Editor-in-Chief
- FMA
- The Fabricator
- FABTECH
- Canadian Metalworking
Categories
- Additive Manufacturing
- Aluminum Welding
- Arc Welding
- Assembly and Joining
- Automation and Robotics
- Bending and Forming
- Consumables
- Cutting and Weld Prep
- Electric Vehicles
- En Español
- Finishing
- Hydroforming
- Laser Cutting
- Laser Welding
- Machining
- Manufacturing Software
- Materials Handling
- Metals/Materials
- Oxyfuel Cutting
- Plasma Cutting
- Power Tools
- Punching and Other Holemaking
- Roll Forming
- Safety
- Sawing
- Shearing
- Shop Management
- Testing and Measuring
- Tube and Pipe Fabrication
- Tube and Pipe Production
- Waterjet Cutting
Industry Directory
Webcasts
Podcasts
FAB 40
Advertise
Subscribe
Account Login
Search
Keeping pace with fabricating technology
Wisconsin job shop has relied on cutting-edge equipment to stay on top of increased customer demands
- By Dan Davis
- February 10, 2016
- Article
- Shop Management
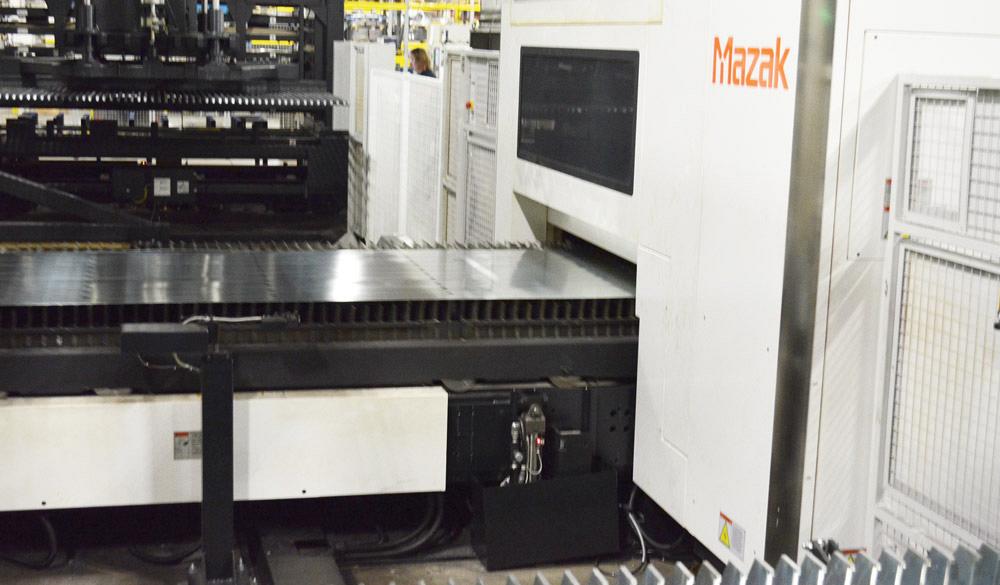
Figure 1
Sjoberg Tool’s new Mazak Optiplex 3015 4-kW fiber laser cuts sheet metal at such a rapid pace that it is changing the way that the shop floor approaches
certain fabrication jobs.
For being only 46, Jim Sjoberg talks like someone who has seen just about everything in metal fabricating. That’s not hard to believe, however, considering that he started receiving a paycheck when he was 12.
“I helped put in the yard when they built the shop,” he said, referring to horticultural handiwork at the old “new” building, which was erected in 1982.
Today Sjoberg Tool & Manufacturing Corp. operates in a 112,000-square-foot facility in Hartland, Wis., which it has called home for over a third of its 40 years of existence. The company, founded by Sjoberg’s dad, a tool- and diemaker, has welcomed the third generation of Sjobergs into the family business.
