- FMA
- The Fabricator
- FABTECH
- Canadian Metalworking
Categories
- Additive Manufacturing
- Aluminum Welding
- Arc Welding
- Assembly and Joining
- Automation and Robotics
- Bending and Forming
- Consumables
- Cutting and Weld Prep
- Electric Vehicles
- En Español
- Finishing
- Hydroforming
- Laser Cutting
- Laser Welding
- Machining
- Manufacturing Software
- Materials Handling
- Metals/Materials
- Oxyfuel Cutting
- Plasma Cutting
- Power Tools
- Punching and Other Holemaking
- Roll Forming
- Safety
- Sawing
- Shearing
- Shop Management
- Testing and Measuring
- Tube and Pipe Fabrication
- Tube and Pipe Production
- Waterjet Cutting
Industry Directory
Webcasts
Podcasts
FAB 40
Advertise
Subscribe
Account Login
Search
Keeping it together at 330 MPH
Strong tubing, strong welds keep top fuel cars in one piece at top speed
- By Eric Lundin
- June 29, 2015
- Article
- Tube and Pipe Fabrication
Since auto racing debuted more than a century ago, the sport has splintered into dozens of types of races and a multitude of specialized cars. The earliest races were little more than publicity stunts for auto manufacturers to showcase the speed and, perhaps more importantly, the durability of production cars. Even today some competitions feature cars that are essentially street legal, such as the grand touring cars used in the 24 Hours of Le Mans and its many 24-hour offshoots. The NASCAR® series cars are further removed from street vehicles, and when you get to the low-slung, open-wheel cars raced in Formula One®, Formula Atlantic, and IndyCar® series races, the vehicles obviously were designed and built for the track.
And then there’s top fuel. Beyond having an engine and four tires, these cars have little in common with any other type of car. An exercise in simplicity, the top fuel category has a handful of safety features, but nearly everything else contributes to getting from point A to point B in the shortest time possible. It doesn’t have a suspension, and it isn’t built for cornering or even steering much. The drivetrain is a direct-drive system, so the driver doesn’t shift. The air/fuel mixture pulls heat from the engine, so the block doesn’t have a water jacket and the car isn’t equipped with a radiator. At about 20 gallons, the fuel tank holds just enough fuel for a few moments to warm the engine, one burnout to heat the tires, and one pass down the track in which the car will cover 1,000 feet in a little more than 3 seconds. Propelled by large amounts of nitromethane pressurized by a no-nonsense supercharger, its engine develops approximately 10,000 horsepower. A top fuel race is a dazzling sight, especially at night when it’s easy to see the unspent fuel that turns into 3-ft. flames shooting from the exhaust headers.
Top fuel cars have one more thing that sets them apart from production cars, and it might be the most important component of all: the chassis.
Chassis Design 101
Every race car frame must be rigid, but not too rigid; likewise, it must be flexible, but not too flexible. The frame’s designers and builders focus their efforts on finding the sweet spot, the combination of rigidity and flexibility that prevents the engine from tearing itself out of the chassis and keeps all the other parts together as it accelerates about 100 MPH for every second of the race.
Don Schumacher Racing (DSR) wins races—lots of them—in part because its fabrication team knows how to build some of the best frames in the industry. Its experience goes back to 1963 when Schumacher started racing street cars in Gary, Ind. Eventually a funny car driver and team owner, he retired in 1974 after winning countless races, 11 national titles, and nine international titles.
DSR fortifies Schumacher’s considerable experience with a variety of technologies, at times sophisticated, like finite element analysis software, and at other times somewhat basic, such as a manual tube bender. A manual bender might seem out of place in such a high-stakes application, but there is little doubt that the team has found a perfect combination of technologies. One of DSR’s most recognized drivers, Don’s son Tony, is the most decorated dragster pilot in modern times.
Stresses and Strains. Most fabricated products are subjected to one stress or another, but the stresses in top fuel racing are extraordinary. The drivetrain accelerates the car at about 4 times the force of gravity (G), a force that comes from the back of the car; at the front end of the car sits a storage compartment with about 100 lbs. of fuel, a pair of tires, and some steering components. Between the two are lengths of seamless AISI 4130 chrome-moly tubing, and they’re robust, but not terribly so.
