Independent welding consumables professional
- FMA
- The Fabricator
- FABTECH
- Canadian Metalworking
Our Publications
Categories
- Additive Manufacturing
- Aluminum Welding
- Arc Welding
- Assembly and Joining
- Automation and Robotics
- Bending and Forming
- Consumables
- Cutting and Weld Prep
- Electric Vehicles
- En Español
- Finishing
- Hydroforming
- Laser Cutting
- Laser Welding
- Machining
- Manufacturing Software
- Materials Handling
- Metals/Materials
- Oxyfuel Cutting
- Plasma Cutting
- Power Tools
- Punching and Other Holemaking
- Roll Forming
- Safety
- Sawing
- Shearing
- Shop Management
- Testing and Measuring
- Tube and Pipe Fabrication
- Tube and Pipe Production
- Waterjet Cutting
Industry Directory
Webcasts
Podcasts
FAB 40
Advertise
Subscribe
Account Login
Search
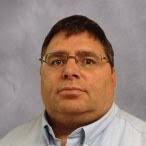
Nino Mascalco
-
- From The Welder
Consumables Corner: Diagnosing the obvious and not-so-obvious causes of porosity
- By Nino Mascalco and Rob Koltz
- Nov 25, 2020
- Consumables
- Article
Weld porosity is a dangerous weld defect that has myriad causes. Rob Koltz and Nino Mascalco analyze a reader's situation and help him nail down what's causing the porosity in his pipe fabrications.
-
- From The Welder
Consumables Corner: How to diagnose and prevent weld cracking
- By Nino Mascalco and Rob Koltz
- Oct 28, 2020
- Consumables
- Article
Weld cracking is a complicated and serious problem that can happen to any welder. Nino Mascalco and Rob Koltz provide a rundown of weld cracking and explain how you can prevent it from happening.
-
- From The Welder
Consumables Corner: Why you shouldn’t use shielding gas with self-shielded FCAW electrodes
- By Nino Mascalco and Rob Koltz
- Aug 26, 2020
- Consumables
- Article
Rob Koltz and Nino Mascalco provide background on FCAW electrodes and explain why it’s a bad idea to use shielding gas with self-shielded electrodes.
-
- From The Welder
Consumables Corner: Strategies for vertical-up welding of stainless steel
- By Nino Mascalco and Rob Koltz
- Jul 8, 2020
- Consumables
- Article
Consumables Corner contributors Rob Koltz and Nino Mascalco help a reader work through performance issues when using gas metal arc welding (GMAW), gas tungsten arc welding (GTAW), and flux-core arc welding (FCAW) for vertical-up applications on stainless steels.
-
- From The Welder
Consumables Corner: Heat input and discoloration in stainless steel welding
- By Nino Mascalco and Rob Koltz
- Apr 15, 2020
- Consumables
- Article
Nino Mascalo and Rob Koltz discuss heat input and weld discoloration in stainless steel welds.
-
- From The Welder
Consumables Corner: Optimizing SAW on pressure vessels, Part II
- By Nino Mascalco and Rob Koltz
- Feb 26, 2020
- Consumables
- Article
In the second part of the series, Nino Mascalo and Rob Koltz further help a manufacturer of carbon steel pressure vessels unearth why he’s having trouble increasing submerged arc welding (SAW) throughput.
-
- From The Welder
Consumables Corner: Optimizing SAW on pressure vessels, Part I
- By Nino Mascalco and Rob Koltz
- Nov 29, 2019
- Consumables
- Article
Nino Mascalo and Rob Koltz help a manufacturer of carbon steel pressure vessels unearth why he’s having trouble increasing throughput.
-
- From The Welder
Consumables Corner: Addressing penetration at the root of aluminum tack welds
- By Nino Mascalco and Rob Koltz
- Sep 26, 2019
- Consumables
- Article
The columnists help a fabricator address its problems with lack of fusion.
