Owner, Brown Dog Welding
- FMA
- The Fabricator
- FABTECH
- Canadian Metalworking
Categories
- Additive Manufacturing
- Aluminum Welding
- Arc Welding
- Assembly and Joining
- Automation and Robotics
- Bending and Forming
- Consumables
- Cutting and Weld Prep
- Electric Vehicles
- En Español
- Finishing
- Hydroforming
- Laser Cutting
- Laser Welding
- Machining
- Manufacturing Software
- Materials Handling
- Metals/Materials
- Oxyfuel Cutting
- Plasma Cutting
- Power Tools
- Punching and Other Holemaking
- Roll Forming
- Safety
- Sawing
- Shearing
- Shop Management
- Testing and Measuring
- Tube and Pipe Fabrication
- Tube and Pipe Production
- Waterjet Cutting
Industry Directory
Webcasts
Podcasts
FAB 40
Advertise
Subscribe
Account Login
Search
Clean. Your. Material.
- By Josh Welton
- September 23, 2015
The last few weeks have marked my first foray into teaching. I’m just getting acclimated, co-instructing a Wednesday night certification class at Macomb Community College in Michigan.
This class has been the highlight of my week so far. Physically, I’m still pretty worn down from the surgeries (diving right back into 100-hr. workweeks was not exactly recommended by my doctors), and while I’m all about doing demonstrations and giving hands-on advice, being productive while not beating up my body has been a nice change of pace. Much like the writing, it’s a new avenue that has opened up, a door unlocked, and I’m excited to see where it leads.
For the students in this class, this isn’t their first rodeo. I dig that most have decent hand/eye coordination, and they seem to want to learn and are eager to pick my brain. And yet there are a lot of basics that still seem to elude them. First and foremost is something that cannot be emphasized enough. It’s the one piece of advice I give to the hundreds of “what advice would you give a beginning welder?” messages I get.
Clean. Your. Material.
This is especially true for the kids working on their TIG and MIG welding. Three weeks in and I’m still telling them the same thing: Grind or sandblast and wire-wheel that base material. No, it’s not a waste of time. It’s absolutely critical. Buy a 4-½ in. grinder and keep it with you. Buy a nice one, you’ll get your money out of it. Add in a few grinding discs, some flap discs, and a knotted wire wheel.
I don’t care if it is just practice. The habits you form now will stay with you forever.
Even just mill scale alters your weld; you need more heat to break through it, and then it still contaminates the weld. You’ll get undercut and porosity from it, and I don’t want to see either in any weld, practice or real.
If you’re overlaying multiple passes, wire-wheel each pass before the next. TIG and MIG welding wire is formulated to bring contaminants to the surface of the weld. You’ll see the silicon and manganese grab the junk and bring it to the top; it shows up in shiny, hard puddles. You don’t want to weld over these puddles, you want to clean them up.
With stick welding it’s somewhat different, but the same idea. Obviously, the layer of flux needs to be chipped off the top. But it also needs to be removed from every nook and cranny. You can’t just “burn it out” with the next pass; that stuff stays in the metal and causes big issues when you go to bend a coupon or send a piece in for X-ray. Chip it, wire-wheel it, pick it, and repeat. I cannot tell you enough how critical it is for interpass cleanup to be spotless.
I don’t have a lot of visuals for this week’s post, but I do have a couple of pictures that show the value of cleaning off mill scale, even for running a few stringers.
There are three sets of welds. Figure 1 shows welds over mill scale. Welding over mill scale not only hurts your chances for consistency, but the layer spits, sputters, and gunks up the tungsten.
Figure 2 shows welds that were done after a quick sandblast session that removed the mill scale. Notice huge improvement. But as I’ve mentioned before, sandblasting still contaminates the base metal. You’re literally shooting dirt at the metal. While the consistency and overall appearance are greatly improved, more can be achieved by quickly hitting it with a wire brush or wire wheel (Figure 3).
Sandblasted, wire-wheeled, then welded. Crisp, consistent, and the tungsten stays sharp. If you don’t have access to a sandblast cabinet, a grinding disc and flap disc on your grinder will do the job. The cleaner and smoother the base material surface is, the greater the potential for a clean, consistent weld.
It’s not the first time you’ve heard me go on about it, and it won’t be the last. It’s such a simple concept; in fact, I’m not sure if anything in the trade has a larger “simple-to-significant” gap.
Cleanliness is next to godliness. Say it. Repeat it. Live it.
All images courtesy of Brown Dog Welding.
subscribe now
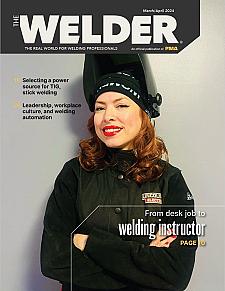
The Welder, formerly known as Practical Welding Today, is a showcase of the real people who make the products we use and work with every day. This magazine has served the welding community in North America well for more than 20 years.
start your free subscriptionAbout the Author
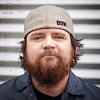
About the Publication
- Stay connected from anywhere
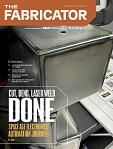
Easily access valuable industry resources now with full access to the digital edition of The Fabricator.
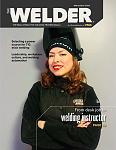
Easily access valuable industry resources now with full access to the digital edition of The Welder.
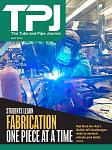
Easily access valuable industry resources now with full access to the digital edition of The Tube and Pipe Journal.
- Podcasting
- Podcast:
- The Fabricator Podcast
- Published:
- 04/16/2024
- Running Time:
- 63:29
In this episode of The Fabricator Podcast, Caleb Chamberlain, co-founder and CEO of OSH Cut, discusses his company’s...
- Industry Events
16th Annual Safety Conference
- April 30 - May 1, 2024
- Elgin,
Pipe and Tube Conference
- May 21 - 22, 2024
- Omaha, NE
World-Class Roll Forming Workshop
- June 5 - 6, 2024
- Louisville, KY
Advanced Laser Application Workshop
- June 25 - 27, 2024
- Novi, MI