When the light turns green and the driver punches the accelerator, the car’s motion turns into a debate between acceleration and inertia. The force of acceleration at the rear of the car is in favor of forward motion, and it’s in a big hurry; inertia, a force stored in the mass of the fuel, the front wheels, and the steering hardware at the front end, would like to stay put. The mediator in this debate is the chassis, and it’s made from lengths of 0.049-, 0.058-, and 0.095-in.-thick tubing.
“The chassis material is thinner than most people realize,” said Joe Fitzpatrick, fabrication supervisor at DSR.
In traditional debates, the mediator isn’t supposed to get involved, but in this case it has no choice. The acceleration puts the tubes that run along the bottom of the chassis in tension and the ones along the top in compression. The chassis reacts by flexing, just a little bit, thereby absorbing some of the force and transferring some of the weight from front to back. This gives the tires more traction, which is augmented by about 1,000 lbs. of downforce developed by the exhaust headers. The additional traction helps to develop more acceleration, which causes more chassis flexing, until the forces of acceleration get the upper hand and the mass at the front of the car gives in and reluctantly goes along for the ride.
Another force, one that is speed-dependent, develops as the dragster moves down the track. At the start of the race, the airfoil does next to nothing; by the time the car reaches its top speed, it adds a mind-boggling 12,000 lbs. of downforce to the rear of the car.
It’s not over yet. Shortly after the racing platform crosses the finish line, the driver releases the drag chute. The result, a rapid deceleration, tries to tear the chassis apart with -5 G.
Design and Build. A chassis for a top fuel car uses quite a bit of tubing. The wheelbase for a funny car measures 125 in. A dragster is more than twice that long at 300 in. Tubing also forms the cockpit and roll cage. Although a rollover is a rare event, a sturdy roll cage is a necessity because occasionally something goes horribly wrong and a car tumbles down the track end-over-end.
Despite the large amount of tubing that goes into a frame, the assembly process runs like clockwork in DSR’s fabrication shop.
“Components for the entire car are drawn and stored as CAD files,” Fitzpatrick said. “To make a frame, we use a build book that lists every tube.” Preparation starts with cutting every tube to length. Some tubes are notched so they join at intersections; others are flared so one tube end fits inside the other. Nearly all of them are installed straight, but a few get bent.
Although every dragster chassis is similar, chassis design is not a one-size-fits-all proposition. Each car is tailor-made to the specific driver. The differences aren’t much, but matching the cockpit’s dimensions to the driver’s height is an important part of good design. At DSR, this means accommodating drivers from 5 ft. 8 in. to 6 ft. 2 in. tall.
Much of the assembly takes place in a huge billet jig that serves as a fixture and a go/no-go gauge. The jig and assorted additional fixtures help to reduce, if not eliminate, variations from one dragster frame to the next.
“Our fixturing is overkill, but I’m not here to save money on fixtures. I’m here to win championships,” Fitzpatrick said.
Two welders work on each frame, one for the right-hand side and one for the left. Ideally, every welder has similar training and experience and identical technique, but it would be impossible to eliminate the small differences in method that two people inevitably have. Some use a little more filler metal, some use a little less; some work a little slower and some a little faster; and other differences crop up. Fitzpatrick knows this and therefore doesn’t focus on eliminating these subtle differences but instead pairs welders who have similar techniques.
“I have welded the right side of every dragster since I started working here,” Fitzpatrick said. His current left-hand man isn’t the most experienced, but the most similar.
Pairing like welders isn’t the only strategy DSR uses for weld consistency. The fabrication team also uses a metal axis pulsator, which imparts a small-amplitude, high-frequency vibration into the workpiece. When used during the welding process, it agitates the weld puddle, which leads to a more uniform grain structure. The result is a weld that is less prone to distortion and cracking.
Still, despite all of the attention that goes into choosing the material, the filler metal, and the welders’ technique, the frames don’t last forever. Good chassis design strikes a balance between durability and weight. A heavier frame is a more durable frame, but heavy cars don’t win races. Racing teams strive to make frames that are strong enough to race and light enough to win.
“We get about 20 or 25 runs on a funny car frame before it needs work,” Fitzpatrick said. “A dragster frame lasts about 70 runs.” The team doesn’t use a laser to measure deflection or sophisticated mathematics to determine how much strain the chassis has endured. It’s much simpler than that, a matter of a racing team’s common sense more than a college graduate’s engineering expertise.
