- FMA
- The Fabricator
- FABTECH
- Canadian Metalworking
Categories
- Additive Manufacturing
- Aluminum Welding
- Arc Welding
- Assembly and Joining
- Automation and Robotics
- Bending and Forming
- Consumables
- Cutting and Weld Prep
- Electric Vehicles
- En Español
- Finishing
- Hydroforming
- Laser Cutting
- Laser Welding
- Machining
- Manufacturing Software
- Materials Handling
- Metals/Materials
- Oxyfuel Cutting
- Plasma Cutting
- Power Tools
- Punching and Other Holemaking
- Roll Forming
- Safety
- Sawing
- Shearing
- Shop Management
- Testing and Measuring
- Tube and Pipe Fabrication
- Tube and Pipe Production
- Waterjet Cutting
Industry Directory
Webcasts
Podcasts
FAB 40
Advertise
Subscribe
Account Login
Search
Harco Metal Products
- August 9, 2010
- Article
- Shop Management
![]() |
Harco engineers assess project specifics |
Southwest Headquarters:
941 W. 23rd St.
Tempe, AZ 85282
480-829-0450
Southeast Headquarters:
185 10th St. S.E.
Fort Payne, AL 35968
256-845-3885
By Claire Pearson
OPENED: 1990
WHY: Before launching Harco Metal Products (Harco), founder and President Jay Hall owned a construction company in a down-turned local economy. Hall was interested in opening a business vastly different from his current endeavor— one with unlimited growth and income potential. Upon realizing that three of the largest global industries (automotive, defense, and medical) dealt with bent tubing, Hall learned everything he could about metal fabrication and started Harco Metal Products.
CAPABILITIES: Harco assists customers with product development, designing, and fabrication of metal tubular parts. Its capabilities include:
- Tube forming: Expanding, reducing, beading, flaring
- Tube bending: CNC mandrel, free -orm, dual-head, roll
- Tubular assembly
- Tubular fluid lines
- Machining: Full-service CNC milling and CNC lathe
- Welding: GMAW, GTAW, robotic, induction brazing, plasma
- Optical measuring
- Systems integration
SHOP WORKHORSE(S): Hall believes no one piece of equipment is more important than another. Any job requires several high-tech machines to accomplish client goals, and it is truly the collective group of equipment that is important. Says Hall, "If all I had was tube benders, I would be very limited in what I could provide my client everything is indispensable, including our high-level staff."
MOST UNUSUAL OR MEMORABLE PROJECT: Harco's most memorable project was the result of a problem faced by renewable-energy company Stirling Energy Systems. Stirling needed a small-diameter tube bent using free-form, multidimensional bending techniques, with repeatability and extremely high assembly tolerances.
Harco devised the theory that by combining the capabilities of two unique machines, the company could meet Stirling’s stringent requirements. Hall flew to Germany with his team, where he met with the heads of Wafios Machinery Corp. and Aicon 3D Systems. Within six days, Hall, Wafios, and Aicon tested and proved Harco's hypothesis.
This was a highly memorable project because it signified the advent of Harco’s adoption of more high-end, state-of-the-art equipment and proved to Hall that the Harco team was capable of completing projects of any size or complexity.
GREATEST CHALLENGE: "This industry as a whole continues to shift from a domestic to a global marketplace. The challenge to adapting well in this environment is being able to read the world ahead of time as customer concerns and technologies change at alarming rates," Hall said.
LOOKING AHEAD: Harco plans to continue diversifying job shop capabilities for increased ability in producing unique metal and tubular assemblies. Going forward, Harco plans to incorporate laser cutting, press brake fabrication, more machining capabilities, and much more to the list of services offered in-house.
ADVICE FOR WOULD-BE SHOP OWNERS: Embrace new technology; build on knowledge; and always listen to your customers' concerns.
CONTACT: Jay Hall at Harco Metal Products, 480-829-0450, jay@tubebending.net, https://www.webendtube.com/
please contact Vicki Bell.
subscribe now
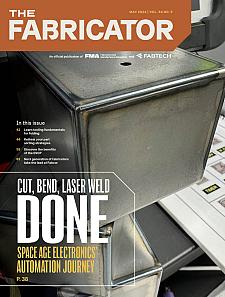
The Fabricator is North America's leading magazine for the metal forming and fabricating industry. The magazine delivers the news, technical articles, and case histories that enable fabricators to do their jobs more efficiently. The Fabricator has served the industry since 1970.
start your free subscription- Stay connected from anywhere
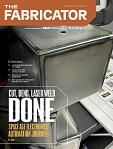
Easily access valuable industry resources now with full access to the digital edition of The Fabricator.
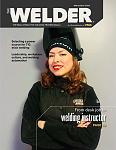
Easily access valuable industry resources now with full access to the digital edition of The Welder.
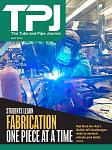
Easily access valuable industry resources now with full access to the digital edition of The Tube and Pipe Journal.
- Podcasting
- Podcast:
- The Fabricator Podcast
- Published:
- 04/16/2024
- Running Time:
- 63:29
In this episode of The Fabricator Podcast, Caleb Chamberlain, co-founder and CEO of OSH Cut, discusses his company’s...
- Trending Articles
Tips for creating sheet metal tubes with perforations
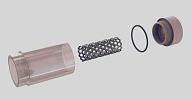
JM Steel triples capacity for solar energy projects at Pennsylvania facility
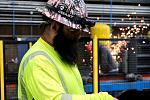
Are two heads better than one in fiber laser cutting?
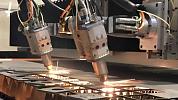
Supporting the metal fabricating industry through FMA
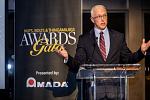
Omco Solar opens second Alabama manufacturing facility
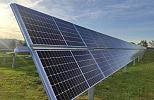
- Industry Events
16th Annual Safety Conference
- April 30 - May 1, 2024
- Elgin,
Pipe and Tube Conference
- May 21 - 22, 2024
- Omaha, NE
World-Class Roll Forming Workshop
- June 5 - 6, 2024
- Louisville, KY
Advanced Laser Application Workshop
- June 25 - 27, 2024
- Novi, MI