- FMA
- The Fabricator
- FABTECH
- Canadian Metalworking
Categories
- Additive Manufacturing
- Aluminum Welding
- Arc Welding
- Assembly and Joining
- Automation and Robotics
- Bending and Forming
- Consumables
- Cutting and Weld Prep
- Electric Vehicles
- En Español
- Finishing
- Hydroforming
- Laser Cutting
- Laser Welding
- Machining
- Manufacturing Software
- Materials Handling
- Metals/Materials
- Oxyfuel Cutting
- Plasma Cutting
- Power Tools
- Punching and Other Holemaking
- Roll Forming
- Safety
- Sawing
- Shearing
- Shop Management
- Testing and Measuring
- Tube and Pipe Fabrication
- Tube and Pipe Production
- Waterjet Cutting
Industry Directory
Webcasts
Podcasts
FAB 40
Advertise
Subscribe
Account Login
Search
Quick die change and the trend toward larger presses
As machines get bigger, QDC keeps pace
- By Mark Cairney
- November 8, 2005
- Article
- Bending and Forming
![]() |
Flexibility and change have become critical components for success in U.S. manufacturing.
Increasingly for contract stampers, these changes include the acquisition of larger mechanical presses. It now is quite common for stampers to use presses with capacities from 800 to 2,000 tons and bed sizes spanning at least 180 inches wide and 84 inches long.
Benefits of Larger Presses
Although there are numerous reasons for this upsizing trend, four specific factors stand out:
- Cheaper labor costs abroad have led many companies to shift the production of small, single-hit parts to overseas facilities. The remaining jobs often are larger (such as automobile hoods and body panels) and thus require presses of substantial size.
- The industry as a whole has realized that using a single large press for progressive-die operations often is more cost-efficient than operating multiple smaller presses.
- Larger press beds allow stampers to perform secondary operations, such as welding and assembly. This in turn provides the value-added benefit of producing a more finished part.
- Increased bed sizes provide increased flexibility for future business opportunities by accommodating the attachment of a variety of transfer systems, as well as facilitating progressive-die operations.
QDC and Large Presses
This shift toward larger presses may result in greater flexibility and time, labor, floor space, and cost savings. But an important question remains: How will this trend affect the future of quick die change (QDC) within the stamping industry?
The answer to that question is critically important, not only to QDC original equipment manufacturers (OEMs), but also to U.S. contract stampers. Before they make sizable investments in capital equipment, it is essential for these organizations to determine the value of QDC in relation to larger presses.
![]() |
Figure 1 Dual-stage die carts allow a die to be prestaged onto one side of the cart in preparation of an upcoming changeover. When the change becomes necessary, a single operator then can move the empty side of the cart into position in front of the press. |
Although the general benefits of QDC have been well-documented, companies need to determine if these factors hold true as press sizes grow.
With this in mind, perhaps the first point to consider is that performing a changeover manually, with crowbars and fork trucks, becomes increasingly time-consuming and difficult as die sizes and weights escalate. The equipment used must be able to transport and position the dies in a quick, efficient, accurate manner.
Additionally, it's important to note that the same competitive and economic factors that have led many organizations to streamline their progressive-die stamping processes also make QDC an attractive option. It becomes a bottom-line issue: The quicker changeover occurs, the more money a company can make. This becomes even more relevant in relation to larger presses, because the potential for extended downtime during changeover becomes greater as die sizes grow.
![]() |
Figure 2 T tables or L tables are mounted to the floor in the rear of the press. Both of these configurations allow two dies to be handled simultaneously. |
Finally, QDC equipment has a positive effect on pressroom safety. By reducing the number of accidents and work-related ergonomic problems, QDC equipment protects the health and safety of employees and drives down the costs associated with medical leave, workers' compensation, lost productivity, and the hiring and training of replacement labor. Although safety always is an important issue, it takes on even greater significance when large dies are being handled because the potential for serious injury becomes greater.
Main Categories of QDC Equipment
Once a stamper decides to implement QDC, the next step is to identify what types of die change equipment are most effective for use with large presses. Before exploring specific pieces of equipment, it is helpful to have a basic understanding of the three main categories into which all QDC components (and systems) fall:
- Die clamping. QDC clamps can be secured quickly to the press bolster and ram. Both clamping and unclamping can be accomplished automatically or with a small amount of manual assistance. Although mechanical varieties are available, hydraulic clamps generally offer a higher degree of safety. Typically, if a hydraulic clamp is not positioned properly, the controls will receive a low-pressure reading or electrical signal, and the press will not be allowed to operate.
- Die transfer and positioning. This equipment grouping allows dies to be loaded into a press (or unloaded from a press) and moved into position quickly and accurately. It helps eliminate the dangers associated with traditional manual methods of die change and also reduces the risk of damaging dies during the handling process.
- Die transport. Transport equipment helps ensure the safe and timely movement of dies between storage locations and press side loading (and unloading) positions.
