Sales Engineer
- FMA
- The Fabricator
- FABTECH
- Canadian Metalworking
Categories
- Additive Manufacturing
- Aluminum Welding
- Arc Welding
- Assembly and Joining
- Automation and Robotics
- Bending and Forming
- Consumables
- Cutting and Weld Prep
- Electric Vehicles
- En Español
- Finishing
- Hydroforming
- Laser Cutting
- Laser Welding
- Machining
- Manufacturing Software
- Materials Handling
- Metals/Materials
- Oxyfuel Cutting
- Plasma Cutting
- Power Tools
- Punching and Other Holemaking
- Roll Forming
- Safety
- Sawing
- Shearing
- Shop Management
- Testing and Measuring
- Tube and Pipe Fabrication
- Tube and Pipe Production
- Waterjet Cutting
Industry Directory
Webcasts
Podcasts
FAB 40
Advertise
Subscribe
Account Login
Search
The next generation of portable beveling
Cutting and machining tables may deliver the best bevel results, but some may find new hand-held equipment to be right for their applications
- By Rohan B. Raut
- March 30, 2016
- Article
- Power Tools
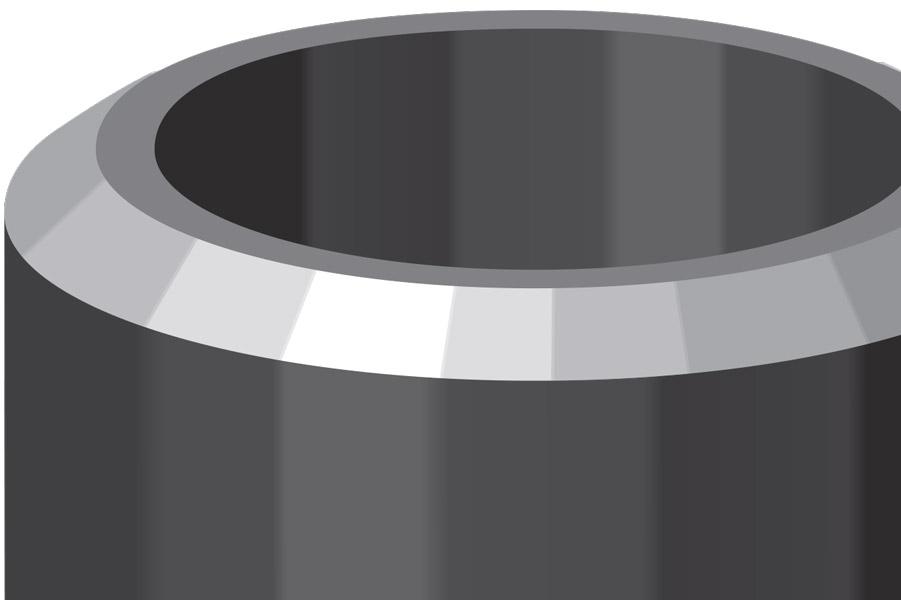
Figure 1
Beveling pipe edges is a critical fabricating task. If the edges are inconsistent, the welder has to contend with variability as the bead is laid, which takes away from the goal of delivering smooth and consistent welding passes.
Proper work preparation typically delivers excellent results. Then it should come as no surprise that good preparation is everything when it comes to creating high-quality welded seams. This is particularly true for fabricators working with plate edges—both straight and curved (see Figure 1)—that are being prepared for V-groove butt welds.
No matter the preparation, both mating pieces need to be compatible. If the fabricator is able to deliver a better groove angle and more symmetrical mating pieces, the better and stronger the final weld will be. The following discussion focuses on all types of metal—carbon steel, stainless steel, aluminum, and other nonferrous metals.
To create the V-groove butt weld (see Figure 2), a fabricator has quite a few preparation options from which to choose; machining, chipping, grinding, oxyacetylene cutting, and air carbon arc cutting are just a sampling. There are pros and cons to consider for the most popular methods. The availability of portable beveling machines also can help to improve the weld prep results.
