Fabrication Segment Manager
- FMA
- The Fabricator
- FABTECH
- Canadian Metalworking
Categories
- Additive Manufacturing
- Aluminum Welding
- Arc Welding
- Assembly and Joining
- Automation and Robotics
- Bending and Forming
- Consumables
- Cutting and Weld Prep
- Electric Vehicles
- En Español
- Finishing
- Hydroforming
- Laser Cutting
- Laser Welding
- Machining
- Manufacturing Software
- Materials Handling
- Metals/Materials
- Oxyfuel Cutting
- Plasma Cutting
- Power Tools
- Punching and Other Holemaking
- Roll Forming
- Safety
- Sawing
- Shearing
- Shop Management
- Testing and Measuring
- Tube and Pipe Fabrication
- Tube and Pipe Production
- Waterjet Cutting
Industry Directory
Webcasts
Podcasts
FAB 40
Advertise
Subscribe
Account Login
Search
How robots are changing heavy fabrication
The new generation of automation helps to keep workers safe and boosts production efficiency in heavy-duty fab shops
- By Chris Poole and Dan Alexander
- March 29, 2017
- Article
- Materials Handling
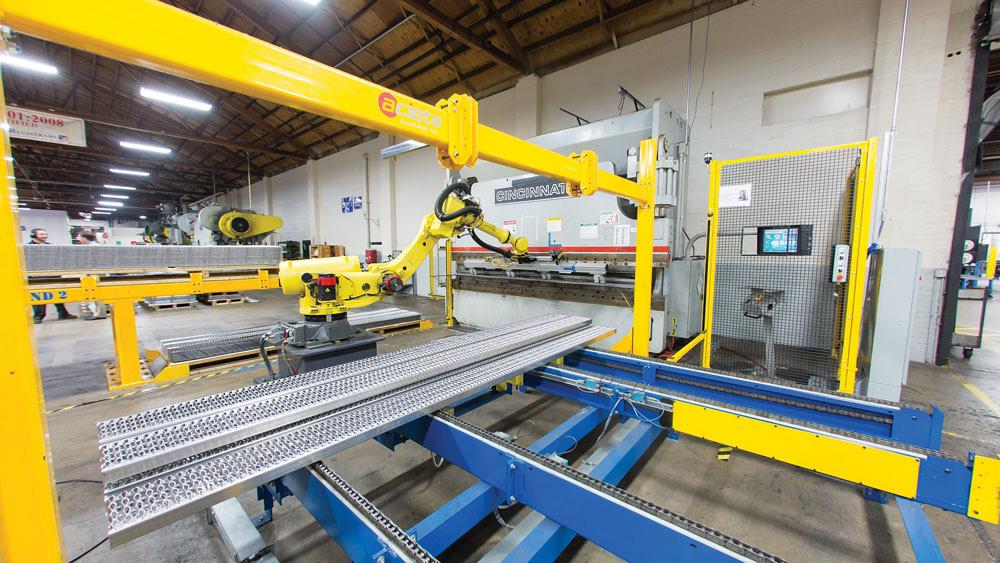
Figure 1
In this automated cell, one robot handles a long and heavy part at a press brake. Such a task might take two or three people to duplicate.
Heavy fabricators, particularly those that work with large-part, large-plate, and foundry applications, have been undergoing a technological evolution with the increasing use of robotic automation. Traditionally, heavy fabricators have relied on people power, hoists, cranes, and manipulators to maneuver large and weighty pieces through the fabrication process. However, robots have become less expensive and easier to use than ever before, which has opened the door for manufacturers and job shops to take a serious look at the benefits and return on investment (ROI) of robotic automation.
Streamlining Large-part Fabrication
Manufacturers of large parts, such as castings and frames for trucks, off-road vehicles, and equipment for agricultural, construction, mining, and defense applications, are limited by their ability to make and move those parts quickly, consistently, and safely. Parts can weigh up to 1,000 lbs. and be as long as 12 ft. Some fabricating activities, such as making bends, call for the giant part to be laboriously moved several times at a press brake.
To improve throughput and quality, large-part manufacturers are turning to robots for machine loading/unloading, part handling, welding, painting, and assembly.
