- FMA
- The Fabricator
- FABTECH
- Canadian Metalworking
Categories
- Additive Manufacturing
- Aluminum Welding
- Arc Welding
- Assembly and Joining
- Automation and Robotics
- Bending and Forming
- Consumables
- Cutting and Weld Prep
- Electric Vehicles
- En Español
- Finishing
- Hydroforming
- Laser Cutting
- Laser Welding
- Machining
- Manufacturing Software
- Materials Handling
- Metals/Materials
- Oxyfuel Cutting
- Plasma Cutting
- Power Tools
- Punching and Other Holemaking
- Roll Forming
- Safety
- Sawing
- Shearing
- Shop Management
- Testing and Measuring
- Tube and Pipe Fabrication
- Tube and Pipe Production
- Waterjet Cutting
Industry Directory
Webcasts
Podcasts
FAB 40
Advertise
Subscribe
Account Login
Search
Collaborative project brings operational 3-D printed excavator one step closer to reality
- September 29, 2016
- News Release
- Shop Management
The Association of Equipment Manufacturers (AEM), Milwaukee, has announced the recent 3-D printing of a prototype excavator using large-scale additive manufacturing technologies.
Known as Project AME (Additive Manufactured Excavator), the excavator is being 3-D printed in three components—cab, boom, and heat exchanger—using various machines at the Oak Ridge National Laboratory’s (ORNL’s) Manufacturing Demonstration Facility (MDF). The boom will be fabricated using a newly developed free-form additive manufacturing technique to print large-scale metal components.
The excavator is a collaboration among AEM, National Fluid Power Association, Center for Compact and Efficient Fluid Power, ORNL, the National Science Foundation, and several universities. The project is supported by the Department of Energy’s Office of Energy Efficiency and Renewable Energy – Advanced Manufacturing Office.
A Georgia Tech research team designed the steel boom, stick, and bucket. A student engineering team from the University of Illinois designed the cab. A research team from the University of Minnesota is responsible for the aluminum-powder bed 3-D-printed oil cooler design.
subscribe now
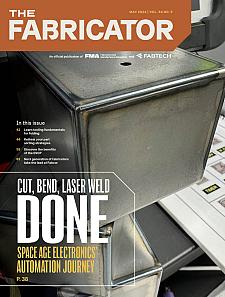
The Fabricator is North America's leading magazine for the metal forming and fabricating industry. The magazine delivers the news, technical articles, and case histories that enable fabricators to do their jobs more efficiently. The Fabricator has served the industry since 1970.
start your free subscription- Stay connected from anywhere
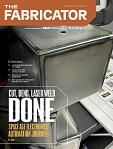
Easily access valuable industry resources now with full access to the digital edition of The Fabricator.
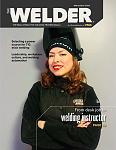
Easily access valuable industry resources now with full access to the digital edition of The Welder.
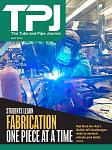
Easily access valuable industry resources now with full access to the digital edition of The Tube and Pipe Journal.
- Podcasting
- Podcast:
- The Fabricator Podcast
- Published:
- 04/16/2024
- Running Time:
- 63:29
In this episode of The Fabricator Podcast, Caleb Chamberlain, co-founder and CEO of OSH Cut, discusses his company’s...
- Industry Events
16th Annual Safety Conference
- April 30 - May 1, 2024
- Elgin,
Pipe and Tube Conference
- May 21 - 22, 2024
- Omaha, NE
World-Class Roll Forming Workshop
- June 5 - 6, 2024
- Louisville, KY
Advanced Laser Application Workshop
- June 25 - 27, 2024
- Novi, MI