Transfer and Transport Equipment
All of the preceding equipment categories typically comprise a complete QDC system, regardless of the press size. However, it is the transfer and transport equipment that has the most effect on increasing the operational uptime of large presses. Following are the three prime examples of such QDC equipment:
- Die carts. The prime function of these rail-guided carts is to remove dies from press beds and replace them with new dies that are moved in from storage positions. The carts can handle dies up to 150 tons and can reduce changeover time to less than five minutes.
Dual-stage die carts can handle two dies simultaneously (see Figure 1). This capability allows a die to be prestaged onto one side of the cart in preparation of an upcoming changeover. When the change becomes necessary, a single operator then can move the empty side of the cart into position in front of the press
An automated push-pull rigid chain system then is activated to pull the die (or sometimes the entire bolster) onto the cart. The cart then is repositioned to align the new die in front of the press, and the push-pull rigid chain is activated once again to position the die within the bed. - T tables or L tables. This die transfer equipment typically is mounted to the floor in the rear of the press (seeFigure 2). As the names suggest, these tables resemble the capital letter T or L. Both of these configurations allow two dies to be handled simultaneously.
The T arrangement, for example, is designed to accommodate dies in three distinct positions: left, right, and center. A new die can be prestaged on the left or right position before a changeover. When the press stops, an automated push-pull rigid chain system is activated to pull the die out of the press and onto the center position.
At this point a second push-pull rigid chain is activated to move the unneeded die sideways onto the empty location at the right of the table. The new die then is pushed into the center position and then into the appropriate position on the press bed.
Options are available on the table. One such option is to hinge the center portion of the table, making it possible to swing it out of the way. This gives operators unobstructed access to the back of the press when the table is not in use. - Rigid chain rolling bolsters. These transfer and positioning systems can be used for presses with bed heights up to 30 inches. Each system has hydraulic die lifters or hydraulic cylinders that are mounted to lift four bolster wheels into functioning positions upon activation. Each wheel is positioned to slide into one of two grooved rails that are installed flush with the floor.
A rigid chain system pushes the bolster out of the press during changeover. At this point an operator can unbolt the die and remove it with an overhead crane. The bolster then is ready to receive the new die, which is bolted and pulled back into the press. The whole process can be completed in 10 to 15 minutes.
To reduce downtime even further, a dual rolling bolster system can be used. This system has a second bolster positioned in front of or behind the press, which allows an operator to prestage a new die before changeover. When the rigid chain is activated, the first bolster is pushed out of the press, and the second bolster (carrying the new die) is pulled in. This reduces changeover to as little as five minutes.
Economic factors and a desire for increased efficiency have caused the stamping industry to gravitate slowly toward larger presses, in turn significantly affecting the future of QDC. These changes have increased the overall value of QDC and elevated the importance of specific pieces of die transport and transfer equipment.
Through the use of such tools as T tables, die carts, and rolling bolster systems, stamping companies can help increase the uptime of their pressroom operations, increase levels of operational safety, and improve their bottom lines.
Mark Cairney is marketing manager with Serapid Inc., 5400 18 Mile Road, Sterling Heights, MI 48314, 586-274-0774, fax 586-274-0775, info-us@serapid.com, www.serapid.com.
About the Author
Related Companies
subscribe now
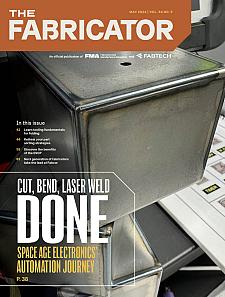
The Fabricator is North America's leading magazine for the metal forming and fabricating industry. The magazine delivers the news, technical articles, and case histories that enable fabricators to do their jobs more efficiently. The Fabricator has served the industry since 1970.
start your free subscription- Stay connected from anywhere
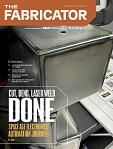
Easily access valuable industry resources now with full access to the digital edition of The Fabricator.
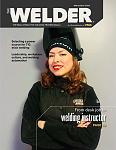
Easily access valuable industry resources now with full access to the digital edition of The Welder.
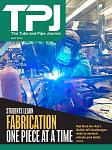
Easily access valuable industry resources now with full access to the digital edition of The Tube and Pipe Journal.
- Podcasting
- Podcast:
- The Fabricator Podcast
- Published:
- 04/16/2024
- Running Time:
- 63:29
In this episode of The Fabricator Podcast, Caleb Chamberlain, co-founder and CEO of OSH Cut, discusses his company’s...
- Industry Events
16th Annual Safety Conference
- April 30 - May 1, 2024
- Elgin,
Pipe and Tube Conference
- May 21 - 22, 2024
- Omaha, NE
World-Class Roll Forming Workshop
- June 5 - 6, 2024
- Louisville, KY
Advanced Laser Application Workshop
- June 25 - 27, 2024
- Novi, MI