Peter Hodgson
- FMA
- The Fabricator
- FABTECH
- Canadian Metalworking
Categories
- Additive Manufacturing
- Aluminum Welding
- Arc Welding
- Assembly and Joining
- Automation and Robotics
- Bending and Forming
- Consumables
- Cutting and Weld Prep
- Electric Vehicles
- En Español
- Finishing
- Hydroforming
- Laser Cutting
- Laser Welding
- Machining
- Manufacturing Software
- Materials Handling
- Metals/Materials
- Oxyfuel Cutting
- Plasma Cutting
- Power Tools
- Punching and Other Holemaking
- Roll Forming
- Safety
- Sawing
- Shearing
- Shop Management
- Testing and Measuring
- Tube and Pipe Fabrication
- Tube and Pipe Production
- Waterjet Cutting
Industry Directory
Webcasts
Podcasts
FAB 40
Advertise
Subscribe
Account Login
Search
Leaving the lab behind: Australian students move stamping research to the plant
- By Michael Cardew-Hall
- April 24, 2001
- Article
- Bending and Forming
Stamping Technology for Automotive Manufacturing Processes (STAMP) is a novel type of research program developed in Australia. The unique aspect of this program is that research is conducted for industry inside actual companies--a radical departure from traditional research, which typically involves experimentation in laboratories. This research model is well-suited to the manufacturing industry, particularly in Australia, where small and medium-size companies are predominant.
The Need for Assistance
STAMP was launched in mid-1997 as a collaborative venture between two Australian universities–The Australian National University and Deakin University--and Ford Motor Company, along with three of its suppliers, BHP Steel Ltd., Castrol Pty Ltd., and Imag Australia. The program was created to address some specific needs of the collaborating partners in the general areas of stamping and sheet metal forming.
As many other stamping professionals throughout the world do, these partners perceived stamping as a black art and believed that problems experienced with new or ongoing parts could be solved only by experts with many years of experience. While this had been the mode of operation for many years at these plants, the continuing need to be efficient and competitive had resulted in the loss of many experienced personnel through downsizing and early retirement.
The black art needed to be replaced by more scientific approaches, and new experts with sound understanding needed to be trained and brought into the industry.
It also was recognized that day-to-day pressures present in stamping operations do not allow long-term projects to be addressed. These projects may have great potential benefit to a plant's operational effectiveness, but they often require extensive background research, experimentation, analysis, and reflection on results–a luxury to busy plant engineers.
When STAMP was initiated, the Ford Stamping Plant in Geelong, Victoria, Australia, was working with a number of separate universities on disparate, sometimes overlapping projects. It was identified that by drawing together the strengths of several institutions and suppliers into a virtual center structure comprising existing industrial and academic facilities, a focused approach could be adopted to meet identified needs. It also provided plant personnel with a single window for access to knowledge and expertise.
The Model
Universities and the stamping industry working together is nothing new. What is novel is the model used within STAMP.
Projects are designed for university research students, who usually are enrolled in two-year Master of Engineering (and occasionally Ph.D.) research degree programs. The length of the projects allows significant problems to be addressed.
The students are in the plant setting for more than 80 percent of their time, working alongside plant personnel. They dress the same as company employees and attend regular operational meetings so that they can better understand the motivations and problems that the plant personnel experience. To maintain the academic nature of their work, students also spend periods of time, either one day a week or longer blocks, at their university campus to read, work on problems using university facilities, or consult academics.
In addition to having an academic supervisor, each student is assigned an industrial supervisor, who typically is a line manager in the plant, and a technical mentor, who helps with the day-to-day facilitation of the project. Both people are key to the success of the students' project. Students meet with their academic supervisors either on the university campus or in the plant. The academics are regular visitors to the plant, spending, on average, one day there every three weeks.
Students have access to production presses to carry out experiments in context, rather than in the abstract in a university laboratory, and findings are likely to yield direct benefits to the operations. In addition to production plants, the students have access to a number of small presses set aside for their use. These have a wider variety of instrumentation and allow students to carry out more fundamental experiments.
The stamping lines and individual presses are considered to be part of the experimental facilities available to the STAMP program. The plant-based experimentation is supported by university-based testing facilities and workshops as needed.
While some projects involve large amounts of experimentation, others focus on the use of computer-aided engineering and manufacturing (CAEM) and finite element modeling methods to improve process understanding and limit problems. Students have access to two UNIX-based engineering workstations located in the Ford plant. These run CAD, CAEM, and metal forming simulation software and are connected via a microwave link to the university network. This link effectively allows a minicampus to exist within the plant.
In addition to the plant-based students, one or two research students work at their university on more long-term projects. They create another avenue of communication for the students in the plant. Further support is provided by a postdoctoral fellow and two research engineers who spend extended periods of time in the plant when projects require them.
Two committees manage the STAMP activities. Both are chaired by senior plant personnel and meet every six weeks:
1. The technical committee is responsible for defining, monitoring, and controlling the projects. It includes some plant personnel, particularly the technical mentors and industrial supervisors, as well as all of the collaborating industrial partners, academics, and students. The projects are identified and scoped by the industrial partners and the academic colleagues. This ensures that a balance is maintained between addressing real problems and academic merit and integrity.
