Contributing Writer
- FMA
- The Fabricator
- FABTECH
- Canadian Metalworking
Categories
- Additive Manufacturing
- Aluminum Welding
- Arc Welding
- Assembly and Joining
- Automation and Robotics
- Bending and Forming
- Consumables
- Cutting and Weld Prep
- Electric Vehicles
- En Español
- Finishing
- Hydroforming
- Laser Cutting
- Laser Welding
- Machining
- Manufacturing Software
- Materials Handling
- Metals/Materials
- Oxyfuel Cutting
- Plasma Cutting
- Power Tools
- Punching and Other Holemaking
- Roll Forming
- Safety
- Sawing
- Shearing
- Shop Management
- Testing and Measuring
- Tube and Pipe Fabrication
- Tube and Pipe Production
- Waterjet Cutting
Industry Directory
Webcasts
Podcasts
FAB 40
Advertise
Subscribe
Account Login
Search
Material handling on squaring shears
Aiding productivity by making the operator's job easier
- By Rod Stouder
- June 13, 2001
- Article
- Shearing
Often it is thought that to get more production from a shearing operation, another shift, or even a new shear must be added. However, because of a lack of funds, personnel, or floor space, a new shear is not always the answer.
The basics of a productive shearing operation are often overlooked. What good is it to have a shear that will do 30 to 60 strokes per minute (SPM) if the material coming into and going out of the shear is not being properly handled?
Typically, only 5 percent of a shearing operation is spent with the shear ram going up and down, cutting material. This means that the other 95 percent is spent handling the flow of material being sheared. Thirty percent of this handling is done on the front side, and 65 percent takes place on the back of the shear.
Material handling involves labor. In the shearing operation, labor is the same whether the shear operator is feeding sheet, cutting, or picking up the mess at the back of the shear.
Improving the flow of material into and out of the shear can increase shearing output. With the use of some basic material handling equipment, a shearing operation can be made more productive.
Feeding the Shear
The first place to consider material handling equipment for a squaring shear is at the front of the shear, especially if the shear is mounted flat on the floor.
Most shears have a 32-inch passline, which means that the shear table is 32 inches from the floor. It has been said that shear tables have been at the same height since the 1920s. If persons of average height are pushing steel at a 32-inch table, that means they are bending over, which is hard on their backs.
Constantly bending over can cause back strain. The more strain that takes place, the more the operator will stop shearing and straighten to relieve the pain. When there is less strain and pain, there should be more productive shearing taking place. Those with shearing operations should think about putting their shears on risers to at least a 36- to 38-in. working passline.
Material flow into the shear can also be improved with infeed assist tables. By keeping the next piece to be sheared at table height or a little higher, the operator can let the material flow downward toward the shear. It is much easier to control a sheet sliding down than it is to lift and pull the same sheet up and onto the shear table.
The operator can choose the most comfortable infeed height and maintain that controlled height at all times. Again, when the operator is working at a comfortable work height, shearing time can become more productive.
Ball transfer and caster fields or even powered infeed rollers can also reduce strain on shear operators. When less force is used feeding the material into the shear, more finished material should come out the back.
Removing Material from the Shear
![]() |
Figure 1: A material support system for a shear. |
The time that passes between the cutting of material and removing it from the shear can account for as much as 65 percent of the shearing operation. This means that for the 15 or 20 minutes worth of shearing, twice this much time is spent sorting and stacking finished parts behind the shear.
A material support system (see Figure 1) at the back of the shear can save wear and dulling on the lower blade because it holds the sheet up and keeps it from dragging across the knife. A support system also holds the sheet in place so that the operator can keep his hands away from the blade during shearing. In addition, a support system eliminates the need for personnel to be under or behind the shear, which means a safer work area. These systems also provide truer backgauging of the parts.
When producing parts that are the same size, a stacker working behind the conveyor eliminates the need for a person to stack by hand. A stacker can place the sheets in a tight stack for banding and shipping. A stacker can also stack the sheets tightly front-to-back and loose from left to right. This makes the sheets easier to handle at the next workstation.
![]() |
Figure 2: A shear with conveyors can be fitted with built-in material supports and trim cut separators. |
Some conveyors have material supports and trim cut separators built into them. While the shear is cutting parts, these devices separate the trim from the finished pieces going out the back of the shear housing. The finished parts then fall into a safe work area (see Figure 2).
Working off of a shear table that has a 32-inch passline, a stacker can make a stack height of 16 to 20 inches. Putting the shear on risers would allow more stack height. As the shear table goes up from the floor, so does the useable stack height. In a production run, this means less time is spent stopping to remove sheared stacks.
Safety
Safety is a major concern. By adding material handling equipment, the risk of injury in the workplace can be reduced with the added benefit of increased production output.
Employee Support
Not every shearing operation will benefit from material handling equipment. However, managers who think it is worth considering should discuss equipment options with the shear operators. Without their input, material handling changes may not pay off in increased shear output.
About the Author
subscribe now
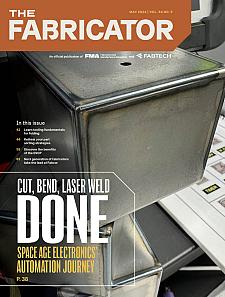
The Fabricator is North America's leading magazine for the metal forming and fabricating industry. The magazine delivers the news, technical articles, and case histories that enable fabricators to do their jobs more efficiently. The Fabricator has served the industry since 1970.
start your free subscription- Stay connected from anywhere
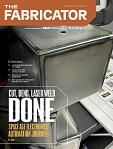
Easily access valuable industry resources now with full access to the digital edition of The Fabricator.
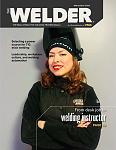
Easily access valuable industry resources now with full access to the digital edition of The Welder.
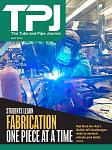
Easily access valuable industry resources now with full access to the digital edition of The Tube and Pipe Journal.
- Podcasting
- Podcast:
- The Fabricator Podcast
- Published:
- 04/16/2024
- Running Time:
- 63:29
In this episode of The Fabricator Podcast, Caleb Chamberlain, co-founder and CEO of OSH Cut, discusses his company’s...
- Trending Articles
Capturing, recording equipment inspection data for FMEA
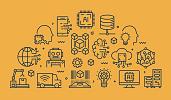
Tips for creating sheet metal tubes with perforations
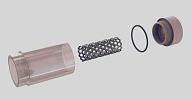
Are two heads better than one in fiber laser cutting?
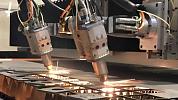
Supporting the metal fabricating industry through FMA
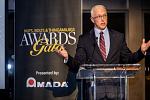
Omco Solar opens second Alabama manufacturing facility
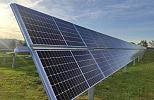
- Industry Events
16th Annual Safety Conference
- April 30 - May 1, 2024
- Elgin,
Pipe and Tube Conference
- May 21 - 22, 2024
- Omaha, NE
World-Class Roll Forming Workshop
- June 5 - 6, 2024
- Louisville, KY
Advanced Laser Application Workshop
- June 25 - 27, 2024
- Novi, MI