Sales and Marketing Manager for Automation Division
- FMA
- The Fabricator
- FABTECH
- Canadian Metalworking
Categories
- Additive Manufacturing
- Aluminum Welding
- Arc Welding
- Assembly and Joining
- Automation and Robotics
- Bending and Forming
- Consumables
- Cutting and Weld Prep
- Electric Vehicles
- En Español
- Finishing
- Hydroforming
- Laser Cutting
- Laser Welding
- Machining
- Manufacturing Software
- Materials Handling
- Metals/Materials
- Oxyfuel Cutting
- Plasma Cutting
- Power Tools
- Punching and Other Holemaking
- Roll Forming
- Safety
- Sawing
- Shearing
- Shop Management
- Testing and Measuring
- Tube and Pipe Fabrication
- Tube and Pipe Production
- Waterjet Cutting
Industry Directory
Webcasts
Podcasts
FAB 40
Advertise
Subscribe
Account Login
Search
Zigzagging your way to material savings
Multi-out results using one-out die
- By Robert Allred i
- October 8, 2015
- Article
- Bending and Forming
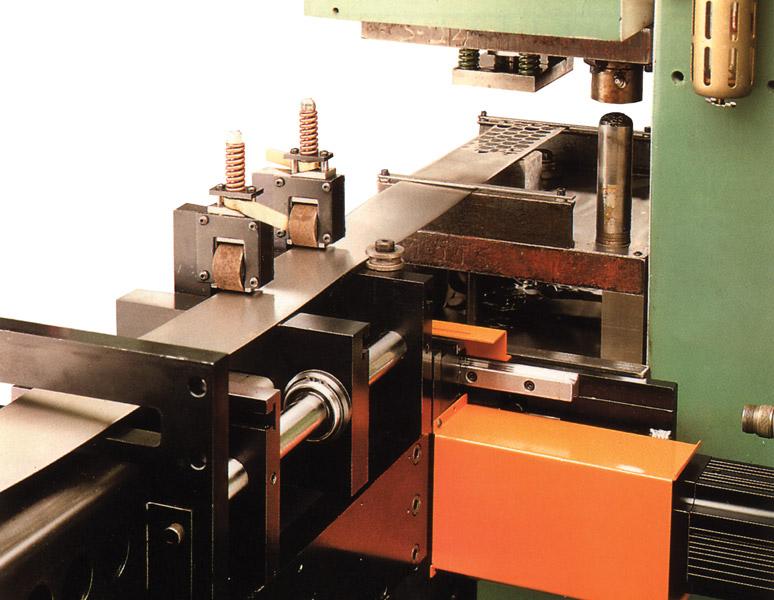
Using a zigzag feeder allows stampers to maximize material utilization and achieve multi-out results with a one-out die.
Although many variations of zigzag press feeds are available, the basic concept is the same: Material is fed into a press in a simultaneous X-Y movement pattern for a staggered part production and optimal part-to-scrap yields (see Figure 1).
But there’s more to zigzag feeds than just scrap reduction.
When first presented with the idea of a zigzag feed, many manufacturers ask, “Why not build a multiple-out tool?” In any application there are many unique factors to consider, but often a zigzag feed can offer several unique advantages.
Typically, a high-tonnage press—with the accompanying higher cost—is required for multi-out dies with multiple punches. Likewise, the multi-out tooling itself is more expensive than simple single-out tools. Stamping manufacturers can achieve the same results of a multi-out die without purchasing a high-tonnage press or large multi-out dies.
In transfer press applications where only one part can be generated per stroke and that single part is moved through the stations, multi-out dies cannot be used. Zigzagging the material may be able to reduce the web, or space, between parts and use more of the material than a multi-out die can.
Scrap generated from the space between parts in the skeleton can be reduced to a rule-of-thumb minimum of 1.5 times the material thickness. Some stampers reduce the space between parts even more by butting the cuts (see Figure 2).
The obvious savings is in material. By nesting the parts together, stampers can save 6 to 7 percent when going from a one-out to a two-out, on average, and around 11 to 12 percent when going from a one-out to a three-out.
