Senior Editor
- FMA
- The Fabricator
- FABTECH
- Canadian Metalworking
Categories
- Additive Manufacturing
- Aluminum Welding
- Arc Welding
- Assembly and Joining
- Automation and Robotics
- Bending and Forming
- Consumables
- Cutting and Weld Prep
- Electric Vehicles
- En Español
- Finishing
- Hydroforming
- Laser Cutting
- Laser Welding
- Machining
- Manufacturing Software
- Materials Handling
- Metals/Materials
- Oxyfuel Cutting
- Plasma Cutting
- Power Tools
- Punching and Other Holemaking
- Roll Forming
- Safety
- Sawing
- Shearing
- Shop Management
- Testing and Measuring
- Tube and Pipe Fabrication
- Tube and Pipe Production
- Waterjet Cutting
Industry Directory
Webcasts
Podcasts
FAB 40
Advertise
Subscribe
Account Login
Search
Parts identification for extreme environments
Marking technology designed to endure cleaning, galvanizing, and other harsh processes
- By Tim Heston
- September 8, 2015
- Article
- Materials Handling
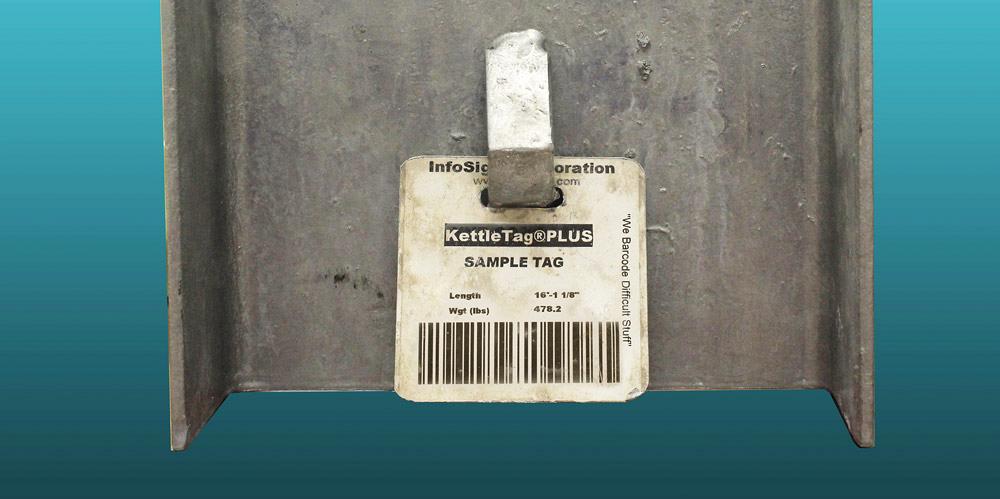
This isn’t a paper tag, but a metal tag with a white coating. The tag remained on the girder throughout the hot-dipped galvanizing process.
It’s not uncommon for a galvanizer to batch two or more jobs together. But what if those jobs are from separate structural fabrication shops? Perhaps the structural beams are similar but still different and destined for construction sites? Immersed in a kettle of zinc at more than 800 degrees F, most part identification marks don’t stand a chance.
“It’s common procedure to remove everything from the steel [before galvanizing]. So if you have paper tags on your steel and I have plastic tags on mine, those will be removed. The work orders will be dipped together in the same process.”
So said Doug Fry, sales manager at Chillicothe, Ohio-based InfoSight Corp., and it’s for this application that InfoSight CEO Dr. John Robertson saw a need for traceability a little more than 10 years ago. Whence came a new marking technology that could withstand hot-dip galvanizing.
In the 1970s Robertson started Telesis Marking Systems, and as part of that business he developed a part marking system for steel mills. The system laser-marked bar codes on metal tags that could be attached automatically to hot billets and slabs. Telesis divested this and other large, custom marking systems in 1993, and from this divesture InfoSight Corp. was formed.
As Fry explained, to call the technology “laser marking” oversimplifies it. The company dubs its marking method LabeLase®. What makes the mark durable isn’t just the laser itself, but the reaction it causes on the label’s white coating and metal substrate. Technically, the laser doesn’t just burn a mark into the metal label but instead induces an interaction between the coating and metal substrate. The resulting mark, Fry said, is designed to be permanent enough to withstand harsh processes like hot-dip galvanizing.
The company does produce automated marking systems that mark directly onto a part. In these instances, the system applies a specialized coating to the area where the label will be, and then marks the bar code (or anything else) onto that coating.
As Fry explained, most structural fabricators start using the identification tags for beams and other components that leave the facility, be it for outside processing like galvanizing or to the job site. Parts are scanned as they leave the structural fabricator and scanned again once they arrive at the galvanizer or job site. Thanks to a bar code tied into a company’s enterprise resource planning (ERP) or similar software, every part has an identity. This ensures that the right component arrives at the right place at the right time.
“Once [fabricators] start using the tag, they see that they have a bar code now, instead of using a basic wax marker or relying on a stenciling kit,” Fry said. “The part now has an identity.”