A Look at Beveling Methods
Grinding is the most common way of preparing a piece of material for the V-groove welding process. A welder uses a resin-bonded grinding wheel and a right-angle grinder to prepare the surface of the material to be welded.
Grinding in this method is quick and easy, and the tools are readily available in the shop or on the job site. Compared to other methods, it is a relatively low-cost way to prepare for the weld. However, although it may be quick and inexpensive, the accuracy of the angle and edge finish cannot be guaranteed, possibly resulting in a compromised final weld. Additionally, this is a rather messy and dangerous method, especially if it is performed in a working environment where the proper safety precautions aren’t taken.
Chipping, most frequently accomplished with a nibbler, removes chunks of material as the nibbler is guided along the edge to be beveled. The prepared edge that results from chipping is unpredictable and uneven and is most often perpendicular to the flat plane of the material.
Oxyacetylene, laser, and waterjet cutting are all nonmechanical methods of removing material to the desired shape and bevel angle. When any of these three are used on a stationary machine, they are extremely quick and accurate. However, if hand-held equipment is used, such as with an oxyacetylene torch, accuracy is sacrificed. These processes can be used on both thin and thicker material. The negative to these three processes is the cost of the equipment and lack of portability due to its size.
Machining, or preparing the edge with a portable mechanical tool equipped with a carbide insert of a desired shape or angle, is one of the most accurate, reliable, cost-effective, efficient, and repeatable methods of achieving the desired edge preparation. With more and more emphasis on getting the job done right—but quickly—machining is becoming the way to achieve the form, fit, and finish required for ideal weld preparation that results in strong, effective, and long-lasting welds. Plus, the portability of today’s edge preparation machines allows them to be used both on the job site and in the shop on both small and large, straight and curved, thin and thick parts.
Machining should be the first choice in edge preparation, mainly because it avoids thermal distortion to the material that is to be welded. When choosing the ideal beveling machine for the application, a fabricator should keep the following qualities in mind:
- Lightweight and easily portable to another area of the shop or to the job site
- Ergonomic handling and easy to guide along the edge of the material
- Robust motor and easy-to-configure milling head to accommodate high-quality, long-lasting carbide inserts
- Multiple angle configurations, or a continuously adjustable angle to allow for flexibility in edge preparations, for the most versatility
Current Hand-held Manual Beveling Technology
For fabricators looking for a cost-effective and portable beveling method for their operations, new hand-held beveling technology is available to meet production goals. With the right tool and a minimal amount of operator training, a fabricator can use a portable beveling machine (see Figure 3) to create a good V-groove edge that results in faster preparation and higher-quality welds.
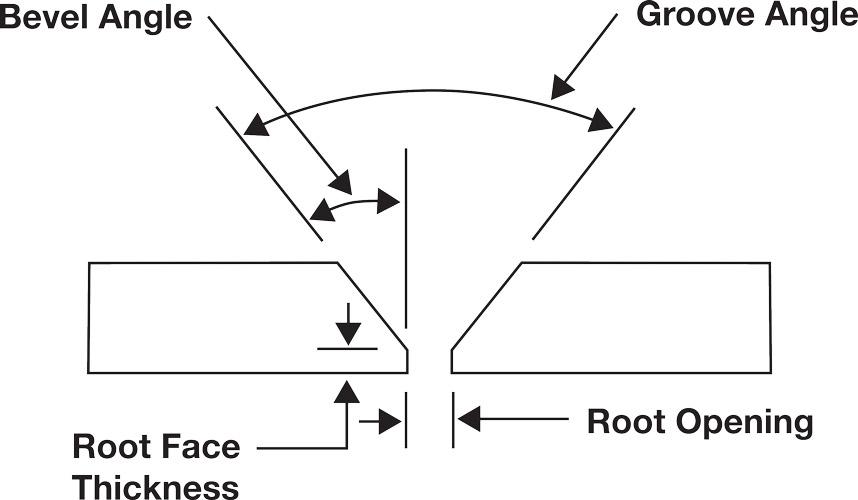
Figure 2
This shows two properly beveled edges that are the first step in delivering a strong V-groove butt weld.
