Project Engineer
- FMA
- The Fabricator
- FABTECH
- Canadian Metalworking
Our Publications
Categories
- Additive Manufacturing
- Aluminum Welding
- Arc Welding
- Assembly and Joining
- Automation and Robotics
- Bending and Forming
- Consumables
- Cutting and Weld Prep
- Electric Vehicles
- En Español
- Finishing
- Hydroforming
- Laser Cutting
- Laser Welding
- Machining
- Manufacturing Software
- Materials Handling
- Metals/Materials
- Oxyfuel Cutting
- Plasma Cutting
- Power Tools
- Punching and Other Holemaking
- Roll Forming
- Safety
- Sawing
- Shearing
- Shop Management
- Testing and Measuring
- Tube and Pipe Fabrication
- Tube and Pipe Production
- Waterjet Cutting
Industry Directory
Webcasts
Podcasts
FAB 40
Advertise
Subscribe
Account Login
Search
Gary Morphy
Excella Technologies
425 Hespeler Rd Suite 521
Cambridge, ON N1R 8J6 Canada
(519) 772 - 5748 x101
Tube Hydroforming Design Flexibility—Part IX:
- By Gary Morphy
- Feb 7, 2006
- Hydroforming
- Article
In this article Gary Morphy reviews high-pressure and pressure sequence hydroforming and discusses factors to consider when deciding which process is best for a particular application. The decision should be based in part on anticipating future needs.
Tube Hydroforming Design Flexibility—Part VIII: Dimensional Stability
- By Gary Morphy
- Jun 14, 2005
- Hydroforming
- Article
Whether they are producing automobiles or hydroforming press parts, designers, manufacturers, and assembly personnel are very concerned about dimensional stability. Surfaces and holes must be located in a specified range and smaller is better. Concern escalates as the drive to improve quality and reduce build tolerances and problems increases.
Tube Hydroforming Design Flexibility—Part VII: Holes
- By Gary Morphy
- Feb 8, 2005
- Hydroforming
- Article
When making holes in hydroformed parts, fabricators have many choices—milling, drilling, laser cutting, plasma cutting, flow drilling, post-piercing, and hydropiercing.
Tube Hydroforming Design Flexibility—Part VI
- By Gary Morphy
- Sep 14, 2004
- Hydroforming
- Article
Tube hydroforming reshapes a tube from a normally round cross section to a desired shape. The final shape, usually rectangular, develops along the part length. The cross-sectional periphery may be consistent throughout the part and equal to the original tube, or it can be expanded in localized...
-
- From The Fabricator
Tube Hydroforming Design Flexibility—Part V
- By Gary Morphy
- Feb 26, 2004
- Hydroforming
- Article
Combined with the information in Part III of this series that focused on cross-section expansion before hydroforming, this article discusses the most common options used in preparing tube for hydroforming and achieving the designer-intended part. Properly executing bending and cross-section...
Tube Hydroforming Design Flexibility—Part IV
- By Gary Morphy
- Oct 23, 2003
- Hydroforming
- Article
Material selection is a very important aspect of design flexibility when striving to fulfill part functionality requirements. Choosing the correct material is fundamental to making the part effectively and efficiently. The way a material is formed and the conditions it needs to withstand for...
Tube Hydroforming Design Flexibility—Part III
- By Gary Morphy
- Apr 24, 2003
- Hydroforming
- Article
The last article in this series noted that variable periphery design, or cross-section expansion, often is thought to be the most important aspect of tube hydroforming design flexibility. Expansion in the hydroforming die commonly is assumed to be the most efficient and most effective method,...
Tube Hydroforming Design Flexibility—Part II
- By Gary Morphy
- Oct 10, 2002
- Hydroforming
- Article
It's difficult to overemphasize the importance of cross section expansion when you're talking about successful and innovative hydroforming of steel tubing. Overemphasizing one aspect of the tube hydroforming design process can take attention away from others and result in less than optimal design....
Tube Hydroforming Design Flexibility—Part I
- By Gary Morphy
- May 16, 2002
- Hydroforming
- Article
Design flexibility is something that all automotive designers want, but too often they lack a thorough understanding of what that means—what aspects of design flexibility apply to a certain part and their effect on cost. A methodology often is adopted when (or even before) a part development...
Hydroforming a new front automotive structure
- By Gary Morphy
- Oct 25, 2001
- Hydroforming
- Article
Hydroforming the parts in a vehicle structure can be of immense benefit on several counts, as a review of a recent project at the author's company can attest.
- Podcasting
- Podcast:
- The Fabricator Podcast
- Published:
- 04/16/2024
- Running Time:
- 63:29
In this episode of The Fabricator Podcast, Caleb Chamberlain, co-founder and CEO of OSH Cut, discusses his company’s...
- Trending Articles
Tips for creating sheet metal tubes with perforations
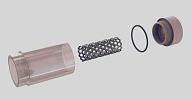
Are two heads better than one in fiber laser cutting?
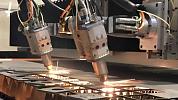
Supporting the metal fabricating industry through FMA
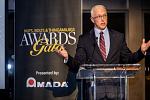
JM Steel triples capacity for solar energy projects at Pennsylvania facility
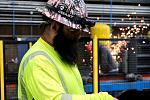
Zekelman Industries to invest $120 million in Arkansas expansion
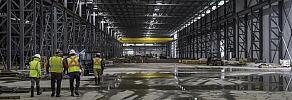
- Industry Events
16th Annual Safety Conference
- April 30 - May 1, 2024
- Elgin,
Pipe and Tube Conference
- May 21 - 22, 2024
- Omaha, NE
World-Class Roll Forming Workshop
- June 5 - 6, 2024
- Louisville, KY
Advanced Laser Application Workshop
- June 25 - 27, 2024
- Novi, MI
- Upcoming Webcasts
Navigating Change: The Manufacturer’s Guide to Change Management with ERP Implementation
- May 16, 2024
- Sponsored
- Presented By: ECI Software Solutions, M1