Editor-in-Chief
- FMA
- The Fabricator
- FABTECH
- Canadian Metalworking
Categories
- Additive Manufacturing
- Aluminum Welding
- Arc Welding
- Assembly and Joining
- Automation and Robotics
- Bending and Forming
- Consumables
- Cutting and Weld Prep
- Electric Vehicles
- En Español
- Finishing
- Hydroforming
- Laser Cutting
- Laser Welding
- Machining
- Manufacturing Software
- Materials Handling
- Metals/Materials
- Oxyfuel Cutting
- Plasma Cutting
- Power Tools
- Punching and Other Holemaking
- Roll Forming
- Safety
- Sawing
- Shearing
- Shop Management
- Testing and Measuring
- Tube and Pipe Fabrication
- Tube and Pipe Production
- Waterjet Cutting
Industry Directory
Webcasts
Podcasts
FAB 40
Advertise
Subscribe
Account Login
Search
Pumped about waterjet cutting
A small machine shop finds new capabilities lead to exciting opportunities
- By Dan Davis
- June 2, 2017
- Article
- Waterjet Cutting
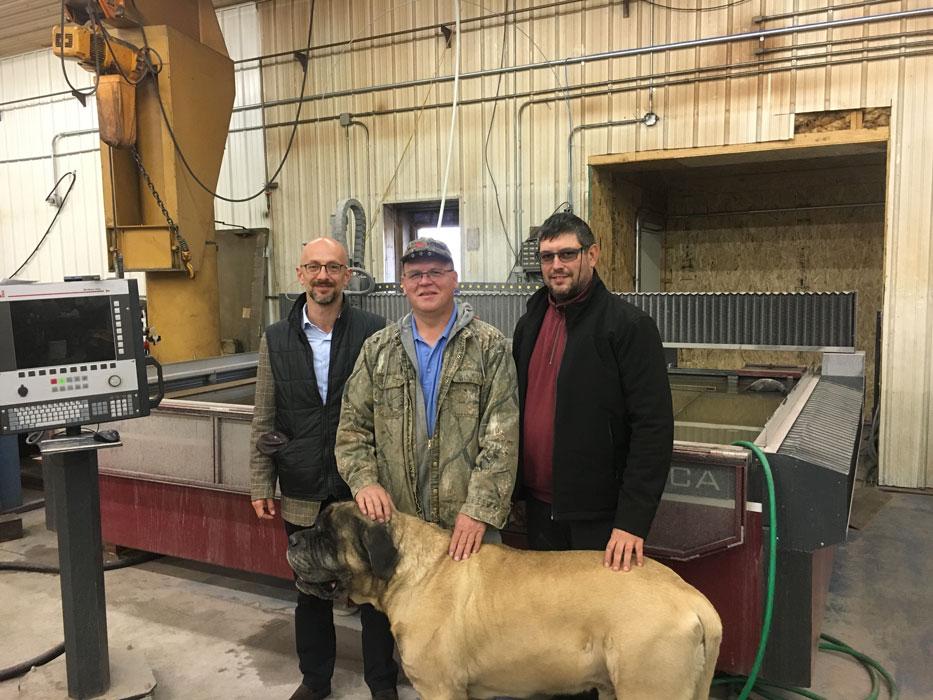
Figure 1
B.J. Schrank and the company mascot, flanked by Roberto Impellittiere (left) and Stefano Giudici, an installation technician (right) from Waterjet U.S.A., stand in front of AA Precision Tooling’s waterjet.
B.J. Schrank is a man who knows what he likes. He’s been doing it for 29 years.
“What I really like to do is metalworking. That’s what I do,” he said. “That’s probably why I didn’t have kids. I spent every minute of every day doing metalworking.”
He’s also done a little welding as well. His dad, who was mechanically inclined but involved in sales, introduced him to welding when he was 6 years old. Schrank started welding on go-karts, and since then he’s never really walked away from metal fabrication and metalworking.
As the owner of AA Precision Tooling in Blooming Prairie, Minn., Schrank has carved out a nice life in his own shop. The shop was larger at one time, but Schrank got tired of working 16-hour days and dealing with workers who’d rather be home not working.
“I decided to downsize, do better work, and charge more for the high-precision work,” he said.