Compact, powerful, and versatile hand-held beveling machines are available in two versions. One type of machine accommodates interchangeable cutting heads, each with a set radius or angle. The other type of hand-held machine has a continuously adjustable angle to allow for a wider range of options for weld preparation.
The most lightweight and portable manual beveling machine, weighing in at around 10 lbs., has interchangeable cutting heads. Each machine typically has a set of two to four angle options—30 degrees, 45 degrees, 0.063 in. (1.6 mm), and 0.098 in. (2.5 mm)—and each milling head accommodates the corresponding angle inserts.
This equipment can bevel small-OD pipe and shorter lengths of plate. In addition to beveling, this type of machine can also be used to deburr and chamfer, straighten edges, and countersink holes.
The second style of machine is also portable, but instead of relying on interchangeable cutting heads to achieve the desired angle, it has continuously adjustable angle settings from 15 degrees to 60 degrees. One milling head holds the sintered carbide cutting inserts that quickly and cleanly prepare for weld seams and bevels on plate or pipes. This machine is suitable for longer lengths of plate and pipes/tubes with an OD of 6.25 in. and larger.
The Next Generation of Plate Beveling
Hand-held, manually guided beveling machines are great for shorter lengths of plate. However, one of the major issues with manual beveling machines is operator fatigue (see Figure 4). Beveling long plates with a hand-held machine (as described previously) requires the operator to constantly hold the machine against the edge of the plate while, at the same time, push the machine forward along the workpiece. In instances where long plates need to be beveled, given the expenditure of operator time and energy, multiple workers are assigned to the same project and work in shifts. This adds time and expense to the project.
A new generation of portable machines automatically bevel unlimited lengths of plate with minimal operator oversight. Designed for plates up to 1.5 in. thick, these self-propelled machines can process both the top and bottom of plate edges in the shop or on the job site. With automatic feed and return, these self-guiding beveling machines attach directly to the plate and have continuously adjustable angles from 15 degrees to 60 degrees and land widths up to 13⁄16 in. Because the units attach to and move along the plate, there is no need for a cart or stand.
Fabricators no longer have to rely on costly cutting tables to deliver the correct beveled edge. Hand-held tools have evolved to deliver similar results.
About the Author
Rohan B. Raut
800-700-5919 / 203-853-9522
subscribe now
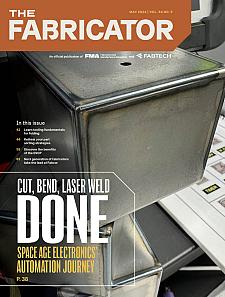
The Fabricator is North America's leading magazine for the metal forming and fabricating industry. The magazine delivers the news, technical articles, and case histories that enable fabricators to do their jobs more efficiently. The Fabricator has served the industry since 1970.
start your free subscription- Stay connected from anywhere
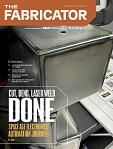
Easily access valuable industry resources now with full access to the digital edition of The Fabricator.
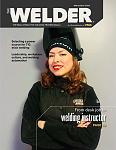
Easily access valuable industry resources now with full access to the digital edition of The Welder.
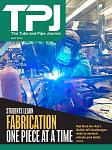
Easily access valuable industry resources now with full access to the digital edition of The Tube and Pipe Journal.
- Podcasting
- Podcast:
- The Fabricator Podcast
- Published:
- 04/16/2024
- Running Time:
- 63:29
In this episode of The Fabricator Podcast, Caleb Chamberlain, co-founder and CEO of OSH Cut, discusses his company’s...
- Industry Events
16th Annual Safety Conference
- April 30 - May 1, 2024
- Elgin,
Pipe and Tube Conference
- May 21 - 22, 2024
- Omaha, NE
World-Class Roll Forming Workshop
- June 5 - 6, 2024
- Louisville, KY
Advanced Laser Application Workshop
- June 25 - 27, 2024
- Novi, MI