Owner, Brown Dog Welding
- FMA
- The Fabricator
- FABTECH
- Canadian Metalworking
Categories
- Additive Manufacturing
- Aluminum Welding
- Arc Welding
- Assembly and Joining
- Automation and Robotics
- Bending and Forming
- Consumables
- Cutting and Weld Prep
- Electric Vehicles
- En Español
- Finishing
- Hydroforming
- Laser Cutting
- Laser Welding
- Machining
- Manufacturing Software
- Materials Handling
- Metals/Materials
- Oxyfuel Cutting
- Plasma Cutting
- Power Tools
- Punching and Other Holemaking
- Roll Forming
- Safety
- Sawing
- Shearing
- Shop Management
- Testing and Measuring
- Tube and Pipe Fabrication
- Tube and Pipe Production
- Waterjet Cutting
Industry Directory
Webcasts
Podcasts
FAB 40
Advertise
Subscribe
Account Login
Search
Troubleshooting TIG
- By Josh Welton
- April 9, 2015
Last month I talked a little bit about basic troubleshooting for MIG welders. This time around I want to hit on TIG troubleshooting, which can be more problematic.
Unlike MIG, in which issues arise mostly with wire feed and spatter, TIG is a clean process with manually fed filler, thereby, eliminating those two elements.
I don’t want to cover hand-eye coordination and bead aesthetics, at least in this post, as much as what to do if you’re struggling with getting a strong arc and a clean puddle.
Collets
When I have issues, I like to start at where the circuit is made, the arc, and work my way back toward the machine. First things first. Are your consumables in good shape? Overzealous tightening of the backing cap, or using mismatched collets/collet bodies/tungsten size, can twist or distort the collet. Chances are that even if it’s jacked up, it won’t hurt your arc quality too much, but it can make the tungsten either so tight in the torch that it’s impossible to adjust or so loose that it wants to fall into the puddle.
Collet bodies themselves rarely need to be replaced, but keeping a decent stock of collets is a good idea. They’re cheap and easy to replace.
While you’re focused on the torch, check the gun itself and the backing cap as well. Missing O-rings, broken caps, or chewed-up gun bodies can result in a contaminated gas flow.
Tungsten
Obviously, the tungsten is important too. The power travels along the surface of the tungsten, so you want it to be as smooth as possible. Stray marks or boogers on the electrode will hurt arc performance.
Something typically taught at the beginning of your welding training bears repeating: Use a dedicated grinder if possible, and minimize grinding marks on the tapered end. If there are any marks they should be lengthwise, parallel to the tungsten.
The end of the taper is where the arc shoots to the metal, so keep it clean. Depending on how many amps you’re using, a slightly flattened tip can work, but I like to keep mine as sharp as possible.
A little aside here: If you’re using a transformer-based machine to weld aluminum, you need a larger-diameter tungsten relative to what you’d use with an inverter. Failure to compensate will cause tungsten tips to disintegrate regularly.
Cups
Now, we could talk cups adnauseam, but we won’t. I’m gonna say just two things:
- Make sure the cup opening is big enough to allow gas flow around the tungsten diameter you’re using.
- Keep the tungsten stickout reasonable, so that the arc is within range of your gas flow’s protection.
There’s plenty to cover on traditional cups, monster nozzles, and everything in between, but for the here and now, let’s focus on a typical cup setup. If you can’t troubleshoot this, you have no business using anything else.
No matter the process, you want to start with clean material. And nowhere is it as important as with TIG. Mill scale and oil on steel cause poor arc performance, shortened tungsten life, porosity, and undercut.
An oxide barrier on aluminum may be partially defeated with proper AC balance and EP/EN settings on some inverters, but it’s still good practice to remove it first. Aluminum oxide creates many of the same problems that mill scale does, and if you’re fighting the material, it’s not a bad place to start.
Operator ErrorNow you’ve got the torch on lockdown, a nicely prepped tungsten, and clean base material, but your puddle is still acting the fool. Operator error could be the cause.