“We replace the front end when the tubes start to sag,” Fitzpatrick said.
Whether building or rebuilding, the company relies on Lincoln Electric welding equipment. Its main machine in the fabrication shop is a Precision TIG® 275, which Fitzpatrick credits for its versatility.
“It’s a great all-around welder,” Fitzpatrick said. “It’s good for titanium, chrome-moly, and aluminum, and it delivers enough current for heavy-wall material.” It uses Micro-Start® II technology, which improves arc starts and arc stability, contributing to precision welds, according to Lincoln. The unit delivers 2 to 340 amps for shielded metal arc welding (SMAW) or gas tungsten arc welding (GTAW).
The company also uses Lincoln’s Invertec® V311-T, but this is a completely different animal. It has 16 user-selectable parameters, including the frequency, AC balance, and the waveform (sine, square, and triangular). It is intended for experienced welders to tailor the weld to the application.
“It’s not a beginner’s welder,” Fitzpatrick said.
Finally, DSR uses a an Invertec V-205-T for trackside repairs. A portable unit, it handles both GTAW and SMAW and delivers up to 200 amps. Although DSR generally uses the square waveform, it is capable of sinusoidal and triangular waveforms.
The company relies on Lincoln’s ER-80 filler metal, which provides 80,000 PSI of tensile strength and has characteristics that make it well-suited to racing.
The pulsator is Bonal Technologies’ Meta-Lax® system. When used during the welding process, the fine vibrations agitate the weld puddle and lead to a finer, more uniform weld grain structure, according to Bonal. The intention is to improve the weld’s mechanical properties and ultimate fatigue life. Bonal claims that the technology can improve weld ductility by 400 percent.
Bad Vibrations. The torque developed by the engine and the stresses that develop from the rapid acceleration and deceleration aren’t the only forces that act on the car’s chassis. Another is the resonant frequency, the frequency at which vibrations induced into the chassis develop maximum amplitude.
The old television ad that showed jazz singer Ella Fitzgerald shattering a wine glass with her voice wasn’t a joke. By matching the glass’s resonant frequency, a trained singer can cause glass to fail. Likewise, every mechanical system, whether it’s a bridge, a building, or a dragster chassis, has a resonant frequency. As long as the system’s resonant frequency doesn’t match the most likely frequencies it will encounter, the vibrations will be minimal and the system will be stable. While the shaking from resonant frequencies puts a lot of stress on the welds, chassis builders have another reason to minimize them.
“Vibration is a waste of energy,” Fitzpatrick said.
Isolating the engine from the chassis would be a good start, but this isn’t practical, so DSR relies on a three-part strategy to improve its understanding of the vibrations that develop and improve its strategies to dampen the worst of them. FEA modeling, strain gauges, and working with a consultant have yielded quite a bit of information on frequencies to avoid.
Its research has revealed that the window in which a resonant frequency wreaks havoc is very small. For example, a frame is essentially still when subjected to vibrations at 13 cycles per second (hertz, Hz) and 17 Hz, vibrates noticeably at 14 Hz and 16 Hz, and shakes violently at 15 Hz.
The chassis design and build cycle doesn’t end when the last weld cools.
It ends when the chassis has been tested, the resonant frequency has been determined, and the team has made some modifications to help dampen the worst of the vibrations.
Nitromethane Unleashed
Carbon, hydrogen, nitrogen, and oxygen are some of the most abundant elements on earth. When combined as CH3NO2, they form nitromethane, an elixir used in engines as varied as radio-controlled airplanes and, of course, top fuel cars. It’s a precious compound, typically priced at $65 to $70 per gallon.
Surprisingly, a gallon of nitromethane provides less energy than a gallon of gasoline. Nitromethane works well as a racing fuel because it needs very little oxygen to react. A gasoline-powered engine actually takes in much more air than gasoline, burning a mist that has an air-to-fuel mixture of 14.7-to-1. An engine running on nitromethane moves a lot more fuel, burning an air-to-fuel mixture of 1.7-to-1. In other words, a nitromethane engine doesn’t waste a lot of cylinder space on air. Although every gallon of nitromethane has about 25 percent of the energy of gasoline, every cylinder stroke burns more than eight times as much fuel, providing a terrific amount of horsepower. It’s so much horsepower that it can’t be measured directly, at least not using a standard dynamometer. Building a custom dyno with this much capacity would be cost-prohibitive, so racers rely on estimating the horsepower. They do know that it’s enough to push the engine to the edge of self-destruction near the end of a typical 1,000-ft. run.
