- FMA
- The Fabricator
- FABTECH
- Canadian Metalworking
Categories
- Additive Manufacturing
- Aluminum Welding
- Arc Welding
- Assembly and Joining
- Automation and Robotics
- Bending and Forming
- Consumables
- Cutting and Weld Prep
- Electric Vehicles
- En Español
- Finishing
- Hydroforming
- Laser Cutting
- Laser Welding
- Machining
- Manufacturing Software
- Materials Handling
- Metals/Materials
- Oxyfuel Cutting
- Plasma Cutting
- Power Tools
- Punching and Other Holemaking
- Roll Forming
- Safety
- Sawing
- Shearing
- Shop Management
- Testing and Measuring
- Tube and Pipe Fabrication
- Tube and Pipe Production
- Waterjet Cutting
Industry Directory
Webcasts
Podcasts
FAB 40
Advertise
Subscribe
Account Login
Search
Civil War re-enactors take aim at metal fabrication
Welding students turn a school bus into a cannon transporter
- By Eric Lundin
- August 31, 2016
- Article
- Tube and Pipe Fabrication
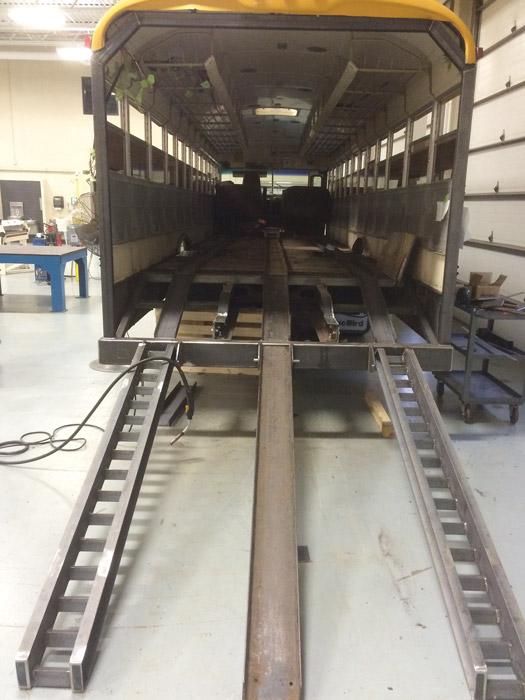
Figure 1
After removing the floor, the student team created a new bumper that would act as an anchoring point for the ramps and the door. Because the new bumper is much lower than the original bumper, the ramps are short and light, and therefore easy to handle.
It has been more than 150 years since the Civil War ended, but it hasn’t been relegated to the history books just yet. Every summer it comes back to life as Civil War re-enactors don replica uniforms and stage mock battles throughout many Union and Confederate states.
Visitors get to tour encampments and see mock battles, getting a sense of the hardships of war, but much more happens behind the scenes. The members of Battery G, 2nd Illinois Light Artillery have two cannons and many miles to cover. For years they used a modified school bus, but when the time came to replace it, they sought an improved design. They enlisted the help of staff and students at Blackhawk Technical College (BTC), Janesville, Wis., for the design and fabrication.
Two BTC welding instructors, Mark Prosser and Jeremiah Johnson, worked with a select group of students to turn an ordinary school bus into a cannon transporter.
Hundreds of Battles, Hundreds of Miles
The task sounded straightforward. The bus’s dimensions, horsepower, and payload capacity were enough to handle two cannons and two limbers (the boxes used to store gunpowder and ammunition). The Civil War re-enactors just needed a system for getting the cannons in (using the 8,000-pound winch from their previous bus) and out (using muscle power).
Still, a bus has a few drawbacks for such an application. First, an unladen school bus is pitched.
“When the bus is empty, the back end sits higher than the front end,” Prosser said. “They’re designed this way so they sit closer to level when they’re full.” Lowering the back end would be ideal, reducing the ramp angle and thus the effort required to haul the cannons into the bus. Second, a school bus floor—a layer of plywood over a layer of sheet metal—isn’t intended for this sort of heavy-duty application. Third, a bus floor is flat except for the housings that cover the rear wheels. As luck wouldn’t have it, a bus’s track and a cannon’s track match, so the cannon wheels have to go over the bus’s wheel housings (tubs). The members of Battery G had used ramps to get the cannons up and over the tubs in the original bus, but even so, it wasn’t an easy task.
A Plan on Wheels. The project, which the students undertook in addition to the regular coursework, took about nine months.
“We’d go out and look at the bus, and we’d talk about making ramps, and the advantages and disadvantages of securing them with pins, and eventually we’d make a decision,” Prosser said. Later they’d discuss another component, and under the guidance of Prosser and Johnson, they worked through factors such as strength, ease of use (disassembly and assembly, if needed), and where and how to stow or store components when not in use. So it went, establishing a concept for each component, and eventually a plan emerged. It consisted of countless discussions and a thousand decisions, but three main points formed the essence of the project:
The original door would have to go (see Figure 1). The team would fabricate a pair of custom-made, barn-type doors that would span the bus’s width.