-
- From The Welder
Consumables Corner: Achieving toughness in the HAZ of weld joints
- By Nino Mascalco and Rob Koltz
- Jul 19, 2019
- Consumables
- Article
Do high preheat, high interpass temperatures, and high heat input affect HAZ performance?
-
- From The Welder
Consumables Corner: What are the requirements for low-hydrogen electrodes?
- By Nino Mascalco, Rob Koltz, and Steve Sigler
- May 17, 2019
- Consumables
- Article
Do you have to follow a customer’s recommendations for low-hydrogen electrodes?
-
- From The Welder
Consumables Corner: Choosing the correct carbon equivalency formula
- By Nino Mascalco, Rob Koltz, and Steve Sigler
- Mar 25, 2019
- Consumables
- Article
Q: We're a midsize fabrication shop that builds and welds machines and structural components from varying types of carbon steel. Some of the material is mild carbon steel, while some is high-strength, low-alloy (HSLA) or stronger grades of structural steel. If we're welding on thicker sections of...
-
- From The Welder
Consumables Corner: Solving weld crack issues with 4150 chrome-moly steel
- By Nino Mascalco, Rob Koltz, and Steve Sigler
- Jan 26, 2019
- Arc Welding
- Article
Q: We currently manufacture a product that comprises a 4150 steel pipe that is 30 in. in diameter and 2 in. thick, welded to a 1018 steel plate that is 3 in. thick. The pipe has a 3/8-in. bevel and we join it using a triple-pass weld. Recently we switched from an ER80 filler metal containing 1...
-
- From The Welder
Consumables Corner: The relationship between ferrite numbers and cracking
- By Nino Mascalco, Rob Koltz, and Steve Sigler
- Nov 19, 2018
- Consumables
- Article
What does a low ferrite number have to do with cracking in stainless steel welded joints? The Consumables Crew explains.
-
- From The Welder
Consumables Corner: A guide to understanding heat treating and how it affects the weld
- By Nino Mascalco, Rob Koltz, and Steve Sigler
- Sep 26, 2018
- Consumables
- Article
The Consumables Corner crew assists a reader interested in learning more about the effects that heat treatment has on filler metals.
-
- From The Welder
Consumables Corner: Aluminum welding for the non-aluminum welder
- By Nino Mascalco, Rob Koltz, and Steve Sigler
- Jul 26, 2018
- Consumables
- Article
The Consumables Corner team counsels a fabricator new to aluminum welding.
- Podcasting
- Podcast:
- The Fabricator Podcast
- Published:
- 04/16/2024
- Running Time:
- 63:29
In this episode of The Fabricator Podcast, Caleb Chamberlain, co-founder and CEO of OSH Cut, discusses his company’s...
- Trending Articles
Tips for creating sheet metal tubes with perforations
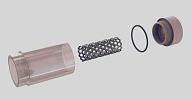
JM Steel triples capacity for solar energy projects at Pennsylvania facility
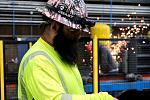
Are two heads better than one in fiber laser cutting?
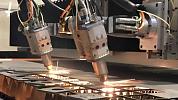
Supporting the metal fabricating industry through FMA
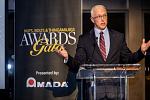
Zekelman Industries to invest $120 million in Arkansas expansion
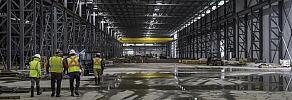
- Industry Events
16th Annual Safety Conference
- April 30 - May 1, 2024
- Elgin,
Pipe and Tube Conference
- May 21 - 22, 2024
- Omaha, NE
World-Class Roll Forming Workshop
- June 5 - 6, 2024
- Louisville, KY
Advanced Laser Application Workshop
- June 25 - 27, 2024
- Novi, MI
- Upcoming Webcasts
Navigating Change: The Manufacturer’s Guide to Change Management with ERP Implementation
- May 16, 2024
- Sponsored
- Presented By: ECI Software Solutions, M1