President
- FMA
- The Fabricator
- FABTECH
- Canadian Metalworking
Categories
- Additive Manufacturing
- Aluminum Welding
- Arc Welding
- Assembly and Joining
- Automation and Robotics
- Bending and Forming
- Consumables
- Cutting and Weld Prep
- Electric Vehicles
- En Español
- Finishing
- Hydroforming
- Laser Cutting
- Laser Welding
- Machining
- Manufacturing Software
- Materials Handling
- Metals/Materials
- Oxyfuel Cutting
- Plasma Cutting
- Power Tools
- Punching and Other Holemaking
- Roll Forming
- Safety
- Sawing
- Shearing
- Shop Management
- Testing and Measuring
- Tube and Pipe Fabrication
- Tube and Pipe Production
- Waterjet Cutting
Industry Directory
Webcasts
Podcasts
FAB 40
Advertise
Subscribe
Account Login
Search
An introduction to reliability-centered maintenance
This information-gathering process can help to keep equipment up and running
- By Bill Frahm
- September 10, 2015
- Article
- Shop Management
Miguel de Cervantes once said, “Forewarned, forearmed; to be prepared is half the victory.” In manufacturing, this is as true as in any endeavor.
Equipment failures in your metal forming facility can lead to downtime and lost production, poor product quality, injuries, death, and environmental damage. Failures will happen, but you can prevent the most damaging consequences with awareness and preparation.
Over a machine's productive lifetime, components wear and corrode from heat, friction, and chemical reaction. Reliability-centered maintenance (RCM) is an accepted process to:
- Create awareness of the causes of failures.
- Anticipate the consequences of equipment failure.
- Develop a cost-effective plan to prevent costly breakdowns.
Failure modes and effects analysis (FMEA) is the foundation of RCM. FMEA identifies potential failures and their probable consequences. The analysis also prescribes remedial actions to prevent or repair failures. RCM uses the results of the FMEA, statistical experiments, and employee experience to create a maintenance schedule to prevent critical consequences. The result is that your schedules migrate from costly and ineffective periodic maintenance to a preventive maintenance program that is proactive and responsive to current and projected equipment conditions.
In response to industry confusion about RCM, the Society of Automotive Engineers published the standard JA1011. The standard defines what elements must be included in an effective RCM process. This standard defines seven questions that it must address to be considered an RCM process:
- What are the functions and associated desired standards of performance of the asset in its present operating context (functions)?
- In what ways can it fail to fulfill its functions (functional failures)?
- What causes each functional failure (failure modes)?
- What happens when each failure occurs (failure effects)?
- In what way does each failure matter (failure consequences)?
- What should be done to predict or prevent each functional failure (proactive tasks and task intervals)?
- What should be done if a suitable proactive task cannot be found (default actions)?
Definitions help to further explain these categories.
Functions. To understand failure, you must understand the intended functions of the identified equipment. Intended functions include both the process and result of equipment operations and the equipment’s functional specifications. For example, a hydraulic pump may include a specification to “provide flows from 0.23 to 65 GPM at 2,000 RPM and hydraulic pressures of up to 15,000 PSI.”
Functional Failures. A functional failure means that the equipment may fail to perform its intended function within the defined specification. This may include the equipment's failure to perform the defined function, poor performance of the function, or performing an unintended function. The equipment functions properly when it consistently performs the expected function within its specified limits.
Failure Modes. This defines the events that can cause each failure in a part or subsystem. Generally, the failure mode defines the way the failure occurs. The mode also should define the failure state of the item. Generally, failure modes include such things as friction, excessive heat, and wear and tear. Failure modes also may include human error and design flaws.
Failure Effects. This defines the immediate effect of a failure on equipment operation, function, or status. Definitions of failure effect should include evidence that the failure occurred, threats to safety or the environment, effects on production or operations, expected physical damage resulting from the failure, and actions to repair the failure.
