Editor-in-Chief
- FMA
- The Fabricator
- FABTECH
- Canadian Metalworking
Categories
- Additive Manufacturing
- Aluminum Welding
- Arc Welding
- Assembly and Joining
- Automation and Robotics
- Bending and Forming
- Consumables
- Cutting and Weld Prep
- Electric Vehicles
- En Español
- Finishing
- Hydroforming
- Laser Cutting
- Laser Welding
- Machining
- Manufacturing Software
- Materials Handling
- Metals/Materials
- Oxyfuel Cutting
- Plasma Cutting
- Power Tools
- Punching and Other Holemaking
- Roll Forming
- Safety
- Sawing
- Shearing
- Shop Management
- Testing and Measuring
- Tube and Pipe Fabrication
- Tube and Pipe Production
- Waterjet Cutting
Industry Directory
Webcasts
Podcasts
FAB 40
Advertise
Subscribe
Account Login
Search
Laser cutting in a new light
The evolution of LED lighting led TAMCO to ditch its hard-tooling ways
- By Dan Davis
- April 13, 2016
- Article
- Laser Cutting
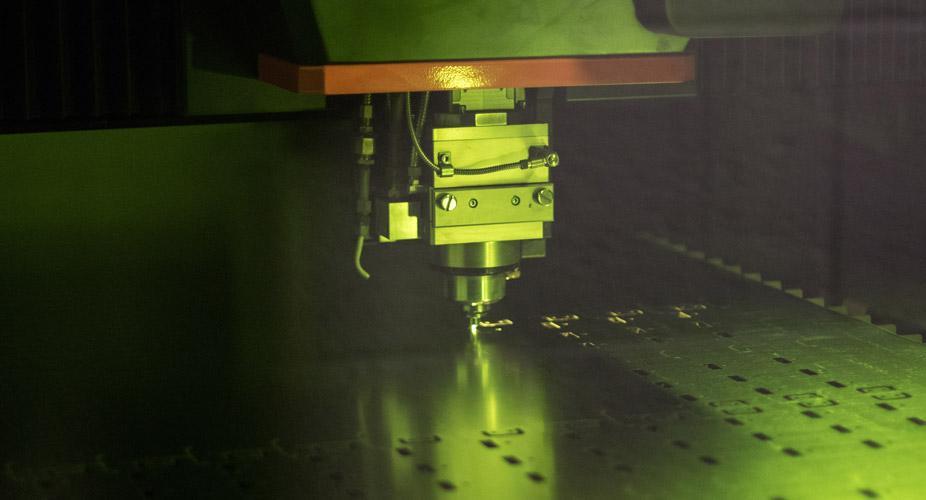
Figure 1
TAMCO Group’s new fiber laser cutting machine delivers a much more focused beam than CO2 laser technology, which means that even at 2 kW, the beam has a greater power density at the focal point than a 4-kW beam on a CO2 laser. Photos courtesy of TAMCO Group.
When change hits an industry that hasn’t undergone dramatic change for almost 100 years, the technology leap can be fast and tumultuous.
TAMCO Group’s manufacturing arm in Port St. Lucie, Fla., knows that all too well. It’s been trying to stay on top of the LED lighting revolution for the past several years.
Most adults only know light bulbs by the traditional incandescent filament design that they grew up with. However, with the advent of the first LED with white light from luminescence conversion in the late 1990s, the lighting market was going to change dramatically. In the 2000s, as the LED technology matured, product design had to take into account a whole new lighting technology, and companies had to keep pace with the continuous improvement in lighting performance. As a result, this put a whole new stress on manufacturers that were now dealing with product designs that have life spans of months instead of years.
To keep up with production needs, TAMCO realized it needed to leave behind its hard-tooling ways. It needed the latest cutting-edge technology for itself, and it found it in a fiber laser (see Figure 1).
Learning About Lighting
TAMCO comprises six brands: Tamlight Lighting, which manufactures residential, commercial, and industrial lighting products; Centaur Electrical Installation, which supplies electrical installation products, such as steel boxes; Motor Control Gear, which makes components for motor control assemblies; RPP Devices, which makes receptacles, switches, and wall plates; Fusion Lamps, a maker of lamps shifting to LED technology; and First For Performance, which supplies items necessary for electrical equipment installation, such as wire nuts, PVC tape, and caulk. Tamlight, Centaur, and Motion Control Gear account for most of TAMCO’s manufacturing activity. The fabricating operation processes primarily 24- and 26-gauge galvanized steel for most parts (see Figure 2). It occasionally works with thicker gauges and with some aluminum, but it primarily works with a limited range of materials.
