- FMA
- The Fabricator
- FABTECH
- Canadian Metalworking
Categories
- Additive Manufacturing
- Aluminum Welding
- Arc Welding
- Assembly and Joining
- Automation and Robotics
- Bending and Forming
- Consumables
- Cutting and Weld Prep
- Electric Vehicles
- En Español
- Finishing
- Hydroforming
- Laser Cutting
- Laser Welding
- Machining
- Manufacturing Software
- Materials Handling
- Metals/Materials
- Oxyfuel Cutting
- Plasma Cutting
- Power Tools
- Punching and Other Holemaking
- Roll Forming
- Safety
- Sawing
- Shearing
- Shop Management
- Testing and Measuring
- Tube and Pipe Fabrication
- Tube and Pipe Production
- Waterjet Cutting
Industry Directory
Webcasts
Podcasts
FAB 40
Advertise
Subscribe
Account Login
Search
Ask the Stamping Expert: Do we really need die safety blocks for die setting?
- By Dennis Cattell
- May 27, 2016
- Article
- Bending and Forming
Q: Are safety blocks really required in a die setting procedure? How does OSHA’s minor servicing exception fit into normal production operations for a job shop that uses continuously running, 100- to 400-ton straight-side presses, both of which are armed with inch modes as well as front and back safety curtains?
A: You must meet OSHA 1910.147 lockout/tagout standards at all times during die setting. Any time you need to put your hands in the die area of a press or you need to work on the die, you must use die safety blocks. This is mandated by the OSHA regulations, and there are no exceptions.
The safety blocks, or jacks, must be fitting with dummy electrical plugs on a metal chain connected securely to each safety block. When you remove the safety blocks from storage and put them into the press or die, you have to remove the plug from the socket in the safety block storage area. That socket is wired to the press’s main motor run control circuit. When the plug is removed from the socket, the circuit is broken, and the main motor cannot run.
Before you go into the die area you must visually confirm that the main motor and flywheel have stopped.
This all takes time and is a troublesome task, but it is absolutely necessary for safety.
The safety blocks are designed for gravitational force to support only the weight of the press slide and the weight of the die. When the flywheel is turning, enough energy is available to crush the safety blocks if the press clutch engages.
Presses fitted with front and rear safety light curtains or guards can run continuously only when the light curtains or guards are operable. If the light curtain is broken or guard opened, the press must stop immediately, not continue and stop on top.
The inch mode must be designed to be a two-handed control function. You must have both hands on the two inch-control buttons to make the press inch over. The two buttons must be set a certain distance apart so that they cannot be operated with just one hand. They also must be arranged electrically so that one button cannot be tied down to make the function take place. If one of the buttons is a switch, it must be spring-loaded to return to the safe mode when released.
Protection also is needed for any other person in the press area when inching, so the front and rear safety curtains or guards must be operable.
Because so many variations of part and die design and so many different circumstances could apply to your 100- to 400-ton presses, I cannot give you a defined answer about OSHA’s minor servicing exception.
I can tell you that OSHA does not require the lockout procedure for minor adjustments or service activities if they are a part of the normal production; if the unexpected energization or start-up of the equipment would not affect the operator’s safety; or employees are provided appropriate protection. At no time should you perform adjustments or service within the point of operation or other hazardous area without taking proper protection measures that meet OSHA and ANSI requirements.
OSHA’s minor servicing exception must not and cannot be used as an excuse to deviate from 1910.147 procedures.
The minor servicing exception for normal and repetitive issues must have written safety procedures documented specifically for that process and authorized by your company and safety department, with training given before the implementation of the process.
I cannot emphasize enough that you must adhere to these procedures to protect everyone in your press shop and your company’s liability.
About the Author
Dennis Cattell
240 W. Fifth St.
Minster, OH 45865
419-628-2331
subscribe now
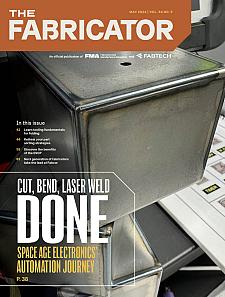
The Fabricator is North America's leading magazine for the metal forming and fabricating industry. The magazine delivers the news, technical articles, and case histories that enable fabricators to do their jobs more efficiently. The Fabricator has served the industry since 1970.
start your free subscription- Stay connected from anywhere
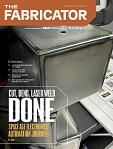
Easily access valuable industry resources now with full access to the digital edition of The Fabricator.
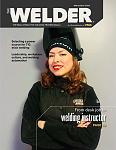
Easily access valuable industry resources now with full access to the digital edition of The Welder.
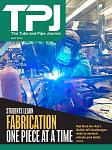
Easily access valuable industry resources now with full access to the digital edition of The Tube and Pipe Journal.
- Podcasting
- Podcast:
- The Fabricator Podcast
- Published:
- 04/16/2024
- Running Time:
- 63:29
In this episode of The Fabricator Podcast, Caleb Chamberlain, co-founder and CEO of OSH Cut, discusses his company’s...
- Trending Articles
Capturing, recording equipment inspection data for FMEA
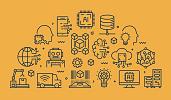
Tips for creating sheet metal tubes with perforations
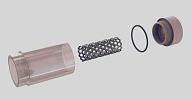
Are two heads better than one in fiber laser cutting?
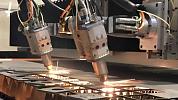
Supporting the metal fabricating industry through FMA
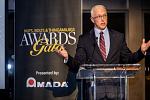
Omco Solar opens second Alabama manufacturing facility
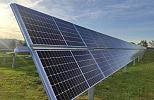
- Industry Events
16th Annual Safety Conference
- April 30 - May 1, 2024
- Elgin,
Pipe and Tube Conference
- May 21 - 22, 2024
- Omaha, NE
World-Class Roll Forming Workshop
- June 5 - 6, 2024
- Louisville, KY
Advanced Laser Application Workshop
- June 25 - 27, 2024
- Novi, MI