- FMA
- The Fabricator
- FABTECH
- Canadian Metalworking
Categories
- Additive Manufacturing
- Aluminum Welding
- Arc Welding
- Assembly and Joining
- Automation and Robotics
- Bending and Forming
- Consumables
- Cutting and Weld Prep
- Electric Vehicles
- En Español
- Finishing
- Hydroforming
- Laser Cutting
- Laser Welding
- Machining
- Manufacturing Software
- Materials Handling
- Metals/Materials
- Oxyfuel Cutting
- Plasma Cutting
- Power Tools
- Punching and Other Holemaking
- Roll Forming
- Safety
- Sawing
- Shearing
- Shop Management
- Testing and Measuring
- Tube and Pipe Fabrication
- Tube and Pipe Production
- Waterjet Cutting
Industry Directory
Webcasts
Podcasts
FAB 40
Advertise
Subscribe
Account Login
Search
Handling structural steel, one truckload at a time
Material handling truck provides faster, safer way to move big steel
- By Eric Lundin
- March 5, 2015
- Article
- Materials Handling
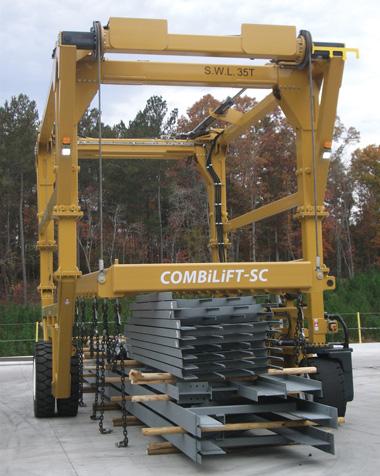
Combilift’s Straddle Carrier is nearly ready to move a load of steel to a waiting trailer. After sliding a series of lifting bars beneath the load, the machine operator attaches the chains to the lifting bars, then lifts and transports the load.
For industrial contractors that turn big steel into even bigger construction projects, the phrase “business as usual” has no meaning. Reinicke Athens Inc. (RAI), Athens, Ga., is one such company. Its customers, which include FORTUNE® 500 companies such as Anheuser-Busch InBev, Caterpillar Inc., General Mills, Georgia Pacific, Kellogg Co., Lockheed Martin, and Siemens, rely on RAI for all manner of work, including plant additions, relocations, and turnkey construction projects. RAI has its own fabrication shop, which brings in wide-flange sections such as I-beam, H-beam, and C-channel, cuts them to length, and welds them to make prefabricated components such as trusses, beams, columns, joists, struts, and gussets that are job site-ready.
At the job site, RAI’s ironworkers put up steel almost as fast as it arrives. The key phrase is “almost as fast as it arrives.” While RAI’s fast-track capability is a point of pride, it often is a matter of necessity. Some job sites simply have little free space, so in such cases the company delivers just one truckload of material at a time.
Needless to say, the job site hums along at peak efficiency only when the yard runs at peak efficiency, meaning the company’s trailers have to be loaded and dispatched as quickly as possible, so the yard must run like clockwork. A load of material that arrives early has to wait until some space is cleared for the incoming material; a load that arrives late means that its team of ironworkers has to wait until the material arrives. Some projects require 60 loads, which means 60 opportunities to get it just right or to leave someone, or an entire team of someones, idle.
The company’s conventional process was to cut, weld, and paint structural components job by job, but the order wasn’t critical. When parts were finished, they were moved outdoors to the inventory section of the yard. From there they were moved to organized stacks in the staging area, and when the time came, the parts were moved, one at a time, onto the waiting trailer. While no load is typical, it wasn’t uncommon for a load to require 8 man-hours to go from staging area to trailer, and some took even longer. One worker lifted and placed each piece with a forklift while the other stood on the trailer and worked as a spotter. It wasn’t easy, it wasn’t fast, and it wasn’t without risks.
RAI President Mark Christopherson figured there had to be a better way to load the trailers. And then one day he found it.
One Trailer Load at a Time
Lift truck manufacturer Combilift Ltd. embraced the growing trend in containerized cargo when it developed the Straddle Carrier. As the name implies, the distance between its tires is wide enough that it straddles a semitrailer, grips the shipping container, lifts it, and carries it to an unloading area. This frees the semi driver to go about his business and takes the pressure off the receiving personnel—they don’t have to unload the container immediately.
