- FMA
- The Fabricator
- FABTECH
- Canadian Metalworking
Categories
- Additive Manufacturing
- Aluminum Welding
- Arc Welding
- Assembly and Joining
- Automation and Robotics
- Bending and Forming
- Consumables
- Cutting and Weld Prep
- Electric Vehicles
- En Español
- Finishing
- Hydroforming
- Laser Cutting
- Laser Welding
- Machining
- Manufacturing Software
- Materials Handling
- Metals/Materials
- Oxyfuel Cutting
- Plasma Cutting
- Power Tools
- Punching and Other Holemaking
- Roll Forming
- Safety
- Sawing
- Shearing
- Shop Management
- Testing and Measuring
- Tube and Pipe Fabrication
- Tube and Pipe Production
- Waterjet Cutting
Industry Directory
Webcasts
Podcasts
FAB 40
Advertise
Subscribe
Account Login
Search
High-volume joining process expands use of aluminum in autos
- June 8, 2015
- News Release
- Assembly and Joining
In partnership with General Motors, Alcoa, and TWB Co. LLC, researchers from the Department of Energy's Pacific Northwest National Laboratory (PNNL) have transformed a joining technique called friction stir welding (FSW). The technique now can be used to join aluminum sheets of varying thicknesses, which is key to producing auto parts that are light yet retain strength where it's most needed.
The PNNL-developed process also is 10 times faster than current FSW techniques, representing production speeds that, for the first time, meet high-volume assembly requirements. It delivers strong, lightweight parts, such as a car door that is 62 percent lighter and 25 percent cheaper than that produced with conventional manufacturing methods.
The two-phase, six-year project is funded by the Department of Energy's Office of Energy Efficiency and Renewable Energy with in-kind partner contributions from each of the participating companies.
An FSW machine looks and acts like a cross between a drill press and a sewing machine. Lowered onto two metal sheets sitting side-by-side, the pin tool spins against both edges. As it travels along, the pin creates friction that heats, mixes, and joins the alloys without melting them. The process welded 0.5 MPM, however, which is too slow for auto industry production standards.
PNNL created dozens of unique tool designs with varying shapes, lengths, and diameters of the pin. These were assessed against a variety of weld parameters, such as the depth, rotation speed, and angle of the tool. Through statistical analysis, the team identified the optimal combination of tool specification and weld parameters that could consistently withstand high-speed production demands.
PNNL provided the weld and tool specifications to TWB Co. and GM. TWB then independently welded, formed, and analyzed more than 100 aluminum blanks in close coordination with GM. GM subsequently stamped its first full-sized inner door panel supplied by TWB—free of imperfections—from aluminum sheets in varying thicknesses.
TWB now has a dedicated FSW machine at its production facility in Monroe, Mich., based on PNNL’s process that can produce up to 250,000 parts per year.
subscribe now
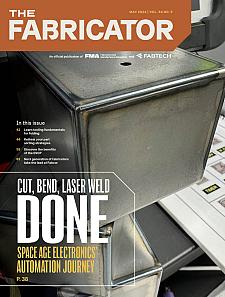
The Fabricator is North America's leading magazine for the metal forming and fabricating industry. The magazine delivers the news, technical articles, and case histories that enable fabricators to do their jobs more efficiently. The Fabricator has served the industry since 1970.
start your free subscription- Stay connected from anywhere
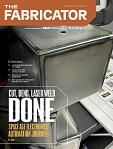
Easily access valuable industry resources now with full access to the digital edition of The Fabricator.
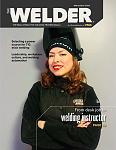
Easily access valuable industry resources now with full access to the digital edition of The Welder.
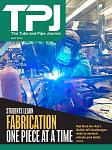
Easily access valuable industry resources now with full access to the digital edition of The Tube and Pipe Journal.
- Podcasting
- Podcast:
- The Fabricator Podcast
- Published:
- 04/16/2024
- Running Time:
- 63:29
In this episode of The Fabricator Podcast, Caleb Chamberlain, co-founder and CEO of OSH Cut, discusses his company’s...
- Trending Articles
Capturing, recording equipment inspection data for FMEA
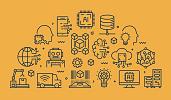
Tips for creating sheet metal tubes with perforations
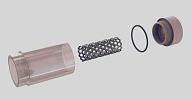
Are two heads better than one in fiber laser cutting?
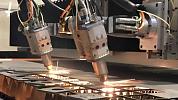
Supporting the metal fabricating industry through FMA
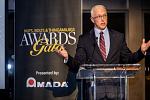
Omco Solar opens second Alabama manufacturing facility
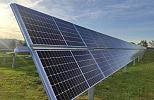
- Industry Events
16th Annual Safety Conference
- April 30 - May 1, 2024
- Elgin,
Pipe and Tube Conference
- May 21 - 22, 2024
- Omaha, NE
World-Class Roll Forming Workshop
- June 5 - 6, 2024
- Louisville, KY
Advanced Laser Application Workshop
- June 25 - 27, 2024
- Novi, MI