With the next generation of Sjobergs now learning the metal fabricating ropes, they are getting a firsthand look at what fabricating technology means for the shop’s success.
“My family has always invested in new equipment, not mansions and cars,” Sjoberg said. “I don’t drive a jalopy, but I don’t have a $200,000 car either. We’ve always had state-of-the-art equipment and that is why we’ve thrived.
“I doubt other privately held companies would be happy with our model. That’s pretty typical in the industry. They don’t want to spend the capital. They want to keep the profit margin huge,” he added. “A family business is willing to do it for less [of a profit margin] typically.”
Keeping up With Customers
Even as a youngster Sjoberg could see why technology was so important to the business: The manufacturing focus could change pretty rapidly.
Sjoberg Tool & Manufacturing began as a tool and die shop, but in the mid-1980s it jumped into high-volume part production. One of the company’s sales representatives won a very substantial metal forming contract, and Sjoberg Tool was suddenly in the stamping business.
Some other significant contracts soon pulled the company into the metal fabricating arena as well. This led to the purchase of its first turret punch press in the late 1980s and its first laser cutting machine in 1992.
The punch press and laser were kept busy, but stamping still dominated the manufacturing mix in the early 1990s. No one thought twice about investing in tooling for production; it was the way it was done in the past, and no one was questioning the wisdom of it—yet.
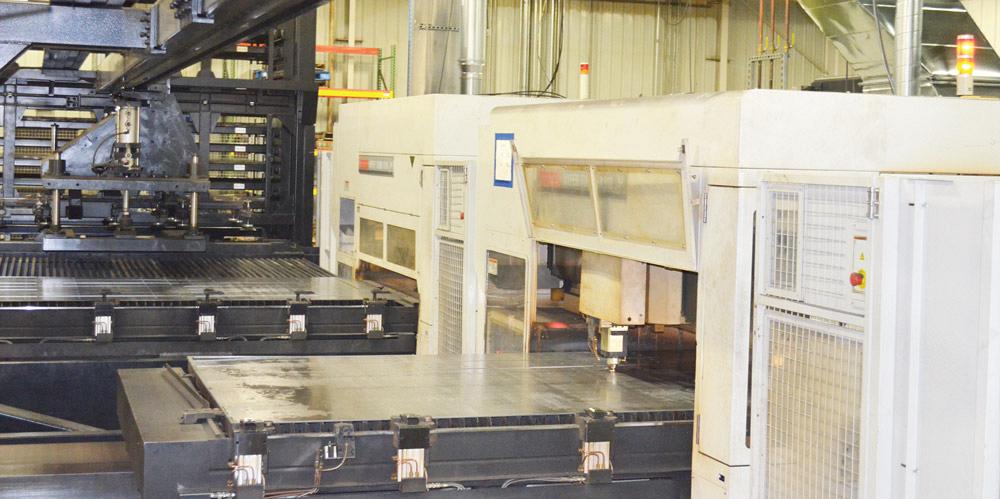
Figure 2
Two of Sjoberg Tool’s Mazak 4-kW CO2 laser cutting machines are connected to a material storage and retrieval system that allows for the 6-year-old machines to remain efficient part producers, particularly for 10-gauge or thicker mild steel.
That started to change by 1994, according to Sjoberg, when the fabricator built its current manufacturing facility. It was going to fill the shop floor with laser cutting capability and fewer stamping presses. The days of 100,000-part orders per month were drawing to a close.
The era of low-volume, high-mix manufacturing had yet to emerge fully. The punch presses and laser cutting machines were still used to pump out hundreds to thousands of the same part.
Sjoberg said the transition to expectations for just-in-time delivery in the 2000s changed that. Manufacturing customers wanted just the parts that were needed, so they didn’t have to go to the trouble of storing and tracking excess inventory.
