Editor-in-Chief
- FMA
- The Fabricator
- FABTECH
- Canadian Metalworking
Categories
- Additive Manufacturing
- Aluminum Welding
- Arc Welding
- Assembly and Joining
- Automation and Robotics
- Bending and Forming
- Consumables
- Cutting and Weld Prep
- Electric Vehicles
- En Español
- Finishing
- Hydroforming
- Laser Cutting
- Laser Welding
- Machining
- Manufacturing Software
- Materials Handling
- Metals/Materials
- Oxyfuel Cutting
- Plasma Cutting
- Power Tools
- Punching and Other Holemaking
- Roll Forming
- Safety
- Sawing
- Shearing
- Shop Management
- Testing and Measuring
- Tube and Pipe Fabrication
- Tube and Pipe Production
- Waterjet Cutting
Industry Directory
Webcasts
Podcasts
FAB 40
Advertise
Subscribe
Account Login
Search
Catching the wave of reshoring
- By Dan Davis
- April 28, 2011
To no one's great surprise, fabricators believe that 2011 is shaping up to be a pretty good year, even in the face of rising steel prices and international turmoil. As several fabricators have told me, when you come from the depths of 2009, you have no choice but to believe things are looking up.
Amidst the positive feelings and cautious optimism, a couple of fabricators noted how they currently are working on jobs that previously were outsourced to China. One fabricator actually called the jobs part of a "trend" and included that work as part of the reason his company will see a 15 percent increase in sales for 2011. Another fabricator called his store fixture business a "growing segment" because of all the jobs coming back from China.
No matter whether it's called "reshoring" or "backshoring," it sure is good news.
Admittedly, a lot of the evidence about outsourced work to China returning to the U.S. is anecdotal. Several vocal advocates—such as Harry Moser, the founder of the Reshoring Initiative, and Michele Nash-Hoff, author of Can American Manufacturing Be Saved?—have emerged to help bring the issue to more people's attention. Perhaps metal fabricators are more aware as a result and now are making note of it. In the end, if it means more work for a shop, how could it be a bad thing?
Actually, the trend should continue to grow. At the very least, multinational OEMs that still call the U.S. home realize it makes sense to have some domestic manufacturing support; putting all their manufacturing eggs into one geographic area isn't too smart, particularly after witnessing what occurred recently in Japan. Also, manufacturing customers increasingly are more concerned with just-in-time deliveries and rapid response from supply chain partners, which can prove difficult when they're receiving work from the other side of the world.
The most telling sign, however, that more manufacturing jobs will be reshored from China is that the country will not be the low-price leader for manufacturing services, and it really doesn't have the motivation to become more lean to compete with its neighbors, such as Vietnam.
Check out this excerpt from lean guru Richard J. Schonberger's guest editorial in the April 2011 issue of Manufacturing Engineering:
"Chinese companies are jacking up pay so employees will stay at their workstations doing intolerable jobs. How intolerable? The typical high-touch assembly task in China (and other developing countries) takes 10 seconds or less. At that rate, the assembler must repeat the same few motions some 3,000 times per shift. Usually there is no cross-training, no job rotation. The utter boredom is bad, the repetitive-motion injuries worse—for the company as well as the employee. They result in high quit rates—quit and take a job down the road for the same or higher wage and a different 3,000-repeats-per-shift job.
"These plants employ legions of supervisors, there to deal harshly with disruptive behaviors, including, in some cases, talking. Backing up the supervisors are extra-large staffs of timekeepers, inspectors, monitors, gatekeepers, and security. Plenty of trainers, too, because with dozens or hundreds quitting every week, new dozens or hundreds must be hired and trained."
I've been told that U.S. manufacturers must beware Chinese manufacturers because they are progressing from simple manufacturing tasks to much more complicated jobs that rely on automated equipment and sophisticated skills. That may be true, but the bureaucratic bloat that exists in these operations can't help these Chinese companies to be competitive on a global scale. And if I know anything about the Chinese government, party leaders are more interested in keeping people employed than running lean and efficient manufacturing operations. I don't believe Chinese companies have the same motivation—or even freedom of choice—to pursue the hard choices that make so many U.S. manufacturers topnotch lean enterprises.
subscribe now
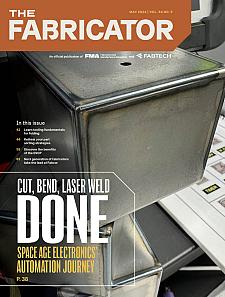
The Fabricator is North America's leading magazine for the metal forming and fabricating industry. The magazine delivers the news, technical articles, and case histories that enable fabricators to do their jobs more efficiently. The Fabricator has served the industry since 1970.
start your free subscriptionAbout the Author
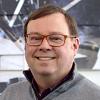
Dan Davis
2135 Point Blvd.
Elgin, IL 60123
815-227-8281
Dan Davis is editor-in-chief of The Fabricator, the industry's most widely circulated metal fabricating magazine, and its sister publications, The Tube & Pipe Journal and The Welder. He has been with the publications since April 2002.
- Stay connected from anywhere
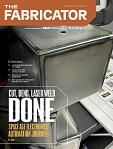
Easily access valuable industry resources now with full access to the digital edition of The Fabricator.
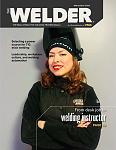
Easily access valuable industry resources now with full access to the digital edition of The Welder.
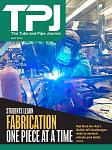
Easily access valuable industry resources now with full access to the digital edition of The Tube and Pipe Journal.
- Podcasting
- Podcast:
- The Fabricator Podcast
- Published:
- 04/16/2024
- Running Time:
- 63:29
In this episode of The Fabricator Podcast, Caleb Chamberlain, co-founder and CEO of OSH Cut, discusses his company’s...
- Industry Events
16th Annual Safety Conference
- April 30 - May 1, 2024
- Elgin,
Pipe and Tube Conference
- May 21 - 22, 2024
- Omaha, NE
World-Class Roll Forming Workshop
- June 5 - 6, 2024
- Louisville, KY
Advanced Laser Application Workshop
- June 25 - 27, 2024
- Novi, MI