More Material Savings
There are other sources of savings by going to a zigzag system instead of positioning one part behind the other in a one-out pattern.
Consolidate Material Widths. If stampers can nest the material close together, they may also be able to reduce the overall material width. This will yield a significant savings above and beyond the savings from nesting.
Reduce Cycle Time. Staggering four parts across a wider width of material with a zigzag feed reduces the run time per coil significantly compared to a linear one-out part arrangement. In the same press running at the same speed, the zigzag feed will yield more parts per coil with a quarter of the coil changeovers.
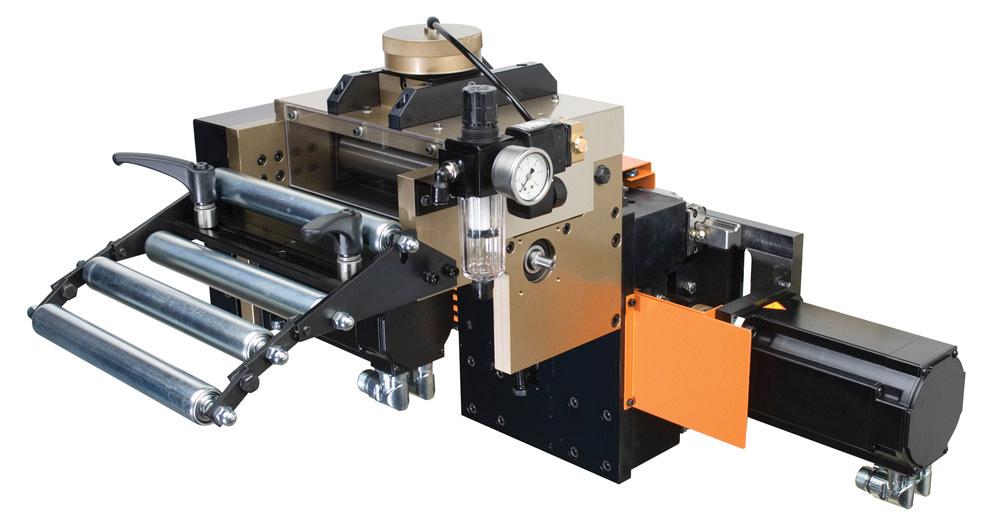
Figure 1
Zigzag feeders feed coil material into a press in a simultaneous X-Y movement for a staggered
part production.
Some advanced zigzag feeds have software that automatically calculates the optimal material pattern for a given width of material (see Figure 3). For some stamping manufacturers, such as those making washers, that presents another savings opportunity.
The auto calculation software can determine the number of parts that can be made from a given material width based on the diameter and thickness of the web. Although this may not give the best yield for each part singularly, overall, the cost may be offset by not having to stock so many widths. For example, a manufacturer consolidating the number of coils of different widths and thicknesses in stock from 80 to 10 would realize cost savings by not having to keep so many coils in inventory.
If the material shifts out of position, advanced zigzag software can reposition a pattern on-the-fly. The software also stores production parameters for easy recall and setup for job-to-job switching.
Many types of zigzag feeds are available, including mechanical, pneumatic, servo hitch, and high-speed servo roll feeds. They can feed the material horizontally or vertically and can be incorporated into integrated compact coil lines.
A compact feeder-straightener-reel line can be configured so that the pivoting system’s pivot point is underneath the reel so that the whole line pivots back and forth to create the zigzag pattern. This is beneficial for thick material because it eliminates the need for a long loop between the straightener and feed, which reduces its footprint.
A relatively new manufacturing concept is the compact zigzag cutting system, which can cut costs on low-budget, low-volume projects. This comprises a compact feeder-straightener-reel line with a circular cutting system. The cutting unit is integrated with the compact line to provide a zigzag pattern that does not require a press to cut the blank. Parts or blanks can be cut on the system.
The circular cutting blades are adjustable for varying diameters. The cutter moves in the Y axis to shift from one side of the coil to the other side, while the compact line moves on the X axis, resulting in a standard, equilateral zigzag pattern. This eliminates the need for expensive hard tooling and for low-volume producers the need for a high-tonnage press to cut these blanks.