RAI and others have found that the truck’s size and lifting capacity make it a good fit for many other loading and unloading tasks and innumerable other material handling applications.
Although the Straddle Carrier is a departure from Combilift’s other products, highly maneuverable, narrow-aisle lift trucks with capacities up to 30,000 lbs., it has some similarities: It requires one operator to lift and transport large, heavy loads; it uses the same 4-cylinder diesel engine as the company’s largest-capacity lift trucks; and it uses the hydrostatic drive system common to the company’s other models.
However, the big difference in the payload it carries has caused RAI’s staff to rethink the way it does business.
“Now we make plans based on what’s needed at the job site next,” Christopherson said. “This drives the logistics all the way through the entire plant. We generate a cut list based on what the job site needs next, and after the parts are welded and painted, they go directly to staging, which eliminates one handling.”
The process is structured, but it’s not without some latitude. The yard’s 10 staging locations provide some manufacturing flexibility. As long as the manufacturing sequence puts priority on the next load needed at the job site, it can make parts for the other nine loads bit by bit. Meanwhile, old-fashioned common sense dictates which parts are produced first.
“We start with the biggest parts, so they form the base, and we finish up the stack with the smallest parts,” Christopherson said. The operator then drives the carrier over the load and slips six or seven lifting bars under the load, between the pieces of dunnage. After securing the bars to the lifting chains, the operator lifts the load and drives it to the waiting trailer. If the load isn’t quite centered when he gets there, no matter—he can make a lateral adjustment up to 6 in. or so if necessary. Likewise, if the trailer is pitched along its length, the operator can adjust the load up to 30 degrees. After setting the load onto the trailer’s dunnage, the operator disconnects the chains, removes the lifting bars, and drives the carrier back to the yard.
“The drivers love it,” Christopherson said. “They used to have to wait quite a while, up to three or four hours, while we loaded the trailer.” These are nonproductive hours, time the driver isn’t earning a dime. “Now we can have them in and out in a half hour. In some cases, it’s as little as 15 minutes,” he said.
Stand Back
Christopherson liked the Straddle Carrier as soon as he saw it, but later he came up with an idea to modify it. His idea would give the driver a better view of the loading process and eliminate the need for a spotter. Christopherson outlined his concept for Combilift’s executive team and the manufacturer agreed to develop its first remote-controlled straddle carrier.
Electronic control systems manufacturers have had plenty of time to perfect remote control. Remote-controlled model airplanes were first developed in the late 1940s, and radio-controlled toy cars have been available since the mid-1960s. Control systems and related technologies have advanced so much in the ensuing decades that unmanned aerial vehicles (UAVs, also known as drones) that perform missions from bases in the Middle East are controlled by U.S. Air Force pilots stationed stateside.
Controls. The remote control system used for the Straddle Carrier isn’t nearly as complex as the type used for aircraft; it’s closer to the type used to drive a radio-controlled car. However, it’s a robust, industrial-strength version. It consists of two off-the-shelf components from Scanreco, a Maxi transmitter and a G3 receiver.
“The control system provides outputs that are proportional to the inputs, so it doesn’t take long to get a feel for controlling the carrier,” said Martin McVicar, Combilift co-founder and CEO. “The controller works in conjunction with a Danfoss hydraulic valve bank system, both of which provide excellent response—the truck reacts both quickly and smoothly to the operator’s inputs. This design eliminates the cab, but the remote-controlled Straddle Carrier handles quite a bit like one equipped with conventional controls in a cab.”
The operator can control all of the vehicle’s functions by remote control: engine ignition on/off, engine start, drive forward and reverse, steer left and right, increase and decrease speed, engage and disengage the parking brake, raise and lower the front lift, raise and lower the rear lift, move the load laterally left and right, and operate the horn.
A key feature is a five-step switch that raises and lowers the maximum speed, which simplifies training and operation.
“If a new operator needs to slow the carrier’s movement suddenly, he can cut the speed quickly by using this switch, bringing the carrier to a crawl,” McVicar said. “This feature also helps experienced operators slow the truck to achieve very fine positioning when necessary.”
