Senior Editor
- FMA
- The Fabricator
- FABTECH
- Canadian Metalworking
Categories
- Additive Manufacturing
- Aluminum Welding
- Arc Welding
- Assembly and Joining
- Automation and Robotics
- Bending and Forming
- Consumables
- Cutting and Weld Prep
- Electric Vehicles
- En Español
- Finishing
- Hydroforming
- Laser Cutting
- Laser Welding
- Machining
- Manufacturing Software
- Materials Handling
- Metals/Materials
- Oxyfuel Cutting
- Plasma Cutting
- Power Tools
- Punching and Other Holemaking
- Roll Forming
- Safety
- Sawing
- Shearing
- Shop Management
- Testing and Measuring
- Tube and Pipe Fabrication
- Tube and Pipe Production
- Waterjet Cutting
Industry Directory
Webcasts
Podcasts
FAB 40
Advertise
Subscribe
Account Login
Search
Moving additive manufacturing forward
EWI’s Buffalo Manufacturing Works has all major AM processes in-house
- By Tim Heston
- September 14, 2016
- Article
- Additive Manufacturing
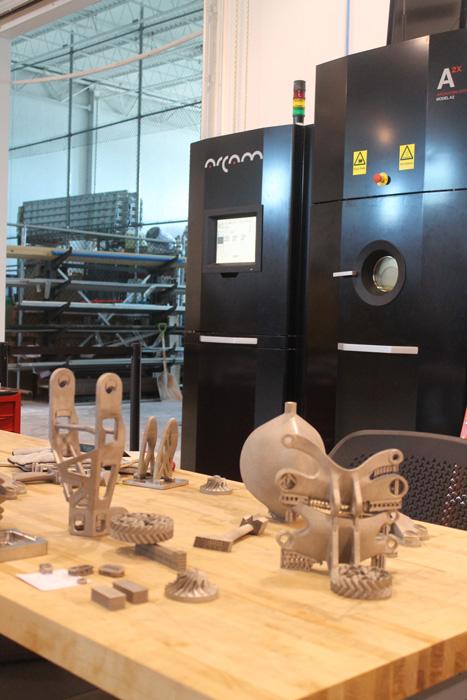
Figure 1
Buffalo Manufacturing Works produced these metal parts with an electron beam powder bed fusion system.
If you attended FABTECH® 2015, you may have taken a photo of the 3-D printed race car or kayak on display at McCormick Place’s Grand Concourse in Chicago. You also may have stopped to take a look at several booths near one of the exhibit hall entrances. Some companies, including several small job shops—early adopters all—demonstrated the geometric possibilities when you build up a part layer by layer.
The show gave a taste of the additive manufacturing (AM) landscape, including the metal additive niche. This month the International Manufacturing Technology Show (IMTS) in Chicago has a two-day conference session devoted to additive processes.
There may be a reason metal additive manufacturing has a presence at both FABTECH, a show largely devoted to sheet metal, plate, tube, and structural forming, fabrication, and welding, and IMTS, best known for machining. Additive has obvious applications in the machine shop. Some machining vendors tout hybrid machines that perform both additive and subtractive manufacturing processes.
At the same time, some of the most well-known metal additive processes, including directed energy deposition and powder bed fusion, essentially fuse metal powders together. “When you get right down to it, [these] metal additive manufacturing processes are welding. Granted, it’s a lot of welding, but it’s still welding.”
So said Michael Ulbrich, president of EWI’s Buffalo Manufacturing Works, a facility that has a full suite of metal additive technologies, from directed energy deposition to sheet lamination. Opened last year in Buffalo, N.Y., the facility is EWI’s first expansion beyond its original facility in Columbus, Ohio, but it won’t be its last. Later this year the organization will open another facility in Loveland, Colo., north of Denver.
Because AM involves the fusing of material, it’s no surprise that EWI has tackled the technology, and not just because of EWI’s roots in welding process development. The organization’s growth plan entails a broad range of manufacturing processes. EWI’s Columbus facility continues its focus on welding and materials joining, and it already has a laser powder bed fusion test bed.
The Buffalo operation focuses on AM and advanced metrology, including computed tomography (CT), as well as industrial automation. The Colorado operation will focus on advanced process monitoring and control technologies.
“A big part of our business model is an industry-led approach,” Ulbrich said. “Everything we do, from the services we provide to the technologies we invest in, focuses on delivering value to a customer today.”