The six- to seven-week lead time for orders has gone the way of the duplicator punch press. Most of the work now falls into a three- to five-day turnaround time, if it doesn’t require paint. (Sjoberg does not provide finishing services at its facility, but a truck from its powder coating service supplier is kept at the shop. The truck is filled and sent to the custom coater as many as five times per week.) Even long-term customers that have worked with Sjoberg Tool long enough to accommodate a four-week lead time typically slip in hot jobs with their regularly occurring orders.
“Delivery is not a given,” Sjoberg said.
That’s where the fabricator can stand out. Sjoberg said the company maintains an on-time delivery rate of about 99 percent. (The average on-time delivery rate for most job shops, according to the Fabricators & Manufacturers Association’s most recent “Financial Ratios & Operational Benchmarking Survey,” is 87.12 percent. It’s been around that level for the past four years.)
“It just keeps getting tighter and tighter every year,” he added.
He credits his approximately 75 employees and an experienced management team that are committed to getting quality products out the door when they are expected to. The can-do attitude provides the motivation to satisfy the customer.
But having the right equipment helps the Sjoberg Tool staff maintain that positive attitude.
Keeping up With Technology
A prime example of the investment in technology that Sjoberg Tool makes is its new Mazak Optiplex 3015, a 4-kW fiber laser (see Figure 1). It was installed eight months ago, and the fabricator is still getting used to its impact on the shop floor.
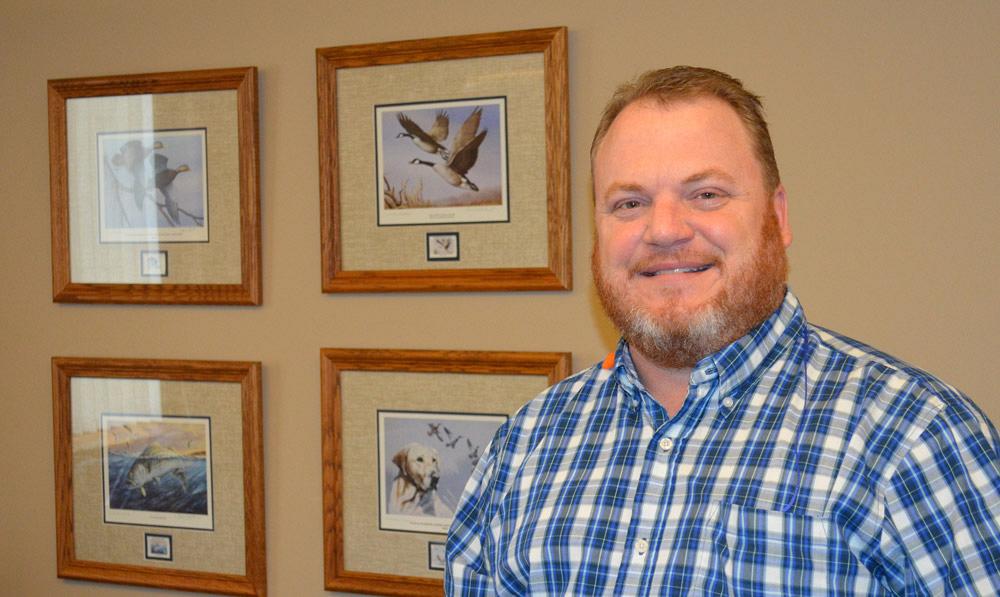
“My competitors are changing and adapting, and I need to as well, because once you get too far behind that curve, you’re never going to catch up. You’re going to be in trouble.” — Jim Sjoberg, Sjoberg Tool & Manufacturing Corp.
“We’re finding out just what we can cut,” said Randy Manhardt, a machine programmer at Sjoberg Tool.
For example, the fiber laser cuts 10-gauge steel at twice the rate of a traditional 4-kW CO2 laser cutting machine, of which Sjoberg Tool still has three (see Figure 2). (The fabricator has six laser cutting machines altogether.) On light-gauge steel, it’s no contest when comparing the fiber laser’s cutting speeds to the CO2’s. Manhardt said that they have found that the fiber laser, in fact, is taking work away from the turret punching equipment (see Figure 3).
