Senior Editor
- FMA
- The Fabricator
- FABTECH
- Canadian Metalworking
Categories
- Additive Manufacturing
- Aluminum Welding
- Arc Welding
- Assembly and Joining
- Automation and Robotics
- Bending and Forming
- Consumables
- Cutting and Weld Prep
- Electric Vehicles
- En Español
- Finishing
- Hydroforming
- Laser Cutting
- Laser Welding
- Machining
- Manufacturing Software
- Materials Handling
- Metals/Materials
- Oxyfuel Cutting
- Plasma Cutting
- Power Tools
- Punching and Other Holemaking
- Roll Forming
- Safety
- Sawing
- Shearing
- Shop Management
- Testing and Measuring
- Tube and Pipe Fabrication
- Tube and Pipe Production
- Waterjet Cutting
Industry Directory
Webcasts
Podcasts
FAB 40
Advertise
Subscribe
Account Login
Search
Advancement challenges in metal fabrication
A changing career ladder complicates the skilled worker problem
- By Tim Heston
- March 2, 2017
- Article
- Shop Management
When I started covering metal fabrication in the late 1990s, I asked readers the classic business-reporter question: “What’s your greatest challenge running your shop?”
I’ve asked it hundreds of times, and I can count on one hand how many times people didn’t answer with, “We can’t find skilled people.” The answer has become so predictable that I now ask the question with an “other than skilled labor” caveat. I know what the greatest challenge is; I just want to know the runner-up.
The statistics say that fewer people are creating more value than ever in manufacturing. This makes sense, considering how technology has helped everyone produce more in less time, and quite often (although it’s not the ideal) with less knowledge, thanks to user-friendly controls and software designed to simplify machine operation.
And yet thousands of jobs remain unfilled.
So why does the labor problem persist? Many point to the skills gap, but that doesn’t make sense for every situation. After all, many modern machines are actually simpler to operate.
I have a hypothesis: A changing career path has exacerbated the labor problem. You can see this if you think about two careers, one of someone about to retire and another of a rookie just coming onboard.
The industry veteran began his career before computers were commonplace. Most important, he moved up a career ladder that had a lot of rungs. He spent a time grinding and as a helper, moving and prepping material. He then spent time as a welder, starting with the simple welds and then, after years of experience, moving on to more challenging work.
He started when manufacturing employed a far greater percentage of the overall labor force. The fabricator employed a lot of people, all at different rungs of the career ladder. Lead times also were longer, and it took longer for jobs to make their way through the shop.
Over the years the shop became more automated and positions on the career ladder were eliminated. No longer did the shop need a layout person, and with faster and more precise machines, more structural members were bolted, not welded. At the same time, fabricated structures became ever more complicated.
What manual welding remains requires true welding talent. The people with that talent are now nearing retirement, and the fabricator no longer can find enough people with experience to replace them.
The welder who started 30 years ago climbed the career ladder, then saw the career rungs disappear behind him. No longer could welders spend years learning the trade. They needed to dive right to challenging work—not an easy thing to do, even for welders with formal training.
Now consider a person just beginning at the same structural fabricator. He starts as a helper, then climbs up the ladder. He shows promise, and so after only a year on the job he’s put on one of the shop’s most advanced plate cutting machines. It has a user-friendly touchscreen control with a 3-D graphical interface—again, designed to help make operator training easier.
He receives the next job, sets up the material, then commences the operation. The machine cuts the plate and moves it automatically downstream, where a QA person notices that the job was cut out of the wrong material grade. It was an honest mistake. The young operator just misread the material label, yet in no time flat he fabricated a large amount of expensive scrap.
The modern shop has two kinds of positions to fill: the semiskilled (weld grinding, material handling, etc.) and the skilled—positions that take varying degrees of dexterity, concentration, and critical thinking. In fact, more fab shop managers today are telling me they’re having trouble filling those semiskilled positions with reliable people. A skilled person may have gone to technical school, learned the ins and outs of software, and hit the ground running on the shop floor. A semiskilled person probably didn’t go to technical school and sees a wide gap between him and highly skilled personnel. Many may view it as “just a job” for this month or this year, not a career.
The problem of finding good people goes back decades, and it happens to align with the gradual changes manufacturing has undergone, spurred by technology and accelerated by globalization and the evolution of capitalism. No matter your opinion on the trade debate, it’s tough to argue with this: People want things better, faster, and cheaper, and getting two out of three isn’t good enough.