The floor behind the rear wheels would be rebuilt with a downward pitch, lowering the rear bumper by 20 in. or so (see Figure 2).
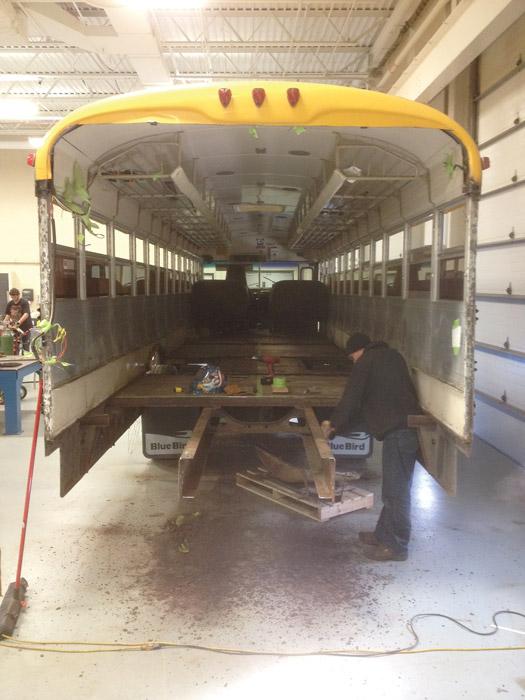
Figure 2
After cutting off the back end of the bus and removing the floor, the student fabricators were ready to begin the assembly phase of the project.
Getting the cannons up and over the wheel tubs wasn’t the only option. The members of Battery G were more than a little dazzled when the BTC team showed them the new removable wheel tubs. Remove two bolts, remove the wheel tubs, pin two ramps into place, and presto! The cannons roll right in.
The key component turned out to be the rear bumper. Robust and sturdy, it keeps the tail end of the bus in good alignment, true and square, which in turn allows the doors to open and close without binding. It’s also the main point of strength for the ramps and 3,000 lbs. of cannon at a time.
In return for all the labor, Battery G made a generous donation to BTC’s student chapter of the American Welding Society, which is organized and overseen by welding instructors Dan Crifase and Bobbi Jo Bishofberger. Donations enable the chapter to fund field trips, cookouts, and recruiting events, but this isn’t all that they gained from the Battery G project. The instructors and the students also gained something that can’t be measured: experience that comes from working on a real-world project.
“It’s the best way to learn this trade,” Prosser said.
Blackhawk Technical College, 608-758-6900, www.blackhawk.edu
About the Author
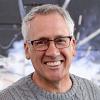
Eric Lundin
2135 Point Blvd
Elgin, IL 60123
815-227-8262
Eric Lundin worked on The Tube & Pipe Journal from 2000 to 2022.
subscribe now
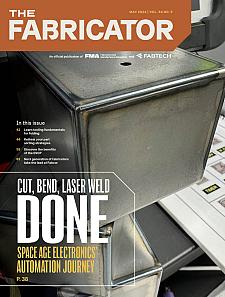
The Fabricator is North America's leading magazine for the metal forming and fabricating industry. The magazine delivers the news, technical articles, and case histories that enable fabricators to do their jobs more efficiently. The Fabricator has served the industry since 1970.
start your free subscription- Stay connected from anywhere
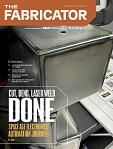
Easily access valuable industry resources now with full access to the digital edition of The Fabricator.
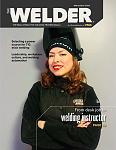
Easily access valuable industry resources now with full access to the digital edition of The Welder.
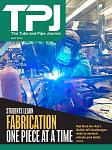
Easily access valuable industry resources now with full access to the digital edition of The Tube and Pipe Journal.
- Podcasting
- Podcast:
- The Fabricator Podcast
- Published:
- 04/16/2024
- Running Time:
- 63:29
In this episode of The Fabricator Podcast, Caleb Chamberlain, co-founder and CEO of OSH Cut, discusses his company’s...
- Trending Articles
Capturing, recording equipment inspection data for FMEA
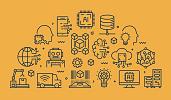
Tips for creating sheet metal tubes with perforations
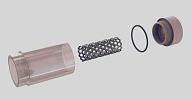
Are two heads better than one in fiber laser cutting?
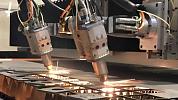
Supporting the metal fabricating industry through FMA
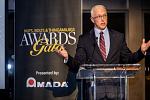
Omco Solar opens second Alabama manufacturing facility
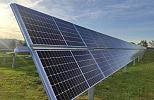
- Industry Events
16th Annual Safety Conference
- April 30 - May 1, 2024
- Elgin,
Pipe and Tube Conference
- May 21 - 22, 2024
- Omaha, NE
World-Class Roll Forming Workshop
- June 5 - 6, 2024
- Louisville, KY
Advanced Laser Application Workshop
- June 25 - 27, 2024
- Novi, MI