Manhardt added that the new technology really hasn’t needed full-time supervision. The automated material storage tower keeps the machine fed, which necessary is because the cutting head reaches speeds of up to 2,400 IPM on very thin-gauge sheet metal. He added that the cutting head was still using the same lens after six months of operation.
Sjoberg Tool has a lot of bending capacity. It has 12 press brakes and four folding machines, two of which are Schröder machines with bidirectional bending (see Figure 4). These machines can make up and down bends without the operator having to flip the panel.
The most recent addition to the fleet of press brakes represents Sjoberg Tool’s first electric press brake, a 100-ton SafanDarley E-Brake with a 10-ft.-wide bending window (see Figure 5). Robert Manhardt, the plant superintendent, said that press brake has the capability to get bending jobs up and running in about 10 minutes, which includes programming. The brake’s controller quickly determines the bend sequence from CAD files and instructs the operator about what tooling is needed (because the tooling library is preinstalled in the software). The operator can install the tooling in the Wila clamping system and go right into bending.
“Repeatability on the electric press brake is unbelievable,” Robert Manhardt said. “The hydraulics can’t match it.”
The fabricator had a 16-ft. Accurpress press brake installed toward the end of 2015. It almost exclusively bends 24-gauge parts as wide as 13 ft.
To make space for the new equipment, Sjoberg said the company invested in a couple of compact racking systems with cassettes that slide in and out of the tower structure with the assistance of a lift truck (see Figure 6). He added that one of these towers replaces three racks typically found in shops.
While its fiber laser cutting machine may have removed some work from the turret punch presses, punching remains a core fabricating activity for Sjoberg Tool. The company has six punch presses, two of which have load/unload capability (see Figure 7).
In what was once the toolroom, machining is now done. The company has four vertical machining centers. Sjoberg said a majority of the machining that takes place is for value-added work done to sheet metal assemblies. The goal is to do as much as possible of that work in-house, eliminating the need to send the assemblies out to a machine shop. The shop isn’t necessarily seeking to take on jobs that call solely for machining.
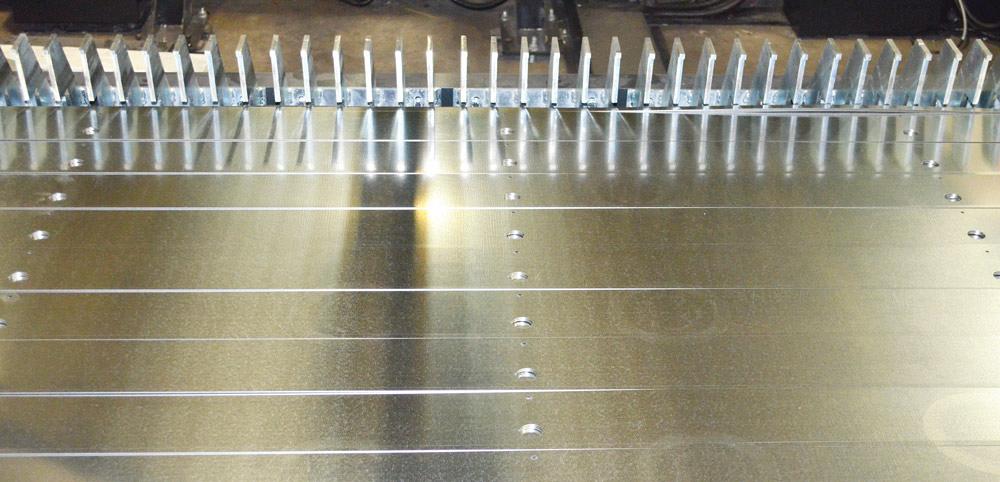
Figure 3
For this long part, the turret punch press can’t match the production speed of the fiber laser cutting machine. Because the part is not hole-intensive, the fiber laser can cut the holes quickly and then blaze through the straight-line cuts. The turret punch would require much more time using a shearing tool to make those same long cuts.
