Senior Editor
- FMA
- The Fabricator
- FABTECH
- Canadian Metalworking
Categories
- Additive Manufacturing
- Aluminum Welding
- Arc Welding
- Assembly and Joining
- Automation and Robotics
- Bending and Forming
- Consumables
- Cutting and Weld Prep
- Electric Vehicles
- En Español
- Finishing
- Hydroforming
- Laser Cutting
- Laser Welding
- Machining
- Manufacturing Software
- Materials Handling
- Metals/Materials
- Oxyfuel Cutting
- Plasma Cutting
- Power Tools
- Punching and Other Holemaking
- Roll Forming
- Safety
- Sawing
- Shearing
- Shop Management
- Testing and Measuring
- Tube and Pipe Fabrication
- Tube and Pipe Production
- Waterjet Cutting
Industry Directory
Webcasts
Podcasts
FAB 40
Advertise
Subscribe
Account Login
Search
Automated guided vehicles get flexible
AGV technology evolves and adapts to highly variable environments
- By Tim Heston
- July 8, 2016
- Article
- Materials Handling
If it were only as easy as getting from point A to B. For many custom fabricators, material often needs to go from B back to A, then perhaps on to C again before going back to B before skipping ahead to D. And this path may change entirely for the next job.
Automating the material handling between jobs for such high-product-mix operations usually hasn’t been practical. The variation is just too great. But some operations have at least scrutinized the process. Often a laser or press brake isn’t running when it should be because the material needed hasn’t been delivered—and finding out why has led some to improvement opportunities.
Companies like General Sheet Metal Works in South Bend, Ind., and Bermo Inc., Circle Pines, Minn., have organized fork truck and tugger traffic into routes. Operators park carts of work-in-process at a “bus stop” in a department, tag the work-in-process for a specific route, and the fork truck driver on that route comes by shortly to pick it up. Like in any custom fab shop, demand and volumes change continually, so a route may have more fork trucks on it to handle the parts-delivery “rush hours.” To make this happen, a fork truck may need to alter its route in the middle of the shift to handle the changes in demand.
This kind of consistency may open the door to some level of material handling automation, including automated guided vehicles (AGVs).
Historically, AGVs have been programmed to go a specific route using wires, magnetic tape, or a vision system based on laser technology. But camera-based AGVs have also hit the market. According to Jeff Christensen, vice president, products, for Pittsburgh, Pa.-based Seegrid, such camera-based technology helps make AGVs more flexible. It doesn’t take long to teach an AGV a new route, and the vehicle itself need not ride along a marked track.
“We can make these vehicles drive by themselves entirely with cameras,” he said. “[The AGV] takes pictures of the space around it, remembers it, and then drives in that space by itself.”
The camera used in these AGVs is about as sophisticated as the rear-view camera in a vehicle, Christensen said, explaining that it’s the software interpreting those pictures that makes the system work.
Seegrid’s AGV system has five “stereo” pairs of cameras that capture a 3-D image of the space around it. The cameras create a “point cloud” or grid around the truck. The system then saves that data to define the space along the AGV’s driving path. In effect, the vehicle “sees” the “grid”—hence the company name, Seegrid.
To program the system, employees guide the AGV along its defined path, its stops, starts, pickups, dropoffs, and other required actions. If the truck needs to honk its horn at a certain intersection, it can be programmed to do so. During training, the AGV “sees” the surrounding area and builds a 3-D map to define the route. This route then can be downloaded to other AGVs in the factory. If the path needs to be changed, an employee guides the AGV once down the new path, after which it remembers the new route, sending the program to other AGVs as needed.
Seegrid does not retrofit existing trucks. “The control system for every truck is different, and the engineering cost-benefit just doesn’t work out,” Christensen said. “But we don’t make trucks either. We build onto existing [new] chassis.”
The AGV can’t replace a fork truck driver who retrieves material from high on a rack; the number of variables is just too great. But after bringing stock down from a rack, the fork truck driver can place it on the AGV, which can then shuttle the stock automatically to the next operation.
According to Seegrid, company founder Hans Moravec invented the core technology behind its camera-based AGV, called “evidence grid,” during the late 1990s at The Robotics Institute of Carnegie Mellon University.
“He had been working on this technology for more than 30 years,” Christensen said, “trying to have cameras [and associated software] do this type of navigation.” Moravec initially developed it for general navigation before launching his company in 2003 to adapt it to the AGV market.
Although the AGV navigates with cameras, it still uses lasers. A light curtain surrounds the truck during operation, and a primary sensor on the truck chassis detects nearby obstructions. If anything gets too close, the vehicle stops.
“These vehicles had more than 200,000 miles of autonomous travel in real-world applications and never had a personnel injury,” Christensen said.
One application (shown in the photos) includes a Whirlpool plant in Clyde, Ohio. It’s an old plant, and according to Seegrid, Whirlpool couldn’t reconfigure its plant to develop a material handling strategy. So in this case, the company adapted camera-based AGVs to transport parts to the assembly lines.
“Their automated trucks do just what their manual drivers were doing,” Christensen explained. “Only the AGVs never take breaks, they never hit anything, and they never go over the speed limit.”
Photos courtesy of Seegrid, 412-379-4500, www.seegrid.com.
About the Author
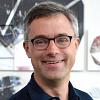
Tim Heston
2135 Point Blvd
Elgin, IL 60123
815-381-1314
Tim Heston, The Fabricator's senior editor, has covered the metal fabrication industry since 1998, starting his career at the American Welding Society's Welding Journal. Since then he has covered the full range of metal fabrication processes, from stamping, bending, and cutting to grinding and polishing. He joined The Fabricator's staff in October 2007.
subscribe now
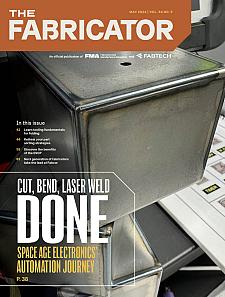
The Fabricator is North America's leading magazine for the metal forming and fabricating industry. The magazine delivers the news, technical articles, and case histories that enable fabricators to do their jobs more efficiently. The Fabricator has served the industry since 1970.
start your free subscription- Stay connected from anywhere
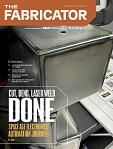
Easily access valuable industry resources now with full access to the digital edition of The Fabricator.
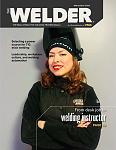
Easily access valuable industry resources now with full access to the digital edition of The Welder.
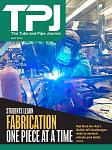
Easily access valuable industry resources now with full access to the digital edition of The Tube and Pipe Journal.
- Podcasting
- Podcast:
- The Fabricator Podcast
- Published:
- 04/16/2024
- Running Time:
- 63:29
In this episode of The Fabricator Podcast, Caleb Chamberlain, co-founder and CEO of OSH Cut, discusses his company’s...
- Industry Events
16th Annual Safety Conference
- April 30 - May 1, 2024
- Elgin,
Pipe and Tube Conference
- May 21 - 22, 2024
- Omaha, NE
World-Class Roll Forming Workshop
- June 5 - 6, 2024
- Louisville, KY
Advanced Laser Application Workshop
- June 25 - 27, 2024
- Novi, MI