Unlike universities or national labs, EWI does not have any long-term source of funding. In recent years some funds have come from EWI’s own products. “We’re not just doing the development work, we’re also commercializing the technologies, sometimes ourselves and other times with industry partners,” Ulrich said. “That’s a growing part of our business.”
But for the most part, EWI’s funding comes from clients that need to develop an advanced manufacturing process. Ulbrich described the organization as providing a bridge between basic research and manufacturers, many of which don’t have the R&D resources of a Boeing or General Electric.
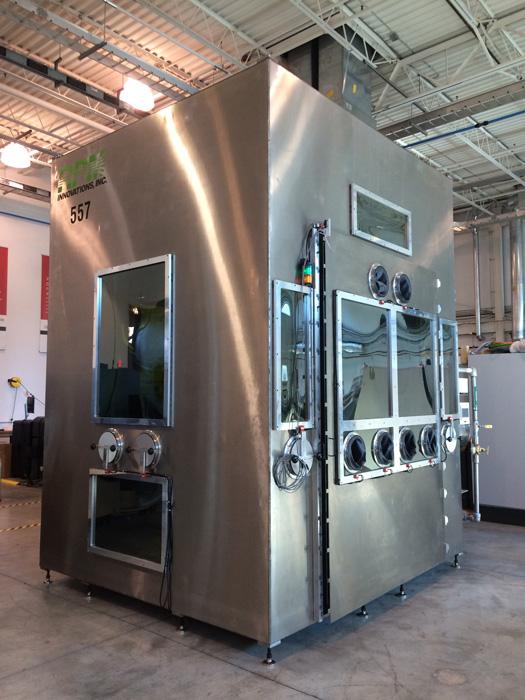
Figure 2
This laser directed energy deposition (L-DED) system can create parts as large as 5 by 5 by 7 feet.
In that vein, EWI launched its Additive Manufacturing Consortium in 2010, a confab of AM stakeholders from public and private sectors, which held its most recent meeting in July at the Buffalo location. People from both sides of the “bridge” attended: researchers from universities and national labs, as well as people from private industry.
Despite all the hype, AM hasn’t spurred an outright revolution in manufacturing; it’s more of a new, albeit powerful and completely different, tool in the manufacturer’s toolbox. It’s also a new technology without long-recognized standards.
Additive has become an important piece of modern manufacturing that, like any other technology, doesn’t reside in a vacuum. It demands expertise in design, materials, processes, and inspection. As Ulbrich explained, EWI’s Buffalo operation has all four.
The Full Suite
“Across our Columbus and Buffalo locations, we have all the different metal additive manufacturing technologies,” Ulbrich said.
In Columbus, EWI has done work in laser powder bed fusion (L-PBF), which uses a laser to fuse the metal powders in a powder bed layer by layer. All of the other AM technologies are at the 12,000-square-foot Buffalo location.Three AM technologies at the facility involve printing polymers, plastics, ceramics, and other materials. Vat photopolymerization creates a part using a UV light to cure a photopolymer resin, layer by layer. Material jetting, for polymers and plastics, is an AM process resembling an inkjet printer. In material extrusion, also called fused deposition modeling (FDM), plastic or polymer material is drawn through a nozzle and is heated and deposited, building up the part layer by layer.
The remaining four AM processes are in the metal additive niche.
Powder Bed Fusion. In addition to the L-PBF system in Columbus, EWI has an electron beam powder bed fusion (EB-PBF) system in Buffalo that uses an electron beam (instead of a laser) in a vacuum to melt metal powders (see Figure 1).
In PBF, a roller deposits a thin layer of powder on a bed, or platen. The laser or electron beam then sinters portions of that layer, effectively fusing one “slice” of the part, per the 3-D CAD model. Once that layer is deposited, the bed moves down, another layer of powder is applied, and another layer is sintered—and so on until the part is complete.
Directed Energy Deposition. In this process, a nozzle mounted to a multiaxis arm feeds either powder or wire into the energy source, which again can be a laser beam or an electron beam. This process resembles cladding in that it can build up material on existing components.
