Editor-in-Chief
- FMA
- The Fabricator
- FABTECH
- Canadian Metalworking
Categories
- Additive Manufacturing
- Aluminum Welding
- Arc Welding
- Assembly and Joining
- Automation and Robotics
- Bending and Forming
- Consumables
- Cutting and Weld Prep
- Electric Vehicles
- En Español
- Finishing
- Hydroforming
- Laser Cutting
- Laser Welding
- Machining
- Manufacturing Software
- Materials Handling
- Metals/Materials
- Oxyfuel Cutting
- Plasma Cutting
- Power Tools
- Punching and Other Holemaking
- Roll Forming
- Safety
- Sawing
- Shearing
- Shop Management
- Testing and Measuring
- Tube and Pipe Fabrication
- Tube and Pipe Production
- Waterjet Cutting
Industry Directory
Webcasts
Podcasts
FAB 40
Advertise
Subscribe
Account Login
Search
Technology Spotlight: Managing manufacturing information overload
Managing manufacturing information overload
- By Dan Davis
- March 2, 2017
- Article
- Shop Management
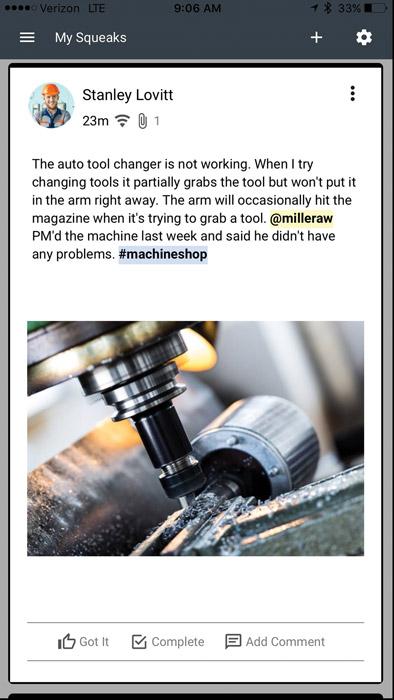
Figure 1
While this may look like a typical social media post, this production update has been created and shared on a platform that aims to help streamline information management for manufacturers and to boost collaboration among co-workers and supply chains.
As metal fabricators and formers strive to deliver parts to customers in the most streamlined manner possible, they are still reliant on traditional shop floor communications, typically dominated by the likes of job packets, white- boards, lights, and alarms. Of course, packets get lost. Whiteboards aren’t located near every work area. Lights and alarms only work when people notice them. Traditional communication methods are not that dynamic. There is a reason that electronic correspondence has replaced snail mail at the job and outside of work.
With that in mind, many shops may have embraced electronic communications more fully. For example, today’s machine tools can be programmed to send out text or e-mail messages detailing job statuses. The problem with this type of communication advancement is that people are now inundated with information. They are growing immune to the multitude of texts and emails that fill up their phones and inboxes, respectively.
The combination of traditional and electronic communications simply isn’t getting it done on the shop floor, where real-time information is critical. In fact, industry experts suggest that the loss associated with poor communication exceeds $240,000 per year (based on two minutes of downtime per month, measured at $10,000 per minute) for a typical midsized manufacturer.
To combat this, IGear has launched what it’s calling an Industrial Internet of Things messaging system to counteract that data deluge often bombarding manufacturing workers. The company, which has spent the last 30 years developing systems and software designed to transform shop floor information into actionable data for manufacturing managers, calls the messages delivered on this platform Squeaks. This messaging app notifies those in a communication group about production status updates, preventive maintenance reminders, or anything else that is judged noteworthy about the production process (see Figure 1). (The messages sent out over this platform are called “squeaks.”)
“This is all about how you take the data and tailor it to your job function,” said Mark Doyle, senior sales executive, IGear.
IGear views this sort of messaging platform as making a real impact in these areas of manufacturing information management, delivery, and adoption:
- Capturing the data. With Squeaks, real-time machine-generated data can be combined with conversations occurring between shop floor workers, supervisors, engineers, and the front office. This makes side conversations available to all and provides instantaneous context for the manufacturing data being fed to the group. The goal is to provide richer information that leads to better decisions.
- Better filtering. If people can improve the filtering of information being sent their way, they can get the details they specifically need without having to wade through extraneous noise.
- Delivering rich visuals. If a picture is worth a thousand words, a video must be worth exponentially more than that. This type of platform allows for the inclusion of graphs, charts, photos, videos, and other multimedia to illustrate a point in conjunction with the written information. The use of these tools makes the consumption of complex data easier.
- Clarifying ownership. Date and time stamps on messages clearly raise the stakes of problem resolution. Everyone is on the clock. These messages also clarify who is responsible for delivering resolutions.
- Boosting collaboration. This type of messaging medium makes it easy for people to interact more easily, even when they aren’t in the same vicinity. Individuals at all levels of the organization are allowed to share insight. When people are given the opportunity to contribute to a conversation, they feel more like team members.
At FABTECH® in Las Vegas last November, Squeaks was integrated with a Komatsu servo stamping press and a Genesis Systems Group robotic welding cell. The equipment “squeaked,” as Doyle called it, updates to a monitor in the Komatsu booth and to Doyle’s Apple watch (see Figure 2). Updates included warnings when welding wire was running low and updates on strokes per minute for the press.
Unlike text messages, the squeaks are archived for future reference. It’s a good resource for those manufacturers that require some level of informal recordkeeping, Doyle said.
IGear Online LLC, 502-423-0999, www.igearonline.com
About the Author
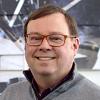
Dan Davis
2135 Point Blvd.
Elgin, IL 60123
815-227-8281
Dan Davis is editor-in-chief of The Fabricator, the industry's most widely circulated metal fabricating magazine, and its sister publications, The Tube & Pipe Journal and The Welder. He has been with the publications since April 2002.
subscribe now
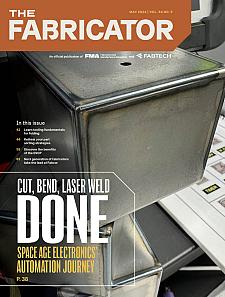
The Fabricator is North America's leading magazine for the metal forming and fabricating industry. The magazine delivers the news, technical articles, and case histories that enable fabricators to do their jobs more efficiently. The Fabricator has served the industry since 1970.
start your free subscription- Stay connected from anywhere
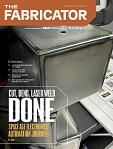
Easily access valuable industry resources now with full access to the digital edition of The Fabricator.
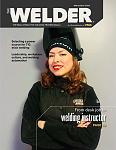
Easily access valuable industry resources now with full access to the digital edition of The Welder.
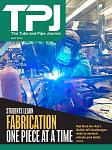
Easily access valuable industry resources now with full access to the digital edition of The Tube and Pipe Journal.
- Podcasting
- Podcast:
- The Fabricator Podcast
- Published:
- 04/16/2024
- Running Time:
- 63:29
In this episode of The Fabricator Podcast, Caleb Chamberlain, co-founder and CEO of OSH Cut, discusses his company’s...
- Industry Events
16th Annual Safety Conference
- April 30 - May 1, 2024
- Elgin,
Pipe and Tube Conference
- May 21 - 22, 2024
- Omaha, NE
World-Class Roll Forming Workshop
- June 5 - 6, 2024
- Louisville, KY
Advanced Laser Application Workshop
- June 25 - 27, 2024
- Novi, MI