When push comes to shove, fabricators that have trouble finding welders, press brake operators, or other highly skilled individuals step up in-house training. We’ve covered a few such fabricators in this magazine that have increased their training efforts. We’ve also covered companies that have partnered with community colleges and have even launched their own schools—like Winsted, Minn.-based Millerbernd Mfg. Co. and Saginaw, Mich.-based Merrill Technologies Group.
Sometimes they’ve restructured their organizations with a renewed focus on worker career paths; managers talk with new employees about their goals and what they want their career to look like. General Stamping & Metalworks in South Bend, Ind., and Special Products & Mfg. in Rockwall, Texas, are prime examples.
Reportedly, these efforts also help overcome (though not entirely) the “these kids don’t know how to work hard today” challenge. With processes documented (i.e., no more tribal knowledge), training formalized, and good communication at every level, the leaders at these and other companies tell me they no longer hear the “these kids today” comments like they used to.
A year ago, as part of The FABRICATOR’s Leadership Summit event, I visited Workshops for Warriors, a San Diego school for veterans who want to pursue a career in machining, welding, and metal fabrication. I was shown the donated machinery, the workspace, and the expansion plans. It was all very impressive, but I was perhaps most impressed with the students. Some drove several hours one way every day to attend, and the school is strict; being a minute late is a serious problem.
Most significant, these students maintain focus and think critically. Modern machines have given everyone so much productive power at their fingertips. Space out and load the wrong material grade, and you can fabricate a lot of scrap in a hurry. Talking with Workshops for Warriors students, I kept thinking, “The industry needs more of these people.”
Today the value of such programs that foster commitment, focus, and critical thinking—whether in a trade school or in-house—cannot be understated.
About the Author
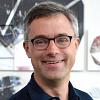
Tim Heston
2135 Point Blvd
Elgin, IL 60123
815-381-1314
Tim Heston, The Fabricator's senior editor, has covered the metal fabrication industry since 1998, starting his career at the American Welding Society's Welding Journal. Since then he has covered the full range of metal fabrication processes, from stamping, bending, and cutting to grinding and polishing. He joined The Fabricator's staff in October 2007.
Related Companies
subscribe now
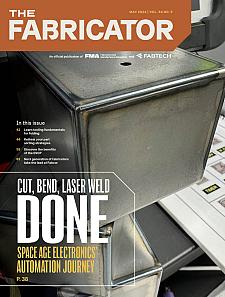
The Fabricator is North America's leading magazine for the metal forming and fabricating industry. The magazine delivers the news, technical articles, and case histories that enable fabricators to do their jobs more efficiently. The Fabricator has served the industry since 1970.
start your free subscription- Stay connected from anywhere
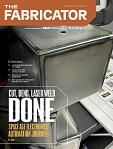
Easily access valuable industry resources now with full access to the digital edition of The Fabricator.
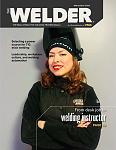
Easily access valuable industry resources now with full access to the digital edition of The Welder.
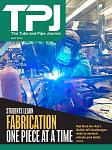
Easily access valuable industry resources now with full access to the digital edition of The Tube and Pipe Journal.
- Podcasting
- Podcast:
- The Fabricator Podcast
- Published:
- 04/16/2024
- Running Time:
- 63:29
In this episode of The Fabricator Podcast, Caleb Chamberlain, co-founder and CEO of OSH Cut, discusses his company’s...
- Trending Articles
Capturing, recording equipment inspection data for FMEA
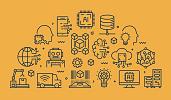
Tips for creating sheet metal tubes with perforations
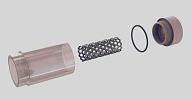
Are two heads better than one in fiber laser cutting?
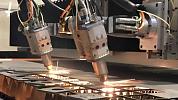
Supporting the metal fabricating industry through FMA
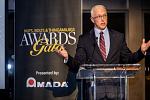
Omco Solar opens second Alabama manufacturing facility
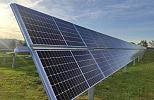
- Industry Events
16th Annual Safety Conference
- April 30 - May 1, 2024
- Elgin,
Pipe and Tube Conference
- May 21 - 22, 2024
- Omaha, NE
World-Class Roll Forming Workshop
- June 5 - 6, 2024
- Louisville, KY
Advanced Laser Application Workshop
- June 25 - 27, 2024
- Novi, MI