- FMA
- The Fabricator
- FABTECH
- Canadian Metalworking
Our Publications
Categories
- Additive Manufacturing
- Aluminum Welding
- Arc Welding
- Assembly and Joining
- Automation and Robotics
- Bending and Forming
- Consumables
- Cutting and Weld Prep
- Electric Vehicles
- En Español
- Finishing
- Hydroforming
- Laser Cutting
- Laser Welding
- Machining
- Manufacturing Software
- Materials Handling
- Metals/Materials
- Oxyfuel Cutting
- Plasma Cutting
- Power Tools
- Punching and Other Holemaking
- Roll Forming
- Safety
- Sawing
- Shearing
- Shop Management
- Testing and Measuring
- Tube and Pipe Fabrication
- Tube and Pipe Production
- Waterjet Cutting
Industry Directory
Webcasts
Podcasts
FAB 40
Advertise
Subscribe
Account Login
Search
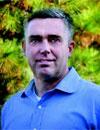
George Winton
Winton Machine Co.
3644 Burnette Road
Suwanee, GA 30024
888-321-1499
Business as usual versus a change for good
- By George Winton
- Aug 25, 2015
- Tube and Pipe Fabrication
- Article
Columnist George Winton discusses a way to combine two operations into one seamless process by adding a drill to a CNC tube bender.
Stationary parts don't make money
- By George Winton
- Nov 9, 2012
- Shop Management
- Article
Seeing bins of parts lying around in your shop? Maybe it’s time to get away from the large-batch method and try one-piece flow. Rather than make a large quantity of Component 1, then Component 2, then Component 3, while a welder downstream waits for Component 3, you could set up a system of one-piece flow that sends a kit of three components. The key to implement this strategy is the bender software.
Assessing the arc
- By George Winton
- Dec 9, 2011
- Tube and Pipe Fabrication
- Article
Large-radius bends are used in many places, such as appliance handles and automobile components. For measuring large-radius bends, fabricators have at least three options: go/no-go fixtures, entering the bent part’s measurements into a CAD program and using it to calculate the radius, and a depth gauge.
Holding the dies
- By George Winton
- Jun 24, 2011
- Tube and Pipe Fabrication
- Article
There are a few popular ways to affix the clamp die and pressure die to a rotary draw bending machine. All aim to accomplish the same thing: provide precise vertical alignment to the mating bend die and provide rigid support for the respective die during the bending process so it resists the...
Getting a grip on tube bending
- By George Winton
- Apr 27, 2011
- Tube and Pipe Fabrication
- Article
A collet closer, commonly found on CNC or NC tube benders, serves an important role in the bending process. When quality is good, little attention is paid to its operation. When one or more quality parameters fall outside of acceptable limits, often the collet closer again is overlooked. A...
Ironing the wrinkles out of copper tubing
- By George Winton
- Mar 10, 2011
- Tube and Pipe Fabrication
- Article
A wiper die is helpful for making wrinkle-free bends. Understanding how one works can help you decide if you need to use one.
Get the slug out
- By George Winton
- Jan 31, 2011
- Tube and Pipe Fabrication
- Article
Punching a hole in a tube is one thing; getting the slug out is something else altogether. Even if most of the slugs exit without a problem, the occasional hanging slug can cause a serious problem. Two methods are mechanical force and air pressure.
Sizing up the job
- By George Winton
- Nov 1, 2010
- Shop Management
- Article
Accounting is straightforward, but it’s not iron-clad; fabricators have latitude in the accounting system they use to bid on contracts. A bottom-up approach, one that analyzes all the costs that go into making a component, is suitable for many parts. A top-down approach looks at the part and asks how much the market will bear. Choosing one or the other is a matter of understanding the market for the part.
The axis of safety
- By George Winton
- Sep 16, 2010
- Tube and Pipe Fabrication
- Article
A tube bender can be considered a collection of power presses and, as such, it needs more than just a few conventional barriers between the operator and the machine. Safety mats, interlocked switches, emergency-stop switches, and interlocked side plates are a few of the safety devices available to machine tool manufacturers.
Feeding the process
- By George Winton
- Jul 9, 2010
- Tube and Pipe Fabrication
- Article
Whether a bending process starts with a cut length of tubular product or a coil, gravitational or torsional forces can lead to unwanted variations in the finished product. In the case of gravity, tube supports can counteract it; for torsion, it’s a matter of matching the coil’s output to the bender’s input.
Doing more with less
- By George Winton
- Apr 29, 2010
- Tube and Pipe Fabrication
- Article
Loading and unloading tube for fabricating often is a manual process. Because labor rates in the U.S. are higher than those in many other countries, manual loading and unloading isn’t competitive. Using an automatic loader/unloader can change that, moving an operation from red to black.
Making a workhorse run
- By George Winton
- Feb 9, 2010
- Tube and Pipe Fabrication
- Article
Vertical compression tube benders have been around for more than 50 years (see Figure 1). Historically associated with high-volume bending, these benders continue to play a role in production environments where parts have just one or two bends. Also known as press benders, they have stood the...
Putting a few end forming basics to work
- By George Winton
- Mar 9, 2009
- Roll Forming
- Article
Whether maintaining or changing the OD, knowing the basics of end forming—especially friction and lubrication—can help achieve a successful result.
Coax Facts
- By George Winton
- Jan 1, 2009
- Tube and Pipe Fabrication
- Article
Continuous improvement and statistical process control are useful,time-tested techniques—they have been used since the 1950s—buttheir use must be tailored to specific applications. For example, atypical manufacturing metric is parts per minute, but many rollformers should measure feet per minute. This and other tips can helproll formers accurately evaluate their productivity and measure theimpact of process improvements.
The ins and outs of extrusion bending
- By George Winton
- Dec 12, 2008
- Tube and Pipe Fabrication
- Article
Extrusions can be tricky to bend and handle. Paying close attention tobender selection, die design, programming, and material handling can help to ensure efficient and productive bending.
- Podcasting
- Podcast:
- The Fabricator Podcast
- Published:
- 04/16/2024
- Running Time:
- 63:29
In this episode of The Fabricator Podcast, Caleb Chamberlain, co-founder and CEO of OSH Cut, discusses his company’s...
- Trending Articles
Tips for creating sheet metal tubes with perforations
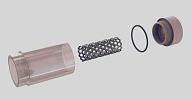
JM Steel triples capacity for solar energy projects at Pennsylvania facility
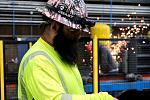
Are two heads better than one in fiber laser cutting?
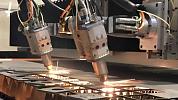
Supporting the metal fabricating industry through FMA
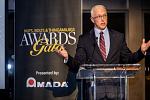
Zekelman Industries to invest $120 million in Arkansas expansion
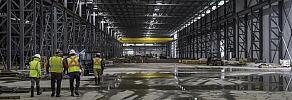
- Industry Events
16th Annual Safety Conference
- April 30 - May 1, 2024
- Elgin,
Pipe and Tube Conference
- May 21 - 22, 2024
- Omaha, NE
World-Class Roll Forming Workshop
- June 5 - 6, 2024
- Louisville, KY
Advanced Laser Application Workshop
- June 25 - 27, 2024
- Novi, MI
- Upcoming Webcasts
Navigating Change: The Manufacturer’s Guide to Change Management with ERP Implementation
- May 16, 2024
- Sponsored
- Presented By: ECI Software Solutions, M1