
- Industry Events
16th Annual Safety Conference
- April 30 - May 1, 2024
- Elgin,
Pipe and Tube Conference
- May 21 - 22, 2024
- Omaha, NE
World-Class Roll Forming Workshop
- June 5 - 6, 2024
- Louisville, KY
Advanced Laser Application Workshop
- June 25 - 27, 2024
- Novi, MI