Example No. 1: Making Lift Trucks
A manufacturer of high-capacity lift trucks has the challenges of heavy components and many different parts when compared to smaller-part fabricators. A typical part can be 10 ft. long, 5 ft. wide, and 0.5 in. thick. It is common for parts to require bending to create large flanges, which are sometimes too tall to pull the formed part directly out through the press brake tooling. Two workers on the floor and an equipment operator tilt and remove a part, flip it, and return it to the press brake in an accurate position, ready for the next bend.
By switching part fabrication and transfer—once handled by multiple operators—to a robotic system (see Figure 1), fabricators can increase productivity an average of 50 percent, reduce scrap, and often achieve an ROI of about 18 months. However, these are just the benefits that are easy to calculate on a spreadsheet. Manufacturers benefit from other, less tangible improvements that make robotic automation ideal for fabricating large parts.
Floor space and machine flexibility can be problems for manual fabrication operations. Operators need a machine or adapter near the tooling to feed heavy parts into and remove them from the press brake. Some shops may develop their own system of casters and stands installed permanently into the floor for moving heavy materials. Additionally, as a large part is being flipped manually, it needs an appropriately large area cleared around the machine for workers to maneuver it, which takes up precious floor space.
While doing this type of fabrication work, laborers become fatigued because of the constant heavy lifting. Reassigning operators from a repetitive, unskilled task to a job that challenges their skills is going to be more interesting and usually improves throughput and process efficiency (see Figure 2). Fabricators with robots are able to increase production, be more competitive, and reduce the need for layoffs during occasional downturns.
A robot arm on a robot transport unit (RTU) track system moves to multiple inbound and outbound positions and quickly feeds, flips, reorients, and removes large fork lift parts using more vertical space so less area needs to be cleared around the machine. The RTU and the rest of the robotic cell may occupy comparable floor space, but the ratio of utility to square footage is undoubtedly higher.
Truly enlightened managers understand that workers should be utilized for their maximum talent potential and not wasted on tasks that are better done by a robot. Workers with rewarding jobs are more likely to stay and take an interest in the team’s success. Reducing employee turnover and eliminating the need for repeated training of new employees saves time and keeps production running smoothly without interruption, which translates into profitability. This is especially powerful during the recovery from a down cycle, when quickly ramping back up can play a pivotal role in fulfilling new orders and being a leader.
Example No. 2: Fabricating Large Plate With Robots
For the last two years, high-powered fiber lasers have made it easier to cut thick plate metal faster. As a result, large-plate fabricators are scrambling to keep up with the demand for products such as structural steel, floor grating, tubes, mounting brackets for large equipment, and machine tool bases.
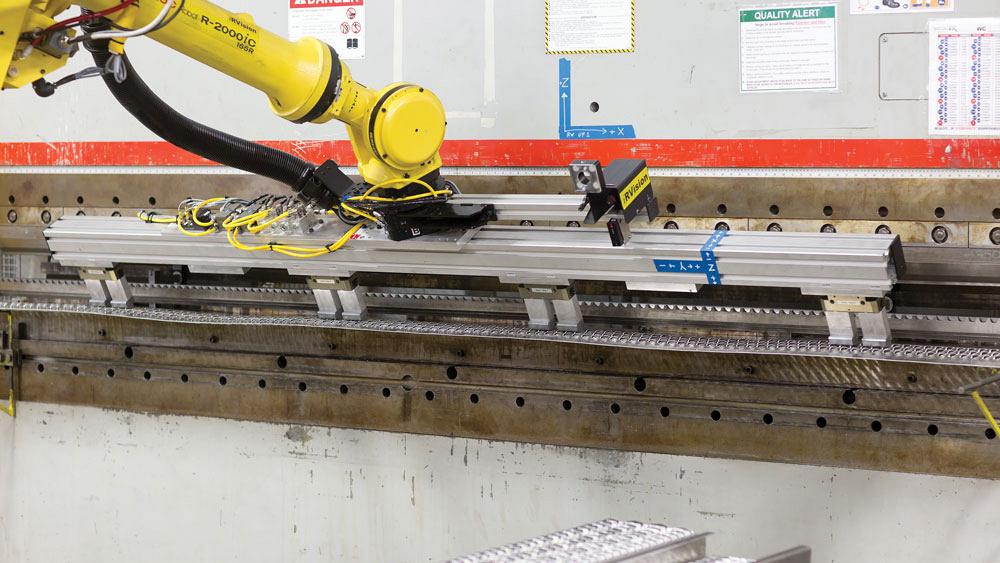
Figure 2
The robot gripper quickly reorients itself to pick up the heavy fabrication and reposition it for the next bend. A press brake operator and a couple of material handlers would be hard-pressed to keep up with the robot.