It’s not like a job shop, even if TAMCO has to fabricate a variety of products. Tom Wouters, TAMCO’s engineering manager, likes the fact that the various products are somewhat related.
“I came from a job shop, and it’s nothing like it,” he said. “In my job shop, we had more variety. Here, everything is related somehow to the electrical store. In the job shop, I was involved in medical, gun ranges, plumbing, and air conditioning. That was just all over the place. I felt scatterbrained in that industry because you could never really focus on one thing.”
That one thing is lighting. However, the market was no longer stable. For example, the fluorescent tube was unchanging. Its shape stayed the same for decades. It made sense for a manufacturer to hard-tool to fabricate those products. That’s why punching machines are a common sight in lighting factories across the U.S.
LED lighting, however, has been marked by rapid technological changes over the past 20 years. According to Wouters, it’s only been in the past 10 years with the emergence of programmable drivers that LED lighting has become more reliable. The increased reliability, along with LED lighting’s low power consumption and long life span, up to 100,000 hours in some cases, helped to propel the adoption rates in the residential and commercial sectors. That has complicated matters from a manufacturing standpoint.
“Now there’s this variation where you’re changing over to LED, and not everybody has the same mounting patterns for your LED boards. There’s no standard to it, so it makes you have to be very flexible in your underlying sheet metal component to be able to go from supplier to supplier and be able to switch out power supplies or printed circuit boards,” Wouters said.
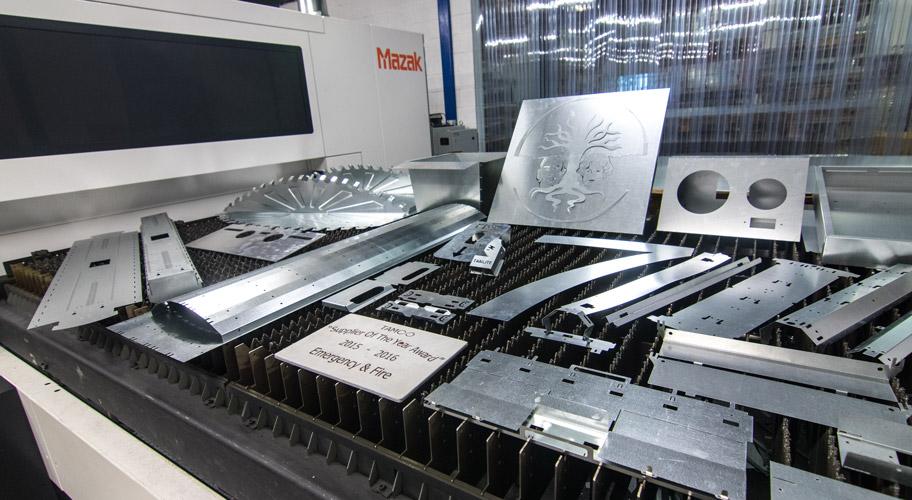
Figure 2
Some of these TAMCO parts are laser-cut on a regular basis, and others represent the laser cutting capabilities that the new fiber laser delivers.
TAMCO also had to redesign its products to accommodate LED lighting. LED lights shine from one side only. Light from fluorescent tubes emanates from all sides.
“So the way that you capture the light from a fluorescent tube is different than how you manipulate the light off an LED. This forces design changes and a whole lot of sheet metal inside of the fixtures, which are way different,” Wouters said. “To the end users, the outsides of the fixtures look identical. You would have no idea the change in the technology.
“And there’s a lot of design work to make that happen,” he added.
That’s why TAMCO needed laser cutting capability. It needed the flexibility to produce parts on a rapid and just-in-time basis, and it didn’t necessarily have the time to be investing in tooling to produce a design that was likely going to change in a few months.
As the search for a new laser cutting machine commenced in the latter half of 2014, Wouters said he knew he wanted to stay away from CO2 technology, which he struggled with at his prior place of employment.