2. The management committee oversees the financial and resource management of the program. It provides guidance on the students' career development beyond the life of their project.
Each year, an independent review of the program's activities is carried out. Each student presents his or her work to an audience of plant personnel, senior academics from the two universities who are not associated with the program, and an eminent professor who has worked extensively in the sheet metal forming area. This group provides an important quality check and critical feedback on the direction and nature of the work being done.
Benefits
At the technical level, this program allows relatively long-term projects to be addressed that normally would be too long for production personnel to be involved in. Because the research is carried out in context, project input and output remain relevant. Researchers are able to understand the limitations of current processes and organizational structures.
Through this program, the partners can attract and retain well-qualified, motivated technical staff within the manufacturing sector. Development and retention of graduates within the partner organizations is a major focus of STAMP, and each student is viewed as a potential employee. Students are recruited through a competitive interview and assessment process. The program attracts both fresh graduates and those who have been in graduate training programs and want a higher degree and more technical work experience in an industrial environment.
A side benefit is that findings and real-world problems can be incorporated into the undergraduate engineering programs at the two universities. Guest speakers now are regularly invited to speak to undergraduate students, providing a knowledge path from industry to the university.
The structure and organization of the program have created a multidisciplinary team. There is an open environment for the discussion of ideas and problems. This is partly due to the individuals involved, but also to the high level of commitment shown by the participating companies and universities.
Specific Outcomes
Each project has three outcome measures:
1. Improvement in process/increase in technical knowledge base in the plant. This is a key outcome. Each thesis generated by the students must have an appendix of how the results will be adopted by the industry partner. Projects completed to date have reduced lubricant and die coating costs, increased practical understanding of forming bake-hardenable steels, enabled viewing of the deep-drawing process as a system, and more.
2. New employees. To date, all of the graduates either have been employed by the partner companies or have gone to supplier organizations upon completion of their projects.
3. Publication of academic works. The industrial partners recognize the academic partners' need to publish scholarly articles. Much of the work that is not of a sensitive nature has been published in international journals or presented at conferences. In addition to being presented at public conferences, the work carried out within STAMP is regularly reported to the industrial partners' global headquarters in the U.S. through various technical stamping forums.
![]() |
Figure 1 One significant project result has been the development of a knowledge capture and dissemination system called Simpress, which initially was developed by research engineers in conjunction with the student projects as a way to use project outcomes as useful tools in the plant. |
While project results have significantly improved understanding of the stamping process in the plant, the most significant outcome has been the development of a knowledge capture and dissemination system called Simpress. This system initially was developed by research engineers in conjunction with the student projects as a way to use project results as useful tools in the plant (see Figure 1).
Developed in close cooperation with staff and students in the plant, the system now forms the basis of a wider knowledge-capture system for stamping operations. It has been designed to allow knowledge and methods from student projects to be incorporated in a modular fashion.
About the Author
subscribe now
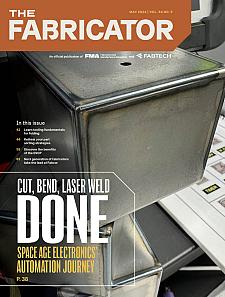
The Fabricator is North America's leading magazine for the metal forming and fabricating industry. The magazine delivers the news, technical articles, and case histories that enable fabricators to do their jobs more efficiently. The Fabricator has served the industry since 1970.
start your free subscription- Stay connected from anywhere
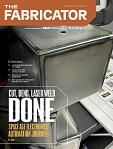
Easily access valuable industry resources now with full access to the digital edition of The Fabricator.
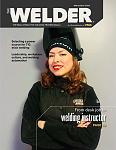
Easily access valuable industry resources now with full access to the digital edition of The Welder.
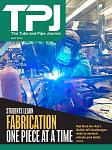
Easily access valuable industry resources now with full access to the digital edition of The Tube and Pipe Journal.
- Podcasting
- Podcast:
- The Fabricator Podcast
- Published:
- 04/16/2024
- Running Time:
- 63:29
In this episode of The Fabricator Podcast, Caleb Chamberlain, co-founder and CEO of OSH Cut, discusses his company’s...
- Trending Articles
Capturing, recording equipment inspection data for FMEA
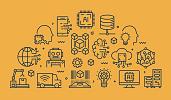
Tips for creating sheet metal tubes with perforations
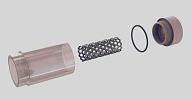
Are two heads better than one in fiber laser cutting?
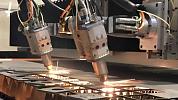
Supporting the metal fabricating industry through FMA
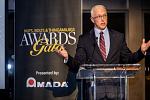
Omco Solar opens second Alabama manufacturing facility
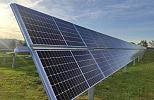
- Industry Events
16th Annual Safety Conference
- April 30 - May 1, 2024
- Elgin,
Pipe and Tube Conference
- May 21 - 22, 2024
- Omaha, NE
World-Class Roll Forming Workshop
- June 5 - 6, 2024
- Louisville, KY
Advanced Laser Application Workshop
- June 25 - 27, 2024
- Novi, MI