So now AA Precision Tooling is a three-person operation: Schrank; Ruben Kubista, who is married to Schrank’s older step-daughter; and Christina Korpi, Schrank’s younger step-daughter. Kubista handles the sheet metal work, and Korpi manages the company’s finances and purchasing, while also helping out in the shop occasionally. It’s a quiet operation that is also a formidable business for its size.
As an example, Schrank invested in a robot for machine tending about three years ago. Penelope, as the robot is called, has almost 500 jobs stored in her control memory. He said he can program a job in about two hours. If a job is already uploaded into Penelope, changeover from one job to another can be done in about 20 minutes. He also has rearranged the shop so that the robot can run multiple machining centers simultaenously.
AA Precision Tooling took another interesting turn after attending the International Manufacturing Technology Show (IMTS) in Chicago. It led Schrank and his team into the world of sheet metal (“flat manufacturing,” as Schrank called it), and eventually to a fabricating project that has the potential for changing the lives of thousands in lesser-developed lands across the globe.
Enter the World of Waterjet Cutting
The AA Precision Tooling team visits every IMTS. While Schrank spends most of his time looking at chipping machinery, he said Kubista likes to walk the few aisles of the fabricating area at the show. So they typically split up and meet for lunch.
At a recent tradeshow, Kubista never strayed too far from the waterjets. Every time Schrank checked in with him, Kubista indicated he was at another table taking in the latest technology.
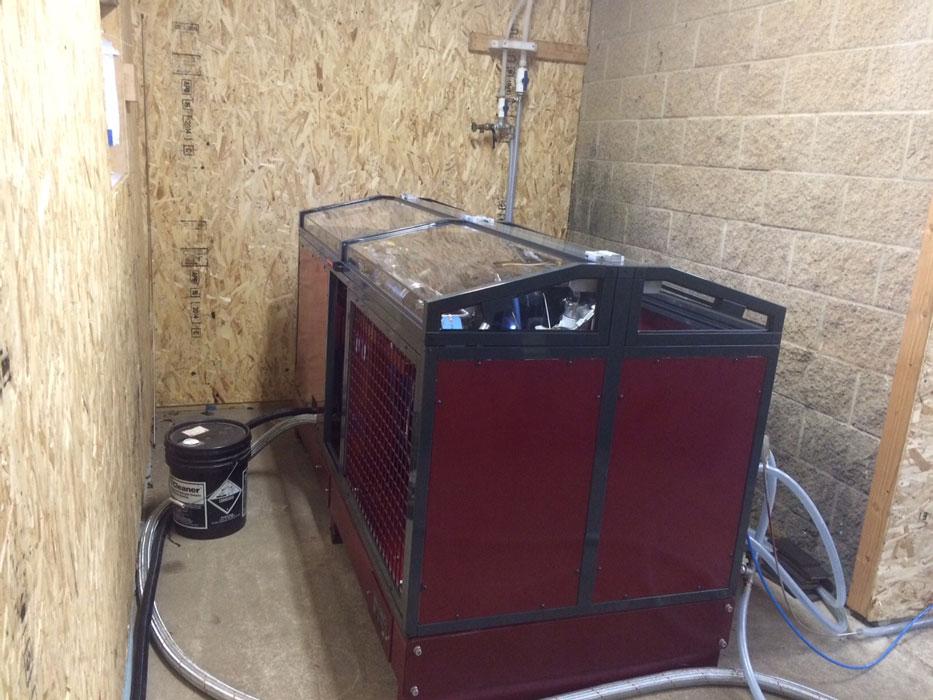
Figure 2
The 60,000-PSI waterjet pump is kept in a separate area from the waterjet to allow for ample room around the machine tool.
When Schrank saw it, he saw potential. Not only would a waterjet give AA Precision Tooling the chance to cut out flat sheet metal and plate, but a 5-axis cutting head could give the shop the means to cut tube, alleviating the need to place these parts in a machining center.
It wasn’t soon after that show that AA Precision Tooling got into the waterjet cutting business (see Figure 1). They purchased a 5-axis, 60,000-PSI Classica waterjet machine from Waterjet USA, Elgin, Ill., and their local dealer, FORGE Manufacturing Solutions. Schrank said the 60,000-PSI pump from KMT Waterjet Systems (see Figure 2) was more than enough to power his single-head machine. A 90,000-PSI machine could have boosted cutting speeds, but not enough to warrant the strain put on consumables, such as the hoses, which would need to be replaced much more frequently if exposed to those higher pressures.
