- FMA
- The Fabricator
- FABTECH
- Canadian Metalworking
Categories
- Additive Manufacturing
- Aluminum Welding
- Arc Welding
- Assembly and Joining
- Automation and Robotics
- Bending and Forming
- Consumables
- Cutting and Weld Prep
- Electric Vehicles
- En Español
- Finishing
- Hydroforming
- Laser Cutting
- Laser Welding
- Machining
- Manufacturing Software
- Materials Handling
- Metals/Materials
- Oxyfuel Cutting
- Plasma Cutting
- Power Tools
- Punching and Other Holemaking
- Roll Forming
- Safety
- Sawing
- Shearing
- Shop Management
- Testing and Measuring
- Tube and Pipe Fabrication
- Tube and Pipe Production
- Waterjet Cutting
Industry Directory
Webcasts
Podcasts
FAB 40
Advertise
Subscribe
Account Login
Search
Ask the Stamping Expert: How can I avoid die crashes?
- By Dennis Cattell
- May 31, 2016
- Article
- Bending and Forming
Q: I am a die setter and press operator who works with progressive dies that run up to 120 SPM. For die and press protection, we have:
- Strip material location with pilots.
- Pilot protection with limit switches.
- Four double-material-thickness stripper sensors in case of slug pull-up.
- Sensor on the feed roll to detect feed roll start.
- End-of-stock detector at entry to coil straightener.
Even using these precautions, we still get die wrecks. Do you have any suggestions?
A: Ninety-five percent of die wrecks are caused by misfeeds that occur through burrs, steel slivers, or slug pull-ups in the die. Misfeeds happen in the first 2 to 5 degrees of the feed cycle and stop the coil material from progressing through the die.
If this type of misfeed occurs, none of the sensors you have in place will stop the press in time to prevent a die wreck. Your sensors are operating at 135 to 175 degrees of the press cycle. When the punches enter the die on the downstroke, there is no time to stop the press before 180 degrees (bottom dead center).
There is so much power in the feed roll at start-up (torque) that if the material is held up in the die, it will not stop the feed roll from turning. Therefore, it will not give a signal to the press to stop. The material will hump, or buckle up and down, in between the feed roll and the die entry.
The trick is to control the position of the hump and make it always travel in the up direction. This can be done by making a bridge between the feed roll and the die with a solid-bottom rail and a top rail with a gap in the center (see Figure 1). Make sure the gap suits the thickness of the material. The gap can be 4 to 10 in., and the distance between the upper and lower bridge plate should be twice the maximum material thickness.
Trapping the material with the bridge in this manner will amplify the hump so that it always travels up. Now you have a location in which to place a stock buckle detector. This sensor will give you a signal at the beginning of the feed cycle (the first 3 to 10 degrees) or at about 200 degrees of the press cycle. If a hump occurs, it will signal the press to stop. You will have ab bout 320 degrees of the press cycle to stop the press before pilot and punch entry into the die.
You might consider starting a preventive maintenance program for the press clutch and brake to help prevent future problems.
Good luck.
About the Author
Dennis Cattell
240 W. Fifth St.
Minster, OH 45865
419-628-2331
subscribe now
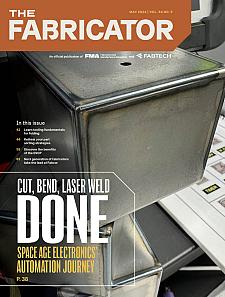
The Fabricator is North America's leading magazine for the metal forming and fabricating industry. The magazine delivers the news, technical articles, and case histories that enable fabricators to do their jobs more efficiently. The Fabricator has served the industry since 1970.
start your free subscription- Stay connected from anywhere
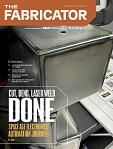
Easily access valuable industry resources now with full access to the digital edition of The Fabricator.
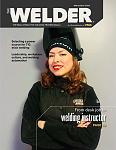
Easily access valuable industry resources now with full access to the digital edition of The Welder.
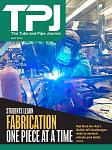
Easily access valuable industry resources now with full access to the digital edition of The Tube and Pipe Journal.
- Podcasting
- Podcast:
- The Fabricator Podcast
- Published:
- 04/16/2024
- Running Time:
- 63:29
In this episode of The Fabricator Podcast, Caleb Chamberlain, co-founder and CEO of OSH Cut, discusses his company’s...
- Trending Articles
Capturing, recording equipment inspection data for FMEA
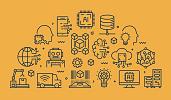
Tips for creating sheet metal tubes with perforations
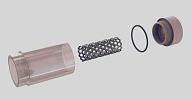
Are two heads better than one in fiber laser cutting?
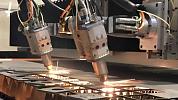
Supporting the metal fabricating industry through FMA
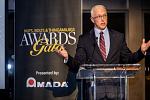
Omco Solar opens second Alabama manufacturing facility
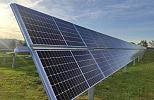
- Industry Events
16th Annual Safety Conference
- April 30 - May 1, 2024
- Elgin,
Pipe and Tube Conference
- May 21 - 22, 2024
- Omaha, NE
World-Class Roll Forming Workshop
- June 5 - 6, 2024
- Louisville, KY
Advanced Laser Application Workshop
- June 25 - 27, 2024
- Novi, MI