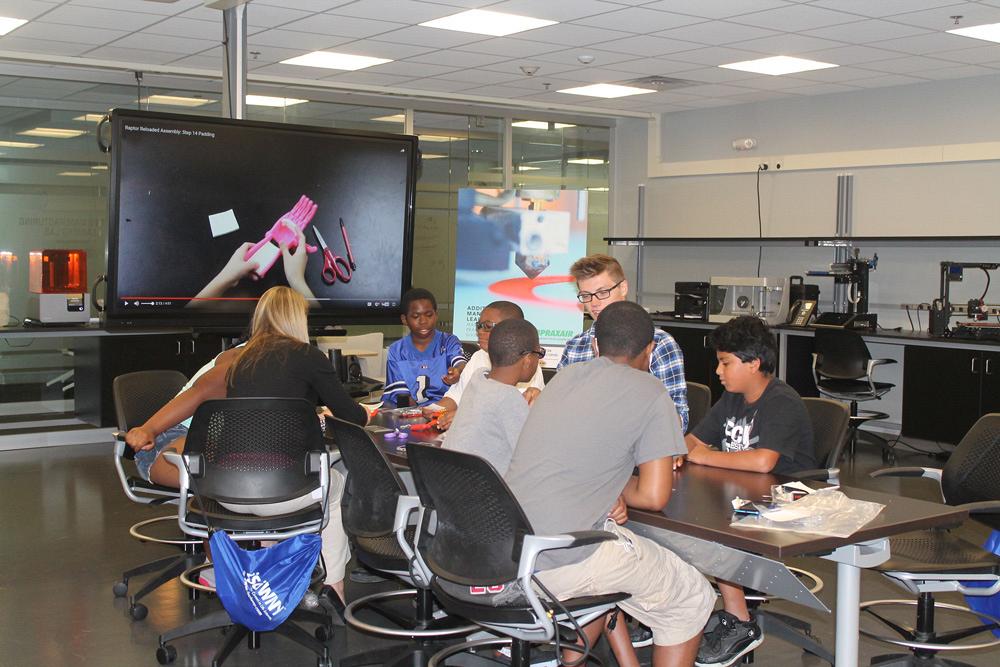
Figure 3
Buffalo Manufacturing Works hosts events for local high schoolers, introducing them to additive technologies.
Buffalo Manufacturing Works currently has laser directed energy deposition (L-DED) systems, including one that can build big parts, up to 5 by 5 by 7 feet (see Figure 2). An electron beam directed energy deposition (EB-DED) system is expected to be delivered by early 2017.
Binder Jetting. This process uses a powder base material and a binder that, as the name suggests, binds the layers together. The process can build parts out of polymers, ceramics, as well as metals like stainless steel.
Sheet Lamination. This process ultrasonically binds sheets of material, including aluminum, copper, and stainless steel.
More Than a Process List
Ulrich added that AM technology development draws expertise from other manufacturing processes. For instance, sheet lamination draws from the company’s years of experience with ultrasonic welding and, most recently, ultrasonic machining—a process EWI is commercializing that uses ultrasound to aid chip flow and facilitate smoother action between the cutting tool and workpiece. PBF and DED development draws from EWI’s experience in laser welding and electron beam welding.
Having all AM capabilities in-house does give the operation flexibility to weigh one technology against another, and the choice, like anything else in manufacturing, depends on the application.
“The main factors are feature size and productivity,” Ulbrich said. A process like L-DED involves relatively low heat and can create extraordinarily fine features, but productivity is low. Meanwhile, an electron beam process like EB-DED has higher productivity, but it may not be able to produce extraordinarily fine features, and it may require some minor postprocess machining. (Of course, L-DED can also require postprocess machining, depending on the application requirements.)
Perhaps more important than having all the processes at hand, Ulrich said, is the organization’s holistic approach, which starts with design. EWI uses software to optimize designs for specific AM processes. For instance, in PBF the bed of powder builds up layer by layer, and the unsintered powder surrounding the sintered material supports the workpiece as it’s produced. There’s no need to design a part for efficient fixturing, as you would for a subtractive process.
“There’s a lot of work regarding topology optimization,” Ulrich said, “so you can take an existing part and redesign it to reduce the material while at the same time allowing it to maintain the same load stresses. And that’s not just looking at the surface, but totally redesigning the part and applying this to different additive technologies based on what makes the most sense. We have a number of [software] packages in-house, and we recently hired someone to focus purely on design for additive manufacturing.”
EWI’s approach also involves inspection, including CT that can peer inside the part structure itself, revealing internal as well as external part features. And some of this work will draw from some advanced metrology and nondestructive examination (NDE) work that will take place at EWI’s Colorado facility. There, staff will focus on streamlining inspection and breaking down the barriers between quality assurance and production. After all, you can’t inject quality into a part that’s already produced. This becomes even more important when working with AM, which generally has long cycle times and often uses expensive materials.