Failure Consequences. This defines the results of a failure. Results may include effects on such things as product quality, cycle times, downtime, economics, employee and environmental safety, and mission accomplishment. RCM recognizes that the consequences of failure are more important than the technical aspects of the failure itself. The categories of failure consequences include:
- Hidden failures. Hidden failures have no direct impact themselves, but may expose the company to multiple cascading failures with serious consequences.
- Safety and environmental consequences. Safety consequences can lead to injury or death. Environmental consequences can be issues that violate local, national, or international environmental standards. Environmental consequences also may lead to injury and death.
- Operational consequences. Operational consequences affect production (output, product quality, customer service, or operating costs in addition to the direct cost of repair).
- Nonoperational consequences. Evident failures that fall into this category affect neither safety nor production, so they involve only the direct cost of repair.
Proactive Tasks and Task Intervals. These define the maintenance tasks necessary to prevent failures or repair equipment should failure occur. In a proactive maintenance operation, maintenance task intervals will be based on the criticality of failure consequences, predictive measures of equipment cycles (such as mean time between failures and mean time to failure), and monitored equipment conditions. In cases where consequences are negligible and repair inexpensive, you may choose to run the component to failure and repair as necessary.
Default Actions. These are tasks to perform when a suitable proactive task is not known or available. Default actions may include redesign, run-to-failure, and root cause analysis.
To get the best results in your analysis, you will need to understand production’s history with equipment maintenance as well as the behavioral characteristics of equipment components. The tools and techniques that support your efforts include FMEA, Weibull analysis, failure curves, thermography, and vibration analysis. Opening conversations with machine operators also will give insight into the behaviors of your equipment and the operators’ actions to remedy perceived problems. We will discuss these techniques further in subsequent articles.
About the Author
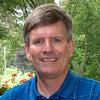
Bill Frahm
P.O. Box 71191
Rochester Hills, MI 48307
248-506-5873
subscribe now
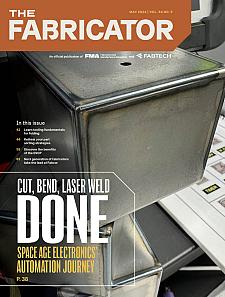
The Fabricator is North America's leading magazine for the metal forming and fabricating industry. The magazine delivers the news, technical articles, and case histories that enable fabricators to do their jobs more efficiently. The Fabricator has served the industry since 1970.
start your free subscription- Stay connected from anywhere
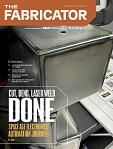
Easily access valuable industry resources now with full access to the digital edition of The Fabricator.
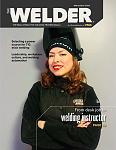
Easily access valuable industry resources now with full access to the digital edition of The Welder.
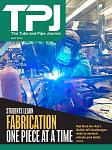
Easily access valuable industry resources now with full access to the digital edition of The Tube and Pipe Journal.
- Podcasting
- Podcast:
- The Fabricator Podcast
- Published:
- 04/16/2024
- Running Time:
- 63:29
In this episode of The Fabricator Podcast, Caleb Chamberlain, co-founder and CEO of OSH Cut, discusses his company’s...
- Trending Articles
Capturing, recording equipment inspection data for FMEA
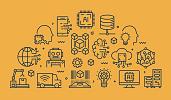
Tips for creating sheet metal tubes with perforations
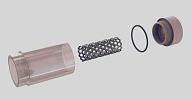
Are two heads better than one in fiber laser cutting?
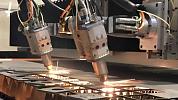
Supporting the metal fabricating industry through FMA
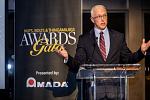
Omco Solar opens second Alabama manufacturing facility
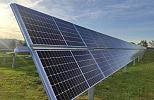
- Industry Events
16th Annual Safety Conference
- April 30 - May 1, 2024
- Elgin,
Pipe and Tube Conference
- May 21 - 22, 2024
- Omaha, NE
World-Class Roll Forming Workshop
- June 5 - 6, 2024
- Louisville, KY
Advanced Laser Application Workshop
- June 25 - 27, 2024
- Novi, MI