Robots stand to make a large impact in these types of applications. As an example, let’s look at the process of forming tube from large plate.
To fabricate trapezoid-shaped tubes from flat laser-cut plate, the manufacturer’s biggest challenge is presenting enormous pieces of plate metal, sometimes up to 72 in. long and 0.375 in. thick, to the press brake. First, two operators or a hoist add 90-degree bends with approximately 1-in. flanges on both long edges. Next, a 5-in. radius is formed to close the flanges against the upper die. Then the formed part is slid off the upper die after forming. Production requirements for an operation like this can be up to 400 tubes per day.
In this instance, seeing the opportunity for safer and more efficient operations with large plate, the tube fabricator upgraded to a robotic system, which doubled throughput. Much like the story of the tortoise and the hare, a robot moves plate material consistently and repeatedly. A human worker may move plate quickly for short intervals, but ultimately needs breaks and gets fatigued over time.
Large-plate fabricators with short runs may not see an immediate ROI based solely on throughput, but the safety improvements may help management to accept any robot investment costs. Repeated lifting and twisting lead to musculoskeletal disorders, which cause time away from work. In jobs like these, a robot creates a much safer working environment (see Figure 3).
Workers handling heavy plate are a huge liability for a company. A manufacturer that uses robots for the heavy lifting can lower workers’ compensation expenses and insurance rates, as well as create happier, less fatigued workers who can contribute more to the tasks that further improve line efficiencies.
Example No. 3: Robots in the Foundry
Traditionally, foundries have been resistant to using robotic automation, mostly because of investment cost concerns. However, foundries that upgraded to robots years ago are now much more competitive than manual-process foundries. ROI can happen in as little as six months, so there’s been a growing appreciation for how robots can help a foundry grow.
What often pushes a foundry to change its mind about robots is when it becomes difficult to retain workers. Labor shortages challenge many manufacturers today, especially those with working environments that are dusty, dirty, and unpleasant. Using robots to supplement the existing workforce lets a business accept more orders without being limited by worker availability.
The process of pouring molten metal into dies is repetitive and dangerous, making it a common foundry application for incorporating a robot. In addition to being a safety issue, a manual laborer dipping a ladle into the furnace and transferring molten metal to a die can result in problems with product consistency.
Humans are far from perfect. Many variables are involved in a successful pour, so it’s not surprising that an inconsistent operator pouring molten metal into a die can cause quality problems. Cameras and sensors on a robot can confirm ladle position, metal levels, and angles of the cup during pouring. A robot has an identical pour every time, with the same amount of metal, same time spent on the pour, and same placement of the pour, which result in a very consistent flow into the die, each and every time. Variances in a metal pour impact part quality, which can result in waste and downtime to fix errors.
A line with repeatable quality is more efficient and productive. In addition, workers can be moved to less dangerous jobs such as maintaining dies, inspection, or secondary operations.