“The fully optimized system was great, except when it went down. The mirror may have had a hole burned in it, or the mirror was out of alignment. It was like that half of the time,” Wouters said. “And every time we were in trouble was when it would break down.”
Initially the search focused on a used laser cutting machine, but as the company did more investigating, the focus on fiber laser cutting technology became stronger. A fiber laser is created in optical fibers that are doped with rare-earth elements. The laser light is delivered to the cutting head using another kind of optical fiber. No mirrors or laser gases are needed to create or deliver the laser to the cutting head, which removes elements that typically require maintenance on CO2 lasers.
Understanding what the fiber laser cutting technology could mean for the shop floor—faster cutting speeds and more uptime when compared to the older CO2 laser cutting method—Wouters realized it was really about new versus older technology. It sounded a lot like conversations about LEDs of days gone by. If he had the choice to purchase LED lighting from five years ago or spend more money and buy today’s lighting, he would always choose the latest technology.
“After we looked into it, it turned out that this was the only way to go,” Wouters said. “Fiber optic was it.”
In January 2015 TAMCO purchased a Mazak Optiplex 3015 2-kW fiber laser.
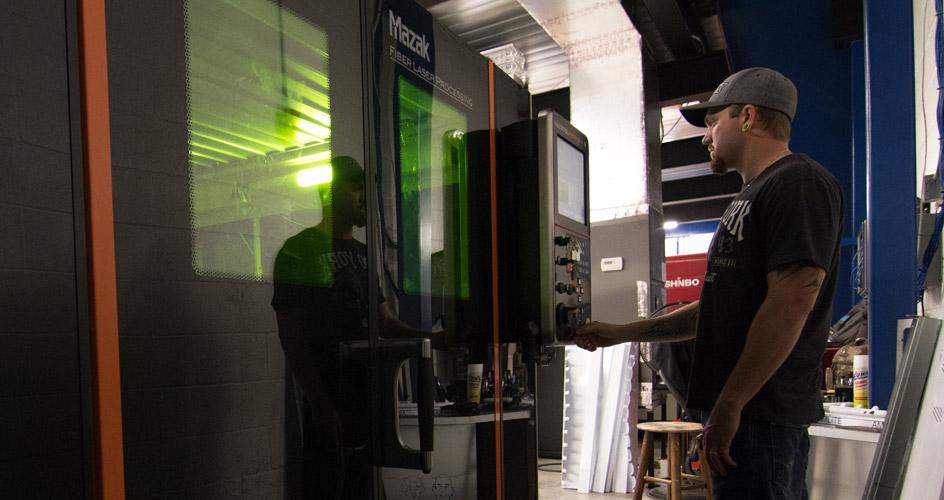
Figure 3
How does a manufacturer’s engineering department end up in charge of a laser cutting machine? When engineers are responsible for producing prototypes for product designs that might have a life span of only six months, they need access to fabricating tools. Also, because the engineering department provides a central function and serves other TAMCO Group companies, it can be responsive to all parties.
Living With a Fiber Laser
Wouters and two others were responsible for getting the laser running. All had experience with CNC machine programming, so the learning curve was fairly quick.
“It’s more simple than it was 10 years ago,” Wouters said.
The engineering department oversees the use of the fiber laser cutting machine (see Figure 3). Wouters said it made sense to set it up that way because the engineering department regularly uses it for prototyping and the equipment serves the company’s many businesses.
Five individuals in the engineering department are responsible for programming and running the laser cutting machine. They use the Mazak software, and Wouters said they have had to tweak only a few parameters to get the desired cutting results.
TAMCO decided to place the laser cutting machine in its own room (see Figure 4). The idea was to make it a sort of clean-room environment where the machine would be spared the dents and dings that other equipment gets on a fabricating shop floor.
The TAMCO staff also chose not to invest in an automatic material loader and unloader device.
Wouters said that if the company ever chooses to invest in an automated material handler, it has the internal expertise and components from a sister division, such as its Motor Control Gear group, to make it an in-house job.
“Learning to work with shop air was really the only challenge,” Wouters said.
Machine tool builders typically suggest that nitrogen be used as the laser cutting assist gas because it expels molten material from the kerf as the cutting head whizzes down the sheet, without leaving an oxidized edge. Shop air also works (see Figure 5) because it has a heavy concentration of nitrogen as part of its overall makeup.