The unit is also equipped with safety features to prevent unwanted operation. For example, the transmitter sends a unique identity code to the receiver, preventing any other transmitter from activating or driving the machine. Furthermore, the receiver is programmed to shut down all of the truck’s motions if the radio link is disrupted.
Training an operator takes about two hours, Christopherson said.
Results. Some of the results are easy to measure: it reduced material handlings from three to two and it lowered the trailer loading time to less than one man-hour. Others aren’t easy to measure, but have big effects on company operations nonetheless. The fabrication shop feeds the staging much more directly than before and therefore it makes only what is needed, reducing work-in-process. Bigger still is the speed with which the company can turn trucks around, which makes it easier to estimate delivery times and keep material flowing to the job site in a timely manner.
However, a much bigger concern is worker safety, Christopherson said. Of the 12 specific areas in which RAI concentrates its safety training, three of them come into play when a spotter climbs onto a trailer bed and a forklift driver approaches with a load: stairway and ladder safety, fall protection, and forklift certification. The remote-controlled carrier eliminates two of them.
The company’s safety record is remarkable. Its 2015 experience modification rate (EMR), 0.67, is far below the industry average (1.0), and the company hasn’t had a lost-time incident in its loading area. So while it would be difficult to improve its safety record in the loading area, removing the spotter is the next step forward. RAI’s management sees this investment as part of an ongoing, forward-thinking strategy to prevent an incident, a way to help keep the work environment safe and send every worker home at the end of the day in the same shape he was in when he arrived at work that morning.
See a video of the carrier in action.
About the Author
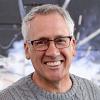
Eric Lundin
2135 Point Blvd
Elgin, IL 60123
815-227-8262
Eric Lundin worked on The Tube & Pipe Journal from 2000 to 2022.
About the Publication
Related Companies
subscribe now
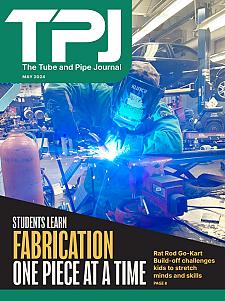
The Tube and Pipe Journal became the first magazine dedicated to serving the metal tube and pipe industry in 1990. Today, it remains the only North American publication devoted to this industry, and it has become the most trusted source of information for tube and pipe professionals.
start your free subscription- Stay connected from anywhere
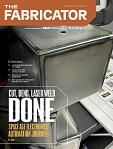
Easily access valuable industry resources now with full access to the digital edition of The Fabricator.
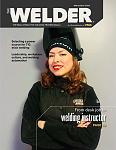
Easily access valuable industry resources now with full access to the digital edition of The Welder.
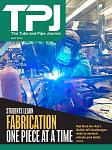
Easily access valuable industry resources now with full access to the digital edition of The Tube and Pipe Journal.
- Podcasting
- Podcast:
- The Fabricator Podcast
- Published:
- 04/30/2024
- Running Time:
- 53:00
Seth Feldman of Iowa-based Wertzbaugher Services joins The Fabricator Podcast to offer his take as a Gen Zer...
- Trending Articles
Zekelman Industries to invest $120 million in Arkansas expansion
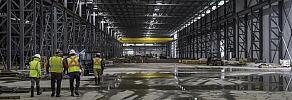
3D laser tube cutting system available in 3, 4, or 5 kW
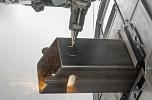
Corrosion-inhibiting coating can be peeled off after use
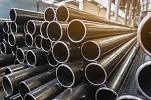
Brushless copper tubing cutter adjusts to ODs up to 2-1/8 in.
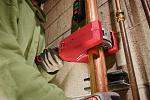
HGG Profiling Equipment names area sales manager
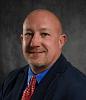
- Industry Events
Pipe and Tube Conference
- May 21 - 22, 2024
- Omaha, NE
World-Class Roll Forming Workshop
- June 5 - 6, 2024
- Louisville, KY
Advanced Laser Application Workshop
- June 25 - 27, 2024
- Novi, MI
Precision Press Brake Certificate Course
- July 31 - August 1, 2024
- Elgin,