- FMA
- The Fabricator
- FABTECH
- Canadian Metalworking
Categories
- Additive Manufacturing
- Aluminum Welding
- Arc Welding
- Assembly and Joining
- Automation and Robotics
- Bending and Forming
- Consumables
- Cutting and Weld Prep
- Electric Vehicles
- En Español
- Finishing
- Hydroforming
- Laser Cutting
- Laser Welding
- Machining
- Manufacturing Software
- Materials Handling
- Metals/Materials
- Oxyfuel Cutting
- Plasma Cutting
- Power Tools
- Punching and Other Holemaking
- Roll Forming
- Safety
- Sawing
- Shearing
- Shop Management
- Testing and Measuring
- Tube and Pipe Fabrication
- Tube and Pipe Production
- Waterjet Cutting
Industry Directory
Webcasts
Podcasts
FAB 40
Advertise
Subscribe
Account Login
Search
Manufacturers in the dark on lighting waste?
Companies waste millions on inefficient lighting
- By Dave Riggle
- January 15, 2008
- Article
- Shop Management
Operating costs can stack up quickly, significantly affecting the bottom line. Simple solutions to cut such costs sometimes are overlooked simply because operators aren't aware of cost-effective measures that could have a noticeable impact on daily operations and expenses. One of those simple solutions is lighting.
Lighting typically is the last line item on the budget operators worry about or assess. Many companies feel as though they have no control over their energy costs, so they never take a critical look at the expenditure. It's just an item on the budget that has to be paid, no matter what the cost. However, such costs can result in millions of dollars of lost revenue each year, not to mention tons of wasted energy and a negative impact on the environment.
Industrial buildings are not designed with lighting efficiency in mind. In fact, the vast majority of manufacturing plants are wasting half of their energy every year using the most common type of lighting—metal halide. Metal halide lights lose 35 percent of their light output during the first year of use. After three years, light output is just 30 percent of the original design.
Even though light output goes down, the energy bills don't. Manufacturers continue to pay the full light bill for less than half the light.
Shining Light on the Situation
The fact is, most manufacturing companies can cut lighting costs by 50 percent to 70 percent each year and have better lighting by switching to energy-efficient lights. The new energy-efficient lights last three times as long—36,000 hours compared to 12,000 hours. This cuts maintenance costs by half.
On top of the savings and improved work environment, companies can capitalize further by taking advantage of the Energy Policy Act of 2005 (EPAct 2005), a federal tax deduction for energy efficiency that applies to lighting upgrades. EPAct 2005 allows energy users to take a one-time federal tax deduction of 60 cents per square foot for upgrading to energy-efficient lighting.
Taking into account only these tax deductions, a company can implement an energy-conscious lighting program rest assured the move will make a positive impact on the bottom line. In addition to the direct monetary savings companies achieve, they simultaneously improve the indoor work environment through better-lit work areas.
Take Atlas Foundry in Marion, Ind., for example. By using energy-efficient lighting and motion sensor controls to turn off or dim lights when areas of the plant are unoccupied, the company gained a $20,400 tax deduction under the EPAct for energy efficiency. Considering the amount of energy saved with the use of more energy-efficient lighting, Atlas Foundry also helped to reduce air pollution by 340,000 pounds a year, or the equivalent of exhause from 578 cars over the next 20 years.
Jim Gartland, Atlas Foundry's president and CEO, said employees appreciate the new lighting and are pleased with an improved work environment.
Steps to Consider
But deciding to take a look at lighting is only the first step in an important process. Many lighting companies and suppliers sell lights. The challenge is that every facility is different, and each has distinct needs and uses for lighting. Therefore, sifting through hundreds of available lighting products to find the right solution for each facility can be time-consuming at best.
If you are considering upgrading lighting and relying on a turnkey supplier, make sure to examine the following:
- The supplier should be versed on the full calculations and total tax preparation documentation required for the EPAct federal tax deduction. This one-time deduction will offset 25 percent of an upgrade cost. The best supplier will design the upgrade so that it qualifies for the deduction. The supplier also will complete all of the paperwork for the deduction, eliminating confusing red tape.
- On-site engineering support should be a prerequisite. With engineers on-site to conduct an energy audit and installation, your facility can achieve a full custom design. This includes the most efficient fixtures for each application, motion sensors to reduce light levels in low-traffic areas of facilities such as warehouses, and on/off control during work to save energy when areas of a facility are unoccupied.
- Financing can be an attractive option.Energy-efficient lighting upgrades generally provide a return on investment within two years of implementation, but most companies still choose to finance them from the energy savings. A supplier that offers financing as part of its services makes it possible for you to implement and realize cost savings immediately without any money out of pocket.
- The supplier should provide hazardous material removal. Old lighting is considered hazardous material and cannot simply be thrown into the trash container. Make sure your energy upgrade includes the removal and disposal of old fixtures.
When deciding whether to upgrade lighting, also consider a full energy audit. This audit should account for all lighting in the building as well as the traffic and work flow on any given day. The audit will provide you with a lighting strategy that outlines an effort to save energy as well as improve operations and safety through quality lighting.
Finally, be sure the lighting upgrade will cause little disruption in operations during the transition. When upgrading lighting, there should be little for you to do other than turn on the lights and save.
About the Author
Dave Riggle
3905 Vincennes Road Suite 303
Indianapolis, IN 46268
317-471-3534
subscribe now
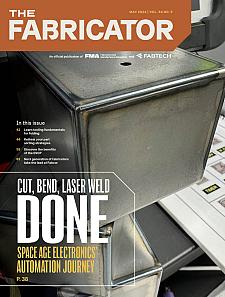
The Fabricator is North America's leading magazine for the metal forming and fabricating industry. The magazine delivers the news, technical articles, and case histories that enable fabricators to do their jobs more efficiently. The Fabricator has served the industry since 1970.
start your free subscription- Stay connected from anywhere
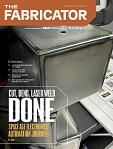
Easily access valuable industry resources now with full access to the digital edition of The Fabricator.
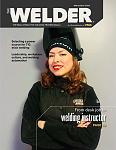
Easily access valuable industry resources now with full access to the digital edition of The Welder.
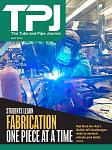
Easily access valuable industry resources now with full access to the digital edition of The Tube and Pipe Journal.
- Podcasting
- Podcast:
- The Fabricator Podcast
- Published:
- 04/16/2024
- Running Time:
- 63:29
In this episode of The Fabricator Podcast, Caleb Chamberlain, co-founder and CEO of OSH Cut, discusses his company’s...
- Trending Articles
Capturing, recording equipment inspection data for FMEA
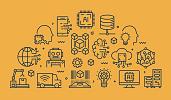
Tips for creating sheet metal tubes with perforations
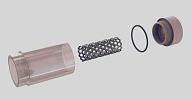
Are two heads better than one in fiber laser cutting?
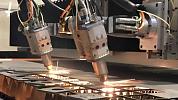
Supporting the metal fabricating industry through FMA
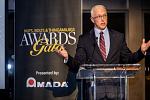
Omco Solar opens second Alabama manufacturing facility
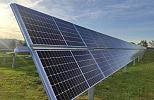
- Industry Events
16th Annual Safety Conference
- April 30 - May 1, 2024
- Elgin,
Pipe and Tube Conference
- May 21 - 22, 2024
- Omaha, NE
World-Class Roll Forming Workshop
- June 5 - 6, 2024
- Louisville, KY
Advanced Laser Application Workshop
- June 25 - 27, 2024
- Novi, MI