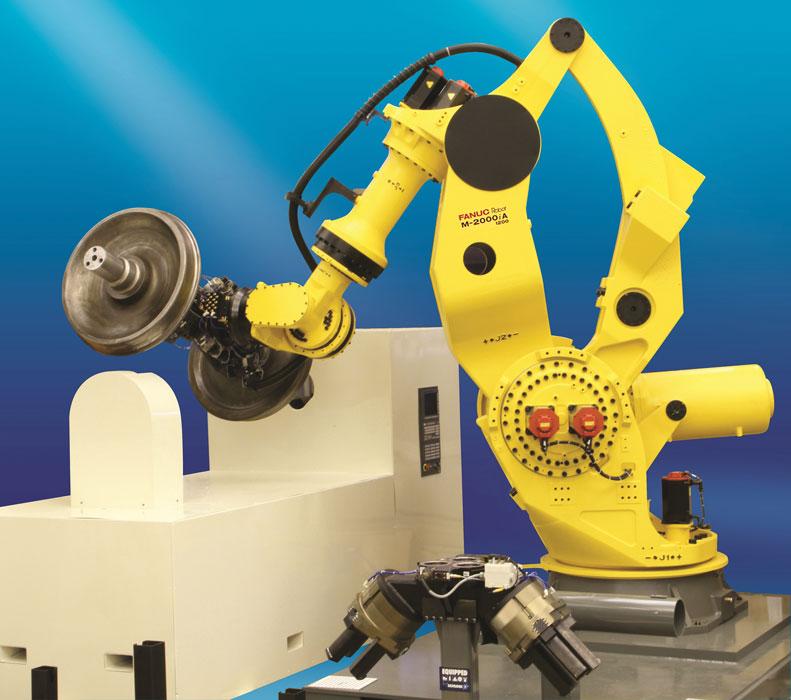
Figure 3
Robots have evolved to the point where they can manipulate very heavy loads. This robot is capable of lifting and maneuvering parts as heavy as 2,600 lbs. Photo courtesy of FANUC America.
Offline Programming
Today’s robotic systems have offline programming capabilities, which removes many of the manual steps in setup and changeover. By working through an entire heavy fabrication process in a virtual environment, operators don’t even need to touch a piece of metal. Instead of workers handling heavy plate unnecessarily and creating scrap during process refinements, the entire fabrication line is established before turning on the machines.
In addition, offline programming minimizes downtime while a cell is configured for a new product. With more simple, intuitive robotic programming available today, most technicians can learn program touchup after just a few hours of training.
Handling large parts and plates is cumbersome, difficult, painstaking, and back-breaking. As heavy fabricators continue to use robots, they will have better control over their businesses and be more competitive. Greater capacity, more projects, and bigger profits will lead to more job creation and new skill sets for workers in North America.
About the Authors
Dan Alexander
Regional Automation and Foundry Applications Manager
414-791-2603
subscribe now
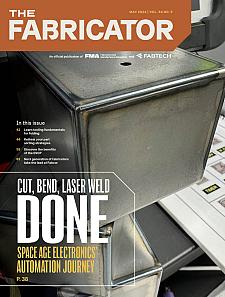
The Fabricator is North America's leading magazine for the metal forming and fabricating industry. The magazine delivers the news, technical articles, and case histories that enable fabricators to do their jobs more efficiently. The Fabricator has served the industry since 1970.
start your free subscription- Stay connected from anywhere
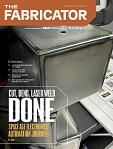
Easily access valuable industry resources now with full access to the digital edition of The Fabricator.
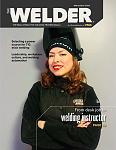
Easily access valuable industry resources now with full access to the digital edition of The Welder.
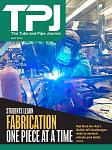
Easily access valuable industry resources now with full access to the digital edition of The Tube and Pipe Journal.
- Podcasting
- Podcast:
- The Fabricator Podcast
- Published:
- 04/16/2024
- Running Time:
- 63:29
In this episode of The Fabricator Podcast, Caleb Chamberlain, co-founder and CEO of OSH Cut, discusses his company’s...
- Trending Articles
Capturing, recording equipment inspection data for FMEA
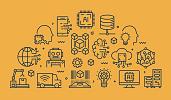
Tips for creating sheet metal tubes with perforations
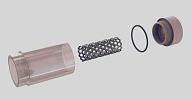
Are two heads better than one in fiber laser cutting?
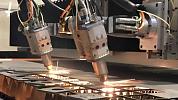
Supporting the metal fabricating industry through FMA
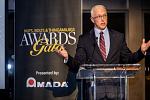
Omco Solar opens second Alabama manufacturing facility
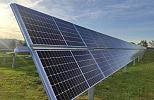
- Industry Events
16th Annual Safety Conference
- April 30 - May 1, 2024
- Elgin,
Pipe and Tube Conference
- May 21 - 22, 2024
- Omaha, NE
World-Class Roll Forming Workshop
- June 5 - 6, 2024
- Louisville, KY
Advanced Laser Application Workshop
- June 25 - 27, 2024
- Novi, MI