Editor-in-Chief
- FMA
- The Fabricator
- FABTECH
- Canadian Metalworking
Categories
- Additive Manufacturing
- Aluminum Welding
- Arc Welding
- Assembly and Joining
- Automation and Robotics
- Bending and Forming
- Consumables
- Cutting and Weld Prep
- Electric Vehicles
- En Español
- Finishing
- Hydroforming
- Laser Cutting
- Laser Welding
- Machining
- Manufacturing Software
- Materials Handling
- Metals/Materials
- Oxyfuel Cutting
- Plasma Cutting
- Power Tools
- Punching and Other Holemaking
- Roll Forming
- Safety
- Sawing
- Shearing
- Shop Management
- Testing and Measuring
- Tube and Pipe Fabrication
- Tube and Pipe Production
- Waterjet Cutting
Industry Directory
Webcasts
Podcasts
FAB 40
Advertise
Subscribe
Account Login
Search
For those who weld old steel, we salute you
- By Dan Davis
- April 16, 2010
When people talk about institutional knowledge in manufacturing, they are talking about the stuff locked up in the brains of old dudes who have all the right answers for all sorts of production puzzles, many of which are not found in books. These guys aren't about to sit down and write a "how-to" book, much less read one, so it's imperative that someone jot down this type of information for up-and-coming fabricators.
This type of information can become part of a formal work procedure that an inexperienced welder can reference if he can't figure out how to right a welding wrong. Many old-school fabricators laugh at the thought of formal quality systems and sitting in training sessions for such things, but this formal approach to sharing knowledge with all members of a shop team, not just the most experienced, keeps a company flexible enough to meet any production challenge.
The "Beyond low-carbon steel" story actually inspired this blog post because the article inspired a wonderful chain of e-mails that anyone who has handled a welding torch should read. Bernie Bisnette sent us this e-mail:
"I just wanted to throw a few points out there that may be of help to those that found the article "Beyond low-carbon steel" interesting. I work as a restoration welder/fabricator restoring trolleys—old trolleys—at the Seashore Trolley Museum in Kennebunkport, Maine. These are rusted, beat-down trolleys! My days are spent dabbling in welding witchcraft, trying to work with the old steels and joining the new to the old.
"I have found the 6013 electrode really performs. The old steel always absorbs the weldment, so favor your new steel and whip it into the old. When the old steel cools, hit it again. The old steel will sink until it is diluted with the new, and once that happens you can run normal passes.
"There are times when DCEN works better than DCEP. You just have to experiment around and watch how the steel is reacting and the amps on the power source. In some instances, I have been down to the point where the rod barely arcs. You just have to watch what is taking place. It takes a while sometimes to get it going.
"Sheet steel is another issue, and preheating can be tricky. I run turn buckles down my sheets of 10- to 16-gauge steel. This way I can turn them to stretch the welded zone. A needle gun is your best friend to peen the weld area and stress-relieve it; then it's time to start turning the buckle.
"I read that when they made these trolleys, they would prestress the steel on leveler-stretchers, so it was installed already stressed. When heat hit it, it could not stretch anymore. You have to be brave and venture in."
We also received a note from R. Daniel Carmichael of Inverness, Fla.: "Anyway, about welding cast iron … two things that my master taught me a long time ago:
- Never weld on ground cast iron. As you know, the high carbon content, upon cooling, precipitates out of the solution as graphite flakes. When you grind on it, you smear the graphite, and when you weld, you are setting yourself up for failure. Always use a clean, sharp file and file the area you are going to weld.
- Never preheat cast iron unless you can preheat the entire casting. If you can't, then keep it as cool as possible, welding only a few inches and allowing it to cool until you can touch it with your bare hand. This may take a while, but you will be successful."
That's advice that won't be shared in any introductory welding course. Be sure and grab the ear of some of these veteran welders before they walk out the door. When they leave, more than their truck will be gone from the shop.
subscribe now
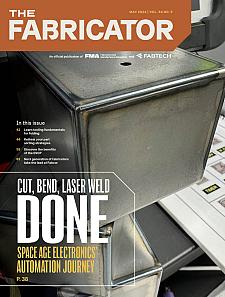
The Fabricator is North America's leading magazine for the metal forming and fabricating industry. The magazine delivers the news, technical articles, and case histories that enable fabricators to do their jobs more efficiently. The Fabricator has served the industry since 1970.
start your free subscriptionAbout the Author
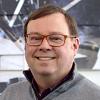
Dan Davis
2135 Point Blvd.
Elgin, IL 60123
815-227-8281
Dan Davis is editor-in-chief of The Fabricator, the industry's most widely circulated metal fabricating magazine, and its sister publications, The Tube & Pipe Journal and The Welder. He has been with the publications since April 2002.
- Stay connected from anywhere
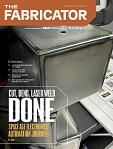
Easily access valuable industry resources now with full access to the digital edition of The Fabricator.
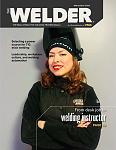
Easily access valuable industry resources now with full access to the digital edition of The Welder.
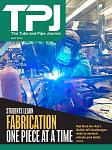
Easily access valuable industry resources now with full access to the digital edition of The Tube and Pipe Journal.
- Podcasting
- Podcast:
- The Fabricator Podcast
- Published:
- 04/16/2024
- Running Time:
- 63:29
In this episode of The Fabricator Podcast, Caleb Chamberlain, co-founder and CEO of OSH Cut, discusses his company’s...
- Trending Articles
Capturing, recording equipment inspection data for FMEA
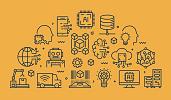
Tips for creating sheet metal tubes with perforations
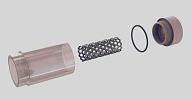
Are two heads better than one in fiber laser cutting?
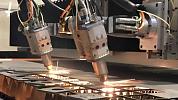
Supporting the metal fabricating industry through FMA
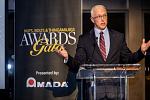
Omco Solar opens second Alabama manufacturing facility
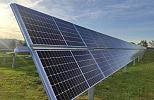
- Industry Events
16th Annual Safety Conference
- April 30 - May 1, 2024
- Elgin,
Pipe and Tube Conference
- May 21 - 22, 2024
- Omaha, NE
World-Class Roll Forming Workshop
- June 5 - 6, 2024
- Louisville, KY
Advanced Laser Application Workshop
- June 25 - 27, 2024
- Novi, MI