Keeping up With Trends
Coinciding with the capital equipment investments are investments in training the workforce. Supported by state grant money, which covers two-thirds of the overall training cost, the fabricator has been able to pay for 5S lean manufacturing and general skills training. Waukesha County Technical College has provided the instruction for these initiatives.
Sjoberg said the company was just starting the second phase of training, in which the remainder of the company is being exposed to basic lean manufacturing terminology and practices. Training also will focus on the tutoring of “champions,” he said, who will help the company get its own program off the ground and hopefully sustain it over the long term.
Sjoberg Tool also created a new position in 2015 to support this transformation. A new engineer, whose sole function is to identify continuous improvement opportunities within the company, has been on the job for just over nine months.
Perhaps symbolic of this need to change is the very rear of the facility. Equipment doesn’t dominate the landscape back there. Shelving does.
On those shelves are long parts that came from the shop floor (see Figure 8). They are being held for a few large customers until they are needed. Those customers are practicing their own version of lean manufacturing, and Sjoberg Tool is responsible for supplying the parts on a JIT basis.
Managing inventory isn’t necessarily what metal fabricators want to do, but it is what fabricators do to satisfy customers. Sjoberg Tool has adapted to holding more inventory over the years, and that probably won’t change. Company management knows that it has to keep pace with customer demands if it wants to remain relevant.
Sjoberg Tool & Manufacturing Corp., 535 S. Industrial Drive, Hartland, WI 53029, 262-367-4469, www.sjobergtool.com
Accurpress, www.accurpress.com
Big Steel Rack, www.bigsteelrack.com
Mazak Optonics Corp., www.mazakoptonics.com
Rainer, www.rainer.it
SafanDarley, www.safandarley.com
Wila USA, www.wilausa.com
About the Author
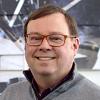
Dan Davis
2135 Point Blvd.
Elgin, IL 60123
815-227-8281
Dan Davis is editor-in-chief of The Fabricator, the industry's most widely circulated metal fabricating magazine, and its sister publications, The Tube & Pipe Journal and The Welder. He has been with the publications since April 2002.
subscribe now
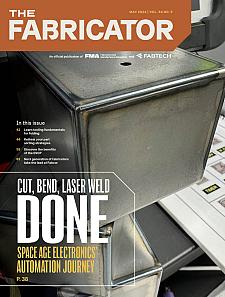
The Fabricator is North America's leading magazine for the metal forming and fabricating industry. The magazine delivers the news, technical articles, and case histories that enable fabricators to do their jobs more efficiently. The Fabricator has served the industry since 1970.
start your free subscription- Stay connected from anywhere
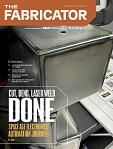
Easily access valuable industry resources now with full access to the digital edition of The Fabricator.
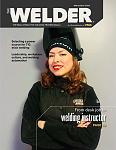
Easily access valuable industry resources now with full access to the digital edition of The Welder.
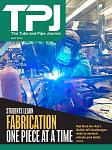
Easily access valuable industry resources now with full access to the digital edition of The Tube and Pipe Journal.
- Podcasting
- Podcast:
- The Fabricator Podcast
- Published:
- 04/16/2024
- Running Time:
- 63:29
In this episode of The Fabricator Podcast, Caleb Chamberlain, co-founder and CEO of OSH Cut, discusses his company’s...
- Industry Events
16th Annual Safety Conference
- April 30 - May 1, 2024
- Elgin,
Pipe and Tube Conference
- May 21 - 22, 2024
- Omaha, NE
World-Class Roll Forming Workshop
- June 5 - 6, 2024
- Louisville, KY
Advanced Laser Application Workshop
- June 25 - 27, 2024
- Novi, MI