The waterjet came at the right time for the job shop as it was in the midst of a large fabrication project for a company that marketed trailers for moving magnetic resonance imaging machines. These were no ordinary trailers. They were air-cushioned to ensure that these high-tech pieces of machinery survived the rough-and-tumble world of over-the-road transportation.
“The waterjet really cut the parts nice for the hitch on those trailers. I did about 30 sets on there,” Schrank said.
AA Precision Tooling prepared about 38 total hitch sets for its customer. The trailer company’s welder used Schrank’s shop as his own workshop. It took about 17 hours of fabricating to build the hitch.
The business relationship was a good one, but the trailer company’s owner was looking to sell his business. Schrank said he wasn’t interested in going into debt to purchase the company just to hang on to the work. Eventually the company owner found a buyer in Pittsburgh, and that job came to an end for AA Precision Tooling.
“God has been good to me. He’s given me my health, and he let me pay off the bills. I don’t owe anyone any money,” Schrank said.
Also, around this time AA Precision Tooling was in the middle of another project that arose while Schrank was sitting in a church pew. On that particular Sabbath morning two years ago, Schrank met Nathan Rittenour, a missionary associated with Congo Frontline Missions, an organization that has a well-drilling team that works to deliver clean drinking and cooking water to villages in the Congo. Often these remote villages rely on polluted rivers and streams or stagnant ponds for their water sources, and that contaminated water can lead to outbreaks of typhoid fever and dysentery.
Rittenour was making the rounds of U.S. churches trying to raise money for the well-drilling activities. He happened to choose the right church because he also got a manufacturing expert along with the proceeds from the collection plate on that day.
Over the next several months, Schrank and Rittenour worked together to sketch out the concept for a pump. The goal was to avoid the typical drop-rod pump that can be difficult for children and some adults to work. With that traditional design, the water pump operator has to exert enough pressure to draw up the rod and the accompanying water that rises along with it.

Figure 3
By cutting parts for the water pump, Schrank had an opportunity to learn the tips and tricks necessary to produce quality tube parts on the waterjet.
Introducing a New Water Pump
In late 2016 the latest prototype pump was completed. This design incorporates a hydraulic system that makes pumping easier. A counterweight assists with the pushing of the handle in a downward motion, and a pressurized bladder helps with the upward movement of the handle.
“A 4-year-old girl is able to run the pump,” Schrank said.
AA Precision Tooling has run a prototype pump at the shop for 30 days and 30 nights, which amounted to more than 2.6 million strokes, enough to pump 225,000 gallons of water. (The development team had run into an issue with the bladder, but replaced it with a stronger material.) They also received a patent-pending designation for the design in the summer of 2016.
As Schrank worked to develop parts for the latest water pump design, he got an education on the company’s waterjet (see Figure 3).
“When you are rotating the part and moving the cutting head at the same time, it gets complicated,” he said.
He admitted that it took some time to get used to the software. Putting a round circle on a tube was easy. Cutting out rectangles in the tubing used in the pump was a challenge because the tube was to be bent at a 30-degree angle, becoming a gusset and tongue support brace. First, the shape was new to the Lantek Flex3D software, so it had to be drawn in the flat form. Second, it had to be applied to the tube as a “skin” in the software, according to Schrank.
When the design work was completed, Schrank had to dial in the waterjet cutting. This involved fixturing parts correctly to avoid vibrations and adjusting the power, from say, 100 percent to 90 percent, to deliver just the right edge.
“It’s very scientific, but there is also some art to it,” Schrank said. “It’s like machining.”
AA Precision Tooling had an order for 20 pumps, and as of mid-March, it had completed 15 of them. One of the earliest pumps, sent to Congo and installed late last year, has been used about 13 hours per day, pumping out more than 7,000 liters of water daily. Schrank said he heard a story that a person from South Africa trekked to Congo just to see the pump in action.
For future pump models, Schrank said he is looking to possibly add a powder coating over the galvanized steel. He had some requests from the field for a choice in colors, and he said that an additional coating might add to a more durable finish.

Figure 1
The waterjet has proven very useful in delivering angle cuts on thick material, such as this 2-in. A36 steel.