How’s your arc length? Keep the tip of the tungsten as close as possible to the workpiece. Tight arc = strong arc. Tight arc = less chance that a breeze can sneak in and mess with your gas flow. Speaking of which, even the slightest air movement can screw with that flow, so take care to protect the weld area from wind.
Torch angle can have an effect as well; try to keep it in the 45- to 90-degree range. An angle that is too slight might cause you to lose gas coverage.
Filler
Still having issues? Some guys would start at this next step, but dirty filler usually isn’t the cause of my problems. Still, contaminated filler, or even dirty hands or gloves, can cause a bubbly puddle.
Wash those hands, change the gloves, and keep the filler sealed up until you use it and/or wipe it down with alcohol before use. Easy-peasy.
Still Struggling?
Now, if you’re still struggling, you’re probably ready to beat your head against a wall. I’ve been there. Check all your gas hoses for cuts, and make sure they’re tightened securely at all connecting points. If you found a compromised hose or connection, hopefully that was it, and your problem is solved. Air sneaking into the gas flow is a sure way to contamination.
But if not, and your puddle is still not right, WHAT?!?!
I can specifically remember all three times this has happened to me. Once the puddle was just garbage, I couldn’t weld anything. I was scratching my head forever.
The second time it sort of welded OK, but left a black ring around the bead.
The third time it was at Macomb Community College. The arc on aluminum became shaky at low amps, and every stainless weld looked burned and uneven. I was there for certification, and the staff thought I was nuts. Having been through similar issues twice before, I told them it was a bad batch of gas. No, they said, can’t be. I just couldn’t weld. “OK, hotshot, go for it then!” I said.
Funny, all of a sudden, the instructor (a friend of mine now) couldn’t weld either. In all three cases, the gas was contaminated.
It happens. Sometimes it’s so extreme you can’t weld at all, other times it’s barely noticeable, but something just isn’t right. After the first instance at my shop, I started making sure I had a second bottle from a separate batch on hand at all times, just to double-check.
There’s a lot more we could cover on machines. Transformers have points that need to be cleaned and adjusted. Inverters have electronics that go bad (and if they do, you’ll see error codes). But most of the time with TIG, it’s between the machine and the torch (and occasionally the bottle), so I wanted to cover the things that I’ve found most often to be the cause of gremlins. Hopefully it helps!
subscribe now
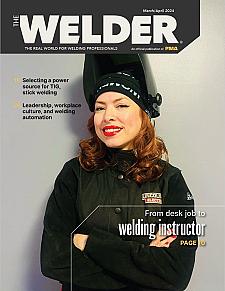
The Welder, formerly known as Practical Welding Today, is a showcase of the real people who make the products we use and work with every day. This magazine has served the welding community in North America well for more than 20 years.
start your free subscriptionAbout the Author
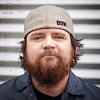
About the Publication
- Stay connected from anywhere
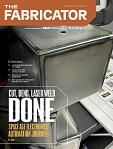
Easily access valuable industry resources now with full access to the digital edition of The Fabricator.
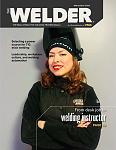
Easily access valuable industry resources now with full access to the digital edition of The Welder.
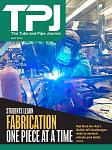
Easily access valuable industry resources now with full access to the digital edition of The Tube and Pipe Journal.
- Podcasting
- Podcast:
- The Fabricator Podcast
- Published:
- 04/16/2024
- Running Time:
- 63:29
In this episode of The Fabricator Podcast, Caleb Chamberlain, co-founder and CEO of OSH Cut, discusses his company’s...
- Industry Events
16th Annual Safety Conference
- April 30 - May 1, 2024
- Elgin,
Pipe and Tube Conference
- May 21 - 22, 2024
- Omaha, NE
World-Class Roll Forming Workshop
- June 5 - 6, 2024
- Louisville, KY
Advanced Laser Application Workshop
- June 25 - 27, 2024
- Novi, MI