Behind the scenes and between races, the DSR crews rarely get a chance to rest. Even when everything is going smoothly—a rarity—they’re busy tracking weather conditions as they change throughout the day.
“As the weather changes, we need to change the fuel content,” Fitzpatrick said. “We change the amount of blower overdrive and the compression ratio because a lot can change between a qualifying run at 3:00 p.m. and a race at 8:00 p.m.
Of course, the star of the show is the driver. Some of the key attributes are lightning-fast reflexes, a taste for danger, and the willingness to ride a 10,000-HP thoroughbred in a 3-second race during which literally anything can happen. Engines have exploded, tires have burst, and, yes, frames have snapped in half. All are expected but none are easy to handle.
Among all of the drivers to ever rise to the challenge—those few brave souls who have attempted to maintain a smidgeon of control over a racing platform that defies all attempts at control—the Schumacher name is destined to remain high-profile for decades to come. Don Schumacher won too many races to count and instituted many safety features during his career, and his team has continued to introduce new ones as his son’s career has unfolded. Tony Schumacher’s winning record and intense personality have earned him a loyal following among fans and unfailing respect among other drivers.
That said, the unsung hero of the sport is hidden beneath the body panels, holding everything together through 4 Gs of acceleration, a top speed of 300 MPH, and -5 Gs of deceleration.
About the Author
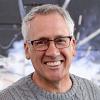
Eric Lundin
2135 Point Blvd
Elgin, IL 60123
815-227-8262
Eric Lundin worked on The Tube & Pipe Journal from 2000 to 2022.
About the Publication
subscribe now
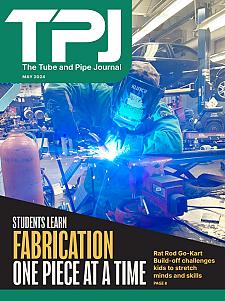
The Tube and Pipe Journal became the first magazine dedicated to serving the metal tube and pipe industry in 1990. Today, it remains the only North American publication devoted to this industry, and it has become the most trusted source of information for tube and pipe professionals.
start your free subscription- Stay connected from anywhere
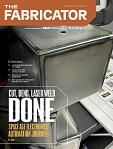
Easily access valuable industry resources now with full access to the digital edition of The Fabricator.
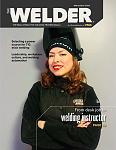
Easily access valuable industry resources now with full access to the digital edition of The Welder.
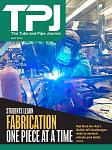
Easily access valuable industry resources now with full access to the digital edition of The Tube and Pipe Journal.
- Podcasting
- Podcast:
- The Fabricator Podcast
- Published:
- 04/30/2024
- Running Time:
- 53:00
Seth Feldman of Iowa-based Wertzbaugher Services joins The Fabricator Podcast to offer his take as a Gen Zer...
- Trending Articles
Team Industries names director of advanced technology and manufacturing
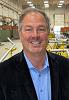
Zekelman Industries to invest $120 million in Arkansas expansion
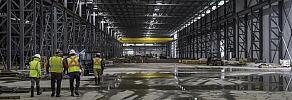
3D laser tube cutting system available in 3, 4, or 5 kW
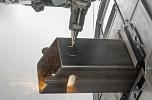
Corrosion-inhibiting coating can be peeled off after use
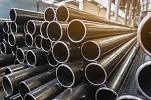
Brushless copper tubing cutter adjusts to ODs up to 2-1/8 in.
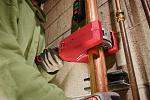
- Industry Events
Pipe and Tube Conference
- May 21 - 22, 2024
- Omaha, NE
World-Class Roll Forming Workshop
- June 5 - 6, 2024
- Louisville, KY
Advanced Laser Application Workshop
- June 25 - 27, 2024
- Novi, MI
Precision Press Brake Certificate Course
- July 31 - August 1, 2024
- Elgin,