In the meantime, AA Precision Tooling is cutting more flat work (see Figure 4). For instance, it has put a 45-degree bevel on a 0.1875-in. stainless steel piece that is later formed into an ellipse to act as an end cap for an HVAC header.
“You can cut it out and machine it, but I’m able to cut that out in minutes, and it’s done rather than trying to grind it into shape,” he said.
The Best Water in Town
One of the side projects that came with the waterjet was establishing a water purification system. The shop’s well water is hard, and Schrank knew he needed something purer and softer to get the best performance from the waterjet.
A friend engineered the purification system, and Schrank plumbed it. The system includes a softener, a filtering system, a reverse-osmosis system, and a water tower.
“I’m burning about 60 gallons of water an hour with the waterjet. I have 500 gallons on tap. When I get down to about 300 gallons, the system starts making water. I make 30 gallons of water per hour. I can run 12 hours straight without running out of water,” he said.
Of course, AA Precision Tooling is not going to cut for 12 hours straight. But even if they cut for a long stretch, maybe four to five hours, when a break comes for cleaning up or changing over to a new job, the water purification system can deliver another 30 gallons ready for use.
News of the purified water has gotten out to neighbors as well. Schrank said that it’s not unusual for people to swing by to fill up their bottles or jugs.
That’s not too bad for a simple metalworker—helping to improve the lives of people on another continent and the neighbors down the street at the same time.
AA Precision Tooling, 507-455-2051, aaprecisiontooling@gmail.com, www.facebook.com/aaprecisiontooling
FORGE Manufacturing Solutions, 515-249-8428, www.forge-usa.com
KMT Waterjet Systems, 620-856-2151, www.kmtwaterjet.com
Waterjet USA LLC, 630-208-1567, www.waterjetusa.com
About the Author
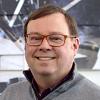
Dan Davis
2135 Point Blvd.
Elgin, IL 60123
815-227-8281
Dan Davis is editor-in-chief of The Fabricator, the industry's most widely circulated metal fabricating magazine, and its sister publications, The Tube & Pipe Journal and The Welder. He has been with the publications since April 2002.
subscribe now
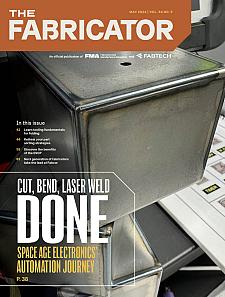
The Fabricator is North America's leading magazine for the metal forming and fabricating industry. The magazine delivers the news, technical articles, and case histories that enable fabricators to do their jobs more efficiently. The Fabricator has served the industry since 1970.
start your free subscription- Stay connected from anywhere
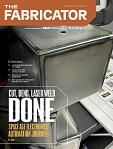
Easily access valuable industry resources now with full access to the digital edition of The Fabricator.
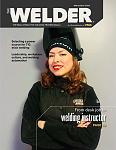
Easily access valuable industry resources now with full access to the digital edition of The Welder.
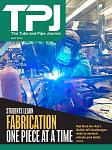
Easily access valuable industry resources now with full access to the digital edition of The Tube and Pipe Journal.
- Podcasting
- Podcast:
- The Fabricator Podcast
- Published:
- 04/16/2024
- Running Time:
- 63:29
In this episode of The Fabricator Podcast, Caleb Chamberlain, co-founder and CEO of OSH Cut, discusses his company’s...
- Trending Articles
Capturing, recording equipment inspection data for FMEA
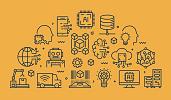
Tips for creating sheet metal tubes with perforations
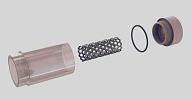
Are two heads better than one in fiber laser cutting?
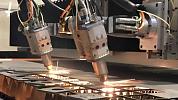
Supporting the metal fabricating industry through FMA
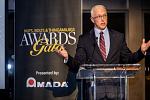
Omco Solar opens second Alabama manufacturing facility
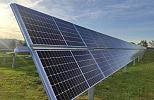
- Industry Events
16th Annual Safety Conference
- April 30 - May 1, 2024
- Elgin,
Pipe and Tube Conference
- May 21 - 22, 2024
- Omaha, NE
World-Class Roll Forming Workshop
- June 5 - 6, 2024
- Louisville, KY
Advanced Laser Application Workshop
- June 25 - 27, 2024
- Novi, MI