Wouters said that they achieve a suitable edge on most of the thin-gauge material they laser-cut. The edges don’t need to be deburred, and even with using shop air, the parts can be powder-coated without much worry. With thicker parts, laser cutting with shop air leaves an edge similar to what a plasma cutter would deliver, which is OK in most instances.
The programmers also have found additional benefits as they have become more familiar with the equipment. Wouters said the shop runs “tons of common-line cutting,” in which parts share the same cut line. Programmers also like to include serrations in the laser-cut part so folding can be done by hand, bypassing the press brake in many instances.
Keeping up With the Cutting
The fiber laser has been turning out parts at a rapid pace, which has added pressure in the bending department. The company’s three press brakes could barely keep up with the turret punch presses, and now they are struggling mightily with the fiber laser cutting machine.
But the decision to incorporate laser cutting into TAMCO’s manufacturing portfolio was a wise move. The job shop that the lighting manufacturer used to rely on for contract laser cutting services is now out of business.
“You get your samples now in five minutes instead of two to three weeks,” he said.
The fiber laser also has proven to be a sales tool.
“When you go to show a customer that you are high-tech, the first thing they want to see is your laser. They want to see sparks flying,” Wouters said.
TAMCO welcomes one to two tours per week of its manufacturing operations. The extra windows (see Figure 6) it had added to the laser cutting machine’s cabinet ensures that everyone gets a chance to see the latest fabricating technology in action.
TAMCO Group, www.tamcogroup.com
Mazak Optonics, 847-252-4500, www.mazakoptonics.com
About the Author
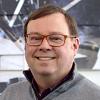
Dan Davis
2135 Point Blvd.
Elgin, IL 60123
815-227-8281
Dan Davis is editor-in-chief of The Fabricator, the industry's most widely circulated metal fabricating magazine, and its sister publications, The Tube & Pipe Journal and The Welder. He has been with the publications since April 2002.
subscribe now
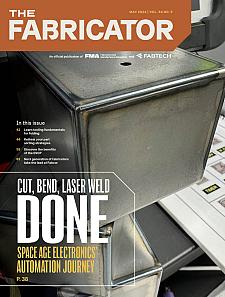
The Fabricator is North America's leading magazine for the metal forming and fabricating industry. The magazine delivers the news, technical articles, and case histories that enable fabricators to do their jobs more efficiently. The Fabricator has served the industry since 1970.
start your free subscription- Stay connected from anywhere
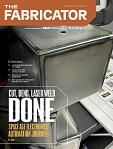
Easily access valuable industry resources now with full access to the digital edition of The Fabricator.
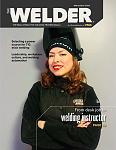
Easily access valuable industry resources now with full access to the digital edition of The Welder.
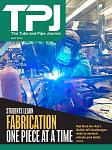
Easily access valuable industry resources now with full access to the digital edition of The Tube and Pipe Journal.
- Podcasting
- Podcast:
- The Fabricator Podcast
- Published:
- 04/16/2024
- Running Time:
- 63:29
In this episode of The Fabricator Podcast, Caleb Chamberlain, co-founder and CEO of OSH Cut, discusses his company’s...
- Trending Articles
Capturing, recording equipment inspection data for FMEA
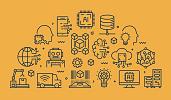
Tips for creating sheet metal tubes with perforations
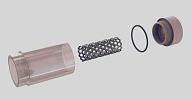
Are two heads better than one in fiber laser cutting?
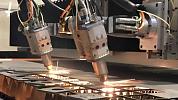
Supporting the metal fabricating industry through FMA
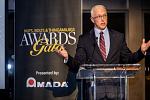
Omco Solar opens second Alabama manufacturing facility
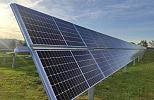
- Industry Events
16th Annual Safety Conference
- April 30 - May 1, 2024
- Elgin,
Pipe and Tube Conference
- May 21 - 22, 2024
- Omaha, NE
World-Class Roll Forming Workshop
- June 5 - 6, 2024
- Louisville, KY
Advanced Laser Application Workshop
- June 25 - 27, 2024
- Novi, MI