Senior Editor
- FMA
- The Fabricator
- FABTECH
- Canadian Metalworking
Categories
- Additive Manufacturing
- Aluminum Welding
- Arc Welding
- Assembly and Joining
- Automation and Robotics
- Bending and Forming
- Consumables
- Cutting and Weld Prep
- Electric Vehicles
- En Español
- Finishing
- Hydroforming
- Laser Cutting
- Laser Welding
- Machining
- Manufacturing Software
- Materials Handling
- Metals/Materials
- Oxyfuel Cutting
- Plasma Cutting
- Power Tools
- Punching and Other Holemaking
- Roll Forming
- Safety
- Sawing
- Shearing
- Shop Management
- Testing and Measuring
- Tube and Pipe Fabrication
- Tube and Pipe Production
- Waterjet Cutting
Industry Directory
Webcasts
Podcasts
FAB 40
Advertise
Subscribe
Account Login
Search
Manufacturing productivity: Work less, accomplish more
- By Tim Heston
- March 29, 2011
By the middle of the book we learn just how wasteful churning out parts really is. The plant has piles of parts and a warehouse chockfull of finished goods. Some finished products sit so long that they become obsolete before the company has a chance to sell them.
So what’s more wasteful: idle, on-the-clock workers, or those idle parts in the warehouse?
Job shops build to order, not to forecast. Still, how serious a problem is an idle worker? Judging by the various job shops I’ve covered, idle workers really aren’t the problem; it’s idle parts, including excess work-in-process (WIP). If parts are moving, WIP is minimal, and the plant is running close to “on edge”--that is, with minimal WIP buffers--lead-times probably are pretty competitive. If a job shop can churn out a job days or weeks faster than the competition, idle workers may not be a problem.
Instead, keeping an eye on part movement may help identify waste and subsequent opportunities for improvement. Say a pile of parts sits in front of a robotic welding cell, where a technician is setting up as fast as he can. WIP grows as laser cutting, punching, and press brake operators feed parts to the joining area. Not all operators may be busy, though. Some people in the press brake department, for instance, may have nothing to do.
That excess WIP is trouble, and those idle workers may be a symptom. It means the floor isn’t producing as much work as it could. In this case, cross-trained operators may help. In one shop I saw a press brake operator move over to a robotic welding cell to help welding personnel relieve the bottleneck.
As workers operate more efficiently, they accomplish more in less time, which may give them time to cross-train in other processes. Cross-training can be vital in job shops. I’ve talked with some shop owners who base wages in part on a worker’s training on multiple processes. The more processes an employee knows, the bigger his paycheck.
An idle worker in such an environment probably isn’t lazy. If he has nothing of value to do--such as cross-training, inspection, or relieving bottlenecks elsewhere in the plant--why should he be working? In fact, idle time may even be a very positive thing. If a company has short lead-times, strong cash flow, and healthy profits, it means workers are accomplishing more in less time. And they may be getting paid the same wage or, because of the company’s financial health, even a little more.
The last time I checked, people don’t mind getting paid more for working less.
subscribe now
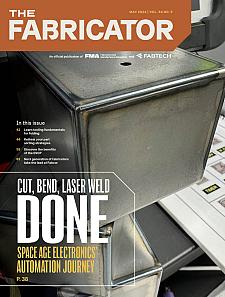
The Fabricator is North America's leading magazine for the metal forming and fabricating industry. The magazine delivers the news, technical articles, and case histories that enable fabricators to do their jobs more efficiently. The Fabricator has served the industry since 1970.
start your free subscriptionAbout the Author
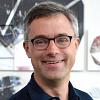
Tim Heston
2135 Point Blvd
Elgin, IL 60123
815-381-1314
Tim Heston, The Fabricator's senior editor, has covered the metal fabrication industry since 1998, starting his career at the American Welding Society's Welding Journal. Since then he has covered the full range of metal fabrication processes, from stamping, bending, and cutting to grinding and polishing. He joined The Fabricator's staff in October 2007.
- Stay connected from anywhere
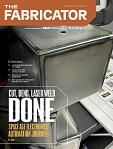
Easily access valuable industry resources now with full access to the digital edition of The Fabricator.
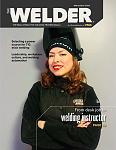
Easily access valuable industry resources now with full access to the digital edition of The Welder.
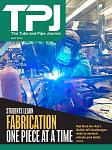
Easily access valuable industry resources now with full access to the digital edition of The Tube and Pipe Journal.
- Podcasting
- Podcast:
- The Fabricator Podcast
- Published:
- 04/16/2024
- Running Time:
- 63:29
In this episode of The Fabricator Podcast, Caleb Chamberlain, co-founder and CEO of OSH Cut, discusses his company’s...
- Trending Articles
Capturing, recording equipment inspection data for FMEA
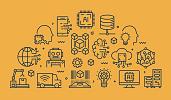
Tips for creating sheet metal tubes with perforations
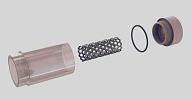
Are two heads better than one in fiber laser cutting?
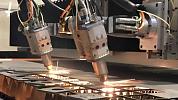
Supporting the metal fabricating industry through FMA
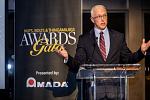
Omco Solar opens second Alabama manufacturing facility
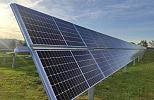
- Industry Events
16th Annual Safety Conference
- April 30 - May 1, 2024
- Elgin,
Pipe and Tube Conference
- May 21 - 22, 2024
- Omaha, NE
World-Class Roll Forming Workshop
- June 5 - 6, 2024
- Louisville, KY
Advanced Laser Application Workshop
- June 25 - 27, 2024
- Novi, MI