Features to Look For
Zigzag feeds create a lot of possibilities for cost savings. Stampers need to determine the specific solution that works best for the application (see Figure 4). A few key features they should look for when considering the purchase of a zigzag system are:
- Simple parameter entry and zigzag-specific software. With the proper software, all the X and Y parameter moves are calculated within the servo feed software. This eliminates the need for the operator to calculate the independent moves.
- X and Y simultaneous movement for high-speed applications.
- Options for parameter entry. One option is to enter the part diameter, web width (scrap), and the number of columns or number of part-outs (two-out, three-out, four-out). Another option is to enter the part diameter, web width, and material width. With the latter system, the software calculates the number of parts that can be made out of the material width entered. On rush orders, the exact material width for the best yield may not be in stock, but a width that gets close probably is.
- Ability to enter the X and Y movements independently to run odd-shaped parts such as rectangles and squares.
- On-the-fly adjustment of the web width so that an operator can increase or decrease it while the machine is running to minimize scrap.
- On-the-fly adjustment of the entire pattern so it can be shifted on-the-fly to stay centered on the strip.
- A control equipped with an industrial modem to allow remote access and analysis for troubleshooting and software updates. This can be accessed via a phone line or Ethernet.
- Portable storage with backup capabilities to hold all programs on the control so that if a program is lost or a failure occurs, a new control can be installed.
For the most part, zigzag feeds are compact and easy to mount and retrofit. It’s a good idea for stampers to investigate the options and features available for the application to find a system that saves time, reduces scrap, and saves money.
About the Author
Robert Allred i
240 W. Fifth St.
Minster, Ohio 45865
419-628-2331
subscribe now
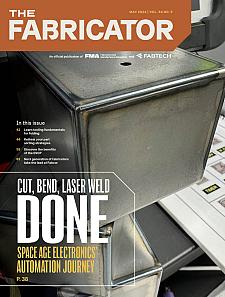
The Fabricator is North America's leading magazine for the metal forming and fabricating industry. The magazine delivers the news, technical articles, and case histories that enable fabricators to do their jobs more efficiently. The Fabricator has served the industry since 1970.
start your free subscription- Stay connected from anywhere
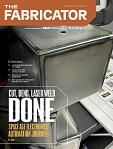
Easily access valuable industry resources now with full access to the digital edition of The Fabricator.
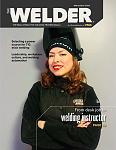
Easily access valuable industry resources now with full access to the digital edition of The Welder.
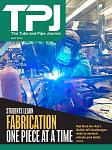
Easily access valuable industry resources now with full access to the digital edition of The Tube and Pipe Journal.
- Podcasting
- Podcast:
- The Fabricator Podcast
- Published:
- 04/16/2024
- Running Time:
- 63:29
In this episode of The Fabricator Podcast, Caleb Chamberlain, co-founder and CEO of OSH Cut, discusses his company’s...
- Trending Articles
Capturing, recording equipment inspection data for FMEA
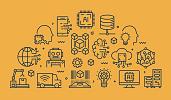
Tips for creating sheet metal tubes with perforations
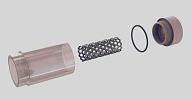
Are two heads better than one in fiber laser cutting?
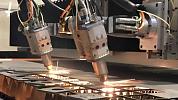
Supporting the metal fabricating industry through FMA
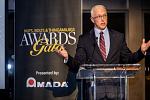
Omco Solar opens second Alabama manufacturing facility
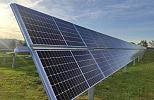
- Industry Events
16th Annual Safety Conference
- April 30 - May 1, 2024
- Elgin,
Pipe and Tube Conference
- May 21 - 22, 2024
- Omaha, NE
World-Class Roll Forming Workshop
- June 5 - 6, 2024
- Louisville, KY
Advanced Laser Application Workshop
- June 25 - 27, 2024
- Novi, MI