At first workers in the fab shop’s shipping area may apply the tags to components before they head out the door. Eventually, though, tags often are applied earlier in the process, such as before blast cleaning and painting. If paint needs to be applied, a fabricator can use a metal tag with a clear protective laminate cover. After blasting and painting, the cover can be removed to reveal the bar code underneath.
Finally, workers at a structural fab shop may apply a tag just after the saw or other primary cutting operation. “As soon as they cut a piece, they put a tag on it,” Fry said.
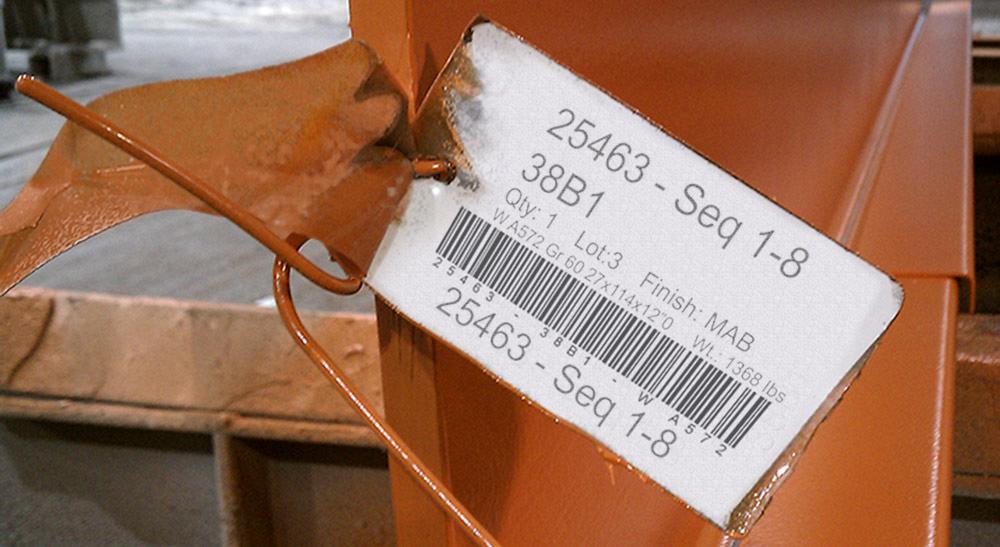
This metal bar code tag was sent through blast cleaning and painting. After painting, the tag’s clear protective laminate cover was removed, revealing the bar code and part number underneath.
If parts spend a lot of time between cutting, punching, and welding or there is a holdup at blast cleaning or painting, parts tracking can reveal these inefficiencies between processes and provide a baseline for improvement. Fry added that the marking technology isn’t limited to bar codes. Drawings, company logos, and anything else that can reasonably fit on a metal tag can work.
As Fry explained, a simple mark, say, “left” or “right,” on a metal tag can help errorproof an operation and, ultimately, free persistent bottlenecks.
Images courtesy of InfoSight Corp., 20700 U.S. Highway 23, P.O. Box 5000, Chillicothe, OH 45601, 740-642-3600, www.infosight.com.
About the Author
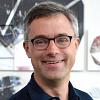
Tim Heston
2135 Point Blvd
Elgin, IL 60123
815-381-1314
Tim Heston, The Fabricator's senior editor, has covered the metal fabrication industry since 1998, starting his career at the American Welding Society's Welding Journal. Since then he has covered the full range of metal fabrication processes, from stamping, bending, and cutting to grinding and polishing. He joined The Fabricator's staff in October 2007.
Related Companies
subscribe now
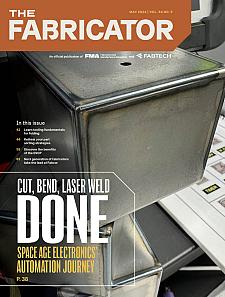
The Fabricator is North America's leading magazine for the metal forming and fabricating industry. The magazine delivers the news, technical articles, and case histories that enable fabricators to do their jobs more efficiently. The Fabricator has served the industry since 1970.
start your free subscription- Stay connected from anywhere
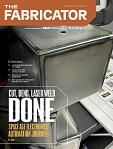
Easily access valuable industry resources now with full access to the digital edition of The Fabricator.
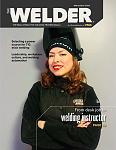
Easily access valuable industry resources now with full access to the digital edition of The Welder.
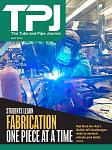
Easily access valuable industry resources now with full access to the digital edition of The Tube and Pipe Journal.
- Podcasting
- Podcast:
- The Fabricator Podcast
- Published:
- 04/16/2024
- Running Time:
- 63:29
In this episode of The Fabricator Podcast, Caleb Chamberlain, co-founder and CEO of OSH Cut, discusses his company’s...
- Industry Events
16th Annual Safety Conference
- April 30 - May 1, 2024
- Elgin,
Pipe and Tube Conference
- May 21 - 22, 2024
- Omaha, NE
World-Class Roll Forming Workshop
- June 5 - 6, 2024
- Louisville, KY
Advanced Laser Application Workshop
- June 25 - 27, 2024
- Novi, MI