Then there’s the required expertise in powder and materials science in general. “We’re working to help suppliers and manufacturers qualify their powders for additive manufacturing applications,” Ulrich said. “With EWI’s broad materials engineering expertise, lab resources, and AM experience, we are able to determine the powder characteristics needed for today’s AM processes.”
Thinking in 3-D
In May 2016 Buffalo Manufacturing Works hosted a 3-D printing contest that drew about 75 middle and high school students. Among other things, they competed in building the best “baking soda” volcano, using 15 desktop 3-D printers (for making plastic parts) in a lab designed for educational outreach (see Figure 3). They needed to print a volcano spout that would allow the baking soda and vinegar mixture to spew at just the right height: an engineering as well as a 3-D printing challenge.
As Ulrich put it, “We had people thinking in three dimensions.”
Outside prototyping and certain low-volume and one-off parts, AM has been simply too costly for many production applications. It’s hard to beat the part production cycle time of a decades-old mechanical stamping press.
But students who are growing up with 3-D printing may ask different questions. Could dozens of machined parts be replaced with one or a handful of specialized, additively manufactured components? More broadly, could a common product be redesigned from the ground up with AM in mind?
erhaps what makes AM so enticing is that it challenges so many age-old manufacturing rules. But as EWI’s approach shows, AM also builds on what has come before. It still deals with physical material and thermal processes, and the fusing of metal. It requires experts in materials, thermal processing, and inspection. Getting these experts talking may not create an additive manufacturing revolution overnight, but it does move the state of the art forward.
Buffalo Manufacturing Works, 716-710-5500, www.buffalomanufacturingworks.com
About the Author
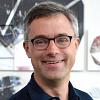
Tim Heston
2135 Point Blvd
Elgin, IL 60123
815-381-1314
Tim Heston, The Fabricator's senior editor, has covered the metal fabrication industry since 1998, starting his career at the American Welding Society's Welding Journal. Since then he has covered the full range of metal fabrication processes, from stamping, bending, and cutting to grinding and polishing. He joined The Fabricator's staff in October 2007.
Related Companies
subscribe now
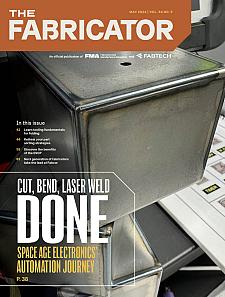
The Fabricator is North America's leading magazine for the metal forming and fabricating industry. The magazine delivers the news, technical articles, and case histories that enable fabricators to do their jobs more efficiently. The Fabricator has served the industry since 1970.
start your free subscription- Stay connected from anywhere
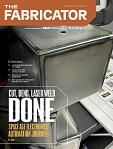
Easily access valuable industry resources now with full access to the digital edition of The Fabricator.
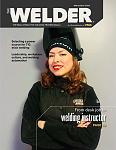
Easily access valuable industry resources now with full access to the digital edition of The Welder.
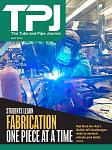
Easily access valuable industry resources now with full access to the digital edition of The Tube and Pipe Journal.
- Podcasting
- Podcast:
- The Fabricator Podcast
- Published:
- 04/16/2024
- Running Time:
- 63:29
In this episode of The Fabricator Podcast, Caleb Chamberlain, co-founder and CEO of OSH Cut, discusses his company’s...
- Trending Articles
Capturing, recording equipment inspection data for FMEA
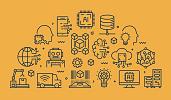
Tips for creating sheet metal tubes with perforations
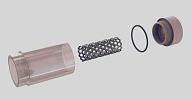
Are two heads better than one in fiber laser cutting?
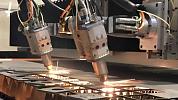
Supporting the metal fabricating industry through FMA
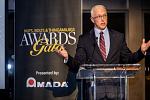
Omco Solar opens second Alabama manufacturing facility
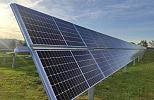
- Industry Events
16th Annual Safety Conference
- April 30 - May 1, 2024
- Elgin,
Pipe and Tube Conference
- May 21 - 22, 2024
- Omaha, NE
World-Class Roll Forming Workshop
- June 5 - 6, 2024
- Louisville, KY
Advanced Laser Application Workshop
